Introduction
FR4 (Flame Retardant 4) is a commonly used material in the manufacturing of printed circuit boards (PCBs). It is a composite material made of woven fiberglass cloth with an epoxy resin binder that is flame resistant. FR4 is known for its excellent mechanical, electrical, and thermal properties, making it an ideal choice for various applications in the electronics industry. One of the crucial properties of FR4 is its thermal conductivity, which plays a significant role in the performance and reliability of electronic devices. In this comprehensive guide, we will delve into the details of FR4 Thermal Conductivity, its importance, factors affecting it, measurement techniques, and ways to enhance it.
What is Thermal Conductivity?
Thermal conductivity is a physical property that describes a material’s ability to conduct heat. It is defined as the rate at which heat is transferred through a material per unit thickness, per unit area, and per unit temperature difference. In other words, thermal conductivity measures how well a material allows heat to flow through it. The SI unit for thermal conductivity is watts per meter-kelvin (W/(m·K)).
Importance of Thermal Conductivity in PCBs
Thermal conductivity is a critical factor in the design and performance of printed circuit boards. PCBs are the backbone of electronic devices, and they are responsible for mechanically supporting and electrically connecting various components using conductive pathways, tracks, or signal traces etched from copper sheets laminated onto a non-conductive substrate. During operation, electronic components generate heat, which must be dissipated efficiently to prevent overheating and ensure the device’s proper functioning and longevity.
A PCB substrate with high thermal conductivity allows for better heat dissipation, reducing the risk of component failure due to thermal stress. On the other hand, a substrate with low thermal conductivity can lead to heat accumulation, which may cause components to malfunction, degrade, or even fail prematurely. Therefore, understanding and optimizing the thermal conductivity of PCB materials, such as FR4, is essential for designing reliable and high-performance electronic devices.
FR4 Thermal Conductivity
FR4 is a popular choice for PCB substrates due to its excellent balance of properties and cost-effectiveness. The thermal conductivity of FR4 is an important consideration in PCB design, as it directly affects the board’s ability to dissipate heat generated by the components.
Typical Values of FR4 Thermal Conductivity
The thermal conductivity of FR4 can vary depending on factors such as the specific composition, manufacturing process, and thickness of the material. However, typical values of FR4 thermal conductivity range from 0.25 to 0.4 W/(m·K) in the through-plane direction (perpendicular to the board surface) and 0.6 to 1.0 W/(m·K) in the in-plane direction (parallel to the board surface).
Direction | Thermal Conductivity Range (W/(m·K)) |
---|---|
Through-plane | 0.25 – 0.4 |
In-plane | 0.6 – 1.0 |
It is important to note that the thermal conductivity of FR4 is anisotropic, meaning that it has different values in different directions. The in-plane thermal conductivity is generally higher than the through-plane thermal conductivity due to the presence of the woven fiberglass reinforcement, which provides a more efficient heat transfer path along the fibers.
Factors Affecting FR4 Thermal Conductivity
Several factors can influence the thermal conductivity of FR4, including:
-
Resin composition: The type and proportion of epoxy resin used in the FR4 Laminate can affect its thermal conductivity. Some specialized resins with higher thermal conductivity can be used to improve the overall thermal performance of the PCB.
-
Fiberglass reinforcement: The type, orientation, and volume fraction of the fiberglass reinforcement in FR4 can impact its thermal conductivity. Higher glass fiber content generally leads to higher in-plane thermal conductivity but may slightly reduce through-plane thermal conductivity.
-
Filler materials: The addition of thermally conductive filler materials, such as ceramic particles or metal oxides, can enhance the thermal conductivity of FR4. However, this may also affect other properties, such as dielectric constant and mechanical strength.
-
Thickness: The thickness of the FR4 laminate can influence its thermal conductivity. Thicker laminates generally have lower through-plane thermal conductivity due to the increased distance heat must travel through the material.
-
Manufacturing process: The manufacturing process, including the curing temperature and pressure, can affect the final thermal conductivity of FR4. Variations in the process parameters may lead to slight differences in thermal conductivity between batches.
Understanding these factors allows PCB designers to make informed decisions when selecting FR4 laminates and designing boards for optimal thermal management.
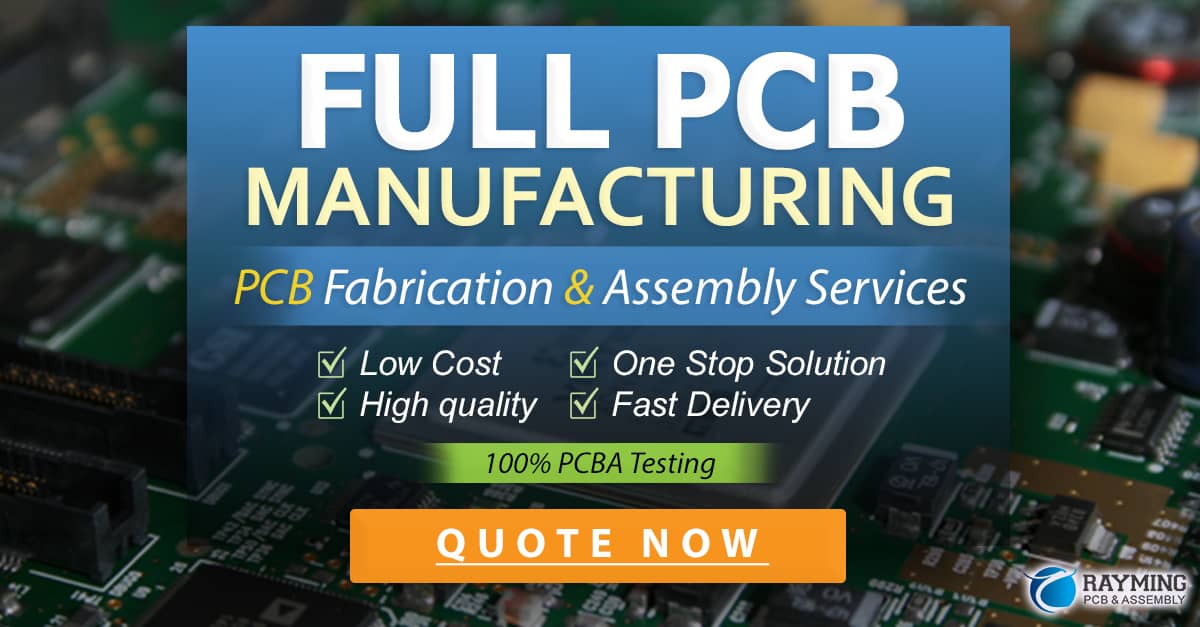
Measuring FR4 Thermal Conductivity
Accurate measurement of FR4 thermal conductivity is essential for characterizing the material and ensuring its suitability for specific applications. Several techniques can be used to measure the thermal conductivity of FR4, including:
-
Guarded Hot Plate Method: This method involves placing the FR4 sample between two temperature-controlled plates, with a guard heater surrounding the main heater to minimize lateral heat flow. The thermal conductivity is calculated based on the power input to the main heater and the temperature gradient across the sample.
-
Laser Flash Method: In this technique, a short laser pulse is used to heat one side of the FR4 sample, and the temperature rise on the opposite side is measured using an infrared detector. The thermal diffusivity of the material is determined from the temperature rise data, and the thermal conductivity is calculated using the material’s density and specific heat capacity.
-
Heat Flow Meter Method: This method uses two heat flow meters, placed on either side of the FR4 sample, to measure the heat flow through the material. The thermal conductivity is calculated based on the heat flow, sample thickness, and temperature difference between the two surfaces.
-
Transient Plane Source (TPS) Method: The TPS method uses a thin, electrically insulated sensor that acts as both a heat source and a temperature sensor. The sensor is placed between two pieces of the FR4 sample, and a constant electrical power is applied to the sensor. The temperature rise over time is measured, and the thermal conductivity is calculated using a mathematical model.
Each measurement technique has its advantages and limitations, and the choice of method depends on factors such as sample size, desired accuracy, and available equipment. Standardized test methods, such as ASTM E1530 and ISO 22007-2, provide guidelines for measuring the thermal conductivity of plastics and insulating materials using the guarded hot plate and laser flash methods, respectively.
Enhancing FR4 Thermal Conductivity
In applications where higher thermal conductivity is required, various strategies can be employed to enhance the thermal performance of FR4 PCBs. These include:
-
Using high-performance FR4 laminates: Some manufacturers offer specialized FR4 laminates with improved thermal conductivity. These laminates may incorporate thermally conductive fillers or use resins with higher thermal conductivity.
-
Incorporating thermal vias: Thermal vias are small, plated through-holes that are strategically placed in the PCB to provide a low-resistance path for heat transfer. By connecting thermal vias to heat-generating components and ground planes, the overall thermal conductivity of the board can be improved.
-
Using Metal Core PCBs: Metal core PCBs (MCPCBs) consist of a metal substrate, typically aluminum, with a thin layer of dielectric material and copper foil laminated on top. The metal substrate provides a high thermal conductivity path for heat dissipation, making MCPCBs suitable for high-power applications.
-
Employing thermal interface materials: Thermal interface materials (TIMs), such as thermal greases, pads, or adhesives, can be used to improve the thermal contact between components and the PCB. These materials fill the air gaps and irregularities between surfaces, enhancing heat transfer.
-
Optimizing PCB layout: Proper PCB layout techniques, such as placing high-power components near board edges, providing adequate copper area for heat spreading, and avoiding thermal bottlenecks, can help improve the overall thermal performance of the board.
By implementing these strategies, designers can effectively manage the thermal challenges associated with FR4 PCBs and ensure the reliable operation of electronic devices.
FAQ
What is FR4, and why is it commonly used in PCBs?
FR4 (Flame Retardant 4) is a composite material made of woven fiberglass cloth impregnated with an epoxy resin binder. It is commonly used in the manufacturing of printed circuit boards (PCBs) due to its excellent mechanical, electrical, and thermal properties, as well as its flame-retardant characteristics. FR4 provides a stable and reliable substrate for mounting and interconnecting electronic components in a wide range of applications.
How does the thermal conductivity of FR4 compare to other PCB materials?
The thermal conductivity of FR4 is relatively low compared to other PCB materials, such as metal core PCBs (MCPCBs) or high-performance ceramic substrates. Typical values of FR4 thermal conductivity range from 0.25 to 0.4 W/(m·K) in the through-plane direction and 0.6 to 1.0 W/(m·K) in the in-plane direction. In contrast, aluminum-based MCPCBs can have thermal conductivities around 1.0 to 3.0 W/(m·K), and ceramic substrates like aluminum nitride (AlN) can have thermal conductivities up to 180 W/(m·K).
Can the thermal conductivity of FR4 be improved?
Yes, the thermal conductivity of FR4 can be improved through various methods. These include using specialized FR4 laminates with thermally conductive fillers or high-performance resins, incorporating thermal vias to provide low-resistance heat transfer paths, and optimizing the PCB layout to minimize thermal bottlenecks. However, for applications requiring significantly higher thermal conductivity, alternative substrate materials like metal core PCBs or ceramic substrates may be more suitable.
How is the thermal conductivity of FR4 measured?
The thermal conductivity of FR4 can be measured using several techniques, including the guarded hot plate method, laser flash method, heat flow meter method, and transient plane source (TPS) method. Each method has its advantages and limitations, and the choice depends on factors such as sample size, desired accuracy, and available equipment. Standardized test methods, such as ASTM E1530 and ISO 22007-2, provide guidelines for measuring the thermal conductivity of plastics and insulating materials.
Why is understanding FR4 thermal conductivity important for PCB design?
Understanding FR4 thermal conductivity is crucial for PCB design because it directly affects the board’s ability to dissipate heat generated by electronic components. A PCB substrate with high thermal conductivity allows for better heat dissipation, reducing the risk of component failure due to thermal stress. On the other hand, a substrate with low thermal conductivity can lead to heat accumulation, which may cause components to malfunction or fail prematurely. By considering the thermal conductivity of FR4 and implementing appropriate thermal management strategies, designers can ensure the reliable operation and longevity of electronic devices.
Conclusion
FR4 thermal conductivity is a critical property that plays a significant role in the performance and reliability of printed circuit boards. Understanding the typical values, factors affecting, and measurement techniques of FR4 thermal conductivity is essential for designing high-performance electronic devices. While FR4 has relatively low thermal conductivity compared to other PCB materials, various strategies can be employed to enhance its thermal performance, such as using specialized laminates, incorporating thermal vias, and optimizing PCB layout.
As electronic devices continue to push the boundaries of performance and functionality, the importance of effective thermal management in PCB design will only continue to grow. By staying informed about the latest advancements in FR4 technology and thermal management techniques, engineers and designers can create robust and reliable electronic products that meet the ever-increasing demands of the industry.
0 Comments