What is a Solder Bar?
A solder bar is a solid stick or rod of solder material used for joining metals together through a process called soldering. Solder bars are available in various alloys, each with specific melting points, strengths, and applications. The most common solder alloys contain tin, lead, silver, copper, or bismuth in different proportions to achieve desired properties such as melting temperature, strength, and wettability.
Solder bars are used in conjunction with a heat source, such as a soldering iron or torch, which melts the solder and allows it to flow into the joint between two metal surfaces. As the solder cools and solidifies, it creates a strong bond that holds the pieces together. Solder bars are favored for their ease of use, preciseness, and ability to create reliable connections in electrical and mechanical systems.
Types of Solder Bars
Solder bars come in various alloy compositions to suit different applications and requirements. The choice of solder bar depends on factors such as the metals being joined, the desired melting temperature, the required strength of the joint, and the environmental conditions the soldered connection will be exposed to. Here are some common types of solder bars:
Lead-based Solder Bars
Lead-based solder bars have been widely used for decades due to their low melting point, excellent wettability, and good electrical conductivity. The most common lead-based solder alloy is 63/37, which contains 63% tin and 37% lead. This alloy has a melting point of 183°C (361°F) and provides a strong, reliable bond.
However, due to the health and environmental risks associated with lead, many countries have restricted or banned the use of lead-based solders in certain applications, particularly in electronics manufacturing. As a result, lead-free alternatives have gained prominence in recent years.
Lead-free Solder Bars
Lead-free solder bars have been developed to address the health and environmental concerns associated with lead-based solders. These solder bars typically contain tin, silver, and copper in various proportions. Some common lead-free solder alloys include:
- SAC305 (96.5% tin, 3% silver, 0.5% copper)
- SN100C (99.3% tin, 0.7% copper, with a small amount of nickel)
- SN96C (96.5% tin, 3% silver, 0.5% copper)
Lead-free solder bars generally have higher melting points compared to lead-based solders, ranging from 217°C to 227°C (423°F to 441°F). They also require stricter process control and may be more prone to defects if not handled properly. However, advancements in lead-free solder formulations have improved their performance and reliability, making them suitable for a wide range of applications.
Silver-bearing Solder Bars
Silver-bearing solder bars contain a small percentage of silver, usually between 2% and 4%, in addition to tin and other metals. The presence of silver improves the mechanical strength, thermal fatigue resistance, and wettability of the solder joint. Silver-bearing solders are commonly used in high-temperature applications, such as automotive electronics, aerospace, and power electronics.
Some popular silver-bearing solder alloys include:
- Sn96Ag04 (96% tin, 4% silver)
- Sn95Ag05 (95% tin, 5% silver)
- SAC305 (96.5% tin, 3% silver, 0.5% copper)
Silver-bearing solder bars have higher melting points compared to lead-based solders, typically ranging from 221°C to 229°C (430°F to 444°F). They also tend to be more expensive due to the added cost of silver.
Flux-cored Solder Bars
Flux-cored solder bars have a core of flux material running through the center of the solder bar. Flux is a chemical compound that helps remove oxides from metal surfaces, promotes wetting, and prevents re-oxidation during the soldering process. Having the flux integrated into the solder bar eliminates the need for a separate flux application step, making the soldering process more efficient and convenient.
Flux-cored solder bars are available in various alloy compositions, both lead-based and lead-free, and with different flux types. The choice of flux depends on the specific application and the desired level of cleanliness and activity. Some common flux types include rosin, no-clean, and water-soluble fluxes.
Applications of Solder Bars
Solder bars find extensive use in various industries and applications where reliable electrical and mechanical connections are essential. Some key areas where solder bars are commonly used include:
Electronics Manufacturing
The electronics industry is one of the largest consumers of solder bars. Solder bars are used to attach electronic components to printed circuit boards (PCBs), create electrical connections between components, and provide mechanical support. The move towards miniaturization and increased functionality in electronic devices has led to a growing demand for high-quality, reliable solder joints.
In electronics manufacturing, lead-free solder bars, such as SAC305 and SN100C, have largely replaced lead-based solders due to RoHS (Restriction of Hazardous Substances) regulations. These lead-free solder bars are used in various soldering techniques, including wave soldering, selective soldering, and hand soldering.
Automotive Industry
The automotive industry relies on solder bars for creating reliable electrical connections in vehicle electronics systems. Solder bars are used to assemble printed circuit boards, sensors, connectors, and other electronic components that control various functions in modern vehicles, such as engine management, safety systems, and infotainment.
Given the harsh operating conditions in automotive environments, such as high temperatures, vibrations, and thermal cycling, solder bars used in this industry must provide excellent mechanical strength and thermal fatigue resistance. Silver-bearing solder bars, like SAC305 and Sn96Ag04, are commonly used in automotive applications due to their superior performance under these challenging conditions.
Aerospace and Defense
Solder bars play a critical role in the aerospace and defense industries, where reliability and durability are paramount. These industries use solder bars to assemble electronic components in aircraft, satellites, military equipment, and weapons systems. The solder joints must withstand extreme temperatures, vibrations, and other environmental stresses while maintaining excellent electrical and mechanical integrity.
High-reliability solder alloys, such as SN96C and Sn95Ag05, are often used in aerospace and defense applications. These alloys provide strong, stable joints that can resist thermal fatigue and mechanical stresses over extended periods.
Plumbing and HVAC
Solder bars are essential tools in the plumbing and heating, ventilation, and air conditioning (HVAC) industries. They are used to join copper pipes and fittings in water supply lines, gas lines, and refrigeration systems. Soldering provides a strong, leak-proof connection that can withstand high pressures and temperatures.
Lead-based solder bars, particularly 50/50 tin-lead alloy, were widely used in plumbing applications due to their excellent wetting properties and low melting point. However, with growing concerns over lead contamination in drinking water, lead-free solder bars have become mandatory in many countries for plumbing applications. Common lead-free solder alloys for plumbing include Sn95Sb05 (95% tin, 5% antimony) and Sn97Cu03 (97% tin, 3% copper).
Jewelry Making
Solder bars are indispensable in jewelry making for joining metal parts, creating intricate designs, and repairing broken pieces. Jewelers use various solder alloys, depending on the metals being joined and the desired appearance of the final product. Some common solder alloys used in jewelry making include:
- Gold solder: Available in different karats and colors to match the gold being soldered
- Silver solder: Used for joining silver pieces or adding accents to gold jewelry
- Platinum solder: Used for soldering platinum jewelry
- Argentium solder: A silver solder specifically designed for use with Argentium sterling silver
Jewelry solders have lower melting points compared to the base metals to prevent damage to the pieces being joined. They also come in different forms, such as sheets, wire, and paste, to accommodate various soldering techniques and applications.
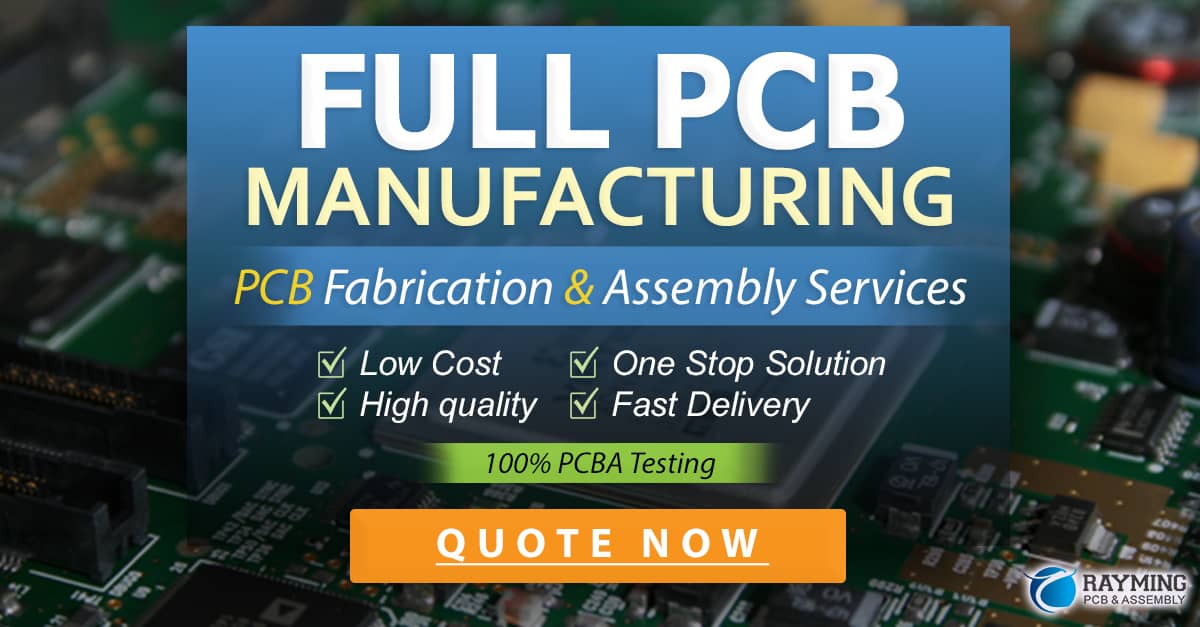
Choosing the Right Solder Bar
Selecting the appropriate solder bar for a specific application involves considering several factors, including:
-
Base metals: The solder bar must be compatible with the metals being joined to ensure proper wetting and a strong bond.
-
Melting temperature: The melting point of the solder bar should be lower than that of the base metals to prevent damage during the soldering process.
-
Strength and durability: The solder alloy should provide adequate mechanical strength and resistance to thermal fatigue and environmental stresses, depending on the application.
-
Regulatory requirements: Some industries, such as electronics and plumbing, have specific regulations regarding the use of lead-based solders. It is essential to choose a solder bar that complies with the relevant standards and regulations.
-
Flux type: For flux-cored solder bars, select the appropriate flux type based on the desired level of cleanliness, activity, and compatibility with the base metals and soldering process.
-
Cost: Consider the cost of the solder bar in relation to the performance requirements and production volume. Some alloys, like silver-bearing solders, may have a higher initial cost but can provide better long-term reliability and performance.
FAQ
1. What is the difference between soldering and welding?
Soldering and welding are both methods of joining metals, but they differ in the process and the temperatures involved. Soldering involves melting a filler metal (solder) with a melting point below 450°C (842°F) to join two base metals without melting them. Welding, on the other hand, involves melting the base metals themselves to fuse them together, usually at temperatures above 450°C (842°F). Soldering is generally used for creating electrical and mechanical connections in applications where the joint is not subjected to high stress or temperatures, while welding is used for creating stronger, more permanent bonds in structural and load-bearing applications.
2. Can I use lead-based solder bars for electronics?
The use of lead-based solder bars in electronics manufacturing is restricted or prohibited in many countries due to the health and environmental risks associated with lead. The European Union’s RoHS (Restriction of Hazardous Substances) directive, for example, limits the use of lead in electronic and electrical equipment. It is recommended to use lead-free solder bars, such as SAC305 or SN100C, for electronics applications to ensure compliance with regulations and minimize the environmental impact.
3. How do I store solder bars?
Solder bars should be stored in a cool, dry place away from direct sunlight and sources of heat. Exposure to moisture and high temperatures can cause the solder bars to oxidize or degrade, affecting their performance during the soldering process. Store solder bars in their original packaging or in airtight containers to prevent contamination and maintain their quality. Properly stored solder bars can have a shelf life of several years, depending on the alloy composition and storage conditions.
4. Can I mix different types of solder bars?
Mixing different types of solder bars is not recommended, as it can lead to inconsistent melting temperatures, poor wetting, and compromised joint strength. Each solder alloy has specific properties, such as melting point, wetting behavior, and mechanical characteristics, which are optimized for specific applications. Mixing different solder alloys can result in unpredictable performance and may cause defects in the soldered joints. It is best to use the solder bar specified for the particular application and avoid mixing different alloys.
5. How do I dispose of used solder bars?
The proper disposal of used solder bars depends on the alloy composition and local regulations. Lead-based solder bars should be treated as hazardous waste and disposed of in accordance with the relevant environmental regulations. Some recycling facilities may accept lead-based solder waste for proper treatment and disposal. Lead-free solder bars, while less hazardous, should still be disposed of responsibly to minimize their environmental impact. Check with your local authorities or waste management service provider for guidance on the appropriate disposal methods for used solder bars in your area.
Conclusion
Solder bars are versatile and essential tools used in various industries for creating reliable electrical and mechanical connections. With a wide range of alloy compositions and properties, solder bars cater to the specific requirements of different applications, from electronics manufacturing to plumbing and jewelry making.
As environmental concerns and regulations drive the shift towards lead-free solders, manufacturers and users must adapt to the challenges and opportunities presented by these alternative alloys. Proper selection, storage, and handling of solder bars are crucial for achieving optimal soldering results and ensuring the long-term reliability of the soldered joints.
By understanding the characteristics, applications, and best practices associated with solder bars, professionals across industries can make informed decisions and contribute to the production of high-quality, sustainable, and reliable products.
0 Comments