Introduction to Wire Harness Manufacturing
Wire harness manufacturing is a crucial process in various industries, such as automotive, aerospace, and electronics. A wire harness, also known as a cable harness or wiring loom, is an organized assembly of electrical cables, wires, and connectors that transmit signals or electrical power throughout a vehicle, aircraft, or other electrical system. The manufacturing process of wire harnesses involves several steps, each requiring precision, accuracy, and attention to detail.
In this comprehensive guide, we will walk you through the step-by-step process of wire harness manufacturing, from design and prototyping to final assembly and testing. We will also discuss the importance of quality control, the various materials and tools used, and the benefits of automation in wire harness production.
The Importance of Wire Harness Manufacturing
Wire harnesses play a critical role in the functioning and safety of electrical systems. They ensure that electrical signals and power are transmitted efficiently and reliably, while also protecting the wires and cables from damage due to environmental factors such as heat, moisture, and abrasion.
Properly designed and manufactured wire harnesses offer several benefits:
- Improved system reliability and performance
- Reduced installation time and costs
- Enhanced safety and protection against electrical faults
- Simplified maintenance and troubleshooting
- Increased flexibility in system design and configuration
Step 1: Design and Engineering
The wire harness manufacturing process begins with the design and engineering phase. This step involves creating a detailed blueprint of the wire harness, including the specific requirements for wires, connectors, and other components.
3D Modeling and Computer-Aided Design (CAD)
Engineers use 3D modeling and CAD software to create a virtual representation of the wire harness. This allows them to visualize the layout, routing, and dimensions of the harness, as well as identify any potential issues or conflicts with other components in the system.
Bill of Materials (BOM) Creation
Once the design is finalized, engineers create a Bill of Materials (BOM) that lists all the components required for the wire harness, including:
- Wires and cables
- Connectors and terminals
- Grommets and seals
- Labels and identification markers
- Heat shrink tubing and other protective materials
The BOM serves as a guide for the procurement and inventory management of the necessary materials.
Prototyping and Testing
Before moving into full-scale production, engineers create a prototype of the wire harness to test its functionality, durability, and compatibility with the intended application. This allows for any necessary adjustments or improvements to be made before finalizing the design.
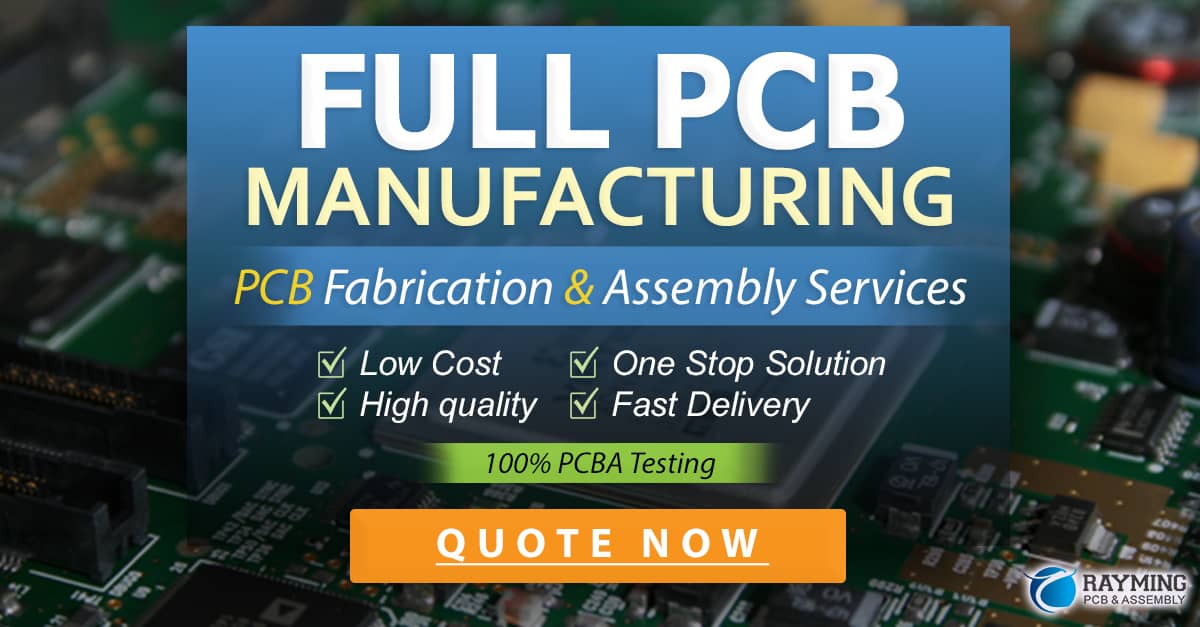
Step 2: Material Preparation
Once the design is finalized and the BOM is created, the next step is to prepare the materials for production. This involves sourcing the required components, cutting the wires and cables to the appropriate lengths, and stripping the insulation from the ends.
Wire and Cable Cutting
Wires and cables are cut to the specified lengths using automated cutting machines or manual tools, such as wire cutters or scissors. The cutting process must be precise to ensure that the wires fit properly within the harness and connect accurately to the corresponding components.
Wire Stripping
After cutting, the insulation is stripped from the ends of the wires to expose the bare conductor. This allows for the attachment of connectors or terminals. Wire stripping can be done manually using wire strippers or automatically using machine strippers, which can process multiple wires simultaneously.
Connector and Terminal Crimping
Connectors and terminals are attached to the stripped ends of the wires using a process called crimping. Crimping involves compressing the connector or terminal onto the wire using a specialized tool, creating a secure and reliable electrical connection. Crimping can be performed manually or with automated crimping machines for higher volume production.
Step 3: Wire Harness Assembly
With the materials prepared, the next step is to assemble the wire harness according to the design specifications. This involves routing the wires, bundling them together, and securing them with appropriate fasteners and protective materials.
Wire Routing and Bundling
Wires are routed and bundled together based on the harness layout and design. This process involves organizing the wires into groups or branches, ensuring that they are properly separated and not crossing or tangling with each other. Wires can be bundled using various methods, such as tying with string, tape, or zip ties, or using specialized harness board accessories like wire saddles or anchor pins.
Harness Boarding
Harness boarding is a technique used to keep the wires organized and secure during the assembly process. The wire harness is laid out on a specialized board or jig, which holds the wires in place and provides a stable platform for attaching connectors, terminals, and other components. The board may have pre-defined paths or channels for routing the wires, as well as designated spots for attaching fasteners or labels.
Connector and Terminal Installation
Once the wires are routed and bundled, the connectors and terminals are installed according to the design specifications. This involves inserting the crimped wires into the appropriate connector cavities or terminal positions and ensuring that they are fully seated and secure. Some connectors may require additional steps, such as applying sealing plugs or locking mechanisms to prevent moisture ingress or accidental disconnection.
Labeling and Identification
To facilitate installation and maintenance, wire harnesses are often labeled or marked with identifying information, such as the harness name, wire gauges, or connector designations. Labels can be applied using various methods, such as adhesive stickers, heat shrink sleeves, or directly printing on the wire insulation. Proper labeling ensures that the harness can be easily identified and troubleshot in the field.
Step 4: Quality Control and Testing
Quality control and testing are critical steps in the wire harness manufacturing process to ensure that the harnesses meet the required specifications and performance standards. This involves visual inspections, electrical testing, and functional testing to verify the integrity and reliability of the harness.
Visual Inspection
Visual inspection is the first line of defense in quality control. Technicians visually examine the wire harness for any defects, such as damaged insulation, loose connections, or incorrect routing. They also verify that all components are present and properly installed according to the design specifications.
Electrical Testing
Electrical testing is performed to ensure that the wire harness is free from short circuits, open circuits, or other electrical faults. This typically involves using specialized test equipment, such as a continuity tester or a high-voltage insulation tester, to measure the resistance, insulation resistance, and dielectric strength of the wires and connectors.
Functional Testing
Functional testing involves connecting the wire harness to the intended system or a simulator and verifying that it performs as expected under various operating conditions. This may include testing the harness under different voltage levels, temperatures, vibrations, or other environmental factors to ensure that it can withstand the intended application.
Automated Testing
For high-volume production or complex harnesses, automated testing systems can be used to improve efficiency and accuracy. These systems use specialized software and hardware to perform electrical and functional tests automatically, reducing the risk of human error and increasing the speed of testing.
Step 5: Packaging and Shipping
Once the wire harness has passed all quality control and testing procedures, it is ready for packaging and shipping to the customer or the next stage of the manufacturing process.
Packaging
Wire harnesses are typically packaged in a manner that protects them from damage during transportation and storage. This may involve using specialized containers, such as plastic trays or boxes, with foam inserts or dividers to keep the harnesses separated and secure. The packaging may also include any necessary documentation, such as installation instructions or quality certificates.
Labeling and Identification
The packaging is labeled with relevant information, such as the part number, quantity, and customer information, to ensure that it can be easily identified and tracked throughout the supply chain.
Shipping
Wire harnesses are shipped to the customer or the next stage of the manufacturing process using appropriate transportation methods, such as trucks, ships, or aircraft, depending on the size, weight, and destination of the shipment. Proper handling and storage procedures are followed to ensure that the harnesses arrive at their destination in the same condition as they left the manufacturing facility.
Automation in Wire Harness Manufacturing
Automation plays an increasingly important role in wire harness manufacturing, as it helps to improve efficiency, reduce costs, and ensure consistent quality. Some of the key areas where automation is used include:
Wire Cutting and Stripping
Automated wire cutting and stripping machines can process large volumes of wires quickly and accurately, reducing the time and labor required for these tasks. These machines can be programmed to handle different wire gauges and insulation types, and can even perform multiple operations simultaneously, such as cutting, stripping, and crimping.
Crimping and Terminal Insertion
Automated crimping machines ensure consistent and reliable crimping of connectors and terminals, eliminating the risk of human error. These machines can be integrated with wire feeding systems and terminal applicators to further streamline the process.
Harness Assembly
Automated harness assembly systems, such as robotic arms or conveyor systems, can be used to route and bundle wires according to a predetermined layout. These systems can also install connectors, terminals, and other components, as well as apply labels or markings.
Testing and Inspection
Automated testing and inspection systems can perform electrical and functional tests on wire harnesses quickly and accurately, reducing the time required for quality control. These systems can also generate detailed test reports and data logs for traceability and analysis.
Materials and Tools Used in Wire Harness Manufacturing
Wire harness manufacturing involves a wide range of materials and tools, each serving a specific purpose in the production process. Some of the key materials and tools include:
Wires and Cables
Wires and cables are the primary components of a wire harness. They are available in various gauges, insulation types, and colors to suit different applications and environments. Common wire and cable types include:
- Copper wire
- Aluminum wire
- PVC insulated wire
- Cross-linked polyethylene (XLPE) insulated wire
- Shielded wire
- Coaxial cable
- Ribbon cable
Connectors and Terminals
Connectors and terminals are used to create electrical connections between wires and other components. They are available in various types, sizes, and configurations, such as:
- Crimp connectors
- Solder connectors
- Insulation displacement connectors (IDC)
- Pin and socket connectors
- Circular connectors
- Rectangular connectors
- Blade terminals
- Ring terminals
Insulation and Protection Materials
Insulation and protection materials are used to protect the wires and cables from damage due to environmental factors, such as heat, moisture, and abrasion. Some common materials include:
- Heat shrink tubing
- Electrical tape
- Braided sleeving
- Conduit
- Grommets and seals
Labels and Identification Markers
Labels and identification markers are used to identify and track the wire harness throughout the manufacturing process and during installation and maintenance. They can be in the form of:
- Adhesive labels
- Heat shrink labels
- Printed markers
- Sleeve markers
- Tie-on tags
Tools and Equipment
Various tools and equipment are used in wire harness manufacturing, including:
- Wire cutters and strippers
- Crimping tools
- Soldering irons
- Heat shrink guns
- Harness boards and jigs
- Testing equipment (e.g., multimeters, continuity testers, and high-voltage insulation testers)
Frequently Asked Questions (FAQ)
- What is a wire harness, and why is it important?
A wire harness is an organized assembly of electrical wires, cables, and connectors that transmits signals or electrical power in a vehicle, aircraft, or other electrical system. It is important because it ensures efficient and reliable transmission of electrical signals and power, while also protecting the wires and cables from damage.
- What are the main steps in wire harness manufacturing?
The main steps in wire harness manufacturing are:
– Design and engineering
– Material preparation
– Wire harness assembly
– Quality control and testing
– Packaging and shipping
- How does automation benefit wire harness manufacturing?
Automation benefits wire harness manufacturing by improving efficiency, reducing costs, and ensuring consistent quality. Automated systems can perform tasks such as wire cutting, stripping, crimping, and testing more quickly and accurately than manual methods, reducing the risk of human error.
- What are some common materials used in wire harness manufacturing?
Common materials used in wire harness manufacturing include:
– Copper and aluminum wires
– PVC and XLPE insulated wires
– Crimp and solder connectors
– Pin and socket connectors
– Heat shrink tubing and electrical tape
– Labels and identification markers
- What types of testing are performed on wire harnesses during the manufacturing process?
During the manufacturing process, wire harnesses undergo several types of testing, including:
– Visual inspection for defects and correct assembly
– Electrical testing for short circuits, open circuits, and other faults
– Functional testing under various operating conditions
– Automated testing using specialized software and hardware
Conclusion
Wire harness manufacturing is a complex and precise process that requires a combination of skilled labor, advanced equipment, and rigorous quality control. By following the step-by-step process outlined in this guide, from design and engineering to packaging and shipping, manufacturers can produce high-quality wire harnesses that meet the demands of various industries and applications.
As technology continues to advance, automation will play an increasingly important role in wire harness manufacturing, helping to improve efficiency, reduce costs, and ensure consistent quality. However, the success of any wire harness manufacturing operation ultimately depends on the expertise and dedication of the people involved, from engineers and technicians to machine operators and quality control inspectors.
By understanding the materials, tools, and processes involved in wire harness manufacturing, as well as the importance of quality control and testing, manufacturers can deliver reliable and high-performance products that meet the needs of their customers and contribute to the advancement of electrical systems across industries.
0 Comments