Introduction to Wire Harness
A wire harness, also known as a cable harness or wiring assembly, is a vital component in various electrical and electronic systems. It is an organized bundle of wires, cables, and connectors that efficiently transmits electrical power and signals between different parts of a device or system. Wire harnesses are used in a wide range of applications, including automobiles, aerospace, medical equipment, telecommunications, and consumer electronics.
The primary purpose of a wire harness is to simplify the installation and maintenance of complex electrical systems by consolidating multiple wires into a single, compact unit. This not only saves space but also reduces the risk of wiring errors and improves the overall reliability of the system.
Key Components of a Wire Harness
A typical wire harness consists of several essential components:
-
Wires: The main component of a wire harness, wires are used to transmit electrical power and signals. They come in various sizes, materials (e.g., copper, aluminum), and insulation types (e.g., PVC, Teflon) depending on the application requirements.
-
Connectors: Connectors are used to join wires to other components or to other wire harnesses. They ensure secure and reliable connections and allow for easy installation and removal when necessary.
-
Terminals: Terminals are attached to the ends of wires and provide a means of connecting the wires to connectors or other components.
-
Insulation and Shielding: Wires are covered with insulation materials to protect them from damage and to prevent short circuits. In some cases, additional shielding may be used to protect the wires from electromagnetic interference (EMI).
-
Protective Coverings: Wire harnesses are often encased in protective coverings such as sleeves, tapes, or conduits to provide additional protection against abrasion, moisture, and other environmental factors.
Wire Harness Manufacturing Process
The manufacturing process for wire harnesses involves several key steps:
1. Design and Engineering
The first step in wire harness manufacturing is the design and engineering phase. This involves creating detailed schematics and diagrams that specify the layout, dimensions, and materials of the wire harness. Engineers use specialized software tools to create these designs, taking into account factors such as:
- Electrical requirements (e.g., voltage, current, resistance)
- Environmental conditions (e.g., temperature, humidity, vibration)
- Space constraints and routing paths
- Regulatory standards and safety requirements
2. Wire Cutting and Stripping
Once the design is finalized, the next step is to cut the wires to the required lengths and strip the insulation from the ends. This is typically done using automated wire cutting and stripping machines, which can process large volumes of wires quickly and accurately.
3. Crimping and Termination
After the wires are cut and stripped, terminals are attached to the ends using a process called crimping. Crimping involves compressing the terminal onto the wire using a special tool, creating a secure and reliable electrical connection. This process can be done manually or using automated crimping machines.
4. Assembly and Routing
The next step is to assemble the individual wires into the final wire harness configuration. This involves bundling the wires together and securing them with ties, tapes, or other fasteners. The wires are then routed through the designated paths, following the design schematics.
5. Connector Installation
Once the wires are assembled and routed, connectors are installed at the appropriate locations. This involves inserting the terminated wires into the connector housing and securing them in place. Some connectors may require additional steps, such as soldering or potting, to ensure a reliable connection.
6. Testing and Quality Control
Before the wire harness is considered complete, it must undergo rigorous testing and quality control procedures to ensure that it meets the required specifications and performs as intended. This may involve visual inspections, continuity tests, insulation resistance tests, and functional tests under various environmental conditions.
7. Packaging and Shipping
Finally, the completed wire harness is packaged for shipping and delivery to the customer. Packaging materials are selected based on the specific requirements of the application, such as ESD protection or moisture resistance.
Benefits of Using Wire Harnesses
Using wire harnesses offers several key benefits over traditional point-to-point wiring:
-
Simplicity: Wire harnesses consolidate multiple wires into a single, organized bundle, simplifying installation and maintenance.
-
Reliability: By using pre-assembled wire harnesses, the risk of wiring errors is greatly reduced, improving the overall reliability of the system.
-
Space Savings: Wire harnesses allow for more efficient use of space, as the wires are bundled together and routed through designated paths.
-
Cost Efficiency: While the initial cost of a wire harness may be higher than individual wires, the overall cost savings in terms of installation time, maintenance, and reduced downtime can be significant.
-
Customization: Wire harnesses can be customized to meet the specific requirements of each application, allowing for greater flexibility in design and functionality.
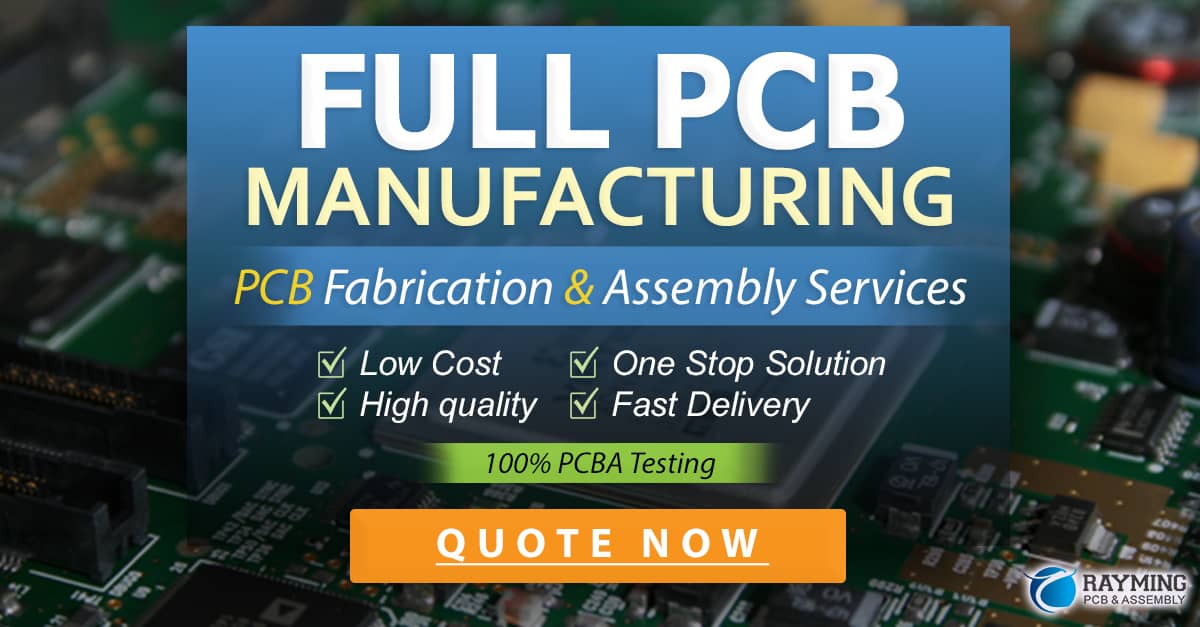
Applications of Wire Harnesses
Wire harnesses are used in a wide range of industries and applications, including:
Automotive
In the automotive industry, wire harnesses are used extensively to connect various electrical components and systems, such as the engine control unit, sensors, actuators, and multimedia systems. Automotive wire harnesses must be designed to withstand harsh environmental conditions, including extreme temperatures, vibration, and exposure to moisture and chemicals.
Aerospace
Aerospace applications require wire harnesses that are lightweight, reliable, and able to withstand extreme environmental conditions. Wire harnesses are used in aircraft for power distribution, avionics, and communication systems. They must meet strict regulatory standards for safety and performance.
Medical Equipment
Medical equipment, such as patient monitors, diagnostic devices, and surgical instruments, rely on wire harnesses to transmit electrical signals and power. These wire harnesses must be designed to meet stringent safety and reliability requirements, as well as being resistant to sterilization processes.
Telecommunications
In the telecommunications industry, wire harnesses are used to connect various components within a network, such as routers, switches, and servers. These wire harnesses must be designed for high-speed data transmission and EMI protection.
Consumer Electronics
Consumer electronics, such as smartphones, laptops, and home appliances, use wire harnesses to connect internal components and provide power. These wire harnesses must be compact, lightweight, and able to withstand the stresses of daily use.
Designing Wire Harnesses for Specific Applications
When designing a wire harness for a specific application, several key factors must be considered:
-
Electrical Requirements: The wire harness must be designed to meet the electrical requirements of the system, including voltage, current, and resistance.
-
Environmental Conditions: The wire harness must be able to withstand the environmental conditions it will be exposed to, such as temperature, humidity, and vibration.
-
Space Constraints: The wire harness must be designed to fit within the available space and follow the designated routing paths.
-
Regulatory Standards: The wire harness must comply with relevant regulatory standards and safety requirements, such as UL, CSA, or IPC/WHMA-A-620.
-
Material Selection: The materials used in the wire harness, including wires, connectors, and protective coverings, must be selected based on the specific requirements of the application.
Wire Harness Testing and Quality Control
To ensure that a wire harness meets the required specifications and performs as intended, several testing and quality control procedures are employed:
-
Visual Inspection: A visual inspection is performed to check for any visible defects, such as damaged wires, loose connections, or incorrect routing.
-
Continuity Test: A continuity test is performed to ensure that each wire in the harness is properly connected and there are no breaks or short circuits.
-
Insulation Resistance Test: An insulation resistance test is performed to ensure that the insulation of the wires is intact and there are no leakage paths.
-
Functional Test: A functional test is performed to ensure that the wire harness performs as intended under various operating conditions.
-
Environmental Testing: In some cases, the wire harness may be subjected to environmental testing, such as temperature cycling or vibration testing, to ensure that it can withstand the expected operating conditions.
Frequently Asked Questions (FAQs)
1. What is the difference between a cable and a wire harness?
While the terms “cable” and “wire harness” are often used interchangeably, there is a slight difference between the two. A cable typically refers to a single insulated conductor or a group of conductors bundled together, while a wire harness is a more complex assembly of multiple cables, wires, and connectors designed for a specific application.
2. Can wire harnesses be repaired if damaged?
In most cases, wire harnesses can be repaired if damaged. However, the extent of the damage and the specific application will determine the feasibility and cost-effectiveness of the repair. Minor damage, such as a single broken wire, can often be repaired by splicing in a new section of wire. More extensive damage may require the replacement of the entire wire harness.
3. How are wire harnesses protected from environmental factors?
Wire harnesses are protected from environmental factors through the use of various materials and techniques, such as:
- Insulation materials (e.g., PVC, Teflon) that provide electrical insulation and protection from moisture and chemicals.
- Shielding materials (e.g., foil, braid) that protect against electromagnetic interference (EMI).
- Protective coverings (e.g., sleeves, tapes, conduits) that provide additional protection against abrasion and other physical damage.
4. What are the most common materials used for wire harness conductors?
The most common materials used for wire harness conductors are:
- Copper: Copper is the most widely used conductor material due to its excellent electrical conductivity, ductility, and relatively low cost.
- Aluminum: Aluminum is sometimes used as a conductor material in applications where weight savings are critical, such as in aerospace. However, it has lower conductivity than copper and requires special termination techniques.
5. How can I ensure that my wire harness design meets the necessary regulatory standards?
To ensure that your wire harness design meets the necessary regulatory standards, you should:
- Consult the relevant standards and regulations for your specific application and industry (e.g., UL, CSA, IPC/WHMA-A-620).
- Work with experienced wire harness manufacturers who are familiar with the regulatory requirements and can guide you through the design and manufacturing process.
- Perform thorough testing and quality control procedures to verify that the wire harness meets the required specifications and standards.
Conclusion
Cable and wire harness assembly is a critical aspect of many electrical and electronic systems, providing a reliable and efficient means of transmitting power and signals between components. By understanding the key components, manufacturing processes, and design considerations involved in wire harness assembly, engineers and manufacturers can create high-quality, customized solutions for a wide range of applications.
As technology continues to advance and systems become increasingly complex, the importance of well-designed and manufactured wire harnesses will only continue to grow. By staying up-to-date with the latest materials, techniques, and regulatory standards, wire harness manufacturers can ensure that they are providing their customers with the best possible solutions for their specific needs.
0 Comments