Introduction to Breadboard-to-PCB Transition
Breadboarding is an essential step in the electronics design process, allowing for quick prototyping and testing of circuits. However, once a design has been finalized, it’s time to move from the breadboard to a printed circuit board (PCB) for a more permanent and reliable solution. This transition from breadboard to PCB is a crucial step in turning a prototype into a full product.
In this comprehensive guide, we’ll walk you through the process of moving from a breadboard prototype to a PCB-based product. We’ll cover the key considerations, design steps, and manufacturing processes involved in this transition.
Understanding the Differences Between Breadboards and PCBs
Before diving into the transition process, it’s important to understand the fundamental differences between breadboards and PCBs.
Breadboards
Breadboards are prototyping tools used for temporary construction and testing of electronic circuits. They consist of a plastic board with a grid of holes, into which component leads and jumper wires can be inserted to create connections without the need for soldering.
Advantages of breadboards:
– Quick and easy prototyping
– Reusable and reconfigurable
– No soldering required
Disadvantages of breadboards:
– Limited durability and reliability
– Not suitable for permanent installations
– Prone to loose connections and electrical noise
Printed Circuit Boards (PCBs)
PCBs are custom-designed boards that provide a permanent and reliable platform for electronic circuits. They consist of a non-conductive substrate (usually fiberglass) with conductive copper traces etched onto the surface to create electrical connections between components.
Advantages of PCBs:
– Durable and reliable
– Compact and space-efficient
– Reduced electrical noise and improved signal integrity
– Suitable for mass production
Disadvantages of PCBs:
– Higher initial cost compared to breadboards
– Requires design and manufacturing time
– Modifications require redesign and fabrication of new boards
Steps in the Breadboard-to-PCB Transition Process
Step 1: Finalize and Validate the Breadboard Design
Before transitioning to a PCB, ensure that your breadboard prototype is fully functional and meets all design requirements. Conduct thorough testing and debugging to identify and resolve any issues.
Step 2: Create a Schematic Diagram
Convert your breadboard circuit into a schematic diagram using electronic design automation (EDA) software. A schematic diagram represents the logical connections between components using standardized symbols.
Tips for creating a schematic diagram:
– Use clear and consistent component symbols
– Label all components and nets
– Organize the schematic for readability
– Include power and ground connections
Step 3: Design the PCB Layout
Using the schematic diagram as a reference, design the physical layout of your PCB using EDA software. The PCB layout determines the placement of components and the routing of copper traces on the board.
Considerations for PCB layout design:
– Component placement for optimal signal integrity and manufacturability
– Trace width and spacing based on current requirements and manufacturing capabilities
– Ground plane and power plane design for noise reduction and power distribution
– Design rule checking (DRC) to ensure compliance with manufacturing constraints
Step 4: Generate Manufacturing Files
Once the PCB layout is finalized, generate the necessary manufacturing files, including:
– Gerber files: Industry-standard files that describe the copper layers, solder mask, and silkscreen
– Drill files: Specifies the locations and sizes of holes for through-hole components and vias
– Bill of Materials (BOM): A list of all components used in the design, including quantities and specifications
Step 5: Prototype and Test the PCB
Before mass production, fabricate a small batch of Prototype PCBs for testing and validation. Assemble the components onto the prototype boards and conduct thorough testing to ensure proper functionality and performance.
Testing considerations:
– Electrical continuity and short-circuit testing
– Functional testing under various operating conditions
– EMC (electromagnetic compatibility) testing, if required
– Stress testing and environmental testing, depending on the application
Step 6: Mass Production and Assembly
Once the prototype PCBs have been validated, proceed with mass production and assembly. Work with a reputable PCB manufacturer and assembly service to ensure high-quality and reliable production.
Mass production considerations:
– Choose appropriate PCB materials and surface finishes based on application requirements
– Specify component sourcing and handling requirements
– Implement quality control measures, such as automated optical inspection (AOI) and functional testing
– Consider packaging and shipping requirements for the final product
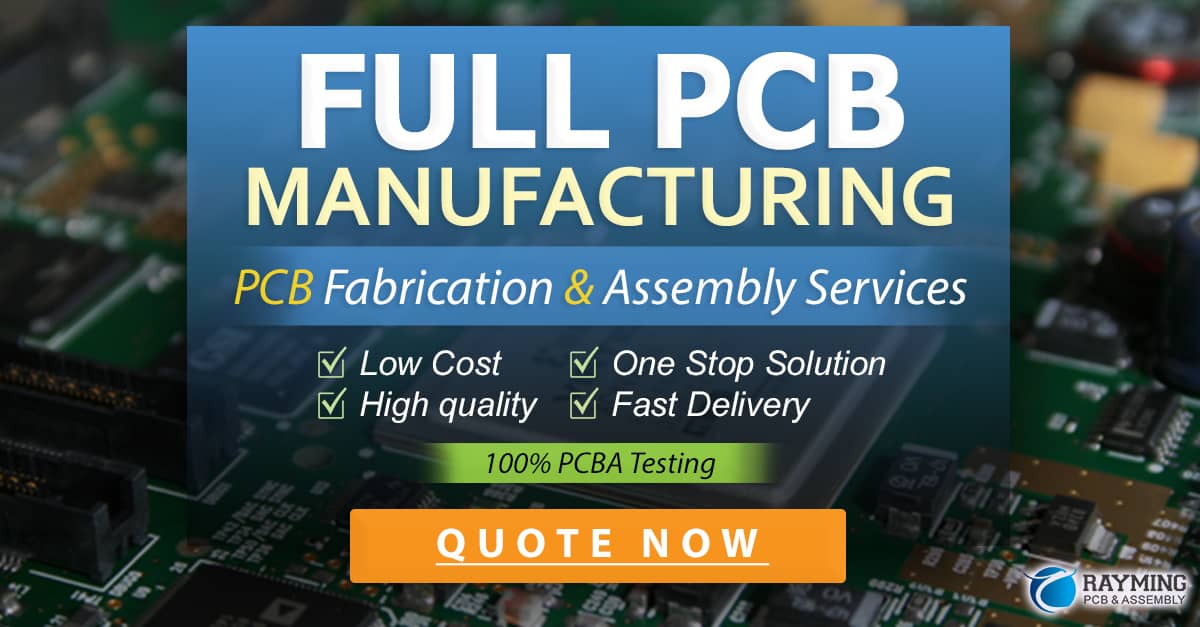
Best Practices for Successful Breadboard-to-PCB Transition
To ensure a smooth and successful transition from breadboard to PCB, consider the following best practices:
-
Document your breadboard design thoroughly, including component values, connections, and any modifications made during testing.
-
Use a modular approach in your schematic and PCB design, separating different functional blocks for easier troubleshooting and future modifications.
-
Follow industry-standard design guidelines and manufacturing constraints to ensure compatibility with PCB Fabrication and assembly processes.
-
Collaborate with experienced PCB designers and manufacturers to leverage their expertise and avoid common pitfalls.
-
Allow sufficient time for design iterations, prototyping, and testing to ensure a high-quality final product.
Common Challenges and Solutions in Breadboard-to-PCB Transition
Challenge 1: Incorrect Component Footprints
Problem: Incorrect component footprints in the PCB design lead to assembly issues and potential functionality problems.
Solution: Double-check component footprints against manufacturer datasheets and use trusted component libraries in your EDA software.
Challenge 2: Signal Integrity Issues
Problem: Poor signal integrity due to improper trace routing, grounding, or component placement.
Solution: Follow best practices for PCB layout, including proper trace width and spacing, ground plane design, and component placement for minimal crosstalk and noise.
Challenge 3: Manufacturing Constraints
Problem: Designs that violate manufacturing constraints, such as minimum trace width or clearance, leading to fabrication issues or higher costs.
Solution: Communicate with your PCB manufacturer early in the design process to understand their specific manufacturing constraints and incorporate them into your design rules.
Challenge 4: Component Availability and Obsolescence
Problem: Designing with components that are difficult to source or at risk of obsolescence, leading to production delays or redesigns.
Solution: Choose components with good availability and long-term supply. Consider alternative components or redesign strategies to mitigate the risk of obsolescence.
Frequently Asked Questions (FAQ)
-
Q: Can I use the same components from my breadboard prototype on the PCB?
A: In most cases, yes. However, ensure that the components are suitable for PCB mounting and that their footprints match the PCB design. -
Q: How long does the breadboard-to-PCB transition process typically take?
A: The timeline varies depending on the complexity of the design and the manufacturing processes involved. A simple design can take a few weeks, while more complex projects may require several months. -
Q: What are the costs involved in transitioning from breadboard to PCB?
A: Costs include PCB design software, prototype fabrication, component procurement, and mass production. The specific costs depend on factors such as design complexity, PCB specifications, and production volume. -
Q: Do I need to have PCB design expertise to transition from breadboard to PCB?
A: While PCB design expertise is beneficial, many EDA software tools offer user-friendly interfaces and automated features that can help novice designers. Collaborating with experienced PCB designers can also facilitate the transition process. -
Q: What should I consider when choosing a PCB manufacturer?
A: Consider factors such as manufacturing capabilities, quality control processes, lead times, pricing, and customer support. Look for manufacturers with experience in your specific industry or application.
Conclusion
Transitioning from a breadboard prototype to a PCB-based product is a significant milestone in the electronics design process. By understanding the differences between breadboards and PCBs, following a systematic transition process, and adhering to best practices, you can successfully convert your prototype into a reliable and manufacturable product.
Remember to prioritize thorough testing, design for manufacturability, and collaboration with experienced professionals throughout the transition process. With careful planning and execution, your breadboard-to-PCB transition will result in a high-quality product ready for mass production and market introduction.
0 Comments