Introduction
Printed circuit boards (PCBs) are an integral part of nearly every modern electronic device. From computers and smartphones to medical devices and vehicles, PCBs provide the foundation for mounting and connecting electronic components using conductive pathways etched from copper sheets laminated onto a non-conductive substrate. The fabrication of PCBs is a complex process involving many steps to transform raw materials into a finished board. In this guide, we will explore the key stages of manufacturing PCBs and the various techniques used by fabricators.
PCB Design and Layout
The first step in the PCB production workflow is designing the board layout. This involves using EDA (electronic design automation) software to map out the circuit schematics and arrange components. Some of the major considerations during design include:
- Component placement – efficient positioning to minimize wire length and crosstalk
- Routing – creating conductive copper pathways between components
- Stackup – selecting laminate materials and number of layers
- High-speed design – minimizing interference and optimizing signal integrity
- manufacturability – designing for ease of fabrication and assembly
For more complex boards, engineers will simulate the design to verify signal and power integrity before the layout data is sent to the fabrication shop.
Inner Layer Fabrication
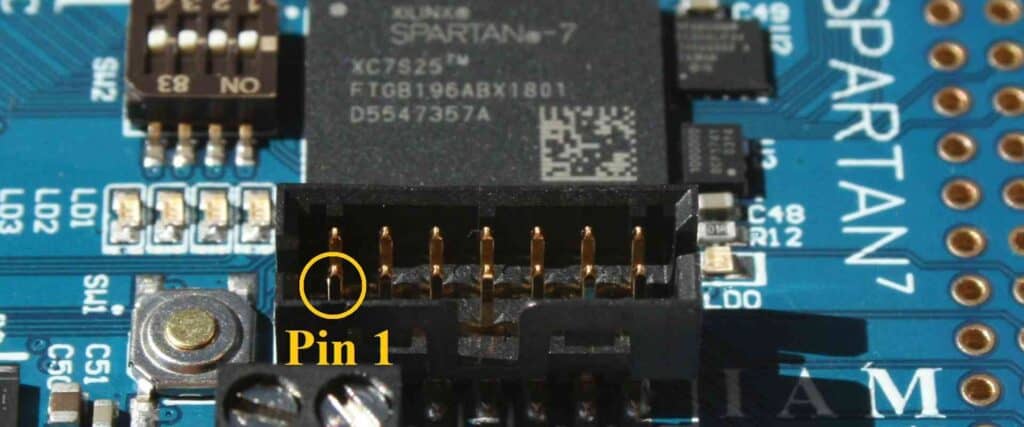
Most PCBs use a multilayer design with alternating layers of copper and substrate to allow for greater component density and more complex circuit routing. The inner layers are fabricated first in the case of multilayer boards. There are two principal methods used:
Subtractive Method
This technique starts with a blank laminate clad with copper on both sides:
- A photoresist (photosensitive polymer) is applied to the copper surfaces
- The board is exposed to UV light through a mask, transferring the circuit pattern onto the photoresist
- The exposed resist is dissolved, revealing the unexposed copper
- The uncovered copper is etched away, leaving only the desired circuit pattern
- The remaining photoresist is stripped away
This subtractive process is repeated for each internal layer. The main advantage is lower cost compared to other methods.
Additive Method
Rather than etching away copper, this technique builds up the conductive pattern:
- A bare laminate is coated with photoresist except for the areas that will become circuit traces
- Copper is electroplated onto the blank traces to desired thickness
- Photoresist is removed, leaving the plated circuit pattern behind
Additive processing produces finer trace resolution but at higher cost. It is better suited for HDI (high density interconnect) boards.
Layer Alignment
For multilayer boards, the etched inner layers must be precisely aligned. This is accomplished using registration holes to stack up the layers and ensure the circuit traces match. Alignment accuracy within 2 microns is standard.
Lamination
Once the inner layers are fabricated, they are interleaved with dielectric substrate layers called prepregs. This full stackup is laminated under heat and pressure to form a solid board. Prepregs flow to bond the layers together while copper layers are fused to adjacent dielectrics. The lamination process parameters are:
Parameter | Typical Range |
---|---|
Temperature | 180-200??C |
Pressure | 300-500 psi |
Time | 1-2 hours |
The lamination process permanently fuses the multilayer board structure.
Outer Layer Processing
After lamination, the outer layer circuitry can be formed using similar subtractive or additive processes described earlier. Additional steps are involved to prepare the outer surfaces:
- Surface preparation – Chemical cleaning and roughening to enable photoresist coating
- Photoresist application and imaging – Exposure of circuit patterns on both outer layers
- Developing – Removing unexposed photoresist
- Etching or plating – Subtractive etching or additive plating to form the circuits
- Stripping – Removing remaining photoresist
Outer layers often receive a solder mask layer to insulate copper and prevent solder bridging. Openings in the mask define solderable pads. An immersion silver coating is applied to maximize solderability.
Hole Drilling and Plating
Another essential fabrication step is drilling holes to allow component leads and vias to pass through the full PCB thickness. High-speed CNC drill presses are used to precisely drill thousands of holes in alignment across all layers. These holes are then plated with copper to form conductive vias.
Common hole features include:
- Through holes – span entire board thickness
- Blind vias – connect inner layers without reaching outer surface
- Buried vias – only connect inner layers
Hole Wall Preparation
A process called desmear is used to remove resin smear from hole walls to ensure good plating adhesion. This involves a light plasma etch followed by chemical cleaning.
Plating
The boards are submerged in a series of plating baths to deposit copper and then other metals like tin-lead:
- Electroless copper – initial copper layer
- Electrolytic copper – thicker copper plating
- Tin-lead alloy – etch-resistant protective coating
Solder Mask and Silkscreen
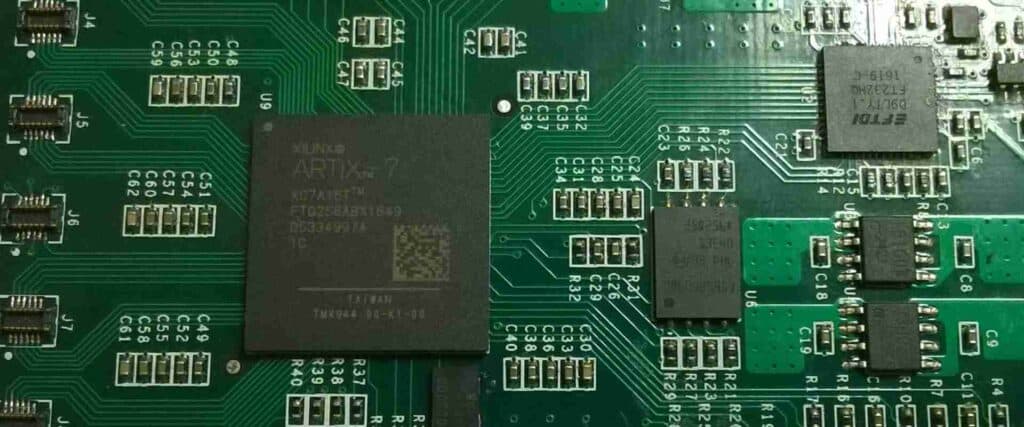
After basic board fabrication is complete, solder mask and silkscreen markings are often applied for aesthetic and functional purposes:
- Solder mask – epoxy layer over copper to control solder spreading
- Silkscreen – printed identifiers, symbols, and outlines using etch-resistant ink
These coatings provide corrosion resistance while allowing solder pads and components to remain exposed.
Final Finish
The last process steps help enhance solderability, protect against oxidation, and improve appearance:
- Immersion gold – thin layer of gold over exposed copper
- Immersion silver – silver plating for excellent solderability
- Organic surface protectant – prevents oxidation and enhances markings
This finish completes the PCB ready for shipment to electronics manufacturers.
Quality Control and Testing
Throughout the fabrication process, PCB manufacturers employ stringent quality control measures:
- Visual inspection of inner and outer layers
- Microsectioning to check layer registration
- Plating thickness measurement
- Hole size and position accuracy
- Etching quality and trace defects
Electrical testing is also conducted to validate board function. Common methods include:
- Continuity testing of traces and vias
- Dielectric constant measurement
- Impedance testing, especially for high-speed boards
- Functional testing of finished boards
Correcting issues found during testing can be done by reworking boards or adjusting processes for subsequent runs.
Summary of Key Fabrication Steps
Stage | Process |
---|---|
Inner Layers | Photolithography |
Etching/Plating | |
Layer stacking | |
Lamination | Fusing of layers |
Outer Layers | Surface preparation |
Photolithography | |
Etching/plating | |
Hole Drilling | CNC drilling |
Hole Plating | Copper electroplating |
Finishing | Plating, solder mask, silkscreen |
Testing | DFM, electrical, functional |
Advanced PCB Fabrication Techniques
As electronics become more complex and highly integrated, PCB manufacturers employ specialized techniques to meet exacting performance and density requirements. Some leading-edge fabrication methods include:
High Density Interconnect (HDI)
HDI utilizes thinner dielectric layers, finer lines and spaces, microvias, and often blind and buried vias. This allows for higher interconnect density to accommodate more components. HDI layers are combined with regular density regions on the same board.
Any Layer HDI
This technique allows microvias to pass between any two layers rather than just adjacent layers. This improves routing flexibility for increased layout density.
Embedded Passives
Passive components like resistors and capacitors are fabricated integral to the PCB by printing or plating thick film materials onto prepared inner layer areas. This saves space while enhancing electrical performance.
Flexible Circuits
Flexible PCBs use polyimide substrates that can bend and flex. Special materials and processes are required for photolithography, hole drilling, and lamination. Flex circuits enable curved and dynamic form factors.
Rigid-Flex
Combines standard rigid FR-4 boards with flexible polyimide sections to transition between zones with different contour requirements. Enables 3D packaging arrangements.
By leveraging these advanced fabrication methods, PCB manufacturers can produce boards to meet the needs of cutting-edge electronic devices and applications. The continual advancement of PCB technology will enable ongoing miniaturization and innovation.
Factors in Choosing a PCB Fabricator
Selecting a qualified PCB production partner is key to ensuring a robust, high-performing printed circuit board and smooth manufacturing experience. Here are some of the top factors to consider when choosing a fabrication shop:
Capabilities – The fabricator should offer all the processes required for a particular board construction including layer count, hole features, tracings, and finishes. Leading-edge methods like HDI are a plus.
Quality – Consistent production quality with thorough inspection, process control, and testing. Attention to detail is critical for complex board fabrication. ISO certification is desirable.
Technical Expertise – An experienced fabricator with knowledgeable engineering support can assess designs for manufacturability and provide guidance to avoid pitfalls. Valuable for advanced processes.
Volume Production – Ability to reliably produce at the scale required whether prototyping to full high-volume production. Flexible workflows are better.
Lead Time – Acceptable turnaround time from order placement to product delivery to suit project schedules and demands.
Communication – Clear contacts and status updates throughout the fabrication process. Quick resolution of any issues.
Cost – Competitive pricing for the required production quality, capabilities, and volumes. Avoid unrealistically lowball pricing.
Selecting a PCB fabricator with the right capabilities, quality systems, technical expertise and responsiveness ensures the best outcome for electronics projects on time and on budget.
Conclusion
The fabrication of printed circuit boards involves a complex, multi-stage manufacturing process with dozens of steps for creating the layered structure, circuitry, and hole interconnects. Key stages include design and layout, inner layer production using photolithographic and plating processes, lamination, outer layer fabrication, hole drilling and plating, final finishing, and extensive testing and inspection.
Advanced techniques like HDI, embedded passives, flexible circuits, and rigid-flex allow fabricators to produce PCBs to meet the needs of sophisticated, compact electronics. Choosing a fabrication partner with proven expertise and capabilities suited to the application is crucial for optimizing PCB design, function, and manufacturability. With rigorous quality control and process refinement, PCB fabricators continue to drive electronics innovation through ever-advancing board technology.
Circuit Board Fabrication FAQ
Here are answers to some frequently asked questions about printed circuit board fabrication:
What are the main steps in PCB fabrication?
The key stages are design/layout, inner layer production, lamination, outer layer processing, hole drilling/plating, finishing, and testing/inspection. Each phase involves many sub-processes using specialized materials and equipment.
How accurate is hole registration in multilayer boards?
Using precision registration techniques, drill hole positions can be aligned across layers with accuracy around 2 microns (0.002 mm). This allows vias to interconnect traces on different layers.
What is HDI technology?
High density interconnect (HDI) utilizes thinner dielectrics with tightly spaced traces and microvias. This enables higher component densities on boards. Sections of HDI are incorporated into standard PCBs.
What is a solder mask and what is its purpose?
A solder mask is a polymer coating applied over the PCB surface that leaves connecting pads exposed. It prevents solder from bridging between closely spaced traces and pads.
Why is surface finish important in PCB fabrication?
Surface finishes like immersion gold, immersion silver, and OSP enhance solderability, prevent oxidation, and improve marking adhesion. They help maximize board assembly yield.
0 Comments