Composition-Based Solder Types
The most common types of solder, based on their composition, include:
Lead-Based Solder
Lead-based solders contain lead (Pb) as the primary component, along with tin (Sn) and sometimes other elements. The most common lead-based solder is 63/37 (63% tin, 37% lead), known for its low melting point and excellent wetting properties. However, due to health and environmental concerns, lead-based solders are being phased out in many applications.
Advantages of Lead-Based Solder
- Low melting point
- Excellent wetting properties
- Good electrical conductivity
- Easy to work with
Disadvantages of Lead-Based Solder
- Toxic lead content
- Environmental and health concerns
- Restricted use in many industries
Lead-Free Solder
As an alternative to lead-based solders, lead-free solders have gained popularity. These solders are typically composed of tin (Sn), silver (Ag), and copper (Cu), forming SAC alloys such as SAC305 (96.5% Sn, 3% Ag, 0.5% Cu).
Common Lead-Free Solder Alloys
Alloy | Composition | Melting Point (°C) |
---|---|---|
SAC305 | 96.5% Sn, 3% Ag, 0.5% Cu | 217-220 |
SN100C | 99.3% Sn, 0.7% Cu, 0.05% Ni | 227 |
SN96C | 96.5% Sn, 3% Ag, 0.5% Cu | 217 |
SN96.5 | 96.5% Sn, 3.5% Ag | 221 |
Advantages of Lead-Free Solder
- Environmentally friendly
- Compliant with RoHS and other regulations
- Good mechanical strength
- Suitable for high-temperature applications
Disadvantages of Lead-Free Solder
- Higher melting point than lead-based solders
- More difficult to work with
- Can cause increased component stress during cooling
- More expensive than lead-based solders
Silver-Based Solder
Silver-based solders contain silver (Ag) as the primary component, along with other elements such as tin (Sn), copper (Cu), and zinc (Zn). These solders offer excellent electrical and thermal conductivity, making them suitable for high-temperature applications and jewelry making.
Common Silver-Based Solder Alloys
Alloy | Composition | Melting Point (°C) |
---|---|---|
Silver Solder | 56% Ag, 22% Cu, 17% Zn, 5% Sn | 618-760 |
Hard Silver | 80% Ag, 20% Cu | 740-800 |
Easy Silver | 65% Ag, 20% Cu, 15% Zn | 700-725 |
Advantages of Silver-Based Solder
- Excellent electrical and thermal conductivity
- High mechanical strength
- Suitable for high-temperature applications
- Corrosion-resistant
Disadvantages of Silver-Based Solder
- Expensive compared to other solder types
- Higher melting point than lead-based and lead-free solders
- Requires specialized equipment and skills
Application-Based Solder Types
Solder types can also be classified based on their intended applications:
Electrical Solder
Electrical solders are used in electronic assemblies, PCBs, and wire connections. These solders must have good electrical conductivity, wetting properties, and mechanical strength. Common electrical solders include lead-based solders like 63/37 and lead-free solders like SAC305.
Plumbing Solder
Plumbing solders are used to join copper pipes and fittings in water supply systems. These solders must be lead-free to prevent water contamination and comply with plumbing codes. Common plumbing solders include 95/5 (95% tin, 5% antimony) and silver-based solders.
Jewelry Solder
Jewelry solders are used in the fabrication and repair of jewelry items. These solders must have good flow properties, color match, and strength. Common jewelry solders include silver-based solders, gold-based solders, and platinum-based solders.
Solder Form Factors
Solder is available in various form factors to suit different applications and processes:
Solder Wire
Solder wire is the most common form factor, consisting of a thin wire of solder alloy. It is available in various diameters and can be solid or flux-cored.
Advantages of Solder Wire
- Easy to use and control
- Suitable for manual soldering
- Available in various alloys and diameters
Disadvantages of Solder Wire
- Not suitable for automated processes
- Limited flux content in solid wire
Solder Paste
Solder paste is a mixture of solder particles suspended in a flux medium. It is used in surface mount assembly processes and applied using stencils or dispensers.
Advantages of Solder Paste
- Suitable for automated processes
- Precise control over Solder volume
- Good flux coverage
Disadvantages of Solder Paste
- Requires specialized equipment
- Limited shelf life
- Can cause solder bridging if not properly applied
Solder bars and Ingots
Solder bars and ingots are large, solid pieces of solder alloy used in wave soldering and dip soldering processes. They are melted in a solder pot to create a solder bath.
Advantages of Solder Bars and Ingots
- Suitable for large-scale production
- Consistent alloy composition
- Cost-effective for high-volume applications
Disadvantages of Solder Bars and Ingots
- Requires specialized equipment
- Not suitable for small-scale or manual soldering
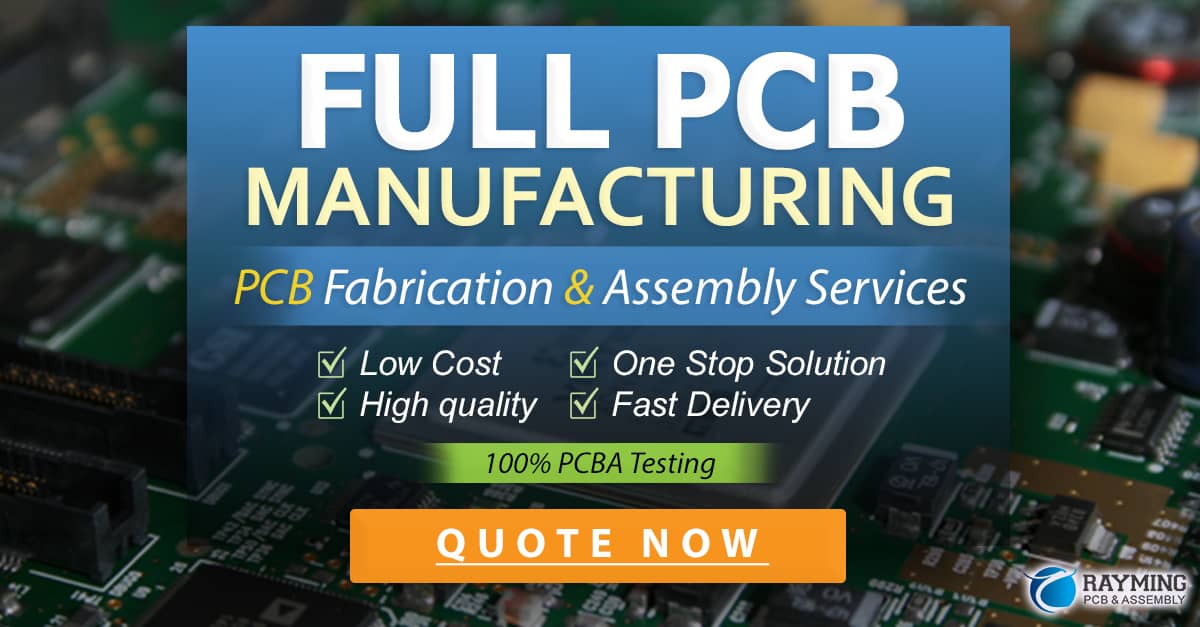
Flux Types
Flux is a chemical compound that helps to remove oxides and improve the wetting of the solder to the base metal. There are three main types of flux:
Rosin Flux
Rosin flux is a natural, non-corrosive flux derived from pine tree resin. It is available in various activities, such as R, RMA, and RA, depending on the level of activation.
Advantages of Rosin Flux
- Non-corrosive and safe for electronics
- Leaves a protective residue
- Available in various activities
Disadvantages of Rosin Flux
- Can leave a sticky residue
- May require cleaning in some applications
Water-Soluble Flux
Water-soluble flux is a highly active, inorganic acid flux that can be easily cleaned with water.
Advantages of Water-Soluble Flux
- Highly active and effective
- Easy to clean with water
- Suitable for high-temperature applications
Disadvantages of Water-Soluble Flux
- Can cause corrosion if not thoroughly cleaned
- Requires cleaning equipment and process
No-Clean Flux
No-clean flux is a mildly active, rosin-based flux that leaves a minimal, non-corrosive residue that does not require cleaning.
Advantages of No-Clean Flux
- Eliminates the need for post-soldering cleaning
- Reduces production time and costs
- Suitable for most electronic applications
Disadvantages of No-Clean Flux
- May leave a visible residue
- Not suitable for high-reliability applications
Frequently Asked Questions (FAQ)
1. What is the most common lead-free solder alloy?
The most common lead-free solder alloy is SAC305, which contains 96.5% tin, 3% silver, and 0.5% copper. This alloy has a melting point of 217-220°C and offers good mechanical strength and reliability.
2. Can lead-based solder be used for plumbing applications?
No, lead-based solders are not permitted for use in plumbing applications due to the risk of lead contamination in drinking water. Plumbing solders must be lead-free and comply with local plumbing codes and regulations.
3. What is the difference between solder wire and solder paste?
Solder wire is a thin, solid wire of solder alloy used in manual soldering processes. Solder paste, on the other hand, is a mixture of solder particles suspended in a flux medium, used in automated surface mount assembly processes. Solder paste is applied using stencils or dispensers and requires specialized equipment for handling and reflow.
4. What type of flux is most suitable for electronic applications?
For electronic applications, rosin flux and no-clean flux are the most suitable options. Rosin flux is non-corrosive and leaves a protective residue, while no-clean flux eliminates the need for post-soldering cleaning and reduces production time and costs. Water-soluble flux, although highly effective, can cause corrosion if not thoroughly cleaned and is not recommended for most electronic applications.
5. How do I choose the right solder alloy for my application?
When choosing a solder alloy, consider the following factors:
– Melting point: The solder alloy should have a lower melting point than the base metals being joined.
– Composition: Choose a lead-free alloy for environmental and health reasons, unless the application specifically requires lead-based solder.
– Wetting properties: The solder should have good wetting properties to ensure a strong and reliable bond.
– Mechanical strength: Consider the mechanical strength requirements of the joint and choose an alloy with appropriate properties.
– Electrical and thermal conductivity: For applications involving electrical or thermal conductivity, choose an alloy with suitable properties, such as silver-based solders.
– Compatibility with flux: Ensure that the solder alloy is compatible with the chosen flux type to achieve optimal results.
In summary, selecting the right solder type involves considering the composition, application, form factor, and flux compatibility to ensure a strong, reliable, and efficient soldering process. By understanding the various solder types and their properties, engineers and technicians can make informed decisions and achieve optimal results in their soldering applications.
0 Comments