Introduction to PCB Assembly Optimization
Printed Circuit Board (PCB) assembly is a crucial process in the manufacturing of electronic devices. The correct orientation of components on the PCB is essential for the proper functioning of the device. Incorrect component orientation can lead to various issues, such as short circuits, signal interference, and even complete device failure. Therefore, it is crucial to follow best practices to ensure the correct component orientation during the PCB assembly process.
In this article, we will discuss the best practices for PCB assembly optimization, focusing on ensuring the correct component orientation. We will cover various aspects of the assembly process, including component placement, soldering techniques, and quality control measures.
The Importance of Correct Component Orientation
Impact on Device Functionality
The correct orientation of components on a PCB is critical for the proper functioning of the electronic device. Each component has a specific role in the circuit, and its orientation determines how it interacts with other components. Incorrect orientation can lead to short circuits, signal interference, and other issues that can compromise the device’s performance.
Potential Consequences of Incorrect Orientation
Incorrect component orientation can have severe consequences, depending on the device’s application. In some cases, it may lead to minor malfunctions, such as incorrect readings or intermittent operation. However, in more critical applications, such as medical devices or aerospace systems, incorrect orientation can result in complete device failure, potentially putting lives at risk.
Best Practices for Ensuring Correct Component Orientation
1. Proper Component Placement
1.1 Placement Machines and Techniques
Modern PCB assembly often relies on automated placement machines to position components on the board. These machines use various techniques, such as vision systems and pick-and-place mechanisms, to ensure accurate component placement. It is essential to maintain and calibrate these machines regularly to ensure consistent performance.
1.2 Manual Placement Considerations
In some cases, manual placement of components may be necessary, particularly for smaller production runs or prototype boards. When placing components manually, it is crucial to follow the PCB layout diagram carefully and double-check the orientation of each component before soldering.
2. Soldering Techniques
2.1 Reflow Soldering
Reflow soldering is a common technique used in PCB assembly, particularly for surface-mount components. This process involves applying solder paste to the PCB pads, placing the components, and then heating the board to melt the solder and form a connection. Proper control of the reflow profile, including temperature and duration, is essential for ensuring correct component orientation and preventing defects such as tombstoning or bridging.
2.2 Wave Soldering
Wave soldering is another technique used for through-hole components. In this process, the PCB is passed over a wave of molten solder, which flows through the holes and forms a connection with the component leads. Ensuring the correct orientation of through-hole components is critical in wave soldering, as incorrect orientation can lead to poor solder joints or damage to the components.
3. Quality Control Measures
3.1 Visual Inspection
Visual inspection is a crucial step in ensuring correct component orientation. After the soldering process, the PCB should be carefully inspected for any visible defects, such as misaligned components, solder bridges, or poor solder joints. Automated optical inspection (AOI) systems can be used to streamline this process and detect defects more efficiently.
3.2 Electrical Testing
Electrical testing is another important quality control measure that can help identify issues related to incorrect component orientation. Various techniques, such as in-circuit testing (ICT) and functional testing, can be used to verify the electrical performance of the assembled PCB and detect any anomalies caused by incorrect component placement.
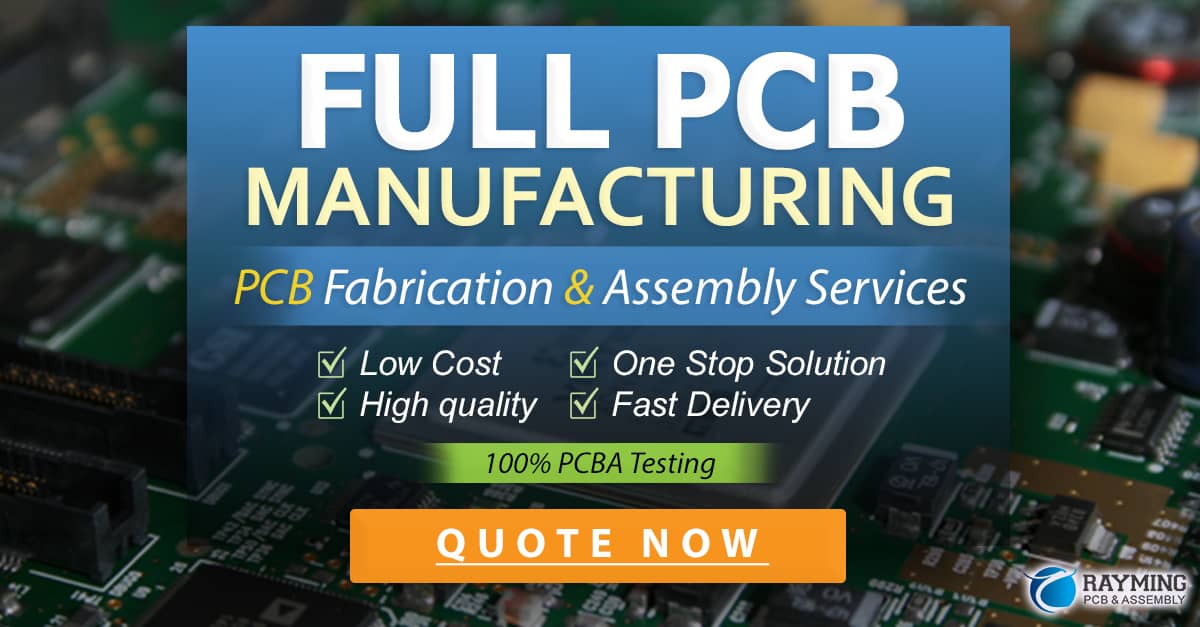
Case Studies
Case Study 1: Medical Device Manufacturer
A medical device manufacturer experienced a high rate of device failures due to incorrect component orientation on their PCBs. By implementing a combination of automated placement machines, reflow soldering with optimized profiles, and stringent visual inspection procedures, they were able to reduce the failure rate by 95% and improve overall device reliability.
Case Study 2: Automotive Electronics Supplier
An automotive electronics supplier faced challenges in ensuring the correct orientation of small, high-density components on their PCBs. By investing in advanced vision systems for their placement machines and implementing a two-stage visual inspection process (pre- and post-soldering), they were able to achieve a defect rate of less than 100 parts per million (ppm) and meet the strict quality requirements of their customers.
Frequently Asked Questions (FAQ)
-
Q: What is the most common cause of incorrect component orientation on PCBs?
A: The most common cause of incorrect component orientation is human error during manual placement. Other factors, such as improper machine calibration or incorrect PCB design, can also contribute to this issue. -
Q: How can I ensure correct component orientation when placing components manually?
A: When placing components manually, always refer to the PCB layout diagram and double-check the orientation of each component before soldering. Use magnification tools, such as a microscope or magnifying lamp, to help identify small components and their orientation markings. -
Q: What are the advantages of using automated placement machines for PCB assembly?
A: Automated placement machines offer several advantages, including higher speed, improved accuracy, and greater consistency compared to manual placement. They can also handle a wider range of component sizes and types, making them suitable for complex PCB designs. -
Q: How can I optimize the reflow soldering process to prevent component orientation issues?
A: To optimize the reflow soldering process, ensure that the solder paste is applied correctly and the components are placed accurately. Use a well-designed reflow profile that considers the specific requirements of the components and PCB materials. Monitor the process closely and make adjustments as needed to prevent defects such as tombstoning or bridging. -
Q: What are the key factors to consider when implementing a quality control plan for PCB assembly?
A: When implementing a quality control plan for PCB assembly, consider factors such as the complexity of the PCB design, the types of components used, and the intended application of the device. Incorporate a combination of visual inspection, automated optical inspection (AOI), and electrical testing to detect defects and ensure the correct functionality of the assembled PCB. Regularly review and update the quality control plan based on feedback from production and field data.
Conclusion
Ensuring the correct component orientation is a critical aspect of PCB assembly optimization. By following best practices in component placement, soldering techniques, and quality control measures, manufacturers can minimize the risk of defects and improve the overall reliability of their electronic devices.
Investing in advanced technologies, such as automated placement machines and AOI systems, can help streamline the assembly process and detect orientation issues more efficiently. However, it is equally important to maintain a well-trained and diligent workforce that understands the importance of correct component orientation and follows established procedures consistently.
As the demand for high-quality, reliable electronic devices continues to grow, implementing best practices for PCB assembly optimization will become increasingly crucial for manufacturers to remain competitive and meet the evolving needs of their customers.
0 Comments