What are solder balls and why do they occur in SMT manufacturing?
Solder balls are small spheres of solder that can form on printed circuit boards (PCBs) during surface mount technology (SMT) manufacturing processes like wave soldering or reflow soldering. They occur when excess solder is present and coalesces into ball shapes instead of properly wetting and forming solder joints between component leads/pads and the PCB.
Solder balling is considered a defect in PCB Assembly because the loose balls can cause short circuits if they come in contact with adjacent pins or conductors. Solder balls also indicate a soldering process that is not well controlled and may have other issues.
Some common causes of solder balling include:
- Excessive solder paste deposit
- Incorrect reflow profile
- Poor wetting of solder to pads/leads
- Contamination on board or component surfaces
- Overly long or hot solder exposure
So what can be done to mitigate solder balling and achieve a more robust SMT process? Here are some key best practices and tips for Avoiding solder balls.
Best practices for preventing solder balls in SMT assembly
1. Control solder paste deposition
Applying the right amount of solder paste is critical. Too much paste will result in excess solder that can ball up. Too little may cause poor wetting and increase ball formation as the limited amount of solder struggles to coalesce into proper joints.
Some tips for optimizing solder paste deposit:
- Use a high quality solder paste suitable for your components and PCB finish
- Ensure proper setup and programming of your solder paste printer
- Regularly clean and maintain screens/stencils to ensure paste release
- Measure and monitor paste deposits to verify volume and consistency
- Consider stepping down stencil aperture sizes for finer pitch components
| Component Pitch | Typical Stencil Thickness |
| — | — |
| > 0.65 mm | 150 – 200 μm |
| 0.5 – 0.65 mm | 125 – 150 μm |
| 0.4 – 0.5 mm | 100 – 125 μm |
| < 0.4 mm | 75 – 100 μm |
Recommended stencil thicknesses based on component lead pitch
2. Optimize the reflow soldering profile
The reflow oven temperature profile must be tailored to your solder paste and PCB to achieve proper melting, wetting, and joint formation without overheating the assembly. Profiles with excessive soak time or peak temperature can degrade paste flux and materials leading to poor wetting, graping, and solder balling.
- Consult paste and component datasheets for recommended profiles
- Use thermocouples and profiling software for oven setup
- Aim for a linear ramp to 30-40°C above paste liquidus temperature
- Minimize time above liquidus to 30-90 seconds
- Avoid cooling faster than 4°C/sec to prevent thermal shock
Example reflow profile graph showing proper temperature gradient
3. Verify solder wetting and board/component conditions
Solder balling often goes hand-in-hand with poor wetting and solderability. Contamination or oxidation on the PCB pads, component leads/terminations, or in the solder paste itself can inhibit proper wetting and contribute to the solder pulling back into balls.
To promote good wetting:
- Verify PCBs and components are clean and free of residues
- Ensure PCB finish is flat and not overly porous
- Check age and storage conditions of boards, components and paste
- Use a nitrogen reflow atmosphere to reduce oxidation
- Consider plasma cleaning or chemical etching to improve surface wetting
- Bake moisture sensitive PCBs/parts before assembly
4. Minimize rework and handling
Manual rework processes after the primary SMT reflow can be a source of new solder ball defects. Touching up solder joints with an iron can add excess solder. Removing components may leave behind solder that then balls up in subsequent reflows. And any additional handling risks contaminating surfaces.
Tips to optimize rework:
- Develop good original processes to minimize rework need
- Use proper tools like vacuum pens to avoid touching PCBs
- Add liquid flux when touching up joints to improve flow
- Completely remove solder from empty pads after removing parts
- Clean PCBs with solvent after any rework and before re-reflow
- Handle PCBs by the edges and use gloves to avoid contamination
5. Implement post-reflow inspection and cleaning
Despite our best efforts, some solder balls may still occasionally occur. Catching them early with post-reflow inspection and removing them promptly can prevent bigger issues down the line. Solder balls tend to “grow” as they tumble around and accumulate more solder in subsequent heating processes.
Post-reflow inspection and cleaning tips:
- Perform 100% visual inspection after SMT reflow
- Use AOI (automatic optical inspection) to aid ball detection
- Remove any solder balls with tweezers while taking ESD precautions
- Consider an automated de-ionized water wash process
- Verify complete removal of solder balls and flux residues
| Inspection Method | Pros | Cons |
| — | — | — |
| Manual Visual | Low cost, flexible | Slow, labor intensive, error prone |
| AOI | Fast, objective, data collection | Higher capital cost, programming required |
| X-ray | Finds hidden defects (voids, BGAs) | Very high cost, slow, safety hazard |
Comparison of common PCB inspection methods
Conclusion
Solder balls are a common yet preventable defect in SMT assembly. By controlling materials and processes – especially solder paste deposition and reflow parameters – we can dramatically reduce the risk of solder balling.
Verifying wetting and taking steps to minimize contamination and handling also contribute to a more robust soldering process. And 100% inspection and prompt removal of any solder balls that do occur prevents them from causing issues later on.
Implementing these SMT best practices can help you consistently build better PCB assemblies with fewer defects and higher reliability.
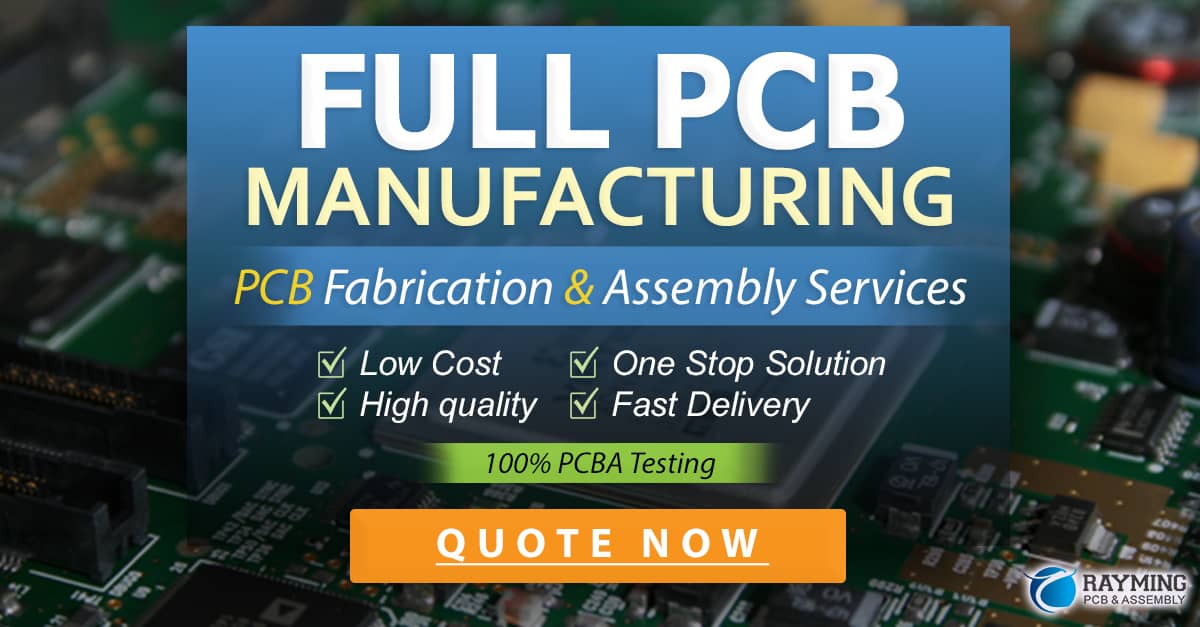
FAQ
What size solder balls should I be worried about?
Any size solder ball can potentially cause issues, but those above 75-100 μm in diameter are generally the threshold for being considered a defect. Smaller solder balls (“solder fines”) are less likely to span the gap between pins and cause a short circuit.
Is there a way to salvage PCBs with excessive solder balls?
If solder balls are widespread it’s often more economical to scrap the affected PCBs than to rework them. For more limited solder ball occurrences, a d.i. water wash followed by careful drying and re-inspection can sometimes be effective at removing them and reclaiming the assemblies.
Can solder balls occur even with lead-free solder paste?
Yes, solder balling can happen with both leaded and lead-free solder pastes. In some ways lead-free solder may be more prone to balling due to its slower wetting speed, higher surface tension, and increased oxidation at higher reflow temperatures. So process controls are even more important with lead-free.
Will a cleaning process always remove solder balls?
Not necessarily. If the solder balls are still adhered to pads or pins then they may not be removed by standard cleaning. Mechanical agitation (brushing) could be required. And if solder balls are trapped under low standoff components then cleaning may not reach them at all.
What’s the best way to find the root cause of solder balling?
Careful monitoring and data collection is key. Document solder paste print and reflow parameters, take cross-sections of solder balls to examine morphology, analyze paste and PCB/component surfaces for contamination. Conduct designed experiments varying materials and parameters to isolate likely factors.
0 Comments