What is an Automotive PCB?
An automotive PCB (Printed Circuit Board) is a specialized type of circuit board designed to meet the unique requirements of the automotive industry. These PCBs are used in various electronic systems within a vehicle, such as engine control units (ECUs), infotainment systems, and advanced driver assistance systems (ADAS). Automotive PCBs are designed to withstand harsh environmental conditions, including extreme temperatures, vibrations, and exposure to chemicals.
Key Features of Automotive PCBs
- High reliability
- Robust design
- Resistance to extreme temperatures
- Vibration and shock resistance
- Compliance with automotive standards (e.g., ISO 26262, AEC-Q100)
Automotive PCB Applications
Automotive PCBs are used in a wide range of applications within the automotive industry. Some of the most common applications include:
Engine Control Units (ECUs)
ECUs are responsible for managing various aspects of a vehicle’s engine, such as fuel injection, ignition timing, and emission control. Automotive PCBs used in ECUs must be able to withstand high temperatures and vibrations while providing reliable performance.
Infotainment Systems
Modern vehicles feature sophisticated infotainment systems that provide audio, video, and navigation functions. Automotive PCBs used in these systems must be capable of handling high-speed data transfer and processing while maintaining signal integrity.
Advanced Driver Assistance Systems (ADAS)
ADAS technologies, such as lane departure warning, adaptive cruise control, and automatic emergency braking, rely on automotive PCBs to process sensor data and make real-time decisions. These PCBs must be highly reliable and capable of rapid data processing.
Other Applications
- Lighting systems
- Power management systems
- Body control modules
- Transmission control modules
Automotive PCB Design Considerations
Designing an automotive PCB requires careful consideration of various factors to ensure reliable performance and compliance with industry standards.
Material Selection
Automotive PCBs must be constructed using materials that can withstand harsh environmental conditions. Common materials used in automotive PCBs include:
Material | Properties |
---|---|
FR-4 | High glass transition temperature, good mechanical strength |
Polyimide | High temperature resistance, excellent mechanical properties |
Ceramic | Excellent thermal conductivity, high temperature resistance |
Layer Stack-up
The layer stack-up of an automotive PCB plays a crucial role in its performance and reliability. A typical 4-layer automotive PCB Stack-up might include:
Layer | Description |
---|---|
Top Layer | Signal layer, components |
Ground Layer | Provides shielding and reduces EMI |
Power Layer | Distributes power to components |
Bottom Layer | Signal layer, components |
Thermal Management
Automotive PCBs must be designed to dissipate heat effectively to prevent component failure and ensure reliable performance. Techniques for improving thermal management include:
- Using thermal vias to transfer heat from components to the PCB’s outer layers
- Incorporating heatsinks or other cooling solutions
- Selecting components with appropriate power ratings and temperature specifications
Signal Integrity
Maintaining signal integrity is critical in automotive PCBs, particularly those used in high-speed applications. Techniques for improving signal integrity include:
- Proper impedance matching
- Use of differential signaling
- Minimizing crosstalk and electromagnetic interference (EMI)
Component Selection
Components used in automotive PCBs must be selected based on their ability to withstand harsh environmental conditions and meet automotive industry standards. Key considerations include:
- Temperature ratings
- Vibration and shock resistance
- Reliability and lifetime expectancy
- AEC-Q100 qualification
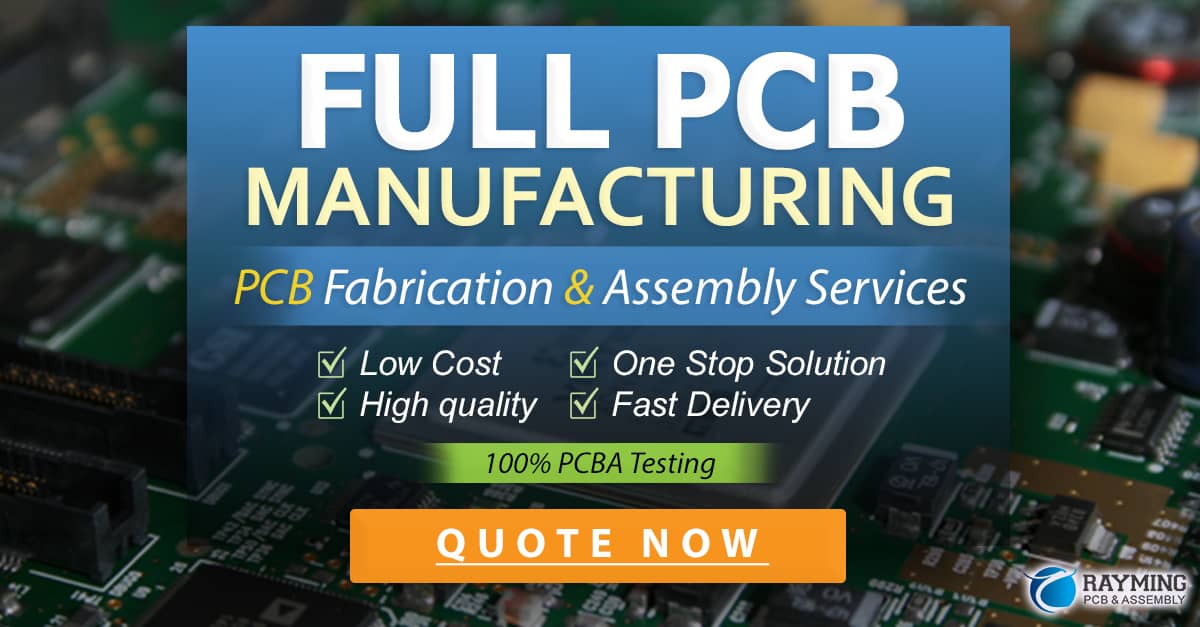
Automotive PCB Manufacturing Process
The manufacturing process for automotive PCBs is similar to that of other PCBs, but with a greater emphasis on quality control and reliability.
-
Design and Layout: The PCB design is created using CAD software, taking into account all of the design considerations mentioned earlier.
-
Material Selection: The appropriate materials are selected based on the specific requirements of the automotive application.
-
Fabrication: The PCB is fabricated using a combination of etching, drilling, and plating processes.
-
Component Placement: Components are placed on the PCB using automated pick-and-place machines.
-
Soldering: The components are soldered to the PCB using reflow or wave soldering techniques.
-
Inspection and Testing: The assembled PCB undergoes rigorous inspection and testing to ensure it meets all quality and performance requirements.
-
Conformal Coating: A protective coating is applied to the PCB to provide additional protection against environmental factors.
Automotive PCB Testing and Validation
To ensure the reliability and performance of automotive PCBs, they must undergo extensive testing and validation. Some of the key tests include:
- Environmental Testing: PCBs are subjected to extreme temperatures, humidity, and vibration to ensure they can withstand harsh automotive environments.
- Electrical Testing: PCBs are tested for proper functionality, signal integrity, and power distribution.
- Accelerated Life Testing: PCBs are subjected to accelerated aging tests to estimate their lifetime performance.
- Compliance Testing: PCBs are tested to ensure they meet relevant automotive industry standards, such as ISO 26262 and AEC-Q100.
Future Trends in Automotive PCBs
As the automotive industry continues to evolve, so too will the requirements for automotive PCBs. Some of the key trends shaping the future of automotive PCBs include:
Increased Electrification
With the growing popularity of electric vehicles (EVs), automotive PCBs will need to handle higher power levels and support more advanced battery management systems.
Autonomous Driving
The development of autonomous driving technologies will require automotive PCBs capable of processing vast amounts of sensor data in real-time while maintaining the highest levels of reliability and safety.
5G Connectivity
The rollout of 5G networks will enable faster data transfer and more reliable connectivity for automotive applications, requiring PCBs that can support high-frequency, high-bandwidth communication.
Miniaturization
As vehicle manufacturers strive to reduce weight and increase efficiency, automotive PCBs will need to become smaller and more compact while still maintaining their performance and reliability.
FAQ
1. What is the difference between automotive PCBs and regular PCBs?
Automotive PCBs are designed to meet the specific requirements of the automotive industry, including resistance to extreme temperatures, vibrations, and chemicals. They also need to comply with strict automotive standards, such as ISO 26262 and AEC-Q100.
2. What materials are commonly used in automotive PCBs?
Common materials used in automotive PCBs include FR-4, polyimide, and ceramic. These materials are selected based on their ability to withstand harsh environmental conditions and provide reliable performance.
3. How are automotive PCBs tested for reliability?
Automotive PCBs undergo rigorous testing to ensure their reliability and performance. This includes environmental testing, electrical testing, accelerated life testing, and compliance testing.
4. What are some of the key applications for automotive PCBs?
Automotive PCBs are used in a wide range of applications, including engine control units (ECUs), infotainment systems, advanced driver assistance systems (ADAS), lighting systems, power management systems, body control modules, and transmission control modules.
5. What are some of the future trends in automotive PCBs?
Future trends in automotive PCBs include increased electrification, autonomous driving, 5G connectivity, and miniaturization. These trends will require PCBs that can handle higher power levels, process vast amounts of data in real-time, support high-frequency communication, and become smaller and more compact.
0 Comments