Introduction to PCBs
Printed Circuit Boards (PCBs) are the backbone of modern electronics. They are used in almost every electronic device, from simple gadgets like calculators and digital clocks to complex systems such as computers, smartphones, and industrial equipment. PCBs provide a reliable and efficient way to connect electronic components and create complete circuits.
In this article, we will focus on bare board PCBs, which are the foundation of any PCB Assembly. We will explore the manufacturing process, materials, design considerations, and various applications of bare board PCBs.
What are Bare Board PCBs?
A bare board PCB, also known as a printed wiring board (PWB), is a PCB without any electronic components mounted on it. It consists of a non-conductive substrate, typically made of fiberglass or other composite materials, with conductive copper traces printed on one or both sides. These copper traces form the electrical connections between the components that will be soldered onto the board later in the assembly process.
Bare board PCBs come in different types, depending on the number of layers and the specific manufacturing process used. Some common types include:
- Single-sided PCBs: These have copper traces on only one side of the substrate.
- Double-sided PCBs: These have copper traces on both sides of the substrate, with through-holes connecting the two sides.
- Multi-layer PCBs: These have multiple layers of copper traces separated by insulating layers, allowing for more complex routing and higher component density.
Advantages of using bare board PCBs
Bare board PCBs offer several advantages over other wiring methods, such as point-to-point wiring or wire-wrap:
- Consistency: PCBs ensure consistent electrical connections, as the copper traces are precisely printed on the substrate.
- Reliability: Properly designed and manufactured PCBs are highly reliable, with a low risk of short circuits or open connections.
- Compact size: PCBs allow for high component density, enabling the creation of compact electronic devices.
- Cost-effective: Mass production of PCBs is cost-effective, especially for large-scale manufacturing.
- Ease of assembly: Components can be easily soldered onto the bare board PCB, streamlining the assembly process.
PCB Manufacturing Process
The manufacturing process for bare board PCBs involves several steps, each critical to ensuring the quality and reliability of the final product.
Step 1: PCB Design
The first step in the manufacturing process is the design of the PCB. This involves creating a schematic diagram that shows the electrical connections between the components, as well as a layout that determines the physical placement of the components and the routing of the copper traces.
PCB design software, such as Altium Designer, Eagle, or KiCad, is used to create the schematic and layout files. The designer must consider factors such as signal integrity, power distribution, thermal management, and manufacturability when creating the design.
Step 2: PCB Fabrication
Once the design is finalized, the PCB fabrication process begins. This involves several sub-steps:
- Substrate preparation: The substrate material, typically a fiberglass composite like FR-4, is cut to the desired size and shape.
- Copper lamination: Thin sheets of copper are laminated onto the substrate using heat and pressure.
- Drilling: Holes are drilled through the substrate to accommodate through-hole components and vias, which connect different layers of the board.
- Patterning: The copper layers are patterned using a photolithography process. This involves applying a light-sensitive photoresist to the copper, exposing it to UV light through a mask that defines the desired trace pattern, and then etching away the unwanted copper.
- Plating: The holes and vias are plated with copper to ensure electrical continuity between layers.
- Solder mask application: A solder mask, typically green in color, is applied to the board to protect the copper traces and prevent solder bridges during the assembly process.
- Silkscreen printing: Text, logos, and component outlines are printed onto the board using a silkscreen process.
Step 3: Quality Control
After the fabrication process, the bare board PCBs undergo a series of quality control checks to ensure they meet the required specifications. These checks may include:
- Visual inspection: The boards are visually inspected for defects such as scratches, dents, or contamination.
- Electrical testing: The boards are tested for continuity, shorts, and opens using specialized equipment like flying probe testers or bed-of-nails fixtures.
- Dimensional verification: The board dimensions, hole sizes, and trace widths are measured to ensure they are within the specified tolerances.
Boards that pass the quality control checks are packaged and shipped to the customer for the final assembly process.
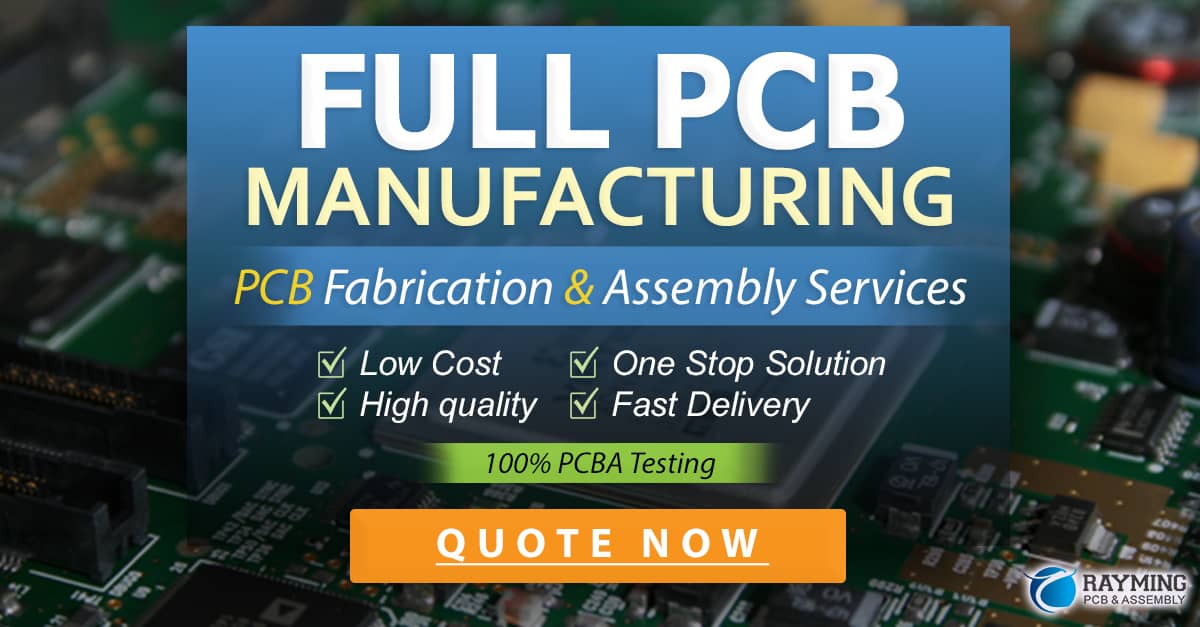
PCB Materials
The choice of materials used in the construction of bare board PCBs is crucial, as it affects the performance, reliability, and cost of the final product.
Substrate Materials
The most common substrate material used in PCBs is FR-4, a composite made of woven fiberglass cloth impregnated with an epoxy resin. FR-4 offers a good balance of mechanical strength, electrical insulation, and thermal stability.
Other substrate materials include:
- High-Tg FR-4: A variant of FR-4 with a higher glass transition temperature, offering better thermal stability and improved performance in high-temperature applications.
- Polyimide: A high-performance polymer that offers excellent thermal stability, chemical resistance, and flexibility. Often used in flex and rigid-flex PCBs.
- Ceramic: Used in high-frequency and high-power applications, ceramic substrates offer excellent thermal conductivity and low dielectric loss.
Copper Foils
The copper foils used in PCBs come in different thicknesses, typically measured in ounces per square foot (oz/ft²). Some common thicknesses include:
- 1/2 oz/ft²: Used in low-power and high-density designs.
- 1 oz/ft²: The most common thickness, suitable for a wide range of applications.
- 2 oz/ft²: Used in high-current and power electronics applications.
The copper foils are typically electrodeposited (ED) or rolled annealed (RA). ED copper offers better adhesion to the substrate, while RA copper provides better thermal and electrical conductivity.
Solder Masks
Solder masks are polymer coatings applied to the PCB to protect the copper traces from oxidation and prevent solder bridges during the assembly process. The most common solder mask color is green, but other colors like red, blue, and black are also available.
Solder masks can be liquid photoimageable (LPI) or dry film. LPI solder masks are applied as a liquid and then cured using UV light, while dry film solder masks are applied as a solid film and then laminated onto the board.
PCB Design Considerations
Designing a bare board PCB involves several considerations to ensure optimal performance, reliability, and manufacturability.
Signal Integrity
Signal integrity refers to the quality of the electrical signals transmitted through the PCB. To maintain good signal integrity, designers must consider factors such as:
- Trace width and spacing: Proper trace width and spacing help minimize crosstalk and maintain characteristic impedance.
- Trace routing: Careful routing of traces, especially for high-speed signals, can minimize reflections and signal distortion.
- Ground and power planes: Solid ground and power planes help provide a low-impedance return path for signals and minimize noise.
Power Distribution
Proper power distribution is essential to ensure that all components receive a stable and noise-free power supply. Designers must consider:
- Power plane layout: The layout of the power planes should minimize voltage drops and ensure even distribution of current.
- Decoupling capacitors: Placing decoupling capacitors close to power pins helps filter out high-frequency noise and maintain signal integrity.
- Voltage regulators: Choosing appropriate voltage regulators and placing them close to the components they supply helps ensure stable power delivery.
Thermal Management
Thermal management is crucial to ensure that components operate within their specified temperature ranges and to prevent premature failure. Designers must consider:
- Component placement: Placing high-power components away from temperature-sensitive components helps minimize thermal interactions.
- Copper pours: Using large copper pours, especially on the outer layers, helps dissipate heat from components.
- Thermal vias: Placing thermal vias under high-power components helps transfer heat to the inner layers and the opposite side of the board.
Manufacturability
Designing for manufacturability (DFM) involves adhering to guidelines that ensure the PCB can be reliably and cost-effectively manufactured. Some key DFM considerations include:
- Minimum trace width and spacing: Adhering to the manufacturer’s minimum trace width and spacing guidelines helps ensure reliable fabrication.
- Drill sizes and pad diameters: Using standard drill sizes and appropriate pad diameters helps minimize manufacturing costs and improve reliability.
- Solder mask and silkscreen clearances: Maintaining adequate clearances between solder mask openings, silkscreen text, and copper features helps ensure proper solder mask adhesion and legible silkscreen printing.
Applications of Bare Board PCBs
Bare board PCBs find applications in a wide range of industries and products. Some common applications include:
Consumer Electronics
Bare board PCBs are used in a variety of consumer electronic products, such as:
- Smartphones and tablets
- Laptops and desktop computers
- Televisions and home entertainment systems
- Gaming consoles and peripherals
- Wearable devices like smartwatches and fitness trackers
Automotive Electronics
PCBs play a crucial role in modern automotive electronics, with applications such as:
- Engine control units (ECUs)
- Infotainment systems
- Advanced driver assistance systems (ADAS)
- Instrument clusters and dashboard displays
- Lighting and climate control systems
Industrial Electronics
Industrial applications of bare board PCBs include:
- Process control systems
- Automation and robotics
- Power electronics and motor drives
- Instrumentation and measurement equipment
- Telecommunications infrastructure
Medical Electronics
PCBs are used in a range of medical electronic devices, such as:
- Diagnostic imaging equipment (X-ray, MRI, CT scanners)
- Patient monitoring systems
- Implantable devices like pacemakers and defibrillators
- Surgical instruments and robotic systems
Aerospace and Defense Electronics
Bare board PCBs are used in various aerospace and defense applications, including:
- Avionics systems
- Satellite communications
- Radar and sonar systems
- Missile guidance and control systems
- Military-grade computing and networking equipment
Future Trends in Bare Board PCBs
As electronic devices continue to evolve, bare board PCBs must adapt to meet new challenges and requirements. Some future trends in PCB technology include:
High-Speed and High-Frequency PCBs
With the increasing demand for faster data transmission and processing, PCBs designed for high-speed and high-frequency applications are becoming more common. These PCBs require advanced materials, such as low-loss substrates and high-performance laminates, as well as specialized design techniques to maintain signal integrity.
Flexible and Rigid-Flex PCBs
Flexible and rigid-flex PCBs are gaining popularity, especially in wearable devices, automotive electronics, and aerospace applications. These PCBs offer the advantage of conforming to unique form factors and withstanding repeated flexing and bending.
Embedded Components
Embedding components like capacitors, resistors, and even active components within the PCB substrate can help reduce board size, improve performance, and simplify assembly. As embedding technologies mature, more PCB designers are likely to adopt this approach.
3D Printed Electronics
Additive manufacturing, or 3D printing, is emerging as a potential method for fabricating PCBs. While still in the early stages of development, 3D-printed electronics could offer benefits such as rapid prototyping, customization, and the ability to create complex, three-dimensional structures.
Frequently Asked Questions (FAQ)
-
What is the difference between a bare board PCB and an assembled PCB?
A bare board PCB is a printed circuit board without any components mounted on it, while an assembled PCB has all the necessary components soldered onto the board and is ready for use in an electronic device. -
Can bare board PCBs be recycled?
Yes, bare board PCBs can be recycled. The recycling process typically involves separating the metal components (copper, gold, and other precious metals) from the non-metallic substrate material. Recycling PCBs helps reduce electronic waste and conserve valuable resources. -
What is the typical turnaround time for manufacturing bare board PCBs?
The turnaround time for manufacturing bare board PCBs depends on various factors, such as the complexity of the design, the number of layers, and the chosen manufacturing service. Typical turnaround times can range from a few days for simple, quick-turn prototypes to several weeks for complex, high-volume production runs. -
How do I choose the right PCB manufacturer for my project?
When choosing a PCB manufacturer, consider factors such as their experience, capabilities, quality control processes, and customer support. Look for manufacturers with a proven track record in your specific industry or application, and those who can meet your technical requirements, such as minimum feature sizes, layer counts, and material choices. Requesting quotes from multiple manufacturers and evaluating their responses can help you make an informed decision. -
What is the difference between a solder mask and a silkscreen on a PCB?
A solder mask is a polymer coating applied to the copper traces on a PCB to protect them from oxidation and prevent solder bridges during the assembly process. It also provides electrical insulation between adjacent traces. A silkscreen, on the other hand, is a printed layer on top of the solder mask that contains text, logos, and component outlines to aid in the assembly process and provide visual identification of components and features on the board.
Conclusion
Bare board PCBs are the foundation of modern electronics, providing a reliable and efficient means of connecting components and creating complete circuits. The manufacturing process for bare board PCBs involves several critical steps, from design and fabrication to quality control, each of which contributes to the overall performance and reliability of the final product.
When designing bare board PCBs, considerations such as signal integrity, power distribution, thermal management, and manufacturability are crucial to ensure optimal performance and cost-effectiveness. The choice of materials, including substrate, copper foils, and solder masks, also plays a significant role in the PCB’s performance and reliability.
Bare board PCBs find applications in a wide range of industries, from consumer electronics and automotive to industrial, medical, and aerospace. As electronic devices continue to evolve, PCB technology must adapt to meet new challenges and requirements, with trends such as high-speed and high-frequency designs, flexible and rigid-flex PCBs, embedded components, and 3D-printed electronics shaping the future of the industry.
By understanding the fundamentals of bare board PCBs, designers and engineers can create reliable, high-performance electronic devices that drive innovation and progress across various sectors.
0 Comments