Introduction to PCB fabrication
Printed Circuit Board (PCB) fabrication is a crucial process in the electronics industry, enabling the creation of complex circuits on a single board. The process involves several steps, from design to manufacturing, ensuring that the final product meets the required specifications and standards. In this article, we will explore the various aspects of fast and quality PCB fabrication, including the key steps involved, the materials used, and the techniques employed to achieve optimal results.
The PCB Fabrication Process
Step 1: PCB Design
The first step in PCB fabrication is the design phase. This involves creating a schematic diagram of the circuit, which is then translated into a physical layout using specialized PCB design software. The layout includes the placement of components, traces, and vias, as well as any necessary markings or labels.
Step 2: Material Selection
Once the design is finalized, the next step is to select the appropriate materials for the PCB. The most common material used for PCBs is FR-4, a glass-reinforced epoxy laminate. Other materials, such as polyimide or ceramic, may be used for high-temperature or high-frequency applications.
Step 3: Copper Cladding
The selected material is then clad with a thin layer of copper on one or both sides, depending on the design requirements. The copper layer serves as the conductive pathway for the electrical signals in the circuit.
Step 4: Drilling
After the copper cladding, the PCB undergoes a drilling process to create holes for through-hole components and vias. The drilling is performed using high-speed CNC machines, ensuring precise and accurate hole placement.
Step 5: Patterning
The next step is to create the desired circuit pattern on the copper layer. This is typically done using a photolithography process, where a photoresist layer is applied to the copper, exposed to UV light through a mask, and then developed to reveal the desired pattern.
Step 6: Etching
Once the pattern is created, the unwanted copper is removed through an etching process. The most common method is chemical etching, where the PCB is immersed in an etchant solution that selectively removes the exposed copper, leaving behind the desired circuit pattern.
Step 7: Plating
After etching, the PCB may undergo additional plating processes, such as electroless nickel/immersion gold (ENIG) or hot air solder leveling (HASL), to improve the solderability and durability of the exposed copper surfaces.
Step 8: Solder Mask Application
A solder mask layer is then applied to the PCB to protect the copper traces from oxidation and to prevent Solder Bridging during the assembly process. The solder mask is typically a green or black polymer coating that is applied using a screen printing or photoimaging process.
Step 9: Silkscreen Printing
The final step in the PCB fabrication process is the application of silkscreen markings, such as component designators, logos, or text. This is done using a screen printing process, similar to the solder mask application.
Materials Used in PCB Fabrication
Material | Description | Applications |
---|---|---|
FR-4 | Glass-reinforced epoxy laminate | General-purpose PCBs |
Polyimide | High-temperature resistant polymer | Aerospace, automotive, and military |
Ceramic | High-frequency and high-temperature resistant | RF and microwave circuits |
Aluminum | Excellent thermal conductivity | LED lighting and power electronics |
Copper | Conductive material for traces and vias | All PCBs |
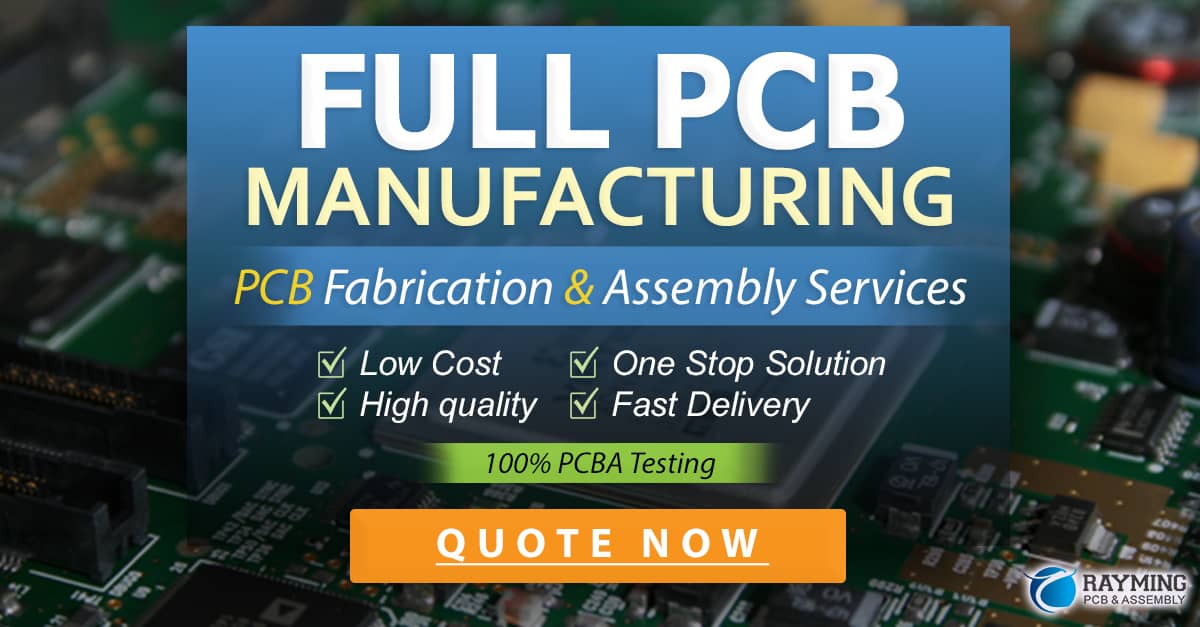
Techniques for Fast and Quality PCB Fabrication
High-Speed Drilling
To achieve fast and accurate drilling, modern PCB fabrication facilities employ high-speed CNC machines with multiple spindles. These machines can drill thousands of holes per minute, significantly reducing the overall fabrication time.
Laser Drilling
For smaller hole sizes and higher precision, laser drilling is used. This technique uses a focused laser beam to vaporize the material, creating holes as small as 50 microns in diameter. Laser drilling is particularly useful for high-density interconnect (HDI) PCBs.
Direct Imaging
Direct imaging is a photolithography technique that eliminates the need for a physical mask. Instead, a digital image of the circuit pattern is directly projected onto the photoresist-coated copper layer. This method reduces the setup time and improves the accuracy of the patterning process.
Automated Optical Inspection (AOI)
AOI systems are used to inspect the PCBs for defects, such as missing components, incorrect polarity, or solder bridging. These systems use high-resolution cameras and advanced image processing algorithms to quickly and accurately detect any issues, ensuring the quality of the final product.
Inline Testing
Inline testing is performed at various stages of the PCB fabrication process to catch any defects early on. This includes electrical testing, such as continuity and insulation resistance tests, as well as visual inspections for surface defects or contaminants.
Benefits of Fast and Quality PCB Fabrication
- Reduced time-to-market for new products
- Lower manufacturing costs due to fewer defects and rework
- Improved reliability and performance of the final product
- Enhanced customer satisfaction and brand reputation
Challenges in PCB Fabrication
Despite the advancements in technology and processes, PCB fabrication still faces several challenges, including:
-
Miniaturization: As electronic devices become smaller and more compact, the demand for high-density PCBs with finer feature sizes increases. This requires more advanced fabrication techniques and tighter tolerances.
-
Material selection: Choosing the right material for a specific application can be challenging, as each material has its own set of properties and limitations. Factors such as thermal stability, dielectric constant, and moisture resistance must be considered.
-
Environmental concerns: The chemicals used in PCB fabrication, such as etchants and solvents, can have a negative impact on the environment if not properly handled and disposed of. Manufacturers must adhere to strict environmental regulations and implement eco-friendly practices.
-
Supply chain management: Ensuring a stable and reliable supply of raw materials, components, and equipment is crucial for maintaining fast and quality PCB fabrication. Disruptions in the supply chain can lead to delays and increased costs.
Future Trends in PCB Fabrication
As the electronics industry continues to evolve, so does PCB fabrication. Some of the future trends in this field include:
-
3D printing: Additive manufacturing techniques, such as 3D printing, are being explored for creating complex, three-dimensional PCB structures. This could enable the fabrication of more compact and lightweight devices.
-
Embedded components: Integrating components, such as resistors, capacitors, and even active devices, directly into the PCB Substrate can save space and improve performance. This trend is expected to gain more traction in the coming years.
-
Flexible and stretchable PCBs: The demand for wearable and flexible electronics is driving the development of flexible and stretchable PCBs. These boards can conform to various shapes and withstand repeated bending and stretching without losing functionality.
-
Sustainable materials: As environmental concerns continue to grow, there is a push towards using more sustainable and recyclable materials in PCB fabrication. This includes the use of biodegradable substrates, Lead-free Solders, and halogen-free flame retardants.
Frequently Asked Questions (FAQ)
1. What is the typical turnaround time for PCB fabrication?
The turnaround time for PCB fabrication varies depending on the complexity of the design, the materials used, and the manufacturing capabilities of the fabrication facility. For standard PCBs, the turnaround time can range from 1-2 weeks, while more complex designs or large quantities may take several weeks.
2. What is the minimum feature size achievable in PCB fabrication?
The minimum feature size in PCB fabrication depends on the manufacturing process and the equipment used. For standard PCBs, the minimum trace width and spacing is typically around 0.1 mm (4 mil). However, with advanced techniques like HDI and laser drilling, feature sizes as small as 0.05 mm (2 mil) or less can be achieved.
3. How do I choose the right material for my PCB?
Choosing the right material for your PCB depends on several factors, including the application, the operating environment, and the desired performance characteristics. Consider the following properties when selecting a material:
– Thermal stability
– Dielectric constant
– Moisture resistance
– Mechanical strength
– Cost
Consult with your PCB fabrication partner or a material expert to determine the best material for your specific requirements.
4. What is the difference between surface mount and through-hole components?
Surface mount components are mounted directly onto the surface of the PCB, while through-hole components have leads that are inserted into holes drilled in the board and soldered on the opposite side. Surface mount technology (SMT) allows for smaller component sizes and higher component density, while through-hole technology offers better mechanical stability and is easier to assemble manually.
5. How can I ensure the quality of my PCB fabrication?
To ensure the quality of your PCB fabrication, consider the following tips:
– Choose a reputable and experienced PCB fabrication partner
– Provide clear and detailed design files, including Gerber files and drill files
– Specify your requirements for material, finish, and tolerances
– Request a design for manufacturability (DFM) review before proceeding with fabrication
– Perform thorough testing and inspection of the fabricated PCBs, including electrical, mechanical, and visual tests
Conclusion
Fast and quality PCB fabrication is essential for the success of any electronic product. By understanding the key steps involved, the materials used, and the techniques employed, designers and manufacturers can optimize the fabrication process to achieve the best possible results. As the electronics industry continues to evolve, staying up-to-date with the latest trends and technologies in PCB fabrication will be crucial for staying competitive in the market.
0 Comments