What is Duroid?
Duroid is a brand name for a family of high-performance PCB laminates manufactured by Rogers Corporation. These laminates are composed of polytetrafluoroethylene (PTFE) reinforced with glass microfibers, resulting in a material with excellent dielectric properties, low dissipation factor, and high thermal stability.
Some of the most popular Duroid laminates include:
- RT/duroid® 5870 – 5880
- RT/duroid® 6002 – 6202
- RT/duroid® 6006 – 6010LM
- RO3000® Series
- RO4000® Series
Each of these laminates has unique properties that cater to specific applications, such as high-speed digital, RF and microwave, and military and aerospace systems.
Advantages of Duroid PCBs
Duroid PCBs offer several advantages over traditional FR-4 based PCBs, making them the preferred choice for high-frequency and microwave applications. Some of these advantages include:
-
Low Dielectric Constant and Dissipation Factor: Duroid materials have a low dielectric constant (Dk) and dissipation factor (Df), which minimizes signal loss and ensures signal integrity at high frequencies.
-
High Thermal Stability: Duroid laminates maintain their electrical properties over a wide temperature range, making them suitable for applications that require operation in extreme environments.
-
Excellent Mechanical Properties: Duroid PCBs have good mechanical strength and dimensional stability, enabling them to withstand the rigors of manufacturing and handling.
-
Low Moisture Absorption: Unlike FR-4, Duroid laminates have low moisture absorption, which helps maintain their electrical properties even in humid conditions.
-
Controlled Impedance: Duroid PCBs can be easily fabricated with controlled impedance traces, ensuring consistent signal propagation and minimizing reflections.
Duroid PCB Manufacturers
Several PCB manufacturers specialize in fabricating Duroid PCBs. These manufacturers have the expertise, equipment, and processes in place to handle the unique challenges associated with working with Duroid materials. Some of the top Duroid PCB manufacturers include:
-
Advanced Circuits: With over 30 years of experience, Advanced Circuits is a leading PCB manufacturer that offers Duroid PCB fabrication services. They have the capability to produce Duroid PCBs with controlled impedance, blind and buried vias, and fine pitch traces.
-
Bay Area Circuits: Bay Area Circuits specializes in quick-turn and prototype Duroid PCB fabrication. They offer a wide range of Duroid materials and can fabricate PCBs with complex features and tight tolerances.
-
Sierra Circuits: Sierra Circuits is a full-service PCB manufacturer that offers Duroid PCB fabrication services. They have experience working with various Duroid laminates and can provide design assistance to optimize PCB performance.
-
Sunstone Circuits: Sunstone Circuits is a well-known PCB Prototype manufacturer that also offers Duroid PCB fabrication. They have a streamlined process for quick-turn Duroid PCBs and offer competitive pricing.
-
Candor Industries: Candor Industries is a leading Duroid PCB manufacturer with state-of-the-art facilities in the United States and Asia. They specialize in high-complexity, high-reliability Duroid PCBs for demanding applications.
These manufacturers have the necessary certifications, such as ISO 9001, AS9100D, and ITAR registration, ensuring that they adhere to stringent quality standards and can cater to various industries, including aerospace, defense, and telecommunications.
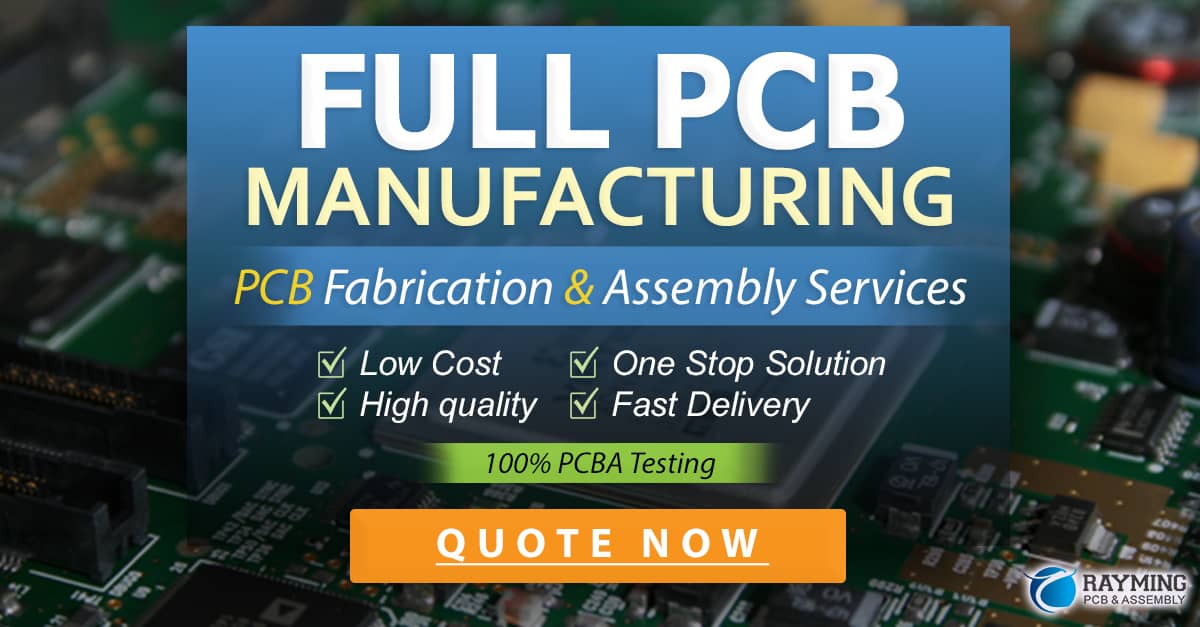
Choosing the Right Duroid PCB Manufacturer
When selecting a Duroid PCB manufacturer, there are several factors to consider to ensure that you receive high-quality PCBs that meet your specific requirements. Some of these factors include:
-
Experience: Choose a manufacturer with extensive experience in fabricating Duroid PCBs. They should have a thorough understanding of the unique properties of Duroid materials and the best practices for handling them.
-
Capabilities: Ensure that the manufacturer has the necessary equipment and processes in place to fabricate PCBs with the features and specifications you require, such as controlled impedance, blind and buried vias, and fine pitch traces.
-
Quality Control: Look for a manufacturer with a robust quality control system in place. They should have a well-documented process for inspecting PCBs at various stages of fabrication and should be able to provide test reports and certificates of conformance.
-
Customer Support: Choose a manufacturer that offers excellent customer support and can provide technical assistance when needed. They should be responsive to your queries and be willing to work closely with you to ensure that your PCBs meet your expectations.
-
Pricing and Lead Times: While price is an important consideration, it should not be the sole deciding factor. Look for a manufacturer that offers competitive pricing without compromising on quality. Additionally, ensure that they can meet your lead time requirements, especially for time-sensitive projects.
Designing Duroid PCBs
Designing Duroid PCBs requires careful consideration of the unique properties of Duroid materials. Designers must take into account factors such as dielectric constant, dissipation factor, and thermal expansion to ensure optimal performance and reliability.
Some best practices for designing Duroid PCBs include:
-
Material Selection: Choose the appropriate Duroid laminate based on the electrical, mechanical, and thermal requirements of your application. Consult with your PCB manufacturer to select the best material for your needs.
-
Controlled Impedance: Design controlled impedance traces to maintain signal integrity and minimize reflections. Work closely with your PCB manufacturer to ensure that the PCB stackup and trace geometries are optimized for controlled impedance.
-
Thermal Management: Consider the thermal properties of Duroid materials when designing your PCB. Ensure that there is adequate heat dissipation and that the PCB layout minimizes thermal stress on components.
-
Via Design: Pay attention to via design, especially when working with high-frequency signals. Use appropriate via sizes and spacing to minimize signal loss and maintain signal integrity.
-
Manufacturing Considerations: Design your PCB with manufacturability in mind. Follow your manufacturer’s design guidelines for minimum trace width and spacing, hole sizes, and other fabrication constraints to ensure that your PCB can be manufactured reliably and cost-effectively.
Duroid PCB Applications
Duroid PCBs find applications in various industries and systems that require high performance and reliability. Some of these applications include:
-
Wireless Communications: Duroid PCBs are widely used in wireless communication systems, such as cellular base stations, satellite communications, and radar systems. They provide low signal loss and high signal integrity, enabling efficient and reliable data transmission.
-
Aerospace and Defense: The excellent thermal stability and low moisture absorption of Duroid materials make them ideal for aerospace and defense applications. Duroid PCBs are used in avionics, missile guidance systems, and other mission-critical systems that require operation in harsh environments.
-
Automotive Radar: With the increasing adoption of advanced driver assistance systems (ADAS) and autonomous vehicles, automotive radar systems are becoming more prevalent. Duroid PCBs are used in these systems due to their low dielectric constant and dissipation factor, which enable high-resolution and long-range radar performance.
-
Medical Imaging: Duroid PCBs are used in medical imaging systems, such as MRI and CT scanners. They provide low signal loss and high signal integrity, enabling high-quality image acquisition and processing.
-
Test and Measurement: High-frequency test and measurement equipment, such as oscilloscopes, spectrum analyzers, and network analyzers, rely on Duroid PCBs for accurate and reliable signal propagation.
Duroid PCB Manufacturing Process
The manufacturing process for Duroid PCBs is similar to that of traditional FR-4 PCBs, with a few key differences. The main steps involved in Duroid PCB manufacturing are:
-
Material Preparation: The Duroid laminates are cut to size and cleaned to remove any contaminants. The laminates are then baked to remove moisture and stabilize their dimensions.
-
Drilling: Holes are drilled into the laminates for vias, component mounting, and tooling. Due to the softness of Duroid materials, special drill bits and parameters are used to minimize burrs and ensure clean hole walls.
-
Plating: The drilled holes are plated with copper to create electrical connections between layers. The plating process for Duroid PCBs requires careful control of the plating chemistry and parameters to ensure good adhesion and coverage.
-
Patterning: The copper layers are patterned using photolithography and etching to create the desired circuit traces and pads. The etching process for Duroid PCBs requires careful control of the etchant concentration and temperature to ensure precise and consistent results.
-
Solder Mask and Silkscreen: A solder mask is applied to the PCB to protect the copper traces and prevent solder bridging. A silkscreen layer is then applied to provide component labels and other markings.
-
Surface Finish: A surface finish, such as ENIG (Electroless Nickel Immersion Gold) or HASL (Hot Air Solder Leveling), is applied to the exposed copper areas to prevent oxidation and improve solderability.
-
Electrical Testing: The finished PCBs are electrically tested to ensure that they meet the specified performance requirements. This includes tests for continuity, insulation resistance, and controlled impedance.
Throughout the manufacturing process, strict quality control measures are implemented to ensure that the PCBs meet the required specifications and are free from defects.
Challenges in Duroid PCB Manufacturing
While Duroid PCBs offer numerous advantages, they also present some unique challenges in manufacturing. Some of these challenges include:
-
Material Handling: Duroid laminates are softer and more flexible than traditional FR-4 laminates, making them more susceptible to damage during handling. Special care must be taken to avoid scratches, dings, and other defects that can affect the electrical performance of the PCB.
-
Drilling: Due to the softness of Duroid materials, drilling can be challenging. Special drill bits and parameters must be used to minimize burrs and ensure clean hole walls. Additionally, the low thermal conductivity of Duroid materials can cause heat buildup during drilling, leading to smearing and other defects.
-
Plating: The low surface energy of Duroid materials can make it difficult to achieve good adhesion and coverage during the plating process. Special plating chemistries and process controls are required to ensure reliable plating.
-
Etching: The low thermal conductivity of Duroid materials can cause uneven heat distribution during etching, leading to over-etching or under-etching. Careful control of the etchant concentration and temperature is necessary to achieve precise and consistent results.
-
Impedance Control: Achieving precise impedance control on Duroid PCBs can be challenging due to the material’s unique dielectric properties. Designers and manufacturers must work closely together to ensure that the PCB stackup and trace geometries are optimized for the desired impedance.
Despite these challenges, experienced Duroid PCB manufacturers have developed specialized processes and controls to mitigate these issues and consistently produce high-quality PCBs.
Frequently Asked Questions (FAQ)
- Q: What is the lead time for Duroid PCBs?
A: The lead time for Duroid PCBs depends on various factors, such as the complexity of the design, the manufacturing process, and the manufacturer’s workload. Typical lead times range from 2-4 weeks for standard designs and can be longer for more complex designs or large quantities. Some manufacturers offer expedited services for shorter lead times.
- Q: How much do Duroid PCBs cost compared to FR-4 PCBs?
A: Duroid PCBs are generally more expensive than FR-4 PCBs due to the higher cost of Duroid materials and the specialized manufacturing processes required. The exact cost difference depends on factors such as the PCB size, layer count, and quantity. On average, Duroid PCBs can cost 2-3 times more than equivalent FR-4 PCBs.
- Q: Can Duroid PCBs be assembled using standard SMT processes?
A: Yes, Duroid PCBs can be assembled using standard surface mount technology (SMT) processes. However, due to the unique properties of Duroid materials, some adjustments to the assembly process may be necessary. For example, the reflow profile may need to be optimized to account for the low thermal conductivity of Duroid materials, and special handling precautions may be required to avoid damaging the PCB.
- Q: Are there any limitations on the minimum feature sizes that can be achieved with Duroid PCBs?
A: The minimum feature sizes that can be achieved with Duroid PCBs depend on the specific Duroid material and the capabilities of the PCB manufacturer. In general, Duroid PCBs can achieve trace widths and spacings down to 3-4 mils (0.075-0.1 mm) and via diameters down to 8-10 mils (0.2-0.25 mm). However, achieving these feature sizes requires careful design and process control, and may not be feasible for all designs.
- Q: Can Duroid PCBs be used for high-power applications?
A: Yes, Duroid PCBs can be used for high-power applications, but careful consideration must be given to the thermal management of the PCB. Duroid materials have low thermal conductivity, which can lead to heat buildup in high-power circuits. To mitigate this, designers can use thicker copper layers, larger trace widths, and additional thermal vias to improve heat dissipation. Additionally, external heat sinking and cooling solutions may be necessary for particularly high-power applications.
Conclusion
Duroid PCBs are a crucial component in many high-frequency and microwave applications, offering superior electrical properties and reliability compared to traditional FR-4 PCBs. Duroid PCB manufacturers play a vital role in enabling these applications by providing specialized fabrication services that cater to the unique properties of Duroid materials.
When selecting a Duroid PCB manufacturer, it is essential to consider factors such as experience, capabilities, quality control, customer support, and pricing. By partnering with a reputable manufacturer and following best practices for designing and manufacturing Duroid PCBs, designers can ensure that their PCBs meet the demanding requirements of their applications.
As the demand for high-performance electronic systems continues to grow, the role of Duroid PCBs and Duroid PCB manufacturers will become increasingly important. By staying at the forefront of material science and manufacturing technologies, Duroid PCB manufacturers will continue to enable innovation and push the boundaries of what is possible in the world of high-frequency and microwave electronics.
0 Comments