What is Polyimide?
Polyimide (PI) is a high-performance polymer known for its excellent thermal stability, mechanical strength, and dielectric properties. It maintains its integrity at temperatures up to 400°C, far exceeding the 130°C glass transition temperature of FR-4. Polyimide also offers:
- High tensile strength and dimensional stability
- Low dielectric constant and dissipation factor
- Resistance to chemicals, radiation, and moisture
- UL 94 V-0 flammability rating
These properties make polyimide a go-to material for printed circuit boards that will be exposed to harsh operating conditions. PI PCBs are commonly used in:
- Aerospace and military electronics
- Downhole drilling and oil/gas exploration
- Automotive under-the-hood applications
- Power electronics and renewable energy
- Medical devices and implantable electronics
- Industrial controls and sensors
Polyimide PCB Construction
Polyimide PCBs are available in several different constructions to meet the needs of specific applications. The most common types are:
Rigid Polyimide PCBs
Rigid polyimide PCBs have a solid polyimide core that provides a stable platform for mounting components. They typically range from 0.2mm to 3mm in thickness. Rigid PI boards offer the highest mechanical strength and thermal conductivity, making them suited for applications with high component density or significant vibration/shock requirements.
Flexible Polyimide PCBs
Flex PI circuits use thin polyimide films, typically 25um to 75um thick, as the base material. The copper traces are bonded directly to the polyimide, allowing the PCB to bend and flex. Flexible polyimide provides excellent mechanical durability, resisting tears and creases that could cause circuit failure. Flex PCBs help save space and weight in compact electronics packaging.
Rigid-Flex Polyimide PCBs
Rigid-flex polyimide PCBs combine flexible polyimide layers with rigid FR-4 or polyimide sections. The rigid areas mount components while the flex regions act as interconnects between rigid sections. Rigid-flex construction provides the best of both board types, enabling 3D circuit configurations for the most demanding aerospace and military electronics.
Advantages of Polyimide PCBs
Polyimide printed circuit boards offer several key benefits over traditional FR-4 materials:
-
High Temperature Resistance
Polyimide maintains its electrical and mechanical properties at extreme temperatures, both high and low. PI withstands lead-free solder reflow temperatures up to 290°C and maintains functionality down to -269°C. This allows reliable operation in harsh environments without risk of delamination or damage. -
Dimensional Stability
Polyimide has a low coefficient of thermal expansion (CTE), typically 12-16 ppm/°C. This closely matches the CTE of copper at 17 ppm/°C. The similar expansion rates prevent warping or twisting of the PCB during thermal cycling, which is critical for aerospace, automotive, and industrial applications. PI also resists moisture absorption, further enhancing stability. -
High Strength-to-Weight Ratio
Polyimide films have a high tensile strength of 150-300 MPa while being incredibly lightweight. Polyimide has a density of 1.42 g/cm3, about half that of FR-4 at 2.7 g/cm3. This allows very thin, lightweight circuit boards that still provide excellent mechanical durability. Flex polyimide can withstand millions of bend cycles without breaking. -
Dielectric Performance
Polyimide has a stable dielectric constant (Dk) of 3.4 and a low dissipation factor (Df) of 0.002 at 1 MHz. These values are consistent across a wide temperature range and up to high frequencies in the GHz range. The low losses make polyimide suitable for high-speed digital and RF/microwave circuits. -
Chemical and Radiation Resistance
Polyimide resists attack from most chemicals, including oils, fuels, acids, and bases. It also withstands exposure to radiation and UV light without degrading. This allows PI PCBs to operate reliably in industrial, automotive, and aerospace environments where contaminants may be present.
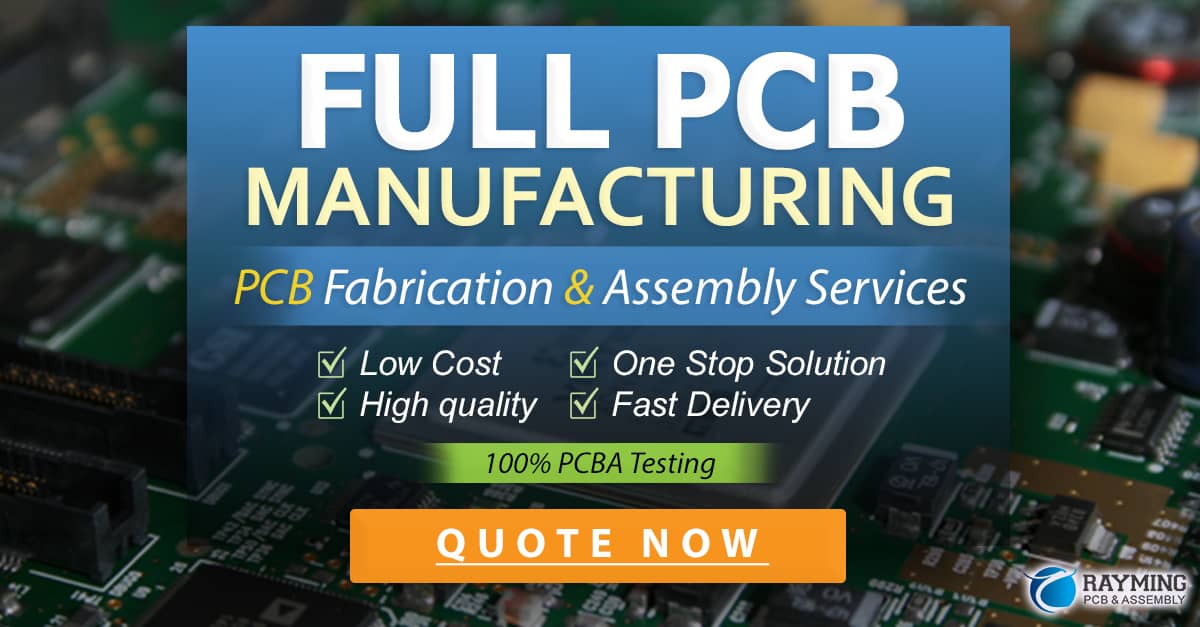
Choosing a Polyimide PCB Manufacturer
Fabricating polyimide PCBs requires specialized equipment and processes compared to standard FR-4 boards. Polyimide has different bonding requirements, and the thin substrates can be challenging to handle. Some key factors to consider when selecting a polyimide PCB manufacturer include:
Experience with Polyimide
Look for a manufacturer with extensive experience processing polyimide materials. They should be familiar with the nuances of imaging, etching, and laminating PI substrates. Verify that they have successfully produced polyimide PCBs for applications similar to yours.
Equipment and Capabilities
Polyimide PCB fabrication requires advanced registration systems to accurately align the thin layers. Laser direct imaging is often used to avoid distorting the substrates during imaging. The facility should also have clean room conditions to prevent contamination of the materials.
Inquire about the manufacturer’s in-house capabilities for crucial processes like:
– Laser drilling of microvias
– Plasma etching for fine-pitch traces
– Solder mask application
– Electrical test and inspection
Lamination Expertise
The key challenge in polyimide PCB construction is properly laminating the layers to prevent delamination and ensure reliable interconnects. The manufacturer should have advanced lamination presses with precise temperature and pressure control. They may use vacuum lamination or autoclave processes for the most demanding high-reliability applications.
IPC Class 3 Certification
For aerospace, defense, and medical applications, choose a manufacturer certified to IPC Class 3 standards. This ensures they follow stringent quality control processes and can meet the tightest tolerances. IPC Class 3 manufacturers are audited regularly to maintain their certification.
Testing and Quality Control
Polyimide PCBs often end up in mission-critical systems where failure is not an option. Partner with a manufacturer that performs thorough electrical testing, visual inspection, and quality control checks on every board. They should use automated optical inspection (AOI) and X-ray inspection to detect any defects.
Also inquire about their capabilities for additional testing and reliability screening, such as:
– Thermal cycling and burn-in
– Highly accelerated stress screening (HASS)
– Microsectioning analysis
– Solderability testing
– Cleanliness testing (ROSE)
Technical Support and Design Assistance
Designing circuits on polyimide substrates often requires special considerations to account for the material properties. Look for a manufacturer who can provide technical support and design review services to ensure your PCB layout is optimized for polyimide fabrication. They should offer suggestions to enhance manufacturability, reliability, and cost-effectiveness.
Polyimide PCB Design Considerations
To get the best performance and reliability from polyimide PCBs, keep these design guidelines in mind:
-
Use a Symmetrical Stackup
Polyimide substrates are thinner than FR-4 and can be more susceptible to warping from asymmetrical layer stackups. Use a balanced construction with an even number of layers and symmetrical copper distribution to prevent twisting. -
Allow for Flex Film Shrinkage
Polyimide films can shrink slightly during lamination, typically 0.05% to 0.10%. Compensate for this in your design by oversizing the panel and using shrinkage-matching copper foils. Consult with your manufacturer on the exact shrinkage values to use. -
Follow Copper Trace Width and Spacing Guidelines
Polyimide allows finer trace geometries than FR-4, but there are still limits. Typical minimums are 0.003″ (75um) traces and spaces, although 0.002″ (50um) is possible with special processing. Use neck-downs and teardrop pads to enhance the reliability of narrow traces. -
Select High-Temperature Laminates and Solder Masks
Make sure your base material and solder mask are rated for the expected operating temperatures. Standard polyimide laminates are rated for 260°C reflow, but high-temperature versions are available for 290°C lead-free assembly. Solder masks should be compatible with your specific laminate material. -
Use Filled Vias and Microvias
Plated through-holes can be a point of weakness in thin polyimide layers. Use filled vias and microvias to enhance reliability, especially in aerospace and defense applications. Filling vias with a solid plug of copper or epoxy improves thermal transfer and eliminates the risk of barrel cracking. -
Specify Controlled Impedance
Polyimide’s stable Dk allows accurate impedance control for high-speed designs. Your manufacturer can adjust the trace width and spacing to hit your target impedance. Be sure to specify the required impedance on your fabrication drawing.
Polyimide PCB Supplier Evaluation
When evaluating potential providers for your polyimide PCB needs, collect detailed information in the following key areas:
Area | Information to Gather |
---|---|
Facilities | Location, size, certifications (ISO, ITAR, UL), manufacturing capacity |
Capabilities | Materials, layer counts, trace/space minimums, via types, lamination methods |
Quality | Testing equipment, inspection procedures, defect rates, quality accreditations |
Engineering | CAD/CAM tools, impedance modeling, signal integrity, DFM support |
Program Management | Account management, communication protocols, schedule tracking, ECO process |
Supply Chain | Component sourcing, value-add services, warehousing, Kanban programs |
Logistics | Packaging, shipping, freight carriers, import/export capabilities |
Evaluate each supplier across these categories to gauge their ability to meet your technical, quality, and business needs. Visit the facility in person, if possible, to audit their processes and meet the team.
Polyimide PCB Cost Drivers
The cost of polyimide PCBs depends on several key factors:
-
Material Selection
Polyimide films are available in various thicknesses and grades, each with different costs. Thinner materials tend to be more expensive. Specialized laminates like low-flow prepregs or adhesiveless materials also increase cost. -
Layer Count and Density
As with any PCB, higher layer counts and denser designs are more costly due to increased processing steps. Polyimide PCBs are often used for high-density interconnect (HDI) designs, which can significantly impact price. -
Board Size and Quantity
Larger boards are more expensive due to material usage. However, you may get a discount for higher volumes. Work with your manufacturer to find the most economical panel utilization. -
Specialty Processes
Advanced features like high aspect ratio vias, filled vias, thin laminates, and fine-pitch BGAs all require additional processing steps that add cost. Consult with your manufacturer early in the design process to find the most cost-effective solution. -
Testing and Reliability Screening
Extensive testing and burn-in can significantly increase the cost of polyimide PCBs for high-reliability applications. Discuss your testing requirements upfront so your manufacturer can provide an accurate quote.
In general, polyimide PCBs are more expensive than standard FR-4 due to the advanced materials and specialized processing required. However, the improved reliability and performance can justify the added cost for demanding applications. Work closely with your manufacturer to balance your technical requirements and budget constraints.
FAQ
What is the minimum thickness for polyimide PCBs?
Polyimide PCBs can be made extremely thin using polyimide films as the base material. Typical minimum thicknesses are:
- Rigid polyimide: 0.2mm (0.008″)
- Flex polyimide: 0.051mm (0.002″)
- Coverlay: 0.025mm (0.001″)
These thin substrates enable compact, lightweight packaging for portable and wearable electronics.
Can polyimide PCBs be used for high voltage applications?
Yes, polyimide has excellent dielectric strength, typically 300 V/mil or higher. By using thicker polyimide laminates and increasing the spacing between conductors, polyimide PCBs can be designed to withstand high voltages in power electronics applications.
Are polyimide PCBs suitable for RF and microwave frequencies?
Polyimide’s stable Dk and low Df make it well-suited for high-frequency RF and microwave circuits. Many radar and telecommunications systems use polyimide PCBs. However, for the most demanding low-loss applications, PTFE laminates like Rogers materials may be preferred.
How do polyimide and polyamide PCBs differ?
Polyimide (PI) and polyamide (PA) are two different high-performance polymers used in PCB substrates. Polyimide offers better thermal stability and mechanical strength, while polyamide has a lower dielectric constant and dissipation factor. Polyamide is often used in combination with other materials to make laminates like Rogers RO4000-series. Polyimide is more commonly used on its own as a substrate.
What certifications are important for polyimide PCB Manufacturers?
Some key certifications to look for in a polyimide PCB manufacturer include:
- ISO 9001 quality management system
- IPC Class 2 or 3 for high-reliability manufacturing
- ITAR registration for defense applications
- AS9100 for aerospace quality control
- ISO 13485 for medical device manufacturing
- UL listing for safety-critical applications
These certifications ensure the manufacturer has the processes and controls in place to consistently produce reliable polyimide PCBs.
0 Comments