What are Aluminum PCBs?
Aluminum PCBs, also known as Metal Core PCBs (MCPCBs), are printed circuit boards that use aluminum as the base material instead of the traditional FR-4 material. The aluminum substrate provides excellent thermal conductivity, allowing heat to dissipate quickly from the components mounted on the PCB. This makes aluminum PCBs ideal for applications that generate a lot of heat, such as high-power LEDs, power electronics, and automotive systems.
Key Features of Aluminum PCBs
- Excellent thermal conductivity
- Lightweight and durable
- High mechanical strength
- Good electrical insulation
- Suitable for high-power applications
Benefits of Using Aluminum PCBs
Enhanced Thermal Management
One of the primary benefits of using aluminum PCBs is their superior thermal management capabilities. The aluminum substrate has a high thermal conductivity, which allows heat to dissipate quickly from the components. This helps to prevent overheating and ensures that the components operate within their optimal temperature range, leading to improved performance and longer lifespan.
Material | Thermal Conductivity (W/mK) |
---|---|
Aluminum | 205 – 250 |
Copper | 385 – 400 |
FR-4 | 0.3 – 0.4 |
As seen in the table above, aluminum has a much higher thermal conductivity compared to FR-4, the traditional PCB material. While copper has even higher thermal conductivity, it is more expensive and heavier than aluminum, making aluminum a more cost-effective choice for many applications.
Lightweight and Durable
Aluminum PCBs are lightweight and durable, making them suitable for applications where weight and robustness are critical factors. The lightweight nature of aluminum helps to reduce the overall weight of the device, which is particularly important in automotive and aerospace applications. Additionally, aluminum PCBs have high mechanical strength, which makes them resistant to vibrations and shocks, ensuring reliable performance in harsh environments.
Cost-Effective Solution
Aluminum PCBs offer a cost-effective solution for high-power applications. While they may be more expensive than traditional FR-4 PCBs, they provide superior thermal management and durability, which can lead to cost savings in the long run. By preventing overheating and ensuring reliable performance, aluminum PCBs can help to reduce maintenance and replacement costs, making them a cost-effective choice for many applications.
Applications of Aluminum PCBs
High-Power LEDs
Aluminum PCBs are commonly used in high-power LED applications, such as lighting fixtures and displays. High-power LEDs generate a significant amount of heat, which can negatively impact their performance and lifespan if not properly managed. By using aluminum PCBs, the heat generated by the LEDs can be quickly dissipated, ensuring optimal performance and longer lifespan.
Power Electronics
Power electronics, such as power supplies, inverters, and motor drives, also benefit from the use of aluminum PCBs. These applications often involve high currents and voltages, which can generate a lot of heat. Aluminum PCBs help to dissipate this heat efficiently, preventing overheating and ensuring reliable operation.
Automotive Systems
Aluminum PCBs are increasingly being used in automotive systems, such as engine control units (ECUs), lighting systems, and infotainment systems. The automotive environment can be harsh, with exposure to high temperatures, vibrations, and shocks. Aluminum PCBs provide the necessary thermal management and mechanical strength to withstand these conditions, ensuring reliable performance and longer lifespan.
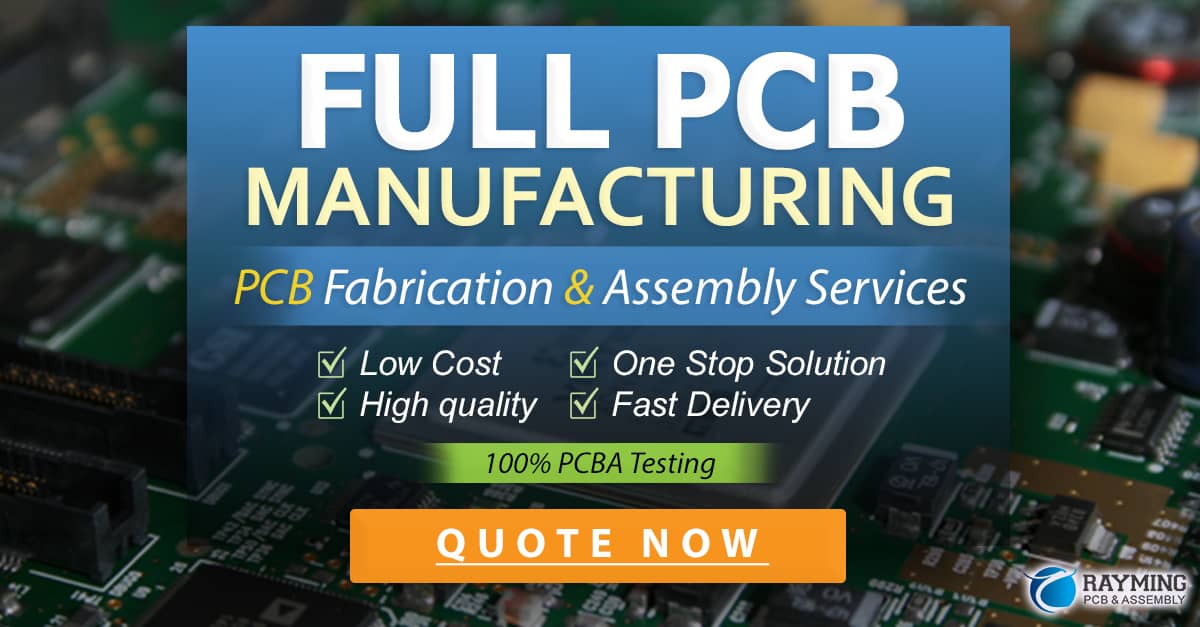
RAYPCB’s Aluminum PCB Solutions
RAYPCB is a leading manufacturer of high-quality aluminum PCBs, offering custom solutions for a wide range of applications. With state-of-the-art manufacturing facilities and a team of experienced engineers, RAYPCB can design and manufacture aluminum PCBs that meet the specific requirements of your application.
Customization Options
RAYPCB offers a range of customization options for aluminum PCBs, including:
- Single-layer and multi-layer designs
- Various aluminum thicknesses
- Different surface finishes (e.g., HASL, OSP, ENIG)
- Custom sizes and shapes
- Blind and buried vias
By working closely with you to understand your application’s requirements, RAYPCB can provide a tailored aluminum PCB solution that meets your needs.
Quality Assurance
RAYPCB is committed to delivering high-quality aluminum PCBs that meet the highest standards of reliability and performance. The company has implemented strict quality control measures throughout the manufacturing process, including:
- Incoming material inspection
- In-process quality checks
- Final product testing
- ISO 9001 and IATF 16949 certifications
These quality assurance measures ensure that every aluminum PCB delivered by RAYPCB meets the required specifications and performs reliably in your application.
Fast Turnaround Times
RAYPCB understands the importance of timely delivery in today’s fast-paced business environment. The company offers fast turnaround times for aluminum PCBs, with lead times as short as 24 hours for prototypes and 5-7 days for production volumes. This enables you to bring your products to market quickly and stay ahead of the competition.
Designing with Aluminum PCBs
When designing with aluminum PCBs, there are several factors to consider to ensure optimal performance and reliability. Here are some key design considerations:
Thermal Management
Proper thermal management is critical when designing with aluminum PCBs. Consider the following factors:
- Component placement: Place high-power components close to the edge of the board to facilitate heat dissipation.
- Thermal vias: Use thermal vias to transfer heat from the components to the aluminum substrate.
- Thermal interface materials: Use thermal interface materials, such as thermal paste or Thermal Pads, to improve heat transfer between the components and the aluminum substrate.
Mechanical Design
Aluminum PCBs have different mechanical properties compared to traditional FR-4 PCBs. Consider the following factors when designing the mechanical aspects of your aluminum PCB:
- Thickness: Choose the appropriate aluminum thickness based on your application’s requirements for thermal management and mechanical strength.
- Mounting: Use appropriate mounting methods, such as screws or rivets, to secure the aluminum PCB to the enclosure or heat sink.
- Flexibility: Keep in mind that aluminum PCBs are less flexible than FR-4 PCBs, so avoid designs that require significant bending or flexing.
Electrical Design
When designing the electrical aspects of your aluminum PCB, consider the following factors:
- Insulation: Ensure adequate insulation between the aluminum substrate and the electrical components to prevent short circuits.
- Grounding: Use appropriate grounding techniques to ensure proper electrical performance and prevent electromagnetic interference (EMI).
- Signal integrity: Consider the impact of the aluminum substrate on signal integrity, especially for high-speed signals, and design your traces and vias accordingly.
FAQ
-
Q: What is the difference between aluminum PCBs and traditional FR-4 PCBs?
A: Aluminum PCBs use an aluminum substrate instead of the traditional FR-4 material, providing better thermal conductivity and mechanical strength. This makes them suitable for high-power applications that generate a lot of heat. -
Q: Are aluminum PCBs more expensive than FR-4 PCBs?
A: Yes, aluminum PCBs are generally more expensive than FR-4 PCBs due to the cost of the aluminum substrate and the specialized manufacturing processes required. However, they offer superior thermal management and durability, which can lead to cost savings in the long run. -
Q: Can aluminum PCBs be used for all types of applications?
A: While aluminum PCBs are suitable for a wide range of applications, they are particularly well-suited for high-power applications that generate a lot of heat, such as LEDs, power electronics, and automotive systems. Traditional FR-4 PCBs may be more appropriate for lower-power applications. -
Q: How do I choose the right aluminum thickness for my PCB?
A: The choice of aluminum thickness depends on your application’s requirements for thermal management and mechanical strength. Thicker aluminum substrates provide better thermal conductivity and mechanical stability but may increase the overall thickness and weight of the PCB. Consult with your PCB manufacturer to determine the optimal aluminum thickness for your application. -
Q: What surface finishes are available for aluminum PCBs?
A: Aluminum PCBs are available with a variety of surface finishes, including HASL (Hot Air Solder Leveling), OSP (Organic Solderability Preservative), and ENIG (Electroless Nickel Immersion Gold). The choice of surface finish depends on your application’s requirements for solderability, durability, and cost. Consult with your PCB manufacturer to determine the best surface finish for your application.
Conclusion
Aluminum PCBs offer a superior solution for high-power applications that require efficient thermal management and robust mechanical performance. By using an aluminum substrate instead of traditional FR-4 material, aluminum PCBs provide excellent thermal conductivity, lightweight durability, and cost-effectiveness. With a wide range of applications, from high-power LEDs to automotive systems, aluminum PCBs are an increasingly popular choice for designers and engineers.
RAYPCB is a leading manufacturer of high-quality aluminum PCBs, offering custom solutions for a wide range of applications. With state-of-the-art manufacturing facilities, experienced engineers, and a commitment to quality assurance, RAYPCB can provide tailored aluminum PCB solutions that meet your specific requirements. By considering key design factors such as thermal management, mechanical design, and electrical design, you can ensure optimal performance and reliability when designing with aluminum PCBs.
As the demand for high-power electronics continues to grow, the use of aluminum PCBs is set to increase. By partnering with a reputable manufacturer like RAYPCB and following best design practices, you can harness the benefits of aluminum PCBs to create innovative, reliable, and cost-effective solutions for your high-power applications.
0 Comments