What is PCB Electrical Testing?
PCB electrical testing is the process of verifying the electrical performance and functionality of a printed circuit board. It involves subjecting the PCB to various tests to ensure that it meets the specified electrical requirements and is free from defects such as short circuits, open circuits, and incorrect component placement.
Importance of PCB Electrical Testing
PCB electrical testing is essential for several reasons:
-
Quality Assurance: Electrical testing helps identify and eliminate defects early in the manufacturing process, ensuring that only high-quality PCBs are used in the final product.
-
Reliability: Thorough electrical testing reduces the risk of device failure in the field, enhancing the overall reliability of the electronic product.
-
Cost Savings: Detecting and fixing issues during the testing phase is more cost-effective than dealing with product recalls or repairs after the device has been shipped to customers.
-
Compliance: Electrical testing helps ensure that the PCB meets industry standards and regulatory requirements.
Types of PCB Electrical Tests
There are several types of electrical tests performed on PCBs, each focusing on different aspects of the board’s functionality. Let’s explore some of the most common tests:
Continuity Test
A continuity test checks for unintended open circuits or breaks in the PCB’s conductive paths. It verifies that the connections between components and traces are intact and have low resistance.
Isolation Test
An isolation test, also known as an insulation resistance test, checks for unintended short circuits between different conductive paths on the PCB. It ensures that there is sufficient electrical isolation between circuits that should not be connected.
Voltage Test
A voltage test measures the voltage levels at various points on the PCB to ensure they are within the specified tolerances. It helps identify issues such as incorrect power supply voltages or voltage drops across components.
Current Test
A current test measures the current flowing through specific circuits on the PCB. It verifies that the current levels are within the expected range and helps identify problems such as excessive current draw or short circuits.
Functional Test
A functional test evaluates the overall functionality of the PCB by simulating real-world operating conditions. It checks whether the PCB performs as intended and meets the desired specifications.
PCB Electrical Testing Equipment
To perform PCB electrical testing, various types of equipment are used. Some of the essential tools include:
Multimeter
A multimeter is a versatile instrument that can measure voltage, current, and resistance. It is commonly used for continuity and voltage tests.
Oscilloscope
An oscilloscope is used to visualize and analyze time-varying signals on the PCB. It helps in identifying issues such as signal integrity problems or timing errors.
In-Circuit Tester (ICT)
An in-circuit tester is an automated testing system that probes the PCB and performs a series of electrical tests. It can quickly identify faults and provide detailed diagnostic information.
Flying probe tester
A flying probe tester is an automated testing system that uses movable probes to contact specific points on the PCB. It offers flexibility in testing complex boards and can be programmed to perform various electrical tests.
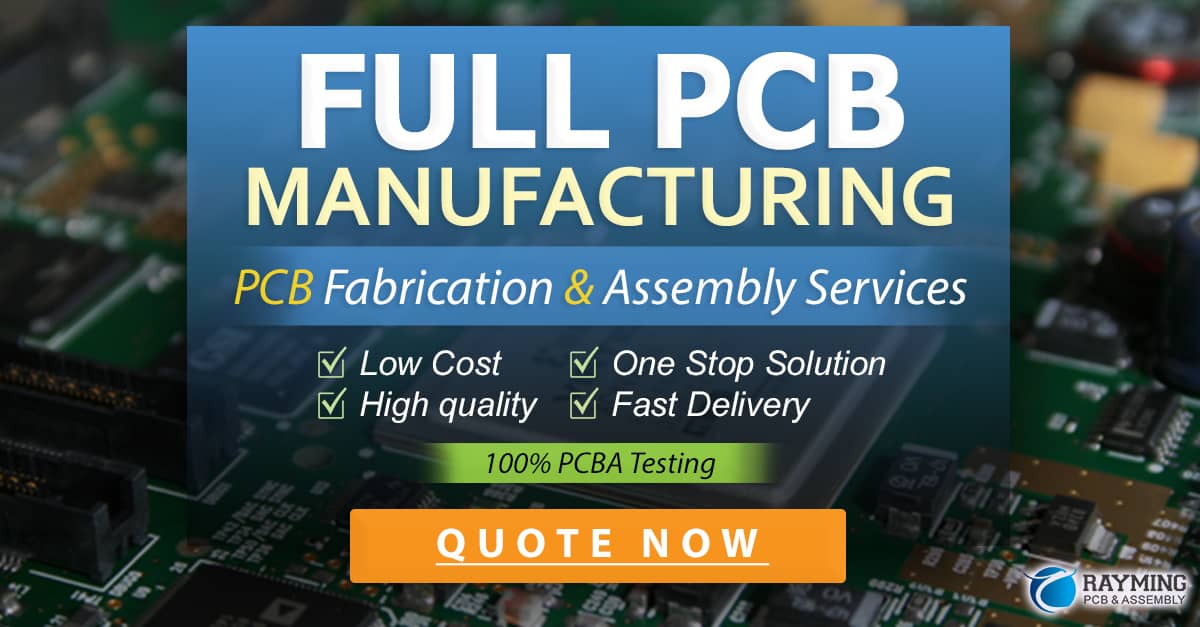
Best Practices for PCB Electrical Testing
To ensure effective and reliable PCB electrical testing, consider the following best practices:
-
Develop a Comprehensive Test Plan: Create a detailed test plan that covers all the necessary electrical tests based on the PCB’s design and requirements.
-
Use Appropriate Test Equipment: Select the right test equipment for each type of test, considering factors such as accuracy, resolution, and compatibility with the PCB.
-
Establish Clear Acceptance Criteria: Define clear pass/fail criteria for each test, based on the PCB’s specifications and industry standards.
-
Maintain Proper Test Environment: Ensure that the testing environment is clean, temperature-controlled, and free from electromagnetic interference (EMI) to obtain accurate test results.
-
Document Test Results: Maintain detailed records of the test results, including any issues found and corrective actions taken. This documentation helps in traceability and future reference.
Frequently Asked Questions (FAQ)
1. What is the difference between continuity and isolation tests?
A continuity test checks for unintended open circuits, ensuring that the connections between components and traces are intact. An isolation test, on the other hand, checks for unintended short circuits between different conductive paths, ensuring sufficient electrical isolation.
2. Can PCB electrical testing be automated?
Yes, PCB electrical testing can be automated using equipment such as in-circuit testers (ICT) and flying probe testers. Automated testing allows for faster and more consistent testing compared to manual methods.
3. How often should PCB electrical testing be performed?
PCB electrical testing should be performed at various stages of the manufacturing process, including prototype validation, pre-production, and production phases. The frequency of testing depends on factors such as the complexity of the PCB, the volume of production, and the criticality of the application.
4. What are the consequences of insufficient PCB electrical testing?
Insufficient PCB electrical testing can lead to several consequences, such as:
– Increased risk of device failure in the field
– Higher warranty and repair costs
– Potential safety hazards
– Damage to the company’s reputation
– Non-compliance with industry standards and regulations
5. How can I improve the efficiency of PCB electrical testing?
To improve the efficiency of PCB electrical testing, consider the following:
– Implement automated testing solutions
– Optimize test coverage by focusing on critical areas and high-risk components
– Use test fixtures and jigs to minimize setup time
– Regularly calibrate and maintain test equipment
– Continuously review and update test procedures based on feedback and new requirements
Conclusion
PCB electrical testing is a vital process in ensuring the quality, reliability, and functionality of electronic devices. By understanding the various types of tests, utilizing the right equipment, and following best practices, manufacturers can effectively identify and address issues early in the production cycle. Investing in comprehensive PCB electrical testing not only saves costs in the long run but also enhances customer satisfaction and builds a strong reputation in the industry.
Test Type | Purpose | Equipment |
---|---|---|
Continuity Test | Checks for open circuits | Multimeter |
Isolation Test | Checks for short circuits | Multimeter |
Voltage Test | Measures voltage levels | Multimeter, Oscilloscope |
Current Test | Measures current levels | Multimeter, Oscilloscope |
Functional Test | Evaluates overall functionality | In-Circuit Tester, Flying Probe Tester |
By embracing the importance of PCB electrical testing and implementing robust testing processes, manufacturers can deliver high-quality electronic products that meet the ever-increasing demands of the market.
0 Comments