Introduction
For electronics designers and engineers, getting prototype printed circuit boards (PCBs) built and assembled quickly is often critically important. When you’re trying to validate a new design or get first articles built for a new product introduction (NPI), delays in PCB prototyping can hamper the development schedule. This article will examine techniques for fast turn PCB assembly when you need boards fabricated and assembled in just a few days.
What is Fast Turn PCB Assembly?
Fast turn PCB assembly refers to the process of taking a new circuit board design from layout files to fully assembled boards in an extremely compressed timeframe—typically 5 days or less. This rapid timeline is enabled by quick-turn fabrication services combined with specialized assembly techniques to populate the boards swiftly.
For fast turn needs, fabrication and assembly steps are streamlined:
- PCB Fabrication – Using quick-turn fabrication processes, bare PCBs can be manufactured in 1-2 days in North America or 3 days in Asia. Quick-turn shops keep certain materials stocked for faster laminate and through-hole plating.
- PCB Assembly – With fabricated boards in hand, assembly can be completed in 1-3 days using specialized techniques like advanced stencil designs, continuous flow soldering, and multishift operations. Programming for automated assembly is expedited.
- Testing – Rapid testing validates assembly and functionality. Automated optical inspection and flying probe testing provide fast results.
With streamlined fabrication, assembly, and testing, designers can have fully functioning board prototypes built and delivered within 5 days or less.
Why Fast Turnaround is Important
For many electronics projects, getting working PCB prototypes built quickly is extremely beneficial:
- Accelerate development schedules – Fast turn assembly enables testing design revisions and new product concepts rapidly. Quickly iterating on hardware accelerates overall development timelines.
- Meet critical deadlines – For startups and established companies alike, fast prototyping can help hit make-or-break deadlines to ship products on schedule.
- Respond to priorities – Getting working boards fast is key when issues emerge that require urgent design modifications or replacements.
- Seize market opportunities – Being first to market with an innovative product can hinge on rapid prototyping speed.
- Shorten sales cycles – Having actual boards to show customers helps close sales faster. Fast turn enables demos, evaluators and pilots.
For these reasons, the ability to turn PCB layouts into functioning boards within 5 days or less is an invaluable asset for many design teams.
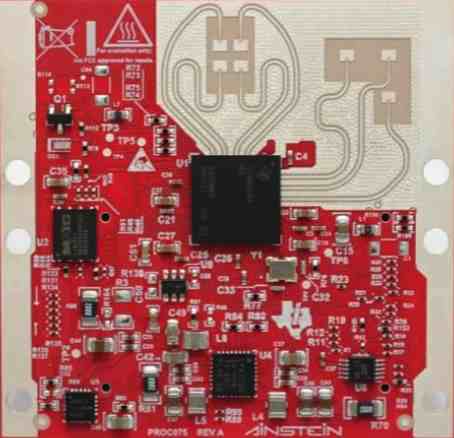
Challenges of Fast Turn Assembly
While fast turn PCB assembly provides huge benefits, it also poses some unique challenges:
- Increased costs – Expedited services at every stage drive up costs, often 2X-5X a typical schedule. It must provide enough value to justify premium pricing.
- Materials limitations – Some advanced PCB materials like Rogers laminates cannot be fabricated overnight. Fast turn is largely limited to FR-4 boards.
- Tighter tolerances – With less time in fabrication, some parameters like minimum trace/space get tighter. Designs may require adjustments.
- Assembly surprises – Rapid build-out can increase chances of unforeseen assembly issues emerging with component choice, BOMs, etc.
- Testing tradeoffs – Accelerated testing focuses on functionality more than long-term reliability. Some issues may be missed.
- Logistical hurdles – Getting boards fabricated and shipped across continents complicates an already tight timeline.
While rewarding when done right, fast turn PCB projects require careful planning plus close coordination between designers, assemblers, and testers to address these challenges.
Key Strategies for Fast Turn Success
To maximize the likelihood of executing fast turn PCB assembly successfully, designers should:
1. Engage assembler early in design phase
Involving the assembly partner early is crucial. The assembler can assess design manufacturability, recommend parts for availability, and plan rapid programming and build processes. Early engagement minimizes potential issues.
2. Design with fast turn constraints in mind
Factors like minimum trace/space, component spacing, and ease of assembly should be considered from the outset for a smooth fast turn build. SMT over through hole parts help speed assembly.
3. Use components geared for fast turn
Choose common, non-obsolete parts that assemblers can quickly source. Avoid hard-to-get components or long lead times. Leverage assembler stock for fastest availability.
4. Validate BOMs carefully
Scrutinize BOMs and component data for missing information that could cause delays. Confirm quantities, reference designators, pin counts, packaging, etc.
5. Build in margin to allow for fixes
For complex or high-value boards, budgeting extra time upfront is wise. This accounts for potential last-minute design modifications requiring PCB respins.
6. Plan for expedited PCB shipping
Using express shipping (e.g. DHL, FedEx) ensures bare boards move rapidly between fabrication, assembly, and delivery sites across continents.
7. Optimize testing for functionality
Focus testing on validating core functionality quickly rather than comprehensive long-term testing. Rely on visual inspection, flying probe, and functionally focused scripts.
By applying these best practices, design teams can effectively leverage fast turn assembly services while avoiding common pitfalls.
Fast Turn Assembly Process Step-By-Step
To provide a better understanding of how fast turn PCB assembly can reliably be completed within 5 days or less, let’s walk through the accelerated process in stages:
Day 1
- Customer places order for fast turn assembly of new PCB design and uploads Gerber, BOM, placement, etc. files to assembler’s site
- Assembler reviews design files and component requirements for manufacturability and availability
- PCB fabrication shop is engaged for next day quick-turn fabrication based on completed design files
- Solder stencils are designed by the assembler and ordered for next day delivery
Day 2
- Bare PCBs are fabricated overnight and shipped via express courier to assembler
- Components are sourced from assembler’s local stock and/or ordered for rapid delivery
- Solder stencils arrive at assembly facility
- Assembly program is generated, optimized for rapid process flow
Day 3
- Components arrive at assembly site for immediate use
- Ad hoc SMT programming modifications are implemented as needed
- SMT machine is programmed for accelerated changeovers between small batches
- SMT board population is completed in a single shift with quick changeovers
Day 4
- SMT boards proceed to wash, AOI optical inspection, and reflow stages
- Through-hole components are hand-inserted as needed
- Loaded boards undergo automated flying probe test sequence
- Covers and labels are added to finished assemblies
- Final packaged boards ship to customer for delivery on day 5
Day 5
- Assembled board prototypes are received by customer ready for verification and testing
This coordinated fast turn process combines purpose-built manufacturing stages enable fully assembled boards in 5 days or less.
Examples of 5 Day Turnaround Successes
To make fast PCB assembly more tangible, here are some real-world examples of companies leveraging 5 day turn services successfully:
- An IoT startup needed to prototype a new wireless sensing device before a big trade show. 5 day assembly enabled them to have working boards to showcase at the event.
- A medical equipment maker had an urgent field safety issue requiring PCB redesign and replacement parts for 500 units. Fast turn assembly got them new board revs built in under a week.
- A robotics firm beat out three competitors to win a large contract by demonstrating their working prototype built using 5 day assembly.
- A consumer electronics company utilized quick-turn services to evaluate multiple design variations for a new media player remote control.
- A defense contractor responded to a new tender request by building a radar sensor prototype for evaluation in less than a week.
For each of these companies, fast turn PCB assembly was instrumental in meeting their objectives under tight deadlines and constraints.
Cost Considerations for Fast Turn PCB Projects
Because of the additional labor, expedited materials, and premium services required at every stage, fast turn PCB assembly comes at a significantly higher cost than standard turn times of ~2-3 weeks. Some guidelines on costs:
- 5 day turn assembly typically costs 2X to 5X the price of standard assembly for the same boards.
- Exact cost premium depends on complexity, board size, BOM, and other variables.
- NRE costs are higher for stencils, programming, testing setup, etc.
- Expedited component procurement, shipping, and handling all add cost.
- Economies of scale don’t apply; per unit pricing is higher.
- Assemblers often charge rush fees on shorter turnaround times.
The accelerated timeline enables prototypes to be built in days rather than weeks. The associated urgent delivery value usually justifies the higher price point for most fast turn customers.
Fast Turn PCB Assembly Checklist
To recap the best practices that contribute to successful rapid prototyping projects:
- Engage assembler early in design stage for design review and planning
- Review requirements like minimum dimensions and parts selection
- Use standard components that are readily available
- Validate BOM completely to minimize errors
- Build in schedule buffer for potential respins if possible
- Confirm logistics plan for fastest materials transport
- Focus testing on core functionality validation
- Get pricing to confirm budget for premium service fees
By following this fast turn PCB assembly checklist, product developers can avoid roadblocks and achieve working board prototypes in 5 days or less.
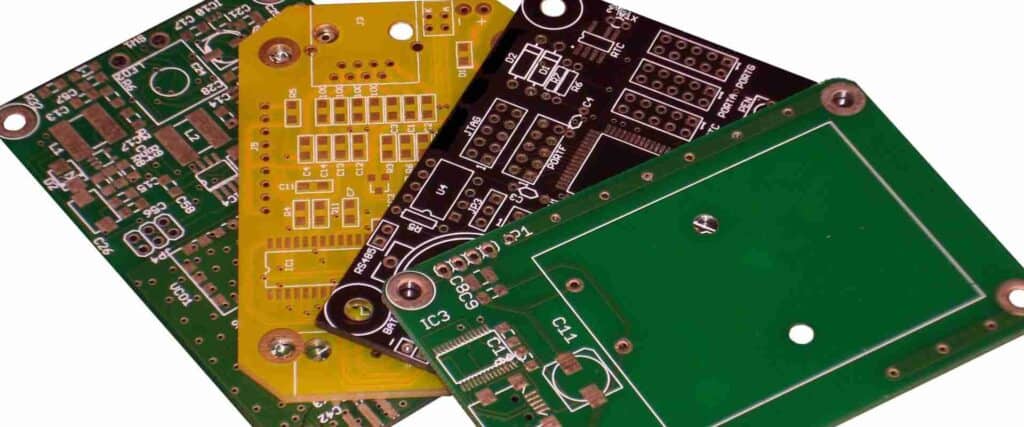
Frequently Asked Questions
Here are some common questions about fast turn PCB assembly and rapid prototyping:
Q: How many PCBs are needed to justify 5 day turn assembly?
A typical 5 day turn order might range from 5 to 30 assembled boards, though more or less could be accommodated. The key factors are the urgency and the value of having prototypes days faster.
Q: Can fast turn support double-sided or multilayer designs?
Yes, fast turn processes support 2-layer (doublesided) and multilayer boards equally well. Complexity does not limit the ability to do 5 day assembly.
Q: What size boards can be assembled in 5 days?
Most SMT assemblers can support board sizes up to 18” x 24” in a 5 day fast turn scenario. Larger or smaller boards can also be accommodated.
Q: Can through-hole components be used in fast turn assembly?
While SMT-only designs are easiest for rapid assembly, through-hole parts can certainly be supported on fast turn boards in combination with SMT.
Q: How are yields/quality affected by the accelerated timeline?
With careful design and assembly practices, yields can match standard turn assembly. The focus shifts from long-term reliability testing to validating functionality quickly.
Conclusion
Fast turn PCB assembly enables engineers to transform designs into working prototypes in 5 days or less. While requiring careful planning, coordination, and budget, rapid prototyping generates huge value through accelerated development, field validation, and time-to-market. By partnering with an experienced quick-turn assembler and applying the strategies outlined here, product teams can slash critical path timelines and achieve more in compressed schedules.
0 Comments