What is FR-4 PCB?
FR-4 PCB, also known as Flame Retardant 4 Printed Circuit Board, is a type of PCB material that is widely used in the electronics industry. It is made from a composite material consisting of woven fiberglass cloth with an epoxy resin binder. The “FR” in FR-4 stands for “Flame Retardant,” indicating that the material has excellent flame-resistant properties.
FR-4 PCBs are known for their superior mechanical and electrical properties, making them an ideal choice for a wide range of applications. They offer good insulation, high strength, and excellent resistance to heat and moisture. These characteristics make FR-4 PCBs suitable for use in various industries, including telecommunications, aerospace, medical devices, and consumer electronics.
Advantages of FR-4 PCB
FR-4 PCBs offer several advantages over other PCB materials, making them a popular choice among manufacturers and designers. Some of the key advantages include:
-
High Strength and Durability: FR-4 PCBs are made from a strong and durable composite material that can withstand mechanical stress and vibrations. This makes them suitable for use in harsh environments and applications that require high reliability.
-
Excellent Electrical Insulation: The epoxy resin used in FR-4 PCBs provides excellent electrical insulation properties. This helps to prevent short circuits and ensures the proper functioning of the electronic components mounted on the PCB.
-
Flame Retardant: As the name suggests, FR-4 PCBs have excellent flame-retardant properties. They are designed to self-extinguish when exposed to fire, minimizing the risk of fire hazards in electronic devices.
-
Moisture Resistance: FR-4 PCBs have good resistance to moisture and humidity. This helps to prevent corrosion and ensures the long-term reliability of the electronic components.
-
Wide Temperature Range: FR-4 PCBs can operate in a wide temperature range, typically from -55°C to +125°C. This makes them suitable for use in various environmental conditions.
FR-4 PCB Manufacturing Process
The manufacturing process of FR-4 PCBs involves several steps, each of which is critical to ensuring the quality and reliability of the final product. The main steps in the manufacturing process are as follows:
-
Design and Artwork Creation: The first step in the manufacturing process is to create the PCB design and artwork. This involves using specialized software to create the schematic diagram and layout of the PCB.
-
Printing and Etching: Once the design is finalized, the artwork is printed onto a photosensitive film. This film is then used to transfer the design onto the copper-clad FR-4 laminate using a photolithographic process. The unwanted copper is then etched away, leaving only the desired circuit pattern.
-
Drilling: After the etching process, holes are drilled into the PCB to accommodate the electronic components and connectors. The drilling process is typically done using computer-controlled drilling machines to ensure precision and accuracy.
-
Plating: The drilled holes are then plated with copper to create a conductive path between the layers of the PCB. This is followed by a tin-lead or lead-free solder plating process to protect the copper and improve solderability.
-
Solder Mask and Silkscreen: A solder mask is applied to the PCB to protect the copper traces from oxidation and prevent solder bridges during the assembly process. A silkscreen layer is then added to the PCB to provide component labels and other identifying markings.
-
Surface Finish: The final step in the manufacturing process is to apply a surface finish to the PCB. This can be done using various methods, such as Hot Air Solder Leveling (HASL), Immersion Silver, Immersion Tin, or Electroless Nickel Immersion Gold (ENIG). The choice of surface finish depends on the specific requirements of the application.
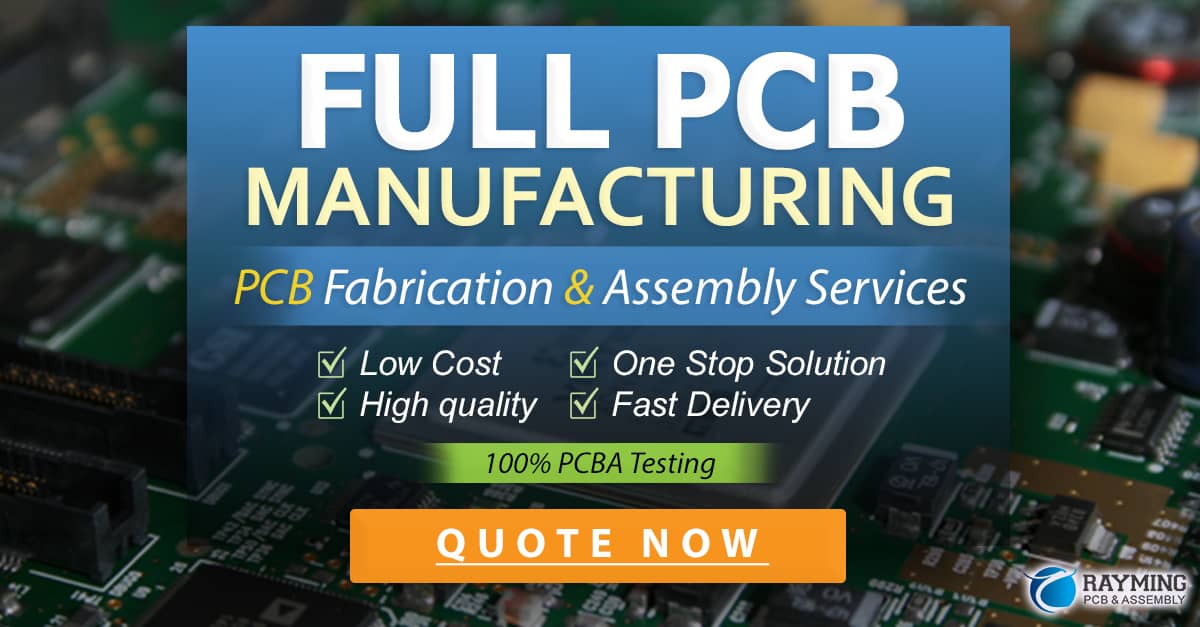
Choosing the Right FR-4 PCB Manufacturer
Choosing the right FR-4 PCB manufacturer is critical to ensuring the quality and reliability of your electronic products. Here are some factors to consider when selecting an FR-4 PCB manufacturer:
-
Experience and Expertise: Look for a manufacturer with extensive experience in producing FR-4 PCBs. They should have a proven track record of delivering high-quality products and have the necessary expertise to handle your specific requirements.
-
Quality Control: Ensure that the manufacturer has a robust quality control system in place. They should follow industry standards and have certifications such as ISO 9001 and UL. Ask about their testing and inspection procedures to ensure that the PCBs meet your specifications.
-
Manufacturing Capabilities: Consider the manufacturer’s manufacturing capabilities, including their production capacity, lead times, and ability to handle both small and large volume orders. They should have state-of-the-art equipment and processes to ensure consistent quality.
-
Customer Support: Choose a manufacturer that provides excellent customer support. They should be responsive to your inquiries and provide timely updates on the status of your order. Look for a manufacturer that offers design support and can provide guidance on material selection and manufacturability.
-
Cost and Delivery: While cost is an important factor, it should not be the sole determining factor when choosing an FR-4 PCB manufacturer. Look for a manufacturer that offers competitive pricing without compromising on quality. Also, consider their delivery times and whether they can meet your scheduling requirements.
Applications of FR-4 PCB
FR-4 PCBs are used in a wide range of applications across various industries. Some of the common applications include:
-
Consumer Electronics: FR-4 PCBs are widely used in consumer electronic devices such as smartphones, tablets, laptops, and televisions. They provide the necessary strength and durability to withstand daily use and ensure reliable performance.
-
Telecommunications: FR-4 PCBs are used in telecommunications equipment such as routers, switches, and modems. They offer excellent signal integrity and help to ensure the reliable transmission of data.
-
Automotive: FR-4 PCBs are used in various automotive applications, including engine control units, infotainment systems, and sensors. They are designed to withstand the harsh environmental conditions encountered in vehicles.
-
Medical Devices: FR-4 PCBs are used in medical devices such as patient monitors, diagnostic equipment, and surgical instruments. They offer high reliability and are designed to meet the strict regulatory requirements of the medical industry.
-
Aerospace: FR-4 PCBs are used in aerospace applications such as avionics systems, radar systems, and satellite communications. They are designed to withstand extreme temperatures and vibrations encountered in aerospace environments.
FR-4 PCB Material Properties
FR-4 PCBs are made from a composite material consisting of woven fiberglass cloth with an epoxy resin binder. The material properties of FR-4 PCBs are as follows:
Property | Value |
---|---|
Dielectric Constant (at 1 MHz) | 4.2 – 4.9 |
Dissipation Factor (at 1 MHz) | 0.020 – 0.030 |
Dielectric Strength (kV/mm) | 20 – 28 |
Thermal Conductivity (W/mK) | 0.3 – 0.4 |
Coefficient of Thermal Expansion (ppm/°C) | 12 – 18 |
Density (g/cm³) | 1.8 – 2.0 |
Flexural Strength (MPa) | 310 – 380 |
Moisture Absorption (%) | 0.1 – 0.3 |
These properties make FR-4 PCBs suitable for a wide range of applications and ensure reliable performance under various environmental conditions.
FR-4 PCB Design Considerations
When designing FR-4 PCBs, there are several factors to consider to ensure optimal performance and manufacturability. Some of the key design considerations include:
-
Layer Stack-up: The number of layers and their arrangement in the PCB Stack-up can affect the signal integrity and manufacturability of the PCB. It is important to choose the appropriate number of layers and their arrangement based on the specific requirements of the application.
-
Trace Width and Spacing: The width and spacing of the copper traces on the PCB can affect the signal integrity and manufacturability of the PCB. It is important to choose the appropriate trace width and spacing based on the current carrying requirements and the manufacturing capabilities of the PCB manufacturer.
-
Via Design: Vias are used to connect the different layers of the PCB. The size and spacing of the vias can affect the signal integrity and manufacturability of the PCB. It is important to choose the appropriate via size and spacing based on the specific requirements of the application and the manufacturing capabilities of the PCB manufacturer.
-
Impedance Control: Impedance control is critical for high-speed PCB designs. It involves controlling the impedance of the copper traces to ensure proper signal integrity. This can be achieved by adjusting the trace width, spacing, and dielectric thickness of the PCB.
-
Thermal Management: Proper thermal management is essential to ensure the reliable performance of the electronic components mounted on the PCB. This can be achieved by using thermal vias, heat sinks, and other thermal management techniques.
Frequently Asked Questions (FAQ)
-
What is the difference between FR-4 and other PCB materials?
FR-4 is a composite material made from woven fiberglass cloth with an epoxy resin binder. It offers superior mechanical and electrical properties compared to other PCB materials such as phenolic paper and CEM-1. FR-4 PCBs have higher strength, better insulation, and excellent flame retardancy. -
Can FR-4 PCBs be used for high-frequency applications?
While FR-4 PCBs are suitable for many applications, they may not be the best choice for high-frequency applications above a few gigahertz. At higher frequencies, the dielectric losses in FR-4 material can become significant, leading to signal integrity issues. For high-frequency applications, other PCB materials such as Rogers or Teflon may be more suitable. -
What is the maximum operating temperature of FR-4 PCBs?
The maximum operating temperature of FR-4 PCBs is typically around 130°C. However, the actual maximum temperature can vary depending on the specific composition of the FR-4 material and the manufacturing process used. Some specialized FR-4 materials can operate at temperatures up to 170°C. -
How do I choose the right thickness for my FR-4 PCB?
The choice of PCB thickness depends on several factors, including the number of layers, the component sizes, and the mechanical requirements of the application. Thicker PCBs offer better mechanical stability and can accommodate more layers, but they also increase the weight and cost of the PCB. Thinner PCBs are lighter and less expensive but may be more prone to warping and mechanical stress. A common thickness for FR-4 PCBs is 1.6 mm, but other thicknesses ranging from 0.4 mm to 3.2 mm are also available. -
Can FR-4 PCBs be recycled?
Yes, FR-4 PCBs can be recycled. The recycling process typically involves shredding the PCBs and separating the different materials, such as copper, fiberglass, and resins, using various mechanical and chemical processes. The recovered materials can then be used to manufacture new PCBs or other products. However, the recycling process for FR-4 PCBs is complex and requires specialized equipment and expertise.
Conclusion
FR-4 PCBs are a popular choice for a wide range of applications due to their superior mechanical and electrical properties. They offer high strength, excellent insulation, and good resistance to heat and moisture. When choosing an FR-4 PCB manufacturer, it is important to consider factors such as experience, quality control, manufacturing capabilities, customer support, and cost.
Designing FR-4 PCBs requires careful consideration of various factors such as layer stack-up, trace width and spacing, via design, impedance control, and thermal management. By following best design practices and working closely with an experienced PCB manufacturer, designers can ensure the optimal performance and reliability of their electronic products.
As the electronics industry continues to evolve, FR-4 PCBs are likely to remain a key material for PCB manufacturing. With their wide range of applications and proven track record of reliability, FR-4 PCBs will continue to play a critical role in enabling the next generation of electronic devices and systems.
0 Comments