Introduction
Circuit board assembly (CBA) is the process of soldering electronic components to a printed circuit board (PCB). It is an essential step in manufacturing electronic products like computers, mobile phones, and appliances. As electronics become more complex and miniaturized, CBA requires precision machinery, skilled technicians, and a highly controlled environment. This makes CBA a critical service that many product designers and engineers rely on.
This guide will provide a comprehensive overview of circuit board assembly services, including the assembly process, testing procedures, supply chain factors, and tips for choosing the right CBA partner. With an understanding of CBA services, product development teams can effectively plan PCB manufacturing and optimize costs, quality, and time-to-market.
The Circuit Board Assembly Process
CBA begins with the printed circuit board and involves multiple steps to solder components in place. Here is a general outline of the circuit board assembly process:
1. Solder Paste Application
The first step is to apply solder paste to the PCB. Solder paste is a sticky mixture of flux and solder alloy particles. It is usually applied by a solder stencil, which is laid over the PCB and spread with a squeegee. This deposits precise amounts of solder paste where solder joints will be located.
2. Component Placement
Electronic components like resistors, capacitors, and integrated circuits are precisely placed on the PCB according to the circuit diagram. High-speed pick-and-place machines automate this process by selecting components from feeders and rapidly placing them on the board.
3. Solder Reflow
The board then enters a reflow oven, which melts the solder paste to form permanent solder joints. The oven follows a thermal profile with different temperatures over time to properly melt the solder without damaging components. This attaches the components firmly to the board.
4. Cleaning and Inspection
After solder reflow, flux residue is cleaned from the board with solutions like isopropyl alcohol. Automated optical inspection (AOI) machines then verify all components were correctly placed and that there are no soldering defects.
5. Conformal Coating
For boards going into harsh environments, a protective conformal coating may be applied. This electrically insulates the board and prevents corrosion from moisture. Common coatings include acrylic, silicone, and parylene.
6. Additional Assembly
Additional assembly and mechanical integration steps may be needed to complete the product. This includes installing connectors, fasteners, heat sinks, and other hardware to the assembled PCB.
Testing and Quality Control
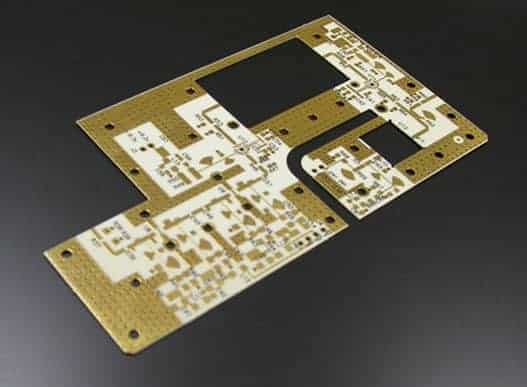
To validate the quality and functionality of the circuit board assembly, electronic manufacturers conduct thorough testing:
- In-circuit testing applies voltage and signals to test component functionality on the board. This verifies the board was assembled correctly.
- Functional testing powers up the fully populated board to validate the complete circuit works as intended. Issues like shorts, opens, and software bugs can be detected.
- Burn-in testing runs the board at elevated temperatures and voltages to induce failures. This weeds out infant mortality and marginal components.
- X-ray inspection uses radiographic imaging to examine internal solder joint quality. This finds problems like insufficient solder, voids, or cracks in joints.
Extensive testing requires significant equipment investment and skilled technicians. Board assembly providers should have rigorous quality control standards to ensure consistent and high-functioning circuit boards.
Supply Chain and Engineering Support
Besides assembly and testing expertise, choosing the right CBA partner also requires examining their whole supply chain and engineering capabilities:
- Component sourcing – They should have established networks of trusted component distributors, a strategy for allocating constrained parts, and systems to detect counterfeit parts.
- Inventory and logistics – The provider should have strong inventory management to avoid material shortages. They also need fast global logistics to deliver finished boards on schedule.
- Manufacturing scale – Larger facilities offer advantages like economies of scale, greater capacity for volume production, and redundancy to mitigate supply chain risks.
- Design for manufacturing (DFM) – Experienced engineers can assess PCB design and recommend optimizations for manufacturability, testability, and quality. This avoids issues before going to production.
- Co-engineering – Full collaboration with the CBA provider during design refinements and process qualifications ensures a smooth production ramp.
Selecting a CBA partner with these supply chain and engineering strengths can greatly improve the manufacturing experience.
Tips for Selecting a Circuit Board Assembly Provider
Here are important factors to consider when outsourcing circuit board assembly:
- Technology capabilities – Look for familiarity with the latest component packaging styles, fine-pitch interconnects, advanced soldering techniques, etc. This ensures they can assemble today’s cutting-edge electronics.
- Quality certifications – Providers should have quality management certifications like ISO 9001, IATF 16949 (automotive), and AS9100 (aerospace). This demonstrates disciplined quality control.
- Security – For IP-sensitive PCB designs, seek providers with robust cybersecurity and physical security to protect confidential product data.
- Continuous improvement – Leading companies emphasize continuous advancement in process control, quality, throughput, and capabilities. This drives innovation for customers.
- Global footprint – Choose suppliers with production sites close to target markets to shorten shipping times and localization.
- Sustainability – Environmentally conscious providers implement green initiatives in their facilities and supply chains. This improves energy efficiency, waste reduction, and chemical use.
By selecting a CBA partner using criteria like these, product teams can feel confident in achieving high-quality, on-time, and cost-effective printed circuit board assembly.
Frequently Asked Questions
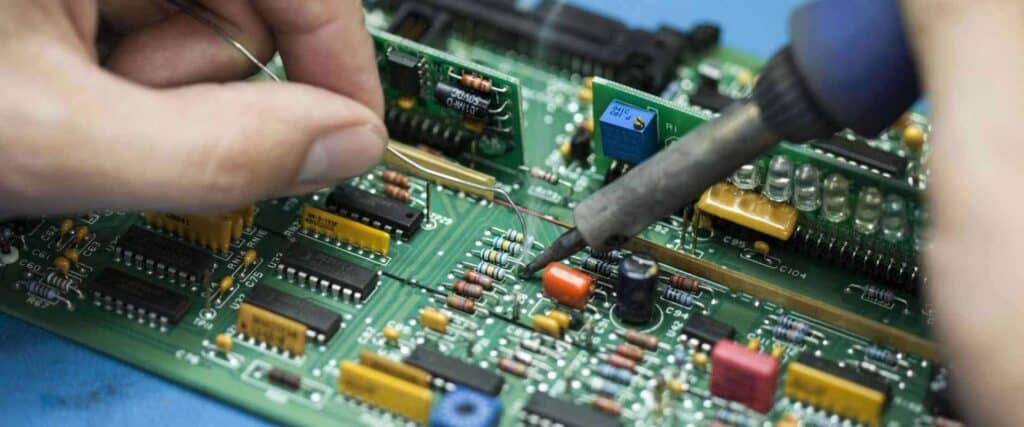
Here are answers to some common questions about circuit board assembly services:
What are the most common defects in PCB assembly?
Typical assembly defects include missing components, wrong component placement, poor solder joint quality, board warp/twist, and shorts between traces. Robust process controls during assembly and inspection aim to minimize defects.
How are very small components mounted on circuit boards?
Small chip components and microBGAs are precisely positioned by pick-and-place machines. The machines use advanced optical alignment and vacuum pickup tools to handle tiny parts. Fine-pitch soldering techniques electrically connect them.
How are through-hole components soldered?
Through-hole parts have wire leads that pass through holes in the PCB. Wave soldering machines solder all through-hole joints simultaneously by passing the bottom of the board over a wave of molten solder. This gives reliable, consistent soldering of through-hole components.
What testing is performed for telecom/network boards?
Telecom products require extensive testing focused on long-term reliability over years of continuous operation. Testing includes HALT (highly accelerated life testing), network simulation, temperature cycling, vibration, and mechanical shock tests.
How can PCB assembly be optimized for cost savings?
DFM analysis, component selection, and design simplification can significantly reduce assembly costs. Standardizing components, minimizing unique parts, maximizing SMT over through-hole parts, and increasing modularization also help optimize cost.
Conclusion
As PCBs remain core to electronic products, circuit board assembly is an essential manufacturing stage. The assembly process requires advanced machinery, stringent process controls, comprehensive testing, and close engineering collaboration between designers and assemblers. By selecting a CBA partner with rigorous quality systems, robust supply chain capabilities, and strong engineering support, product teams can stay focused on design while feeling confident in the manufacturing process. A trusted CBA provider becomes an extension of the product development team, driving innovation and quality for demanding industry applications.
0 Comments