What is PCB Back Drilling?
PCB back drilling, also known as controlled depth drilling or back-side drilling, is a PCB manufacturing process that removes the unused portion of a plated through-hole (PTH) on a printed circuit board. It is commonly used in high-speed PCB designs to reduce the stub length of vias, which can cause signal integrity issues at high frequencies.
In a typical PCB manufacturing process, vias are drilled through the entire thickness of the board, even if they are only needed to connect a few layers. This results in a stub, which is the unused portion of the via that extends beyond the last connected layer. At high frequencies, these stubs can act as tiny antennas, causing signal reflections and degrading the quality of the signal.
Back drilling solves this problem by removing the unused portion of the via, leaving only the necessary length required to connect the desired layers. This process is performed using a specialized drill bit that is precisely controlled to drill only to a specific depth, removing the stub without damaging the connected layers.
Benefits of PCB Back Drilling
Back drilling offers several benefits for high-speed PCB designs:
-
Improved Signal Integrity: By removing the unused portion of the via, back drilling reduces the stub length, which minimizes signal reflections and improves the overall signal integrity of the PCB.
-
Reduced EMI: Shorter stubs also reduce electromagnetic interference (EMI) caused by the via stubs acting as tiny antennas.
-
Better Impedance Control: Back drilling allows for better control over the impedance of the vias, which is crucial for maintaining signal integrity in high-speed designs.
-
Increased Bandwidth: With improved signal integrity and reduced EMI, back drilling enables PCBs to operate at higher frequencies and support greater bandwidths.
When to Use PCB Back Drilling
Back drilling is typically used in high-speed PCB designs where signal integrity is critical. Some common applications include:
- High-speed digital interfaces (e.g., PCIe, USB, SATA)
- RF and microwave circuits
- Automotive and aerospace electronics
- Medical devices
- Telecommunications equipment
As a general rule, back drilling should be considered when the operating frequency of the PCB exceeds 5 GHz or when the rise time of the signal is less than 100 ps. However, the decision to use back drilling should be based on a thorough analysis of the PCB design and its specific requirements.
How to Implement PCB Back Drilling
Implementing PCB back drilling involves several steps:
1. PCB Design
During the PCB design phase, the designer must identify the vias that require back drilling and specify the desired stub length for each via. This information is typically conveyed to the PCB manufacturer using a drill file or a back drill table.
The designer should also consider the following factors when designing a PCB for back drilling:
- Via size and placement
- Layer stack-up
- Dielectric materials
- Impedance requirements
2. PCB Fabrication
Once the PCB design is complete, the fabrication process begins. The PCB manufacturer will first drill the vias through the entire thickness of the board using a standard drilling process.
After the initial drilling, the back drilling process is performed using a specialized drill bit that is precisely controlled to drill only to the specified depth for each via. The depth of the back drill is typically set to remove the stub to within 10-20 mils (0.254-0.508 mm) of the last connected layer.
The back drilling process requires careful control and monitoring to ensure that the drill bit does not damage the connected layers or exceed the specified depth. Some PCB Manufacturers use advanced techniques, such as laser depth control or x-ray inspection, to ensure the accuracy and consistency of the back drilling process.
3. PCB Assembly and Testing
After the back drilling process is complete, the PCB undergoes the standard assembly and testing procedures. It is important to verify that the back drilling process has not compromised the integrity of the vias or the overall functionality of the PCB.
Some common testing methods for back-drilLED PCBs include:
- Time-domain reflectometry (TDR)
- Impedance testing
- High-speed signal integrity testing
- X-ray inspection
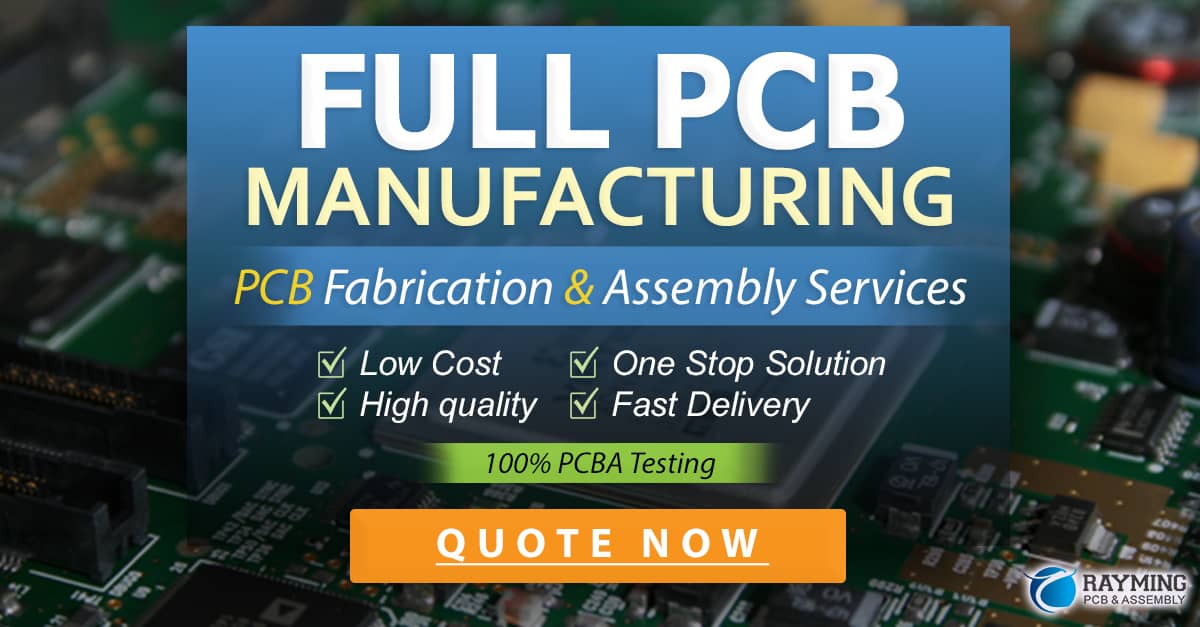
Challenges and Limitations of PCB Back Drilling
While back drilling offers significant benefits for high-speed PCB designs, it also presents some challenges and limitations:
1. Increased Cost
Back drilling adds an additional step to the PCB manufacturing process, which increases the overall cost of the PCB. The cost increase is typically proportional to the number of vias that require back drilling and the complexity of the drilling process.
2. Limited Via Size
Back drilling is most effective for larger via sizes (typically >0.2 mm) due to the limitations of the drilling equipment. Smaller vias may not be suitable for back drilling, as the drill bit size and depth control become more challenging.
3. Potential for Damage
If not properly controlled, the back drilling process can potentially damage the connected layers of the PCB. This can lead to reliability issues and reduced yields. Careful process control and monitoring are essential to minimize the risk of damage.
4. Design Complexity
Designing a PCB for back drilling requires careful consideration of via placement, layer stack-up, and impedance requirements. This can increase the complexity of the PCB design process and may require additional expertise and resources.
Alternatives to PCB Back Drilling
While back drilling is a common technique for reducing via stub length, there are some alternatives that can be considered depending on the specific requirements of the PCB design:
1. Blind and Buried Vias
Blind and buried vias are another method for reducing stub length in high-speed PCB designs. Blind vias are drilled from one surface of the board to a specific inner layer, while buried vias are drilled between inner layers without extending to either surface.
Blind and buried vias can be used to create shorter, more direct connections between layers, reducing the overall via length and minimizing stubs. However, they also add complexity and cost to the PCB manufacturing process.
2. Via-in-Pad (VIP)
Via-in-pad is a technique where vias are placed directly in the surface mount pads of components. This allows for shorter, more direct connections between the component and the inner layers of the PCB.
VIP can be used in conjunction with back drilling to further reduce stub lengths. However, it requires careful design considerations and may not be suitable for all components or PCB layouts.
3. High-Density Interconnect (HDI)
High-density interconnect (HDI) is a PCB manufacturing technology that uses microvias and sequential lamination to create high-density, high-performance PCBs.
HDI can be used to create shorter, more direct connections between layers, reducing the need for back drilling. However, HDI also adds significant complexity and cost to the PCB manufacturing process.
Frequently Asked Questions (FAQ)
1. What is the difference between back drilling and controlled depth drilling?
Back drilling and controlled depth drilling are two terms that refer to the same process of removing the unused portion of a plated through-hole (PTH) on a PCB. The terms are often used interchangeably.
2. How much does back drilling increase the cost of a PCB?
The cost increase associated with back drilling varies depending on the number of vias that require drilling and the complexity of the drilling process. As a general rule, back drilling can increase the cost of a PCB by 10-20% compared to a standard PCB without back drilling.
3. Can back drilling be used on all types of PCBs?
Back drilling is most commonly used on high-speed Digital PCBs where signal integrity is critical. It may not be necessary or cost-effective for lower-speed or less complex PCB designs.
4. What is the minimum via size that can be back drilled?
The minimum via size that can be effectively back drilled is typically around 0.2 mm (8 mils). Smaller vias may not be suitable for back drilling due to the limitations of the drilling equipment and the potential for damage to the connected layers.
5. How does back drilling compare to other via stub reduction techniques?
Back drilling is one of the most common and effective techniques for reducing via stub lengths in high-speed PCB designs. It offers a balance of performance, cost, and manufacturability compared to other techniques such as blind/buried vias or HDI. However, the choice of via stub reduction technique depends on the specific requirements and constraints of each PCB design.
Conclusion
PCB back drilling is a valuable technique for improving signal integrity and reducing EMI in high-speed PCB designs. By removing the unused portion of plated through-holes, back drilling minimizes via stub lengths and enables PCBs to operate at higher frequencies with greater bandwidth.
However, back drilling also presents some challenges and limitations, including increased cost, limited via size, and potential for damage. PCB designers must carefully consider these factors and weigh the benefits of back drilling against other via stub reduction techniques.
As PCB speeds continue to increase and signal integrity becomes ever more critical, back drilling is likely to remain an important tool in the PCB designer’s toolkit. By understanding the principles, benefits, and limitations of this technique, designers can make informed decisions and create high-performance PCBs that meet the demands of today’s advanced electronic systems.
0 Comments