The Importance of Choosing the Right Cable Assembly Manufacturer
Selecting the right cable assembly manufacturer is a critical decision that can have a significant impact on the success of your electronic products. Here are some key reasons why choosing the right manufacturer is so important:
Quality and Reliability
The quality and reliability of your cable assemblies directly affect the performance and longevity of your electronic devices. A reputable cable assembly manufacturer will use high-quality materials, adhere to strict manufacturing standards, and employ rigorous testing procedures to ensure that their products meet or exceed industry standards.
Cost-Effectiveness
While it may be tempting to choose a manufacturer based solely on price, it’s essential to consider the long-term cost-effectiveness of your decision. A low-quality cable assembly may lead to increased maintenance costs, product failures, and customer dissatisfaction, ultimately costing you more in the long run.
Timely Delivery
In today’s fast-paced business environment, meeting deadlines is crucial. A reliable cable assembly manufacturer will have a proven track record of delivering products on time, even in the face of unexpected challenges or tight schedules.
Customization and Flexibility
Every electronic product has unique requirements, and your cable assembly manufacturer should be able to adapt to your specific needs. Look for a manufacturer that offers customization options and has the flexibility to accommodate your design changes or production scale.
Key Factors to Consider When Choosing a Cable Assembly Manufacturer
Now that we’ve established the importance of selecting the right cable assembly manufacturer, let’s delve into the key factors you should consider during the selection process.
Industry Experience and Expertise
When evaluating potential cable assembly manufacturers, consider their industry experience and expertise. Look for a manufacturer with a proven track record of serving clients in your specific industry, as they will have a better understanding of your unique requirements and challenges.
Additionally, assess the manufacturer’s technical expertise and their ability to provide valuable insights and recommendations based on their experience. A knowledgeable manufacturer can help you optimize your cable assembly design, select the most suitable materials, and ensure compliance with relevant industry standards.
Manufacturing Capabilities and Facilities
Evaluate the manufacturing capabilities and facilities of the cable assembly manufacturer to ensure they can meet your production needs. Consider factors such as:
- Production capacity: Can the manufacturer handle your production volume and scale up as your business grows?
- Equipment and technology: Does the manufacturer invest in state-of-the-art equipment and technology to ensure consistent quality and efficiency?
- Cleanroom facilities: If your cable assemblies require a controlled environment, does the manufacturer have certified cleanroom facilities?
Quality Control and Testing Procedures
A robust quality control system is essential for ensuring the consistency and reliability of your cable assemblies. When selecting a manufacturer, inquire about their quality control processes and testing procedures. Some key aspects to consider include:
- Incoming material inspection: Does the manufacturer have a strict process for inspecting and qualifying incoming materials?
- In-process quality checks: Are there regular quality checks throughout the manufacturing process to identify and correct any issues early on?
- Final testing and inspection: Does the manufacturer perform thorough final testing and inspection to ensure that the finished products meet all specified requirements?
Certifications and Compliance
Depending on your industry and target markets, your cable assemblies may need to comply with various standards and regulations. When choosing a cable assembly manufacturer, verify that they hold the necessary certifications and comply with relevant standards, such as:
- ISO 9001: Quality Management System
- IPC/WHMA-A-620: Requirements and Acceptance for Cable and Wire Harness Assemblies
- UL (Underwriters Laboratories) certifications
- RoHS (Restriction of Hazardous Substances) compliance
A manufacturer with the appropriate certifications demonstrates their commitment to quality and ensures that your cable assemblies will meet the required standards.
Customer Service and Support
Excellent customer service and support are essential for a smooth and successful partnership with your cable assembly manufacturer. Look for a manufacturer that prioritizes communication, responsiveness, and customer satisfaction.
Consider the following aspects when evaluating a manufacturer’s customer service:
- Dedicated account management: Will you have a dedicated point of contact who understands your needs and can promptly address any concerns or questions?
- Technical support: Does the manufacturer offer technical support to help you troubleshoot issues or optimize your cable assembly design?
- Flexibility and adaptability: Is the manufacturer willing to adapt to your changing needs and requirements?
The Cable Assembly Manufacturing Process
Understanding the cable assembly manufacturing process can help you better evaluate a manufacturer’s capabilities and ensure that they can produce cable assemblies that meet your specific requirements. Here’s a brief overview of the typical steps involved in the manufacturing process:
1. Design and Engineering
The first step in the cable assembly manufacturing process is the design and engineering phase. This involves creating a detailed design specification that outlines the physical and electrical characteristics of the cable assembly, such as:
- Cable type and size
- Conductor material and gauge
- Insulation and jacket materials
- Connector types and configurations
- Shielding requirements
- Environmental considerations (e.g., temperature, humidity, chemical exposure)
The manufacturer’s engineering team will review your design specification and provide recommendations to optimize the design for manufacturability, reliability, and cost-effectiveness.
2. Material Selection and Procurement
Once the design is finalized, the manufacturer will select and procure the necessary materials, such as cables, connectors, and accessories. A reputable manufacturer will have established relationships with reliable suppliers and will ensure that all materials meet the required specifications and quality standards.
3. Cable Cutting and Stripping
The next step is to cut the cables to the required lengths and strip the insulation from the ends to expose the conductors. This process is typically automated using specialized equipment to ensure consistent and precise results.
4. Connector Installation
After the cables are prepared, the connectors are installed using various methods, such as crimping, soldering, or welding. The choice of installation method depends on the connector type, the application requirements, and the manufacturer’s capabilities.
5. Assembly and Bundling
The individual cables are then assembled and bundled together according to the design specification. This may involve the use of cable ties, lacing, or other methods to ensure a neat and organized assembly.
6. Testing and Inspection
Throughout the manufacturing process, the cable assemblies undergo various testing and inspection procedures to ensure they meet the required quality standards. This may include:
- Continuity testing to verify electrical connections
- Insulation resistance testing to ensure adequate insulation between conductors
- Hipot (high potential) testing to detect any insulation breakdowns or leakage currents
- Visual inspection to check for any physical defects or damage
7. Packaging and Shipping
Finally, the finished cable assemblies are packaged and shipped to the customer. The packaging should be designed to protect the assemblies during transit and ensure they arrive in perfect condition.
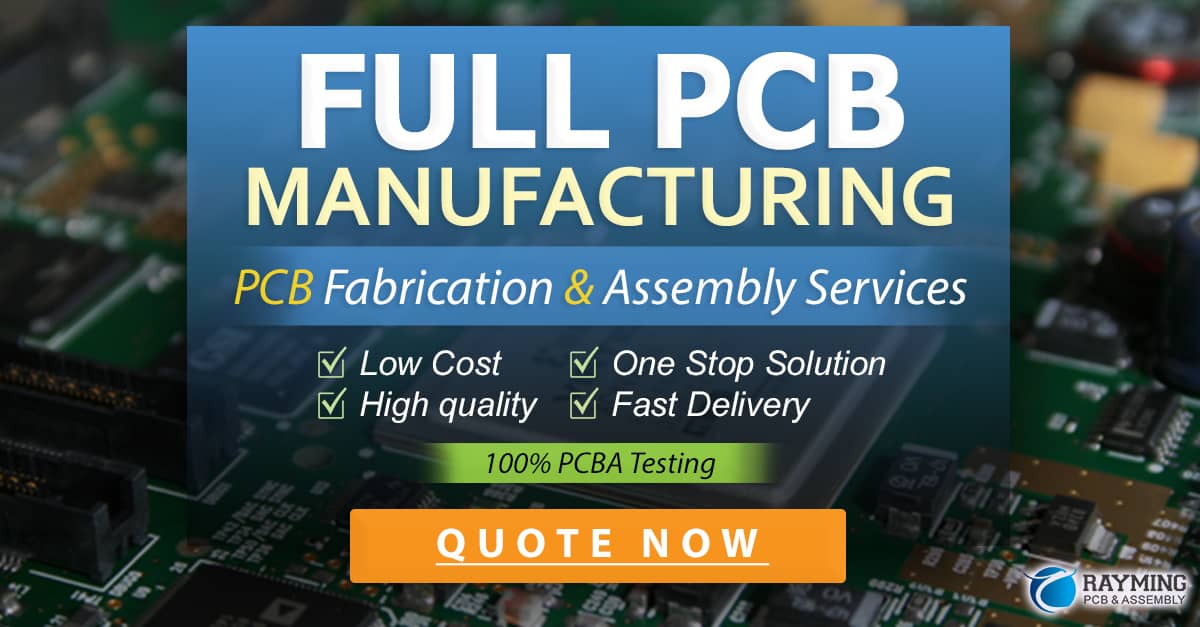
Frequently Asked Questions (FAQ)
1. How do I determine my cable assembly requirements?
To determine your cable assembly requirements, consider the following factors:
- The application and environment in which the cable assembly will be used
- The required electrical and physical characteristics, such as voltage, current, signal type, and connector configurations
- Any industry-specific standards or regulations that the cable assembly must comply with
- The expected production volume and timeline
It’s essential to work closely with your cable assembly manufacturer to ensure that all requirements are clearly defined and documented in the design specification.
2. What is the typical lead time for cable assembly production?
The lead time for cable assembly production can vary depending on several factors, such as:
- The complexity of the design and the materials required
- The manufacturer’s production capacity and workload
- The availability of raw materials and components
- The required testing and certification processes
In general, lead times can range from a few weeks to several months. It’s important to discuss your timeline requirements with the manufacturer upfront and plan accordingly.
3. How can I ensure the quality of my cable assemblies?
To ensure the quality of your cable assemblies, consider the following:
- Choose a reputable cable assembly manufacturer with a proven track record of quality and reliability
- Clearly define and document your quality requirements in the design specification
- Discuss the manufacturer’s quality control processes and testing procedures in detail
- Request regular quality reports and conduct periodic audits to verify compliance
- Establish a quality agreement that outlines the roles, responsibilities, and expectations of both parties
4. What is the difference between custom and standard cable assemblies?
Custom cable assemblies are designed and manufactured to meet specific customer requirements, while standard cable assemblies are pre-designed and readily available off-the-shelf.
Custom cable assemblies offer the advantage of being tailored to your exact needs, but they may have longer lead times and higher costs due to the custom design and tooling required.
Standard cable assemblies are typically less expensive and have shorter lead times, but they may not meet all of your specific requirements.
The choice between custom and standard cable assemblies depends on your unique needs, budget, and timeline.
5. How can I reduce the cost of my cable assemblies without compromising quality?
There are several ways to reduce the cost of your cable assemblies without compromising quality:
- Optimize your design for manufacturability and simplicity, reducing the number of components and processes required
- Consider standardizing your cable assembly designs across multiple products or applications to achieve economies of scale
- Work with your cable assembly manufacturer to identify cost-saving opportunities, such as alternative materials or production methods
- Plan your production schedule in advance to avoid rush orders or expedited shipping, which can increase costs
- Establish a long-term partnership with your manufacturer to negotiate better pricing based on volume commitments and loyalty
Remember, while cost is an important consideration, it should not come at the expense of quality and reliability.
Conclusion
Choosing the perfect cable assembly manufacturer is a critical decision that requires careful consideration of various factors, such as industry experience, manufacturing capabilities, quality control, certifications, and customer service. By understanding the cable assembly manufacturing process and the key factors to consider, you can make an informed decision that ensures the quality, reliability, and performance of your electronic products.
Remember to clearly define your requirements, communicate openly with your manufacturer, and establish a strong partnership based on trust and mutual success. With the right cable assembly manufacturer by your side, you can focus on your core business while leaving the complexities of cable assembly production in capable hands.
0 Comments