The ability to turn around printed circuit boards (PCBs) quickly and efficiently is critical in today’s high-tech landscape. Whether you’re a startup trying to get your product to market ahead of the competition or an established company needing prototypes fast, reducing PCB production time makes a big difference.
In this article, we’ll explore key tips and strategies for fast turn PCB production. We’ll look at how to prepare your design files, choose the right manufacturer, utilize advanced manufacturing techniques, and more. With the right approach, you can slash your PCB lead times and get innovative products into customers’ hands faster.
Keys to Fast PCB Turnaround Times
Several main factors impact how quickly you can get your finished PCBs:
- Design preparation – Properly preparing Gerber and drill files using consistent naming conventions streamlines handoffs to your manufacturer. Good documentation like fabrication notes also helps.
- Manufacturer capabilities – Partner with a manufacturer that offers advanced capabilities like automated optical inspection (AOI) and direct imaging (DI) to reduce production steps. Localization also minimizes shipping lags.
- Quick-turn services – Many manufacturers offer expedited services with lead times ranging from 24 hours to 5 days, for an additional fee.
- Smaller quantities – Opt for smaller prototyping quantities (10-50 units). The more boards required, the longer production takes.
- Panelization – Panelizing multiple PCB designs into one large board maximizes production efficiency.
- Board complexity – Simpler boards with fewer layers translate to faster assembly. High-complexity boards take more time.
- Communication – Maintain open communication with your manufacturer to proactively address any potential delays.
Choosing a Manufacturer for Fast Turnaround
Choosing the right PCB manufacturer is key for fast turnarounds. Here are top factors to consider:
Location
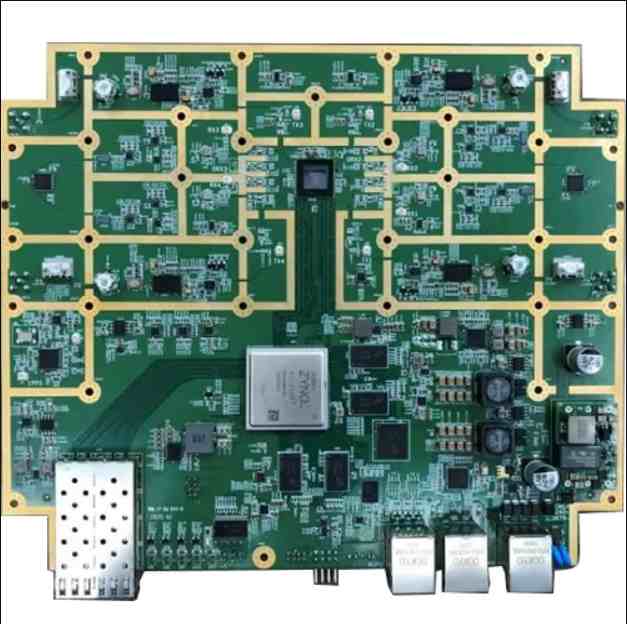
- Opt for a manufacturer located close to you to minimize shipping time. For fastest turnarounds, local often beats offshore.
Expedited Services
- Many manufacturers offer quick-turn services with lead times as low as 24 hours. Expect to pay a premium for ultra-fast delivery.
Production Capabilities
- Prioritize manufacturers using cutting-edge tech like DI, AOI, robotics, etc. to streamline processes.
Prototyping Focus
- Look for manufacturers used to working with prototypes in small volumes if this matches your needs.
Communication
- Ensure your manufacturer has systems in place for good customer communication and addressing rush orders.
Reputation
- Vet potential manufacturers thoroughly based on customer reviews, quality standards, and industry reputation.
Here is a comparison table of common PCB manufacturer lead times:
Service | Lead Time | Description |
---|---|---|
Standard | 10-15 days | Default service for medium quantities |
Expedited | 5-7 days | Faster service for additional fee |
Super Expedited | 3-5 days | Rush service for high priority orders |
Ultra Expedited | 24-48 hours | Lightning fast for critical projects |
Optimizing Your Design Files
Properly preparing your PCB design files is crucial for fast turnarounds. Follow these tips:
CAD Outputs
- Export all required Gerber files, drill files, pick and place files, etc. per your manufacturer’s specifications.
File Organization
- Organize layers into clearly named folders (e.g. “GerberFiles,” “DrillFiles”).
Layer Callouts
- Use consistent naming conventions for all layers based on industry standards.
Fabrication Notes
- Include a fabrication drawing with custom notes for your board finish, solder mask, silkscreen, etc.
Cam Files
- For maximum clarity, provide cam files with preview images of all layers overlaid.
Zip Archives
- Compress all files into a single ZIP archive for easy transfer.
Following best practices for your design file preparation prevents back and forth and avoids potential delays.
Leveraging Advanced Manufacturing Techniques
To achieve the fastest possible turnaround times, partner with a manufacturer utilizing advanced build processes. Here are some key techniques:
Direct Imaging (DI): This lithography method images the layout pattern directly without a physical mask. It enhances line width control and reduces steps.
Automated Optical Inspection (AOI): AOI systems use cameras to automatically scan boards and verify quality against the CAD design. This eliminates human inspection error and speeds testing.
Automated Testing: Automated testing systems check continuity, resistance, voltage, and other electrical parameters through test probes. This accelerates validation.
Intelligent Storage: Smart warehouses with automated storage and retrieval systems maximize efficiency in retrieving materials and inventoried boards.
Direct Ordering: Web platforms that allow customers to directly order boards 24/7 can facilitate faster ordering and production starts.
Shift Scaling: Manufacturers who intelligently scale staff and machinery across multiple shifts enable round-the-clock production.
The more automation and intelligence incorporated into manufacturing, the faster PCBs can be delivered.
Panelization for Efficient Prototyping
For fastest production of prototypes, consider panelization. This involves arranging multiple PCB designs onto a larger panel to be manufactured simultaneously:
[Diagram of panelization]
Panelization maximizes board surface area use, streamlines assembly steps, and avoids setup/changeover between boards. Benefits include:
- Faster processing: More boards produced per production run
- Lower costs: Shared setup costs across panelized boards
- Quality consistency: Assembly conditions kept constant across panel
- Material savings: More efficient material utilization with less waste
For prototyping quantities under 50 units, panelization can cut production time by 50% or more. Just be sure to partner with an experienced manufacturer used to panelization.
Maintaining Open Communication
Clear ongoing communication with your PCB manufacturer is imperative to getting boards produced rapidly. Be proactive with:
Project Expectations
- Set clear expectations up front around deliverables, quantities, and lead times. Agree on terms.
Design Reviews
- Encourage reviews of your design files to catch potential manufacturability issues early.
Progress Updates
- Check in periodically for updates on production status, expected completion, etc.
Priority Flags
- Flag orders as high priority so manufacturers allocate resources accordingly.
Issue Resolution
- If delays arise, discuss options with your manufacturer to get back on track.
With good communication and alignment, manufacturers can take action to expedite throughput and deliver your boards faster.
Getting Functional Prototypes
For the fastest possible functioning prototypes:
Simplify Designs
- Avoid complex multilayer boards and stick to 2-4 layers if possible during prototyping.
Use 0402 or Larger Components
- Smaller 0201 and 01005 components prolong SMT assembly.
Request Solder Samples
- Have a small batch wave/reflow soldered to test solderability before full assembly.
Forgo Lead Handling
- Skip lead patterning or careful lead cutting to optimize throughput.
Use Test Points
- Include test points to facilitate validation rather than relying solely on probes.
Let Functionality Suffice
- The goal is working prototypes – aesthetics like solder masking can wait.
Prioritizing functionality over final production-level quality cuts lead times.
Summary
Quick PCB turnarounds require careful planning and execution:
- Prepare design files properly and partner with a capable manufacturer
- Use advanced manufacturing techniques like DI and AOI
- Utilize panelization for fastest prototyping
- Communicate frequently and set clear expectations
- Focus on core functionality over aesthetics
With the right approach, you can slash weeks or even months off your PCB production schedules. Fast turnaround supports rapid development cycles and quicker time to market – giving your company a key competitive advantage.
Fast Turn PCBs Frequently Asked Questions
Here are some common questions around fast turn PCB production:
Q: How much more does expedited PCB production typically cost versus standard turn times?
A: Expedited services typically range from 1.5X to 2X the cost of standard turn times. Ultra-expedited 24-48 hour services can be 3X standard costs or more.
Q: What is the main benefit of using a local PCB manufacturer versus one located overseas?
A: Local manufacturers minimize shipping times. For fastest turnarounds, avoiding overseas shipping lags is optimal. Communication can also be easier with local vendors.
Q: What manufacturing techniques allow the fastest PCB fabrication?
A: Direct imaging (DI) eliminates the traditional masking process, while automated optical inspection (AOI) accelerates quality verification. Both significantly reduce production time.
Q: How many PCBs are typically panelized together for prototyping?
A: Smaller quantities of 3-12 boards are common for panelization. This achieves efficiency gains without excessive material waste.
Q: Can PCB manufacturers deliver on extremely aggressive 24-48 hour lead times?
A: Manufacturers specializing in prototyping and equipped with quick-turn capabilities can often accommodate 1-2 day lead times, albeit for an additional fee.
0 Comments