In the realm of printed circuit board (PCB) technology, aluminum has emerged as a unique and versatile material for various applications. While traditional PCBs are typically made of fiberglass or phenolic resin substrates, aluminum PCBs offer distinct advantages that make them indispensable in specific industries and applications. This article will delve into the world of aluminum PCBs, exploring their characteristics, advantages, and the diverse range of applications where they excel.
Understanding Aluminum PCBs
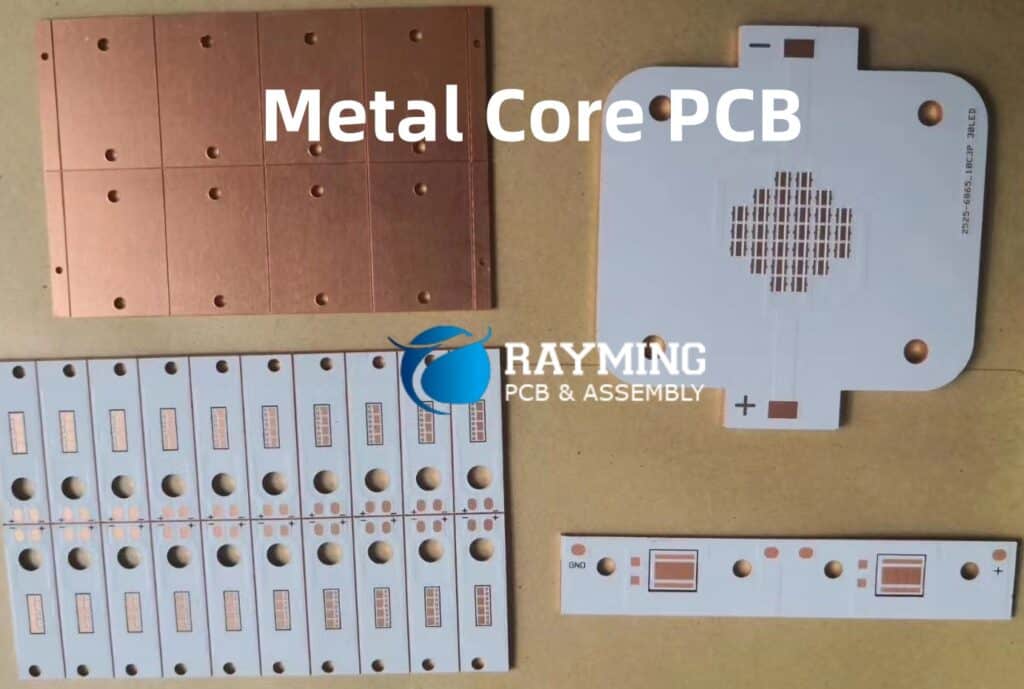
Before we explore the applications of aluminum PCBs, it’s essential to understand their fundamental properties and characteristics.
Composition and Structure
Aluminum PCBs are constructed using aluminum as the base substrate material, typically an aluminum alloy with high thermal conductivity. The aluminum substrate is coated with a dielectric layer, such as polyimide or alumina, onto which the conductive copper traces and pads are deposited or etched.
Advantages of Aluminum PCBs
Aluminum PCBs offer several advantages over traditional PCBs, making them suitable for various applications:
- Excellent Thermal Conductivity: Aluminum is an excellent thermal conductor, outperforming materials like FR-4 (fiberglass-reinforced epoxy laminate) commonly used in traditional PCBs. This superior thermal conductivity allows for efficient heat dissipation, making aluminum PCBs ideal for applications involving high-power components or harsh thermal environments.
- Lightweight and Rigid: Aluminum is a lightweight yet rigid material, providing a sturdy base for PCB assemblies while reducing overall weight. This characteristic is beneficial in applications where weight is a critical factor, such as aerospace, automotive, and portable electronics.
- Corrosion Resistance: Aluminum is naturally resistant to corrosion, making it suitable for use in harsh environments where traditional PCBs might degrade or fail.
- Electromagnetic Interference (EMI) Shielding: The conductive nature of aluminum provides excellent EMI shielding capabilities, which is crucial in applications involving sensitive electronic components or radio frequency (RF) systems.
- Recyclability: Aluminum is a highly recyclable material, making aluminum PCBs an environmentally friendly choice for electronics manufacturing.
Applications of Aluminum PCBs
Aluminum PCBs have found widespread applications across various industries due to their unique properties and capabilities. Here are some of the key applications where aluminum PCBs excel:
Power Electronics
Power electronics applications, such as motor drives, inverters, and power supplies, often involve high currents and significant heat generation. Aluminum PCBs’ excellent thermal conductivity and lightweight design make them well-suited for these applications, providing effective heat dissipation and allowing for compact and efficient designs.
Automotive Electronics
The automotive industry has embraced aluminum PCBs for various electronic systems, including engine control units (ECUs), infotainment systems, and advanced driver assistance systems (ADAS). The lightweight and rigid nature of aluminum PCBs contributes to weight reduction and improved fuel efficiency, while their thermal management capabilities ensure reliable operation in harsh automotive environments.
Aerospace and Defense
The aerospace and defense sectors demand high-performance and reliable electronic systems capable of withstanding extreme environmental conditions. Aluminum PCBs’ corrosion resistance, EMI shielding, and thermal management capabilities make them ideal for applications such as avionics, radar systems, and satellite electronics.
LED Lighting and Display Systems
LED lighting and display systems generate significant amounts of heat, which can adversely affect their performance and lifespan. Aluminum PCBs’ excellent thermal dissipation properties help to efficiently remove heat from the LEDs, ensuring optimal performance and longevity.
Telecommunications and RF Systems
The telecommunications and RF industries require PCBs with excellent EMI shielding and thermal management capabilities. Aluminum PCBs meet these requirements, making them suitable for applications such as base stations, wireless routers, and RF amplifiers.
Industrial Automation and Control Systems
Industrial automation and control systems often operate in harsh environments with exposure to temperature extremes, vibrations, and contaminants. The ruggedness and corrosion resistance of aluminum PCBs make them suitable for use in these challenging conditions.
Medical and Healthcare Electronics
The medical and healthcare industries demand high-reliability electronics capable of operating in demanding environments. Aluminum PCBs’ thermal management capabilities and resistance to corrosion make them suitable for applications such as patient monitoring devices, medical imaging equipment, and surgical instruments.
Advantages and Disadvantages of Aluminum PCBs
Like any technology, aluminum PCBs have their advantages and disadvantages, which should be carefully considered when selecting the appropriate PCB material for a specific application.
Advantages
- Excellent thermal conductivity for efficient heat dissipation
- Lightweight yet rigid construction
- Corrosion resistance in harsh environments
- EMI shielding capabilities
- Environmentally friendly and recyclable
Disadvantages
- Higher cost compared to traditional PCBs
- Limited flexibility and susceptibility to stress fractures
- Specialized manufacturing processes and equipment required
- Potential galvanic corrosion issues when combined with dissimilar metals
- Limited availability of high-layer count options
Comparison with Traditional PCBs
To better understand the advantages and suitability of aluminum PCBs, it’s helpful to compare them with traditional PCBs made from materials like FR-4.
Characteristic | Aluminum PCBs | Traditional FR-4 PCBs |
---|---|---|
Thermal Conductivity | Excellent | Poor to moderate |
Weight | Lightweight | Heavier |
Rigidity | High | Moderate |
Corrosion Resistance | High | Low to moderate |
EMI Shielding | Excellent | Moderate |
Cost | Higher | Lower |
Flexibility | Limited | Higher |
Availability (High Layer Count) | Limited | Widely available |
As the table illustrates, aluminum PCBs excel in thermal management, weight reduction, rigidity, corrosion resistance, and EMI shielding, making them suitable for applications with demanding environmental conditions or high-power requirements. However, traditional FR-4 PCBs offer better flexibility, lower cost, and wider availability for high-layer count designs.
FAQ (Frequently Asked Questions)
- Q: Can aluminum PCBs be used in high-frequency applications? A: While aluminum PCBs offer excellent EMI shielding, their electrical properties may not be optimal for high-frequency applications compared to traditional PCB materials. However, with careful design and the use of specialized dielectric materials, aluminum PCBs can be utilized in certain high-frequency applications.
- Q: Are aluminum PCBs more expensive than traditional PCBs? A: Yes, aluminum PCBs tend to be more expensive than traditional FR-4 PCBs due to the higher cost of materials and specialized manufacturing processes required.
- Q: Can aluminum PCBs be repaired or reworked? A: Repairing or reworking aluminum PCBs can be more challenging compared to traditional PCBs due to the potential for stress fractures and the specialized processes involved. However, with proper techniques and equipment, it is possible to perform repairs or rework on aluminum PCBs.
- Q: Are aluminum PCBs suitable for high-layer count designs? A: Aluminum PCBs are typically limited in terms of high-layer count designs due to manufacturing constraints. Traditional FR-4 PCBs are more widely available and better suited for high-layer count applications.
- Q: Can aluminum PCBs be used in consumer electronics? A: While aluminum PCBs are not commonly used in consumer electronics due to their higher cost, they can be found in certain high-end or specialized consumer products where thermal management, EMI shielding, or weight reduction is critical.
Conclusion
Aluminum PCBs have carved a significant niche in the electronics industry, offering unique advantages in thermal management, weight reduction, corrosion resistance, and EMI shielding. Their applications span a wide range of industries, including power electronics, automotive, aerospace, LED lighting, telecommunications, industrial automation, and medical electronics.
While aluminum PCBs may come at a higher cost and have limitations in terms of flexibility and high-layer count designs, their exceptional thermal conductivity and reliable performance in harsh environments make them an invaluable choice for applications with demanding thermal or environmental requirements.
As technology continues to evolve and the demand for high-performance, efficient, and reliable electronics increases, aluminum PCBs will undoubtedly play a crucial role in meeting these challenges. By leveraging their unique properties and capabilities, engineers and designers can push the boundaries of electronic systems, enabling innovative solutions across various sectors.
0 Comments