What is PCB Panelization?
PCB panelization is the process of grouping multiple printed circuit board designs onto a single panel for production. This allows many PCBs to be manufactured together, which improves efficiency and reduces costs compared to fabricating each PCB individually.
Panelization is an important step in PCB manufacturing, especially for small PCBs or high volume production. Grouping multiple PCBs on larger panels makes them easier to handle and allows them to be run through the pick-and-place and soldering processes.
Why Use PCB Panelization?
There are several key benefits to panelizing PCBs for production:
- Improved manufacturing efficiency by allowing many boards to be processed at once
- Lower cost per PCB by producing a greater quantity together
- Easier handling of very small PCBs
- Faster assembly since multiple boards can be populated and soldered together
Overall, panelization simplifies the manufacturing process and makes it more cost-effective, especially for high volume PCB orders. It’s an important optimization used for most PCB designs.
PCB Panelization Methods
There are a few different methods commonly used for panelizing PCBs. The best panelization technique depends on the size, shape, quantity, and design requirements of the particular PCBs being produced.
The main PCB panelization methods are:
- Tab Routing
- V-Scoring
- Perforated Boards
- Snapable Boards
Let’s look at each of these methods in more detail.
Tab Routing Panelization
Tab routing is one of the most common PCB panelization methods. With this technique, each individual PCB is connected to the main panel by small tabs. After the full panel is assembled, the individual boards can be separated from the panels by breaking or cutting the tabs.
Advantages of tab routing include:
- Works well for simple rectangular PCB shapes
- Strong tabs keep boards secure during manufacturing
- Tabs can be made small to minimize waste material
- Provides very clean and smooth board edges after depaneling
Disadvantages include:
- Leaves behind small protrusions where the tabs break off (mouse bites)
- Tabs can put stress on boards leading to potential damage during separation
- Not ideal for irregular board shapes
Tab routing is a good general-purpose panelization method but other techniques may be preferred for some designs.
V-Scoring Panelization
V-scoring is a panelization method where a v-shaped groove is cut partway through the panel material between each PCB. This creates a pre-defined break line where the panel can be easily split apart after assembly. The v-shaped profile focuses the breaking stress to enable cleaner snapping of the boards with less risk of damage compared to tab routing.
Advantages of v-scoring include:
- Provides clean separation of boards with smooth edges
- Reduces stress on boards during depaneling
- Allows for slightly more irregular board shapes compared to tab routing
- No wasted tab material left behind after breaking boards out of the panel
Disadvantages include:
- Scoring cuts make the panel less rigid which can cause problems during assembly
- Grooves can collect dirt and debris during manufacturing
- More complex and expensive than tab routing
- Not suitable for very thick PCBs or specialty materials
V-scoring is often used when clean edges and low depaneling stress are priorities. It’s a good option for projects using thinner PCBs.
Perforated Board Panelization
Perforated board panelization uses a series of drilled holes to define the break lines between individual PCBs on the panel. The holes perforate the board making it easy to snap apart after assembly.
Advantages include:
- Creates very clean and debris-free board edges
- Holes allow panel to remain rigid for easy handling and assembly
- Supports more complex and irregular board shapes
- Lower cost than routing or v-scoring
Disadvantages include:
- Perforations may not be as precise or consistent as scoring or routing
- Some risk of hole misalignment or inaccurate placement
- Can be difficult to snap thick, rigid PCBs without damage
Perforated panels are frequently used for projects requiring odd-shaped boards or where cost is a driving factor. The ability to keep boards secure yet separate them cleanly makes this a popular panelization option.
Snapable PCB Panelization
Snapable panelization involves adding small notches, or mouse bites, to create snap off points between the individual boards on the panel. Each PCB is connected to the panel by short, narrow sections that can be easily broken after assembly. This technique is somewhat of a hybrid between tab routing and perforated panelization.
Advantages of snapable PCB panelization include:
- Provides very secure board mounting during manufacturing
- Allows clean snap-off separation of finished boards
- Supports a wide range of board shapes and sizes
- Generally lower cost than routing or v-scoring
Disadvantages include:
- Mouse bites leave small nubs behind on board edges after snapping
- Notches can create some stress on boards during depaneling
- Waste material is generated similar to tab routing
Snapable PCB panelization is a good choice when ease of manufacturing, secure assembly, and clean board separation are all important priorities. The low cost and versatility make it one of the most popular methods.
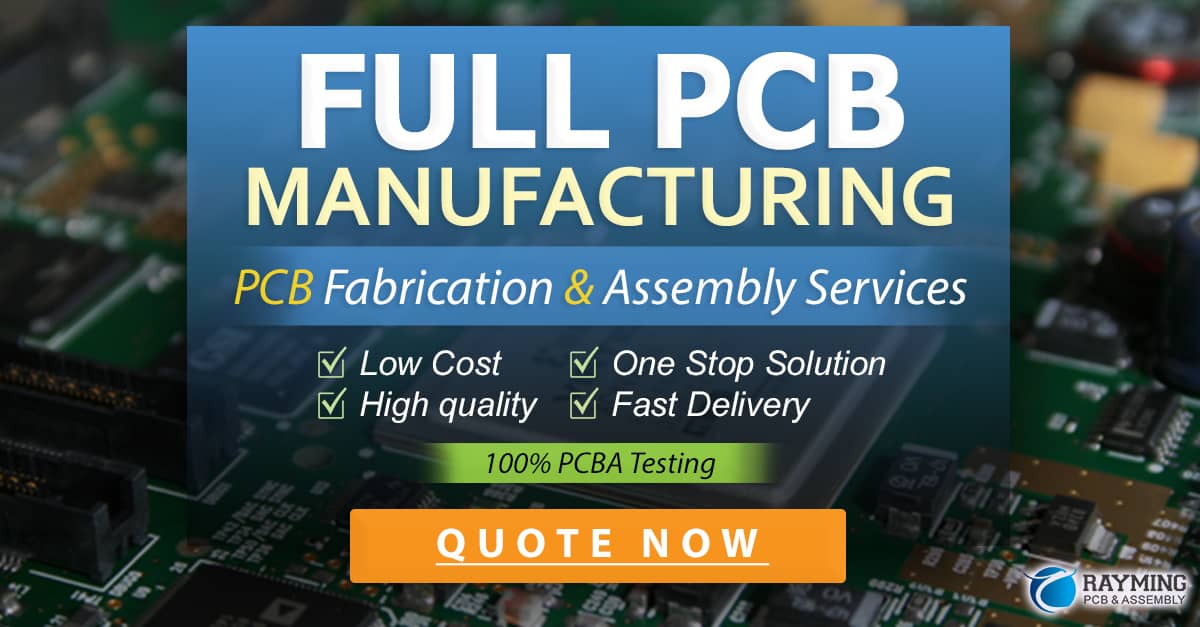
PCB Panelization Comparison
To summarize the differences between the main PCB panelization methods, refer to this comparison table:
Method | Advantages | Disadvantages |
---|---|---|
Tab Routing | Strong tabs, minimal waste, clean edges | Leaves nubs, stresses board |
V-Scoring | Clean edges, low stress | Panel less rigid, collects debris |
Perforated | Clean edges, rigid panel, low cost | Less precise, potential misalignment |
Snapable | Secure, clean, versatile, low cost | Leaves nubs, some stress |
Choosing a PCB Panelization Method
With multiple panelization techniques available, it’s important to select the method that best fits the specific requirements and priorities of your PCB project. Here are some factors to consider when choosing how to panelize your PCBs:
-
Board Shape and Size – The shape and dimensions of the individual PCBs can influence which panelization method is most suitable. Simple rectangular boards are easy to tab route, while more complex profiles may require v-scoring or perforated panelization.
-
Material Thickness – Thicker, more rigid PCB materials can be more difficult to snap apart cleanly. Tab routing or v-scoring may be preferable to perforated or snapable methods for thick boards to avoid damaging the PCBs during depaneling.
-
Required Edge Quality – Some projects may have strict requirements for smooth, clean PCB edges after separation from the panel. V-scoring or perforated panelization typically produce the cleanest edges, while tab routing and snapable methods leave some small nubs behind.
-
Manufacturing Cost – The choice of panelization method can impact the cost of PCB Fabrication. Tab routing and snapable panelization tend to be more economical, while v-scoring is usually more expensive. Perforated panels can offer a good balance of cost and quality.
-
Production Volume – High volume PCB production may benefit from panelization methods that maximize assembly efficiency and minimize waste, such as v-scoring. Lower volumes can take advantage of the simplicity and low cost of tab routing or snapable designs.
By evaluating your PCB project against these criteria, you can determine the panelization method that offers the best mix of manufacturing efficiency, edge quality, ease of assembly, and cost-effectiveness for your needs.
PCB Panelization Tips and Best Practices
To ensure successful PCB panelization and manufacturing, consider these tips and best practices:
-
Consult with your PCB manufacturer – Always discuss your panelization plans with your fabrication partner. They can provide guidance on which methods are best suited for your design based on their equipment and experience.
-
Consider panelization during PCB design – Think about how your boards will be panelized early in the design process. This can help you optimize the shape, size, and layout of your PCBs for the most efficient panelization and assembly.
-
Keep panel sizes within manufacturer limits – Each fabrication shop will have minimum and maximum panel sizes they can accommodate. Make sure your panelized designs fall within these limits to avoid production issues.
-
Leave adequate spacing between boards – Provide sufficient room between individual PCBs on the panel for the panelization features, such as tabs, grooves, or perforations. This spacing is essential for clean and reliable board separation.
-
Minimize waste material – Optimize the layout of your boards on the panel to use the available space efficiently and reduce the amount of waste material left behind after separating the PCBs.
-
Test your depaneling process – Before starting full production, test your depaneling method on a small batch of panels to ensure the PCBs can be separated cleanly without damage. Make any necessary adjustments to your panelization design before proceeding.
By following these guidelines and carefully selecting the appropriate panelization method for your project, you can streamline your PCB manufacturing process, reduce costs, and ensure the highest quality end product.
FAQ
- What is the most common PCB panelization method?
Tab routing is one of the most frequently used PCB panelization methods due to its simplicity, low cost, and suitability for a wide range of board designs. It’s especially common for simple rectangular PCBs.
- Can I mix different panelization methods on the same panel?
Yes, it’s possible to use multiple panelization techniques on a single panel, such as combining tab routing with v-scoring. However, this can increase the complexity and cost of fabrication. It’s best to choose a single method that meets all your requirements whenever possible.
- How much space should I leave between PCBs on a panel?
The minimum spacing between PCBs on a panel depends on the panelization method being used. Generally, you should leave at least 3-5 mm between boards for tab routing, v-scoring, or perforations. Consult with your manufacturer for specific guidelines.
- What’s the best panelization method for thick PCBs?
For thicker, more rigid PCBs, tab routing or v-scoring are often preferable to perforated or snapable methods. The tabs or grooves provide a more controlled and predictable break point to minimize the risk of board damage during depaneling.
- How do I choose the right panel size for my PCBs?
The ideal panel size for your PCBs depends on several factors, including the dimensions of the individual boards, the panelization method being used, and the capabilities of your manufacturer. Work with your fabrication partner to determine the panel size that offers the best balance of efficiency, cost, and quality for your specific project.
0 Comments