What is a Cable Assembly?
A cable assembly, also known as a Wire Harness, wiring assembly or wiring loom, is a group of wires or cables bundled together into a single unit. The wires are cut to specific lengths and may include terminals or connectors on one or both ends. Cable assemblies are designed to simplify the installation and routing of wiring in electrical and electronic systems. They provide a cost-effective and efficient solution for connecting components.
Key features of cable assemblies include:
- Bundled wires/cables cut to length
- May include terminals, connectors, labels, sleeving, shielding
- Simplify wiring installation and routing
- Designed for specific applications
- Provide reliable connections
- Cost-effective wiring solution
Cable assemblies are used in virtually every industry that utilizes electrical or electronic equipment, such as:
Industry | Applications |
---|---|
Automotive | Engine wiring harnesses, dashboard wiring, lighting |
Aerospace | Avionics, in-flight entertainment, sensors, power distribution |
Medical | Patient monitoring, imaging systems, surgical tools |
Industrial | Control panels, robotics, machinery, sensors |
Consumer Electronics | Appliances, computers, A/V equipment |
Telecommunications | Networking equipment, server racks, switching systems |
The demand for cable assemblies continues to grow, driven by the increasing complexity of electronic systems, need for reliability, and pressure to reduce costs. The global cable assembly market is projected to reach USD 195.3 billion by 2025, at a CAGR of 5.9% from 2020 to 2025.
Benefits of Custom Cable Assemblies
While off-the-shelf cable assemblies are readily available for many general purpose applications, custom cable assemblies offer significant benefits, especially for mission-critical systems or challenging environments. Key advantages of custom cable assemblies include:
1. Designed for Specific Requirements
Custom cable assemblies are engineered to meet the exact electrical, mechanical and environmental requirements of the end application. This includes factors such as:
- Number and gauges of conductors
- Types of insulation and jacketing materials
- Shielding against EMI/RFI
- Flexibility and bend radius
- Resistance to abrasion, chemicals, moisture, or temperature extremes
- Current carrying capacity
- Flammability and smoke generation
By optimizing the design for the specific application, custom cable assemblies maximize performance and reliability. Off-the-shelf cable assemblies, in contrast, are designed for general purpose use and may not have the ideal characteristics for a given application.
2. Simplified Installation and Maintenance
Custom cable assemblies are built to simplify installation and reduce assembly time. The wires are cut to the correct lengths, labeled, and terminated with the appropriate connectors. This eliminates the need for cutting, stripping, crimping and soldering individual wires in the field. Technicians simply need to route the cable assembly and plug in the connectors.
Well-designed cable assemblies also make maintenance and troubleshooting easier. With individual wires bundled together and properly labeled, technicians can quickly trace signals and identify potential problems. Damaged cable assemblies can be swapped out as a single unit, rather than having to replace individual wires.
3. Improved Reliability
Custom cable assemblies are professionally engineered and manufactured in a controlled environment to ensure high quality and reliability. Automated crimping and soldering equipment ensures consistent and robust terminations. Cable assemblies are 100% tested for continuity, insulation resistance and high potential (hipot) to detect any defects.
In contrast, field wiring using individual conductors is prone to human error, especially in tight spaces or harsh conditions. Poor crimps, cold solder joints, nicked insulation and other wiring errors can lead to intermittent faults or failures in the future.
4. Cost Savings
Although custom cable assemblies have higher upfront costs compared to individual wires and connectors, they offer significant savings over the total lifecycle in several ways:
- Reduced installation time and labor costs
- Fewer wiring errors and rework
- Improved system reliability and less downtime
- Faster diagnostics and repairs
- Flexibility to use pre-tested subassemblies
- Ability to outsource assembly to lower cost regions
In many cases, the total installed cost of a Custom Cable Assembly is lower than using individual wires and connectors. There are also indirect cost savings from higher production yields, fewer field failures and warranty claims.
5. Enhanced Appearance
Custom cable assemblies have a clean, professional appearance that improves the perceived quality of the end product. Instead of a “rat’s nest” of tangled wires, the cable assemblies are neatly bundled and identified with labels. Sleeving or over-molding can be used to give the cable assemblies a finished, sculpted look.
Careful attention to cable management and routing also enhances aesthetics. Custom cable assemblies can be designed with the optimal lengths and break-out locations for a given enclosure. Bulky connectors can be hidden out of sight. The result is an organized system that looks purposefully designed.
Design Considerations for Custom Cable Assemblies
Designing a custom cable assembly requires careful consideration of the electrical, mechanical and environmental requirements of the application. Key factors to consider include:
1. Electrical Requirements
- Number and gauges of conductors
- Voltage and current ratings
- Shielding against EMI/RFI
- Dielectric properties of insulation
- Capacitance and impedance characteristics
- Bandwidth and attenuation for high-speed signals
2. Mechanical Requirements
- Flexibility and bend radius
- Tensile strength and elongation
- Abrasion and cut-through resistance
- Crush and impact resistance
- Flammability and smoke generation
- Density and weight
3. Environmental Requirements
- Operating temperature range
- Resistance to chemicals, oils, solvents
- Resistance to moisture, fungus, UV
- Outgassing in vacuum
- Biocompatibility for medical applications
4. Terminations and Connectors
- Types of terminations (solder, crimp, IDC, etc.)
- Styles of connectors (circular, rectangular, card edge, etc.)
- Mating cycles and retention forces
- Plating finishes of contacts
- Sealing against moisture ingress
- Shielding effectiveness
- Keying and color coding
5. Cable Management and Protection
- Sleeve and jacket materials
- Strain reliefs and service loops
- Cable ties, clamps, and ducts
- Shielding termination and grounding
- Labels and markings
- Over-molding for mechanical protection
Designers need to balance these different requirements to arrive at an optimized cable assembly design. Trade-offs often need to be made between factors such as flexibility and durability, shielding effectiveness and weight, or material costs and performance.
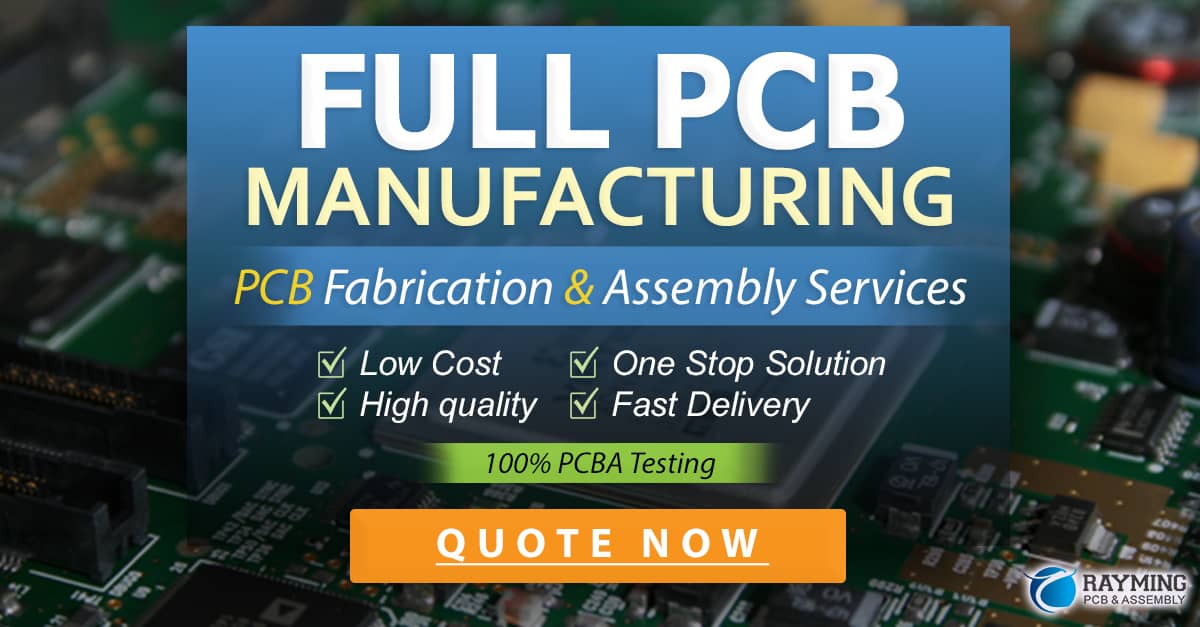
Cable Assembly Manufacturing Process
The manufacturing process for custom cable assemblies typically involves the following steps:
-
Engineering and Design: The cable assembly is designed based on the customer’s requirements and specifications. This includes creating schematic diagrams, bills of materials, and 3D CAD models.
-
Prototyping and Testing: Prototypes of the cable assembly are built and tested to validate the design. This may include electrical testing, mechanical stress testing, and environmental testing. Any issues are corrected before moving to production.
-
Wire Preparation: The individual wires are cut to length, striped, and tinned if necessary. The wires may also be twisted together to form pairs or triads.
-
Termination: The wires are terminated with connectors or terminals using crimping, soldering, or IDC methods. Automated equipment is often used to ensure consistent quality.
-
Assembly: The terminated wires are bundled together into the cable assembly. This may involve adding labels, sleeves, tapes, braids, or other components. The assembly is secured with cable ties or clamps.
-
Inspection and Testing: The completed cable assembly is visually inspected and electrically tested to ensure it meets all requirements. This includes continuity testing, insulation resistance testing, and high potential testing.
-
Packaging and Shipping: The cable assemblies are packaged to protect them during shipping and storage. This may include individual bags, boxes, or reels depending on the size and quantity of the assemblies.
Quality control is critical throughout the manufacturing process to ensure consistent and reliable cable assemblies. This includes incoming inspection of raw materials, in-process inspection during assembly, and final testing of completed assemblies.
Many Cable Assembly Manufacturers are certified to quality standards such as ISO 9001, AS9100 for aerospace, or ISO 13485 for medical devices. These certifications provide assurance that the manufacturer has well-defined and controlled processes in place.
Types of Custom Cable Assemblies
There are many different types of custom cable assemblies designed for specific applications and environments. Some common types include:
1. Molded Cable Assemblies
Molded cable assemblies have a protective over-mold or sleeve that encapsulates the wires and connectors. The molding can be made from various materials such as PVC, polyurethane, or silicone depending on the requirements for flexibility, durability, and environmental resistance.
Molded cable assemblies offer several benefits:
- Strain relief and protection at connector interfaces
- Improved aesthetic appearance
- Seal against moisture and contamination
- Resistance to abrasion, chemicals, or UV exposure
- Color coding and branding with logos
2. Flat Ribbon Cable Assemblies
Flat ribbon cable assemblies consist of multiple conductors laid side-by-side in a flat, rectangular profile. The conductors are typically 28 to 34 AWG with a pitch of 0.05 inches (1.27 mm). The flat profile allows for high density connections and reduces cable bulk.
Ribbon cables are commonly terminated with insulation displacement connectors (IDCs) that pierce through the insulation to contact the conductors. The IDCs may be in the form of crimp connectors or press-fit connectors such as D-subminiature or PCB transition headers.
Flat ribbon cable assemblies are used extensively in electronics for internal interconnects between PCBs, displays, and other components. They are also used for external connections to printers, scanners, and test equipment.
3. Coaxial Cable Assemblies
Coaxial cable assemblies are designed to carry high-frequency signals with low loss and high immunity to interference. They consist of a center conductor surrounded by an insulating dielectric, a braided or foil shield, and an outer jacket.
Coaxial cables are terminated with various types of connectors optimized for RF performance, such as BNC, TNC, SMA, or Type N. The connectors must be carefully installed to maintain the characteristic impedance of the cable and minimize signal reflections.
Coaxial cable assemblies are used extensively in telecommunications, aerospace, defense, and test and measurement applications. They are essential for transmitting high-speed data, video, and RF signals.
4. Multi-Conductor Cable Assemblies
Multi-conductor cable assemblies contain multiple insulated conductors bundled together in a common jacket. The conductors may be color-coded or numbered for identification. The jacket provides mechanical protection and may be shielded to reduce EMI/RFI.
Multi-conductor cable assemblies are used for power distribution, signal transmission, and control applications. They offer design flexibility to optimize the number and gauges of conductors for a given application.
Multi-conductor cables can be terminated with a wide variety of connectors, such as circular, rectangular, or custom designed connectors. The connectors may include features such as locking mechanisms, sealing, shielding, or strain relief.
FAQ
1. What is the difference between a cable assembly and a wire harness?
Cable assemblies and wire harnesses are often used interchangeably, but there are some differences. A cable assembly typically refers to a group of wires or cables with connectors on one or both ends, while a wire harness refers to a group of wires that are bundled together and secured with ties, tape, or conduit. Wire harnesses may or may not have connectors attached. In practice, the terms are often used synonymously.
2. How do I specify a custom cable assembly?
To specify a custom cable assembly, you should provide as much detail as possible about your requirements, including:
- Number, gauges, and types of conductors
- Insulation and jacketing materials
- Shielding and grounding requirements
- Types of connectors or terminations
- Length and routing of the assembly
- Environmental conditions (temperature, moisture, chemicals, etc.)
- Applicable standards and certifications (UL, CSA, RoHS, etc.)
- Target price and production volume
It’s best to work closely with a cable assembly manufacturer to develop a detailed specification and design. They can offer guidance on materials, processes, and testing to ensure the cable assembly meets your needs.
3. What are the most common connectors used in cable assemblies?
There are countless types of connectors used in cable assemblies, depending on the application and industry. Some of the most common include:
- Circular connectors: M8, M12, M23, MIL-DTL-38999, MIL-DTL-5015
- Rectangular connectors: D-Sub, Micro-D, DIN 41612, MIL-DTL-83513
- Modular connectors: RJ45, USB, HDMI, D-Sub
- Terminal blocks and barrier strips
- Crimp lugs and ring terminals
- Board-to-board connectors
- Wire-to-wire splices and taps
The choice of connector depends on factors such as the number of contacts, current and voltage ratings, environmental sealing, mating cycles, and compatibility with industry standards.
4. How long does it take to get custom cable assemblies?
The lead time for custom cable assemblies depends on the complexity of the design, the availability of materials, and the production capacity of the manufacturer. Simple cable assemblies using standard materials and processes may have lead times as short as a few days, while complex assemblies with custom components and special testing requirements may take several weeks or months.
Most cable assembly manufacturers offer expedited services for urgent needs, but this may come at a premium cost. It’s best to plan ahead and place orders well in advance of your production needs to ensure on-time delivery.
5. How much do custom cable assemblies cost?
The cost of custom cable assemblies depends on many factors, including:
- Number and type of conductors
- Insulation and jacketing materials
- Types of connectors or terminations
- Length and complexity of the assembly
- Testing and certification requirements
- Production volume and lead time
In general, custom cable assemblies have higher upfront costs compared to off-the-shelf cables due to the engineering and setup involved. However, they can offer significant savings in terms of installation time, reliability, and total cost of ownership.
Cable assembly manufacturers typically offer volume discounts for larger orders, as well as cost savings for using standard components and processes. It’s best to work with the manufacturer to optimize the design and manufacturing process for your specific needs and budget.
In conclusion, custom cable assemblies offer many benefits over off-the-shelf cables or field wiring, including improved reliability, simplified installation, and lower total costs. By carefully specifying and designing the cable assembly for your specific application, you can ensure optimal performance and longevity. Working closely with an experienced cable assembly manufacturer can help you navigate the many options and trade-offs to arrive at the best solution for your needs.
0 Comments