Flexible printed circuits (FPCs), also called flex PCBs or flex circuits, are lightweight, bendable interconnects well suited for movable applications with dynamic folding/twisting needs or severe space constraints precluding rigid boards. From tiny sensors to foldable consumer devices to intricate medical instruments, flex PCB innovation enables countless essential products.
This has driven specialization of an expansive flex PCB manufacturing ecosystem spanning small propriety process startups through diversified electronics conglomerates. Let’s analyze the 10 most prominent global flex circuit producers by capability scale and technology leadership enabling product miniaturization across industries.
Flex PCB Demand Drivers
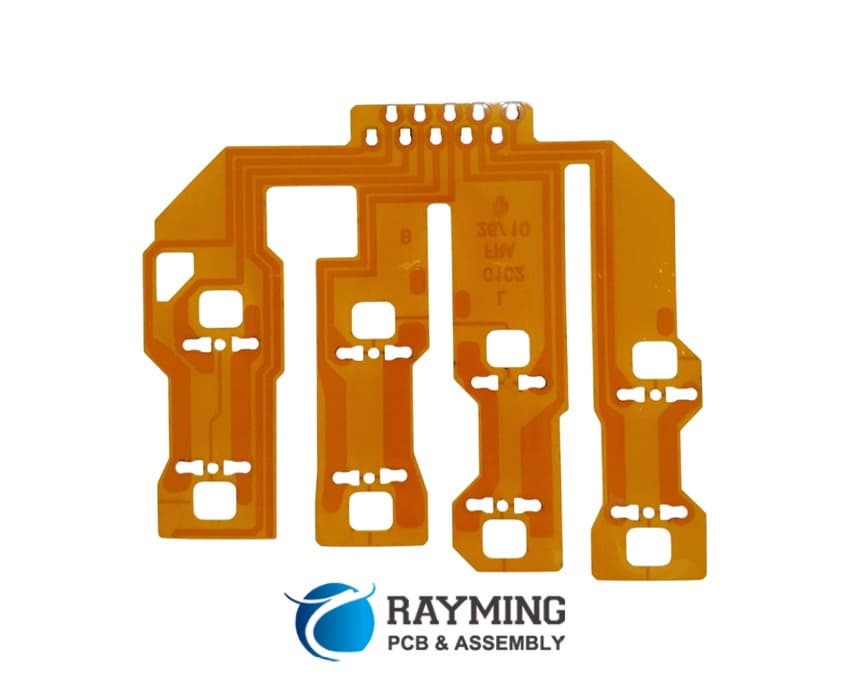
Why has interest in flex PCB technology surged recently from designers?
Foldable/Wearable Consumer Electronics – Phones, tablets, PCs integrating folding displays with tight radii facilitated by flex board interconnections while wearables leverage ultra-thin profile cabling.
Automotive Electronics – In-vehicle dynamic flex cabling for steering/dashboard controls, increasing use in sensors and lighting too.
Medical Instruments – Endoscopes, imaging probes, hearing aids, vital measurement patches.
Defense/Aerospace – Helmets, navigation systems, weapon systems buttons/connectivity.
Industrial Internet of Things – Interposers and cabling for modular connected smart sensors
From enrolling consumer early adopters to assurance in mission critical systems, flex printed circuits bridge across application segments.
Flex PCB Material, Construction and Process Overview
The combination of specialized materials science and advanced micro-machining fabrication sets flex PCBs apart:
- Base polymer films including Kapton polyimide, acrylic adhesives, PET, PEN or composites replace rigid fiberglass laminates. Metal foils commonly rolled onto films.
- Photolithographic patterning forms circuits – however chemical etchants tuned for flexible substrates plus laser direct imaging processes specialized.
- Alternate substrates like LCP (Liquid crystal polymers) and PTFE films also gain adoption for extreme temperature ratings.
- Ultra-fine lines down below 8 microns enable dense interconnects. Blind/buried vias and skipping plating resists cater towards HDI designs.
- Laser cutting, precision die stamping fully singulates boards from panelized build flows.
Leading flex PCB manufacturers outlined below leverage innovations across these process domains alongside application intimacy to fuel product roadmaps.
1. Career Technology (MFLEX)
One of the earliest and now largest flexible PCB producers globally, Career Tech leverages an extensive flex technology patent portfolio stemming from founderships back in the 1960s. Regarded as instrumental pioneers in commercializing flex circuits starting from cameras through modern connectivity and computing demands.
Headquarters: Suzhou, China
Founded: 1999 from previous JYSH, Mflex lineage
Flex Capability:
- Among first introducing laser direct imaging capabilities
- Ultra-high complexity multilayer build up flex and rigid-flex
- Branded Flextronics manufacturing services customer
Facilities: >20 plants across China, Malaysia, Serbia
Key End Markets: Consumer electronics, automotive, medical, aerospace
FY2021 Revenue: $2.1 billion
With both scale and consistent flex PCB innovations to enable customer roadmaps, Career Tech leads the pack as formidable flex circuit player meeting the most exacting OEM expectations.
2. Flexium Interconnect
Copy code
Founded in the year 2000, Flexium rose rapidly to become a top five global flex PCB manufacturer anchored by advanced R&D. They also operate a dozen sales offices across countries to support regional access. One of the wider reaching sales/support networks worldwide.
Headquarters: Hsinchu, Taiwan
Founded: 2000
Flex Capability:
- 8 micron line/space circuits
- Aggressive investment in laser direct imaging equipment
- Rigid-flex expertise sought after
Facilities: 5 Manufacturing Plants across 3 continents
End Applications: Automotive cameras/sensors, medical devices
FY2021 Revenue: $880 million
Flexium highlights one of the stronger Asia-based flex PCB design-through-manufacturing pureplays advancing the field.
3. MINCO
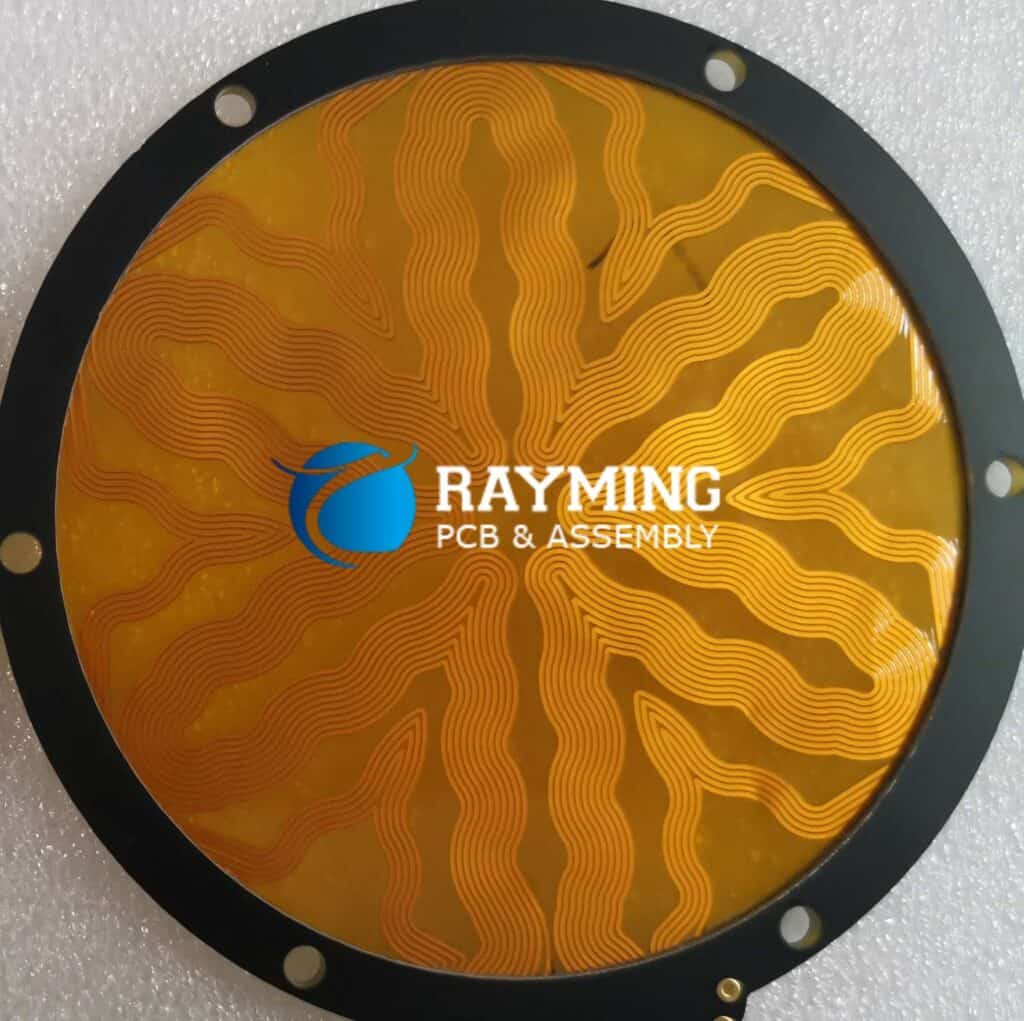
While MINCO produces flex and rigid printed circuit boards alike, they stand distinctly as long time flex specialists since the 1950s originating from Minnesota. Retains over 3600 global patents covering materials science inventions improving thermal conduction, attachment reliability, density and high frequency signal integrity over decades of targeted innovation before flex was mainstream.
Headquarters: Minneapolis, Minnesota USA
Founded: 1956
Flex Capabilities:
- High thermal conductivity dielectric films
- Ultra-fine features below 10 microns standard
- Extensive RF/microwave and power electronics expertise sought after
Facilities: Wisconsin and Minnesota, USA (ISO-13485 certified med devices line)
End Applications: Aerospace/defense, medical electronics
FY2021 Revenue: $210+ million
As one of the most pedigreed flex technology houses entering 7th decade, Minco remains the gold standard for pioneering expertise combining deep application intimacy with high performance specialty materials for mission critical systems.
4. Zhen Ding Tech
Founded in Taiwan with current Singapore HQ, Zhen Ding Tech has grown into top global flex PCB producer riding key partnership with Foxconn-HonHai Precision serving immense consumer electronics needs. Covering high volume smartphones flex cables plus lower volume yet high mix modules across product categories.
Headquarters: Singapore
Founded: 2002
Flex Capability:
- High volume optimized lines
- Fan-out wafer level packaging interconnect and substrate expertise
- Extensive consumer electronics integration depth
Facilities: Taiwan, Singapore, Mexico, China
End Applications: Apple iPhone, Automotive infotainment panels
FY2021 Revenue: $1.14 billion
Unique scale in ultra-high volume flex manufacturing for smart consumer devices while diversifying technology into adjacent applications.
5. Multi-Fineline Electronix (MFLEX)
MFLEX, an agile spinout from semiconductor group Amkor, gained renown for its expertise in realizing miniaturized flexible printed circuits down below 25 micron geometries necessary for densely integrated products. Founding DNA around extreme precision high layer count build up interconnect technologies.
Headquarters: Irvine, California
Founded: 2004
Flex Capability:
- Pedigreed leadership driving flex PCB innovation into emerging apps
- Proprietary microvias, ultra-fine trace multilayer, and stacked via formation techniques
Facilities: California and Texas (USA), Suzhou (China)
End Applications: Defense systems, medical instruments
FY2021 Revenue: $500+ million
Standout advanced skillset for unlocking electronics roadmap advancement through purpose built high complexity routing solutions to circumvent conventionally perceived product constraints or bottlenecks.
6. Flex (Flextronics)
While Flextronics stands universally recognized as the largest end-to-end electronics manufacturing services conglomerate spanning everything from printed circuit boards through complete product assemblies, their printed circuit board division retains uniquely strong capabilities specifically around innovative flex PCB technology. This traces back to their 2016 acquisition of flexible printed circuits leader Multek, inheriting 40+ years of expertise. Flextronics leverages these flex material science talents across their global customer programs.
Headquarters: Singapore
Founded: 1990
Flex Capability:
- Vertically integrated flex fabrication through upstream polymeric raw materials R&D consultants
- Quick turn prototyping services leverage Velflex substrates inventory
- Defense, medical, automotive pedigree
Facilities: 35+ countries
End Applications: Broad multifaceted support
FY2021 Revenue: $26.3 billion
Market dominating scale and breadth across flex PCB ecosystem from materials through manufacturing strengthens supply chain stability for product developers.
7. Interflex
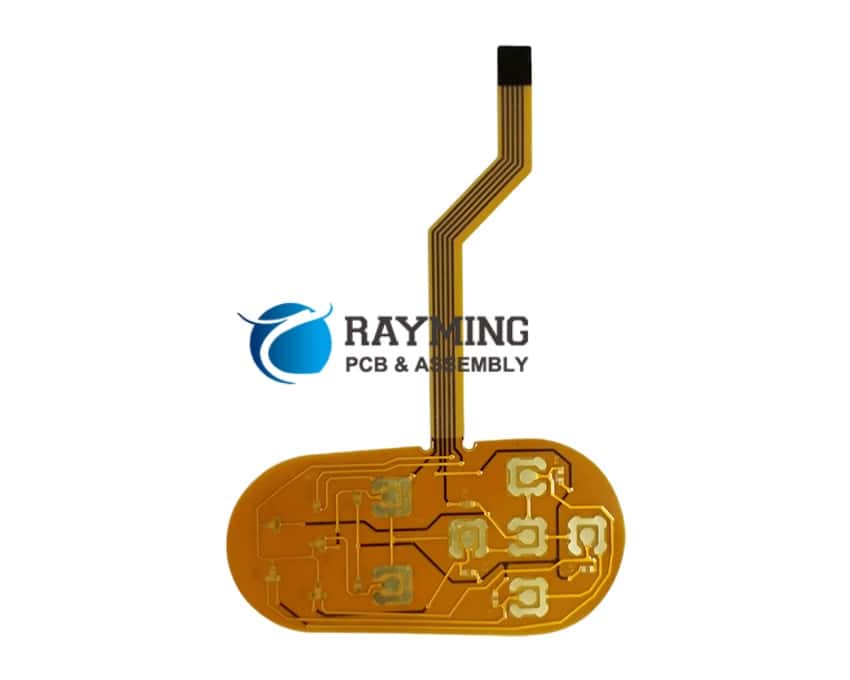
Founded 1969 in Japan, Interflex stands uniquely as one of the early globalization success stories within electronics manufacturing as an ingenious pioneer transferring flexible printed circuit expertise out of Asia to serve American and European customers cost effectively. Ushered in robust design-manufacturing flex ecosystem in US with California circuits factory supported by headquarters application expertise and process advice, alongside prolific Japanese output.
Headquarters: Osaka, Japan
Founded: 1969
Flex Capability:
- Rigid-flex expertise melding flex printed circuits with rigid board sections.
- Miniaturization trendsetters annually improving circuit linewidth precision.
- Pedigreed medtech and imaging systems circuits
Facilities: Japan, Sacramento CA Plant
End Applications: Endoscopes, ultrasound transducers, electronics testing
FY2021 Revenue: $250+ million
Longtime technical leadership bridging eastern and western hemispheres with reliable high complexity flex solutions certified for mission-critical needs.
8. RayMing Technology
An exemplar of mainland China’s rapid printed circuits manufacturing rise, Rayming Tech demonstrates agility going from startup to industry heavyweight in under a decade marked by hefty investments in cutting edge equipment and worldclass process certifications. Specializing in high mix low volume intricate flexible boards catering towards startup milatech and pushing boundaries around density and embedded passives integration.
Headquarters: Shenzhen, China
Founded: 2005
Flex Capability:
- Surface finish experts with ENIG, Imm. Ag, targeted paste printing guiding placement
- Capable of volume order-to-order flexibility despite scale
- Redundant equipment minimizing risk
Facilities: Mainland China
End Applications: Wearables, internet of things
FY2021 Revenue: $132 million
Rapidly earning reputation for navigating customer custom complex circuit needs with precision as new competitive force meeting specialization niche so vital for product innovation pace. Geopolitically stabilizes supply too.
9. Sumitomo
While diversified Japanese conglomerate Sumitomo Group has a hand across seemingly every major global industry from mining to transportation to real estate to finance, a core electronics competence traces back to printed wiring boards kicked off in the mid 1980s at the dawn of consumer electronics expansion. Retained technical expertise cultivating both scale production plus small batch specialty manufacturing cementing reputation for difficulty high layer count multilayer flex enabling medical devices and communications infrastructure.
Headquarters: Tokyo, Japan
Founded: 1985
Flex Capability:
- Multilayer flex and rigid-flex for high frequency and density
- Mass lamination expertise for ultra-thin flex
- Focus on medical electronics partnerships
Facilities: Japan, China, Malaysia, USA
End Applications: Endoscopes, OCT systems, RF communications
FY2021 Revenue: $800+ million electronics division
Longstanding flex printed circuit innovation steeped in material science prowess reliably serving mission-critical niches where performance and trust indispensable.
10. TTM Technologies
Founded in 1998, TTM Technologies has aggressively expanded into one of the industry’s most geographically diverse mid/large tier PCB manufacturers covering over a dozen speciality technology areas including instrumentation, lighting, and automotive electronics. But importantly maintained overlap with complex flex PCBs for sophisticated applications including aerospace antennas and defense systems tacking on niche expertise through targeted acquisitions like specialty supplier Honeywell Circuits.
Headquarters: Costa Mesa, California
Founded: 1998
Flex Capability:
- Strategic M&A accumulation of flex technology breadths
- Strong US defense customer base
- Rigid flex expertise
Facilities: North America and China
End Applications: Avionics, missiles and munitions
FY2021 Revenue: $2.5+ billion
Breadth across applications imparting hard won wisdom around tailoring flexible printed circuits advances optimally aligned to customer program requirements.
Flex PCB Landscape Summary
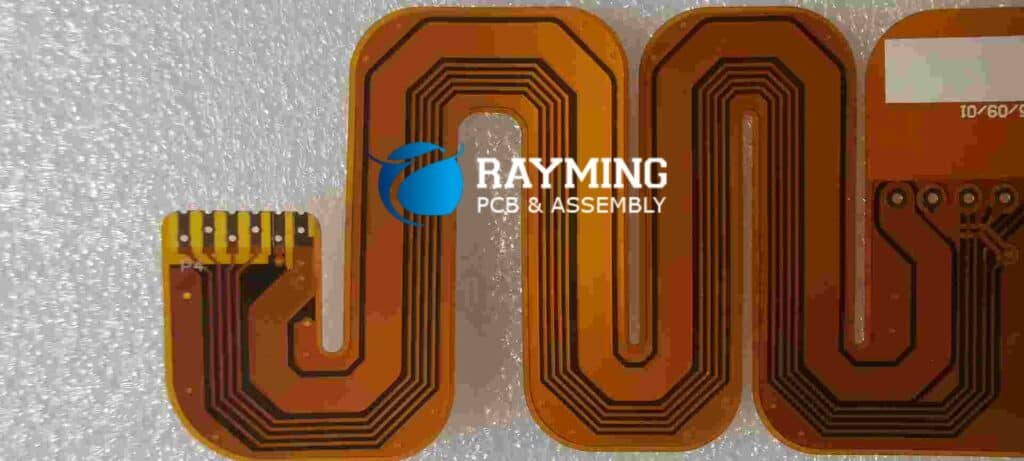
The manufacturers above represent key flexible circuit producers pushing interconnect innovations across global electronics sectors by navigating immense materials and process intricacies. As increasing miniaturization demands challenge rigid printed circuit scalability limits, leveraging polymer sciences and fabrication extremization unlocks vital next generation product expansion.
Frequently Asked Questions
Q: Why has medical device technology provoked more innovation in flex PCBs than most other segments recently?
A: Miniaturized diagnostics and surgical tools rely intensely on intricately routed tiny flexible circuits but face stringent certifications (ISO-13485 for example) with little margin of error given human lives at stake, provoking creative material and topographical problem solving.
Q: How are flex PCB manufacturers improving environmental sustainability?
A: Converting to aqueous dry film photoresists reduces chemical waste. Also recycling initiatives around polymer and copper reclamation. Some adopt solar power for facilities. Work remains but incremental improvements underway.
Q: Which key flex PCB technology milestones expanded capabilities drastically for designers?
A: Laser direct imaging enables smaller vias. Fine tip photolithography and plating technology yield higher circuit densities. Introduction of LCP and glass fabric substrates operate at extreme temps. Adhesives keep up with dielectric films flexibility.
Q: Why does flex PCB industry consolidation remain fairly limited compared to rigid board M&A despite fragmentation?
A: Mission critical quality dependence on proprietary process specialization sustained over long periods fosters customer loyalty that disincentives larger entities from attempting merge emerging innovators losing talent. Plus anti-trust reviews.
Q: How are semiconductors and flex PCBs symbiotically enabling each other’s progress?
A: Flex PCB innovation supports redistribution density, stacking, and ruggedization necessary to amplify functionality from new ICs. In turn, chips integrate more diverse mixed signal, RF, and power efficiency unlocking performance seeks for envelope pushing flexible interconnect applications. Accelerative interdependency underway.
So in summary, specialized flexible circuit manufacturers outlined above persistently pioneer material sciences essential for overcoming relentless industry demands for smaller, faster, and more dynamic modern electronics systems through sustained proprietary inventions. This innovation focus cements crucial roles across supply chains depending deeply on their collaboration and knowledge leadership harnessing promise of flex PCB technology fully towards tomorrow.
0 Comments