Introduction to DC Motor Speed Control
DC motors are widely used in various applications, from small-scale projects to industrial automation, due to their simplicity, reliability, and ease of control. One of the most important aspects of using DC motors is the ability to regulate their speed according to the requirements of the application. In this article, we will explore the different methods and circuits used for DC motor speed control, helping you find a suitable speed regulation system for your needs.
Importance of DC Motor Speed Control
DC motor speed control is essential for several reasons:
-
Precision: Many applications require precise control over the motor’s speed to achieve the desired output or performance.
-
Energy efficiency: By controlling the motor’s speed, you can optimize power consumption and reduce energy waste.
-
Prolonged motor life: Running a motor at the appropriate speed helps prevent overheating and excessive wear, extending its lifespan.
-
Adaptability: Speed control allows a single motor to be used in various applications with different speed requirements.
Methods of DC Motor Speed Control
There are several methods for controlling the speed of a DC motor, each with its own advantages and limitations. Let’s explore some of the most common techniques.
Voltage Control
One of the simplest methods for controlling the speed of a DC motor is by varying the voltage applied to its terminals. According to the motor’s characteristic equation:
V = E + I * R
Where:
– V is the applied voltage
– E is the back EMF (electromotive force) generated by the motor
– I is the current flowing through the motor
– R is the motor’s armature resistance
As the applied voltage (V) increases, the motor’s speed also increases, and vice versa. This method is straightforward to implement but has some drawbacks:
-
Limited speed range: The motor’s speed can only be varied within a certain range, depending on the motor’s specifications and the available voltage.
-
Poor speed regulation: Changes in load can cause the motor’s speed to fluctuate, as the back EMF (E) varies with the motor’s speed.
PWM (Pulse Width Modulation) Control
PWM is a more advanced method for controlling the speed of a DC motor, offering better speed regulation and a wider speed range compared to voltage control. In PWM control, the motor is supplied with a series of pulses, and the width (duration) of these pulses determines the effective voltage applied to the motor.
The duty cycle of the PWM signal represents the percentage of time the voltage is applied to the motor. For example, a 50% duty cycle means the voltage is applied for half of the PWM period, resulting in an effective voltage of half the supply voltage.
Advantages of PWM control:
-
Wide speed range: PWM allows for a much wider range of speed control, from very low speeds to the motor’s maximum speed.
-
Better speed regulation: By continuously adjusting the duty cycle, PWM can maintain a constant motor speed even under varying load conditions.
-
Energy efficiency: PWM control reduces power dissipation in the control circuit, as the switching elements (e.g., transistors) are either fully on or off.
Microcontroller-based PWM Control
Implementing PWM control using a microcontroller offers several benefits:
-
Flexibility: Microcontrollers can easily generate PWM signals with configurable frequencies and duty cycles.
-
Closed-loop control: By incorporating feedback sensors (e.g., encoders or tachometers), a microcontroller can implement closed-loop speed control, automatically adjusting the PWM signal to maintain the desired speed.
-
Integration with other systems: Microcontrollers can communicate with other devices and systems, enabling the integration of the motor control into a larger automation or control system.
Here’s an example of a simple microcontroller-based PWM motor speed control circuit using an Arduino:
const int motorPin = 9;
const int potPin = A0;
void setup() {
pinMode(motorPin, OUTPUT);
}
void loop() {
int potValue = analogRead(potPin);
int dutyCycle = map(potValue, 0, 1023, 0, 255);
analogWrite(motorPin, dutyCycle);
}
In this example, the motor speed is controlled by a potentiometer connected to an analog input pin of the Arduino. The analogRead()
function reads the potentiometer value (0-1023), which is then mapped to a PWM duty cycle (0-255) using the map()
function. The analogWrite()
function generates the PWM signal on the specified pin, controlling the motor speed.
DC Motor Speed Control Circuit Components
To build a DC motor speed control circuit, you’ll need the following components:
-
DC motor: Choose a motor that suits your application’s requirements in terms of voltage, current, power, and speed range.
-
Power supply: Select a power supply that matches the motor’s voltage and current requirements.
-
Control circuit: This can be a simple voltage divider for voltage control, a PWM generator circuit using discrete components, or a microcontroller-based PWM control system.
-
Switching elements: Depending on the control method and the motor’s current requirements, you may need transistors, MOSFETs, or motor driver ICs to switch the current through the motor.
-
Potentiometer or other input device: For manual speed control, use a potentiometer or another input device (e.g., a rotary encoder or a digital interface) to set the desired speed.
-
Protective components: Include fuses, diodes, and capacitors to protect the circuit from overcurrent, voltage spikes, and noise.
Here’s a table summarizing some common DC motor speed control methods and their key characteristics:
Method | Complexity | Speed Range | Speed Regulation | Efficiency |
---|---|---|---|---|
Voltage Control | Low | Limited | Poor | Low |
PWM (Discrete) | Medium | Wide | Good | Medium |
PWM (Microcontroller) | High | Wide | Excellent | High |
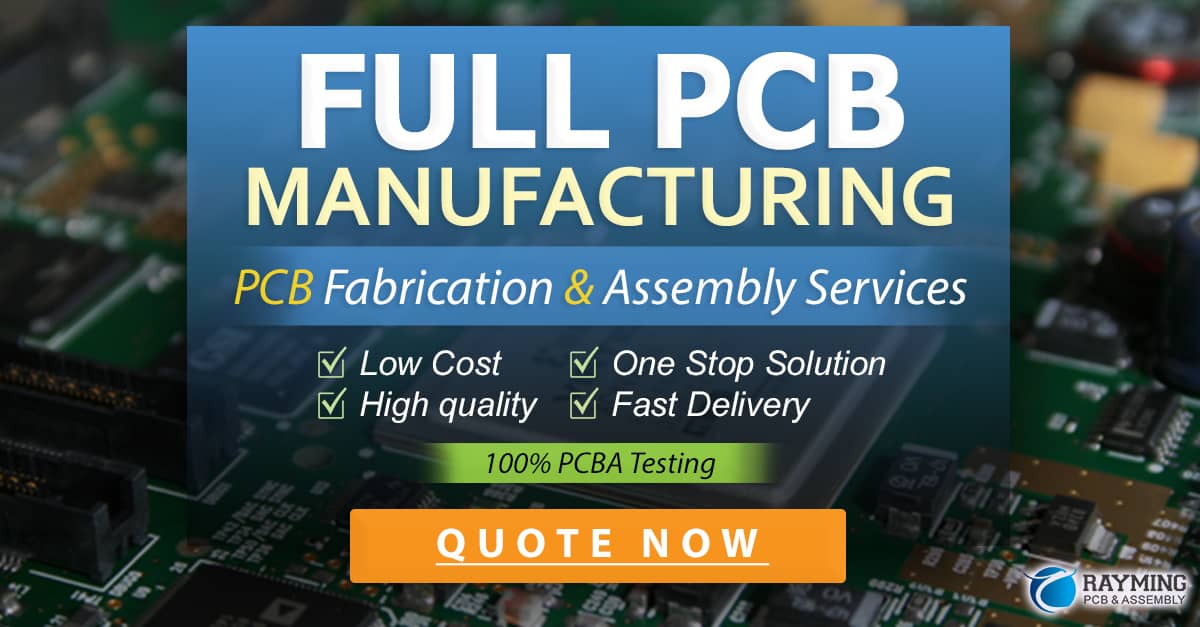
Selecting the Right Speed Control Method
When choosing a speed control method for your application, consider the following factors:
-
Speed range: Determine the required speed range for your application and select a control method that can achieve it.
-
Speed regulation: If your application demands precise speed control under varying load conditions, opt for a method with good speed regulation, such as PWM control.
-
Complexity: Consider your own technical skills and the time available for implementation when selecting a control method. Simple voltage control may be sufficient for basic applications, while more advanced methods like microcontroller-based PWM control offer greater flexibility and performance.
-
Cost: Evaluate the cost of components and development time for each control method. Simple methods may be more cost-effective for small-scale projects, while advanced methods may be justified for high-performance or large-scale applications.
-
Integration: If your motor control system needs to communicate with other devices or be part of a larger automation setup, consider using a microcontroller-based control method for easier integration.
Implementing a DC Motor Speed Control Circuit
Once you have selected the appropriate speed control method for your application, follow these steps to implement the circuit:
-
Gather components: Obtain all the necessary components for your chosen control method, including the DC motor, power supply, control circuit components, and protective elements.
-
Design the circuit: Create a schematic diagram of your speed control circuit, ensuring that all components are correctly connected and rated for the expected voltage and current levels.
-
Build the circuit: Assemble the components on a breadboard or PCB, following your schematic diagram. Double-check all connections to avoid short circuits or incorrect wiring.
-
Test and calibrate: Apply power to the circuit and test the motor’s speed control. Use a multimeter or oscilloscope to verify the control signal and motor voltage. Calibrate the input device (e.g., potentiometer) to ensure the desired speed range is achieved.
-
Optimize and refine: Observe the motor’s performance under different load conditions and make any necessary adjustments to the control circuit or code to improve speed regulation and overall performance.
Frequently Asked Questions (FAQ)
-
What is the difference between a brushed and brushless DC motor?
Brushed DC motors have physical brushes that contact the commutator to switch the current direction, while brushless DC motors use electronic commutation with permanent magnets and stator windings. Brushless motors are more efficient and have a longer lifespan, but they require more complex control circuits. -
Can I use a DC motor speed control circuit with an AC motor?
No, DC motor speed control circuits are designed specifically for DC motors. AC motors require different control methods, such as variable frequency drives (VFDs) or triac-based controllers. -
How do I determine the current rating for my DC motor speed control circuit?
The current rating of your speed control circuit should be based on the maximum current draw of your DC motor. Consult the motor’s datasheet or measure the current under load to determine the appropriate rating for your switching elements and protective components. -
What is the advantage of using a motor driver IC instead of discrete components?
Motor driver ICs, such as the L298N or TB6612FNG, simplify the design and implementation of DC motor speed control circuits by integrating the necessary switching elements, protection features, and control interfaces into a single package. They can handle higher current levels and offer additional features like direction control and current sensing. -
Can I control multiple DC motors with a single speed control circuit?
Yes, you can control multiple DC motors with a single speed control circuit by using a microcontroller with multiple PWM outputs or by duplicating the control circuit for each motor. However, ensure that your power supply can handle the combined current draw of all the motors and that each motor has its own protective elements.
Conclusion
DC motor speed control is a crucial aspect of many applications, and choosing the right speed control method depends on factors such as the required speed range, speed regulation, complexity, cost, and integration with other systems. By understanding the different methods available and their characteristics, you can select the most suitable speed control circuit for your needs.
When implementing your chosen speed control method, be sure to follow best practices for circuit design, component selection, and testing. With a well-designed and properly calibrated speed control circuit, you can achieve precise, efficient, and reliable speed regulation for your DC motor-based applications.
0 Comments