Introduction to PCB Electrical Testing
Printed Circuit Board (PCB) manufacturing is a complex process involving multiple steps to create a functional board that meets the required specifications. One critical aspect of PCB manufacturing is electrical testing, which ensures that the manufactured board performs as intended and is free from defects.
Importance of Electrical Testing in PCB Manufacturing
Electrical testing is crucial in PCB manufacturing for several reasons:
1. Verifying functionality: Electrical testing confirms that the PCB functions as designed, with all components and connections working correctly.
2. Identifying defects: Testing helps identify any defects or issues in the PCB, such as short circuits, open circuits, or incorrect component placement.
3. Ensuring reliability: Thorough electrical testing ensures that the PCB will perform reliably in its intended application.
4. Meeting standards: Electrical testing helps ensure that the PCB meets industry standards and customer requirements.
Types of Electrical Tests in PCB Manufacturing
There are various types of electrical tests performed during PCB manufacturing, each serving a specific purpose. Some of the common tests include:
Continuity Test
A continuity test checks for unintended open circuits in the PCB. It verifies that all the intended connections are present and that there are no broken traces or missing components.
Isolation Test
An isolation test, also known as an insulation resistance test, checks for unintended short circuits between different parts of the PCB. It ensures that there is sufficient electrical isolation between components and traces that should not be connected.
Voltage Test
A voltage test measures the voltage levels at various points on the PCB to ensure they are within the expected range. This test helps identify any issues with power distribution or voltage regulation on the board.
Current Test
A current test measures the current flow through specific parts of the PCB to ensure it is within the expected range. This test helps identify any issues with current-carrying capacity or excessive power consumption.
Functional Test
A functional test verifies that the PCB performs its intended function correctly. This test typically involves applying input signals to the board and measuring the output signals to ensure they match the expected values.
PCB Electrical Testing Methods
There are several methods used for electrical testing of PCBs, each with its own advantages and limitations. Some of the common methods include:
Flying Probe Test
A flying probe test uses mobile probes that move across the PCB to make contact with specific test points. This method is flexible and can test a wide range of PCB designs, but it is relatively slow compared to other methods.
Bed of Nails Test
A bed of nails test uses a fixture with fixed probes that make contact with specific test points on the PCB. This method is faster than flying probe testing but requires a custom fixture for each PCB design.
In-Circuit Test (ICT)
An in-circuit test uses a bed of nails fixture to test individual components on the PCB. This method can identify defects at the component level but requires access to both sides of the board.
Boundary Scan Test
A boundary scan test uses built-in test circuitry in the components on the PCB to test the connections between them. This method can test complex boards with high component density but requires components that support boundary scan.
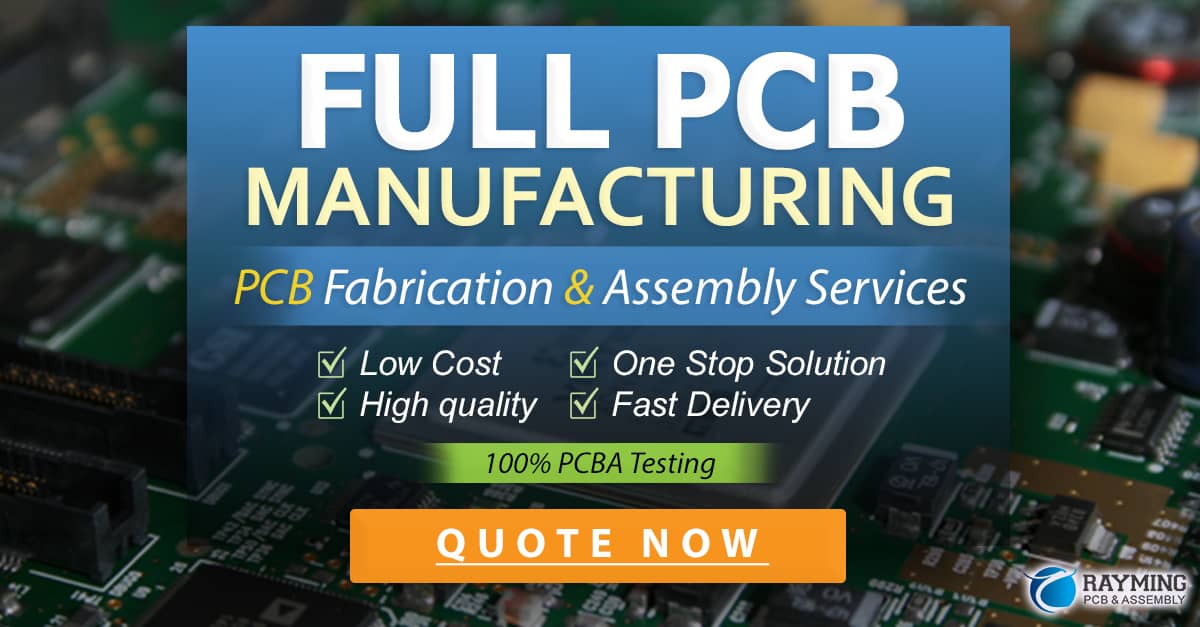
Electrical Test Coverage
Electrical test coverage refers to the extent to which a PCB is tested for defects and functionality. Higher test coverage means a more thorough test and a lower risk of defects going undetected.
Factors Affecting Test Coverage
Several factors can affect electrical test coverage, including:
– PCB design complexity
– Component types and packaging
– Test access points
– Test method limitations
– Time and cost constraints
Balanced Test Coverage
Achieving 100% test coverage is often impractical due to time and cost constraints. Instead, a balanced approach is used to maximize test coverage within the available resources.
Test Method | Typical Test Coverage |
---|---|
Flying Probe | 80-90% |
Bed of Nails | 90-95% |
In-Circuit Test | 95-98% |
Boundary Scan | 95-99% |
A combination of test methods is often used to achieve the desired test coverage while optimizing time and cost.
Electrical Test Fixtures
Electrical test fixtures are used to interface between the PCB and the test equipment. They provide a reliable and repeatable way to make contact with the test points on the board.
Types of Test Fixtures
There are two main types of electrical test fixtures:
1. Bed of nails fixture: Uses fixed probes to make contact with specific test points on the PCB.
2. Flying probe fixture: Uses mobile probes that move across the PCB to make contact with test points.
Fixture Design Considerations
Designing an electrical test fixture involves several considerations, including:
– Test point accessibility
– Probe type and placement
– Fixture durability and maintainability
– Signal integrity and shielding
– Fixture cost and lead time
A well-designed test fixture is crucial for reliable and efficient electrical testing of PCBs.
Electrical Test Data Analysis
Electrical test data analysis involves interpreting the results of the electrical tests to identify any defects or issues with the PCB.
Data Collection
Test data is typically collected by the test equipment and stored in a format that can be analyzed later. Common data formats include:
– CSV (Comma-Separated Values)
– XML (eXtensible Markup Language)
– Database files
Data Analysis Techniques
There are several techniques used for analyzing electrical test data, including:
– Limit comparison: Comparing test results against predefined limits to identify out-of-spec values.
– Trend analysis: Identifying trends or patterns in the test data that may indicate potential issues.
– Statistical analysis: Using statistical methods to identify significant deviations or anomalies in the test data.
Effective data analysis is crucial for identifying defects and improving the PCB manufacturing process.
Electrical Testing in the PCB Manufacturing Process
Electrical testing is typically performed at several stages during the PCB manufacturing process.
In-Process Testing
In-process testing is performed during the PCB assembly process to identify defects as early as possible. This can include:
– Solder paste inspection
– Automated optical inspection (AOI)
– X-ray inspection
Final Testing
Final testing is performed after the PCB is fully assembled and ready for shipment. This typically includes:
– Continuity and isolation testing
– Voltage and current testing
– Functional testing
Rework and Repair
If defects are identified during testing, the PCB may need to be reworked or repaired. This can involve:
– Component replacement
– Trace repair
– Conformal coating touch-up
Effective rework and repair processes are crucial for minimizing scrap and ensuring the quality of the final product.
Electrical Testing Standards and Certifications
There are several standards and certifications that apply to electrical testing of PCBs.
IPC Standards
The IPC (Association Connecting Electronics Industries) publishes several standards related to PCB manufacturing and testing, including:
– IPC-A-610: Acceptability of Electronic Assemblies
– IPC-6012: Qualification and Performance Specification for Rigid Printed Boards
– IPC-9252: Requirements for Electrical Testing of Unpopulated Printed Boards
ISO Certification
The International Organization for Standardization (ISO) publishes several standards related to quality management and testing, including:
– ISO 9001: Quality Management Systems
– ISO/IEC 17025: General Requirements for the Competence of Testing and Calibration Laboratories
PCB manufacturers and testing facilities may seek ISO certification to demonstrate their commitment to quality and testing competence.
UL Certification
Underwriters Laboratories (UL) is a global safety certification company that provides testing and certification services for PCBs and other electronic products. UL certification demonstrates that a product meets specific safety and performance standards.
Meeting relevant standards and certifications is crucial for ensuring the quality and reliability of PCBs in critical applications.
Best Practices for Electrical Testing in PCB Manufacturing
To ensure effective and efficient electrical testing of PCBs, several best practices should be followed:
- Design for testability: PCBs should be designed with testing in mind, including adequate test access points and clear labeling.
- Choose the right test methods: Select test methods that provide the desired coverage and accuracy while optimizing time and cost.
- Develop comprehensive test plans: Create detailed test plans that specify the tests to be performed, the test equipment and fixtures to be used, and the acceptance criteria.
- Maintain test equipment and fixtures: Regularly calibrate and maintain test equipment and fixtures to ensure accurate and reliable test results.
- Analyze test data effectively: Use appropriate data analysis techniques to identify defects and trends, and take corrective action as needed.
- Continuously improve processes: Regularly review and improve electrical testing processes based on data analysis and feedback from customers and stakeholders.
By following these best practices, PCB manufacturers can ensure that their products meet the highest quality and reliability standards.
FAQ
What is electrical testing in PCB manufacturing?
Electrical testing is the process of verifying that a manufactured PCB functions as intended and meets the required specifications. It involves various tests to check for defects, measure electrical parameters, and ensure the overall quality of the board.
Why is electrical testing important in PCB manufacturing?
Electrical testing is crucial in PCB manufacturing to ensure that the final product functions correctly, reliably, and safely. It helps identify defects and issues that could lead to malfunctions or failures in the end application, which could be costly or even dangerous.
What are some common electrical tests performed on PCBs?
Some common electrical tests performed on PCBs include continuity testing, isolation testing, voltage and current testing, and functional testing. These tests check for issues such as open or short circuits, insufficient isolation between components, incorrect voltage or current levels, and overall functionality.
How is electrical test coverage determined for a PCB?
Electrical test coverage is determined by factors such as the PCB design complexity, component types and packaging, available test access points, test method limitations, and time and cost constraints. A combination of test methods is often used to achieve the desired coverage while optimizing resources.
What are some best practices for effective electrical testing in PCB manufacturing?
Some best practices for effective electrical testing in PCB manufacturing include designing for testability, choosing the right test methods, developing comprehensive test plans, maintaining test equipment and fixtures, analyzing test data effectively, and continuously improving processes based on feedback and data analysis.
Conclusion
Electrical testing is a critical aspect of PCB manufacturing that ensures the quality, reliability, and functionality of the final product. By understanding the various types of tests, methods, and best practices involved in electrical testing, PCB manufacturers can optimize their processes to deliver high-quality boards that meet the needs of their customers.
Effective electrical testing requires a combination of skilled personnel, advanced equipment, and robust processes. By investing in these areas and continuously improving based on data analysis and feedback, PCB manufacturers can stay competitive in an increasingly demanding industry.
As PCB technology continues to evolve, with higher component densities, faster speeds, and more complex designs, electrical testing will remain a crucial step in ensuring the success of these products. By staying up-to-date with the latest testing standards, methods, and best practices, PCB manufacturers can deliver the quality and reliability that their customers require.
0 Comments