What is Differential trace impedance?
Differential trace impedance is a critical aspect of high-speed PCB design, especially in applications involving differential signaling. It refers to the impedance between two traces carrying differential signals, which are equal in magnitude but opposite in polarity. Maintaining a consistent differential impedance throughout the length of the traces is essential for ensuring signal integrity and minimizing reflections, crosstalk, and electromagnetic interference (EMI).
In a typical PCB Stackup, differential traces are routed over a reference plane, such as a ground or power plane, which helps to control the impedance and provide shielding. However, in some cases, it may be necessary to route differential traces without a reference plane, either due to design constraints or the absence of a continuous reference plane in the stackup. This scenario presents unique challenges in managing differential trace impedance.
Factors Affecting Differential Trace Impedance
Several factors influence the differential trace impedance, including:
- Trace width and spacing
- Dielectric Constant (Dk) of the PCB material
- Thickness of the dielectric layer
- Presence of a reference plane
- Frequency of the signal
When routing differential traces without a reference plane, the lack of a consistent return path and the absence of shielding can lead to impedance discontinuities, increased crosstalk, and EMI issues.
Challenges in Managing Differential Trace Impedance Without Reference Plane
Inconsistent Return Path
In the absence of a reference plane, the return current for differential signals must find an alternative path. This can lead to an inconsistent return path, causing impedance variations along the length of the traces. The return current may flow through adjacent traces, power planes, or even through the air, depending on the geometry and proximity of other conductors.
Increased Crosstalk
Without the shielding provided by a reference plane, differential traces are more susceptible to crosstalk from nearby signals. The coupling between traces can lead to signal degradation, jitter, and bit errors, especially at high frequencies.
Electromagnetic Interference (EMI)
Differential traces without a reference plane are more likely to radiate electromagnetic energy, contributing to EMI. The lack of shielding allows the electric and magnetic fields to escape from the traces, potentially interfering with other components or systems.
Techniques for Managing Differential Trace Impedance Without Reference Plane
Despite the challenges, there are several techniques that can help manage differential trace impedance in the absence of a reference plane:
1. Increasing Trace Spacing
One way to mitigate the impact of the missing reference plane is to increase the spacing between differential traces. By increasing the distance between the traces, the coupling between them is reduced, helping to maintain a more consistent impedance and reduce crosstalk.
Trace Spacing | Relative Impedance Change |
---|---|
2 x Trace Width | Baseline |
3 x Trace Width | -5% to -10% |
4 x Trace Width | -10% to -20% |
Table 1: Impact of increasing trace spacing on differential impedance.
2. Using Shielding Traces
Another technique is to use shielding traces alongside the differential pairs. These shielding traces, also known as guard traces, are placed on either side of the differential traces and are connected to a stable reference, such as ground. The shielding traces help to confine the electric and magnetic fields, reducing crosstalk and EMI.
Shielding Trace Width | Relative Crosstalk Reduction |
---|---|
0.5 x Differential Trace Width | -3 dB to -6 dB |
1.0 x Differential Trace Width | -6 dB to -10 dB |
1.5 x Differential Trace Width | -10 dB to -15 dB |
Table 2: Impact of shielding trace width on crosstalk reduction.
3. Minimizing Discontinuities
Impedance discontinuities can occur when differential traces encounter changes in geometry, such as bends, vias, or transitions between layers. To minimize these discontinuities, it is important to follow good PCB Layout practices:
- Use smooth, gradual bends instead of sharp corners
- Avoid unnecessary layer transitions
- Match the trace width and spacing when transitioning between layers
- Use differential vias with identical geometry and spacing
4. Employing Impedance-Controlled Dielectric Materials
The choice of PCB dielectric material can also impact differential trace impedance. Using materials with a consistent dielectric constant (Dk) and low Loss Tangent (Df) can help maintain impedance stability. Some advanced PCB materials, such as Rogers or Isola, offer controlled impedance properties that can be beneficial in managing differential trace impedance without a reference plane.
5. Simulation and Modeling
To predict and optimize the differential trace impedance in the absence of a reference plane, simulation and modeling tools can be employed. These tools, such as Keysight ADS, Ansys HFSS, or Mentor Graphics HyperLynx, allow designers to analyze the impedance, crosstalk, and EMI performance of differential traces under various conditions. By simulating different trace geometries, spacings, and dielectric materials, designers can find the optimal configuration for their specific design constraints.
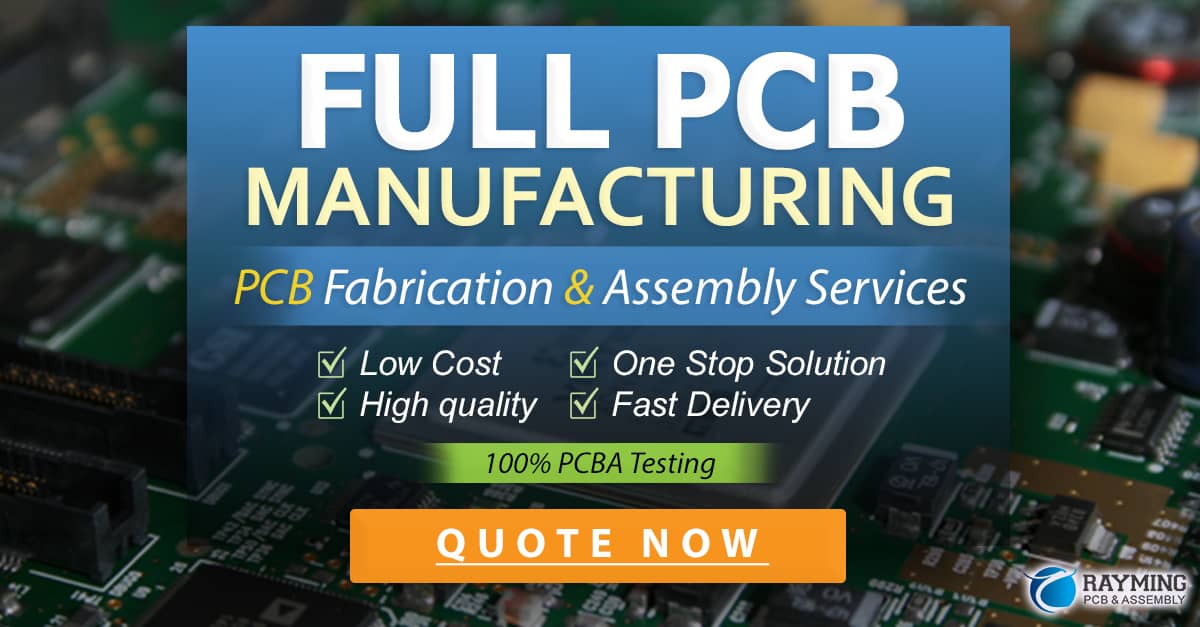
Conclusion
Managing differential trace impedance without a reference plane presents unique challenges in high-speed PCB design. The absence of a consistent return path and the lack of shielding can lead to impedance variations, increased crosstalk, and EMI issues. However, by applying techniques such as increasing trace spacing, using shielding traces, minimizing discontinuities, employing impedance-controlled dielectric materials, and leveraging simulation and modeling tools, designers can effectively mitigate these challenges and ensure reliable differential signaling in their PCB designs.
Frequently Asked Questions (FAQ)
-
Q: What is the impact of missing a reference plane on differential trace impedance?
A: The absence of a reference plane can lead to an inconsistent return path for differential signals, causing impedance variations along the length of the traces. It can also increase crosstalk and electromagnetic interference (EMI) due to the lack of shielding. -
Q: How does increasing the spacing between differential traces help manage impedance?
A: Increasing the spacing between differential traces helps to reduce the coupling between them. This, in turn, helps to maintain a more consistent impedance and reduce crosstalk, even in the absence of a reference plane. -
Q: What are shielding traces, and how do they help in managing differential trace impedance?
A: Shielding traces, also known as guard traces, are placed on either side of the differential traces and are connected to a stable reference, such as ground. They help to confine the electric and magnetic fields, reducing crosstalk and EMI. -
Q: What are some good PCB layout practices to minimize impedance discontinuities in differential traces?
A: To minimize impedance discontinuities, it is important to use smooth, gradual bends instead of sharp corners, avoid unnecessary layer transitions, match trace width and spacing when transitioning between layers, and use differential vias with identical geometry and spacing. -
Q: How can simulation and modeling tools help in managing differential trace impedance without a reference plane?
A: Simulation and modeling tools allow designers to analyze the impedance, crosstalk, and EMI performance of differential traces under various conditions. By simulating different trace geometries, spacings, and dielectric materials, designers can find the optimal configuration for their specific design constraints, even in the absence of a reference plane.
0 Comments