Introduction to PCB V-Scoring
PCB V-Scoring, also known as V-Grooving, is a process used in the manufacturing of printed circuit boards (PCBs) to create pre-determined breaking points or snap-off sections on the board. This technique allows for easy separation of individual PCBs from a larger panel, simplifying the assembly process and reducing the risk of damage to the circuits during separation.
What is PCB V-Scoring?
V-Scoring is a method of creating a groove or notch on the surface of a PCB panel, typically in a V-shape, which serves as a weak point for controlled breaking. The depth and angle of the V-Score determine the ease with which the PCB can be separated from the panel. This process is often used in conjunction with other PCB fabrication techniques, such as routing and depaneling.
Benefits of PCB V-Scoring
- Efficient PCB separation: V-Scoring allows for quick and clean separation of individual PCBs from a larger panel, reducing the time and effort required for assembly.
- Reduced risk of damage: By creating controlled breaking points, V-Scoring minimizes the risk of damage to the PCB circuits during the separation process.
- Improved accuracy: V-Scoring ensures precise and consistent separation of PCBs, maintaining the integrity of the board’s dimensions and features.
- Cost-effective: Implementing V-Scoring in the PCB manufacturing process can lead to cost savings by reducing the need for additional depaneling equipment and minimizing material waste.
PCB V-Scoring Techniques
There are several techniques used to create V-Scores on PCB panels, each with its own advantages and limitations. The choice of technique depends on factors such as the PCB material, thickness, and desired break-away force.
Mechanical V-Scoring
Mechanical V-Scoring involves using a cutting tool, such as a V-shaped blade, to create a groove on the surface of the PCB panel. This method is suitable for a wide range of PCB materials and thicknesses, and it offers a high degree of precision and consistency.
Advantages of Mechanical V-Scoring
- Versatility: Mechanical V-Scoring can be used on various PCB materials, including FR-4, aluminum, and ceramic substrates.
- Precision: The depth and angle of the V-Score can be precisely controlled, ensuring consistent and accurate PCB separation.
- Speed: Mechanical V-Scoring is a relatively fast process, allowing for efficient production of large quantities of PCBs.
Limitations of Mechanical V-Scoring
- Tool wear: The cutting tools used in mechanical V-Scoring are subject to wear and tear, requiring regular maintenance and replacement.
- Material stress: The mechanical nature of the process can introduce stress on the PCB material, potentially affecting its performance and reliability.
Laser V-Scoring
Laser V-Scoring utilizes a high-powered laser to create a groove on the surface of the PCB panel. This non-contact method offers several advantages over mechanical V-Scoring, particularly in terms of precision and flexibility.
Advantages of Laser V-Scoring
- High precision: Laser V-Scoring allows for extremely precise control over the depth, width, and angle of the V-Score, ensuring consistent and accurate PCB separation.
- Minimal material stress: As a non-contact method, laser V-Scoring introduces minimal stress on the PCB material, reducing the risk of damage or deformation.
- Flexibility: Laser V-Scoring can easily accommodate changes in PCB design or layout, as the laser can be programmed to create V-Scores in any desired pattern or location.
Limitations of Laser V-Scoring
- Cost: Laser V-Scoring equipment can be more expensive than mechanical V-Scoring tools, which may impact the overall cost of PCB production.
- Material compatibility: Some PCB materials, such as those with high reflectivity or low absorption, may be challenging to process using laser V-Scoring.
Designing for PCB V-Scoring
To ensure the successful implementation of V-Scoring in your PCB design, consider the following guidelines:
V-Score Placement
- Avoid placing V-Scores near critical components or traces to minimize the risk of damage during PCB separation.
- Ensure that the V-Score location allows for easy and clean separation of the individual PCBs from the panel.
- Consider the panel layout and optimize the V-Score placement to maximize material utilization and minimize waste.
V-Score Depth and Angle
- The depth of the V-Score should be carefully calculated based on the PCB material and thickness to ensure consistent and controlled breaking.
- The angle of the V-Score can affect the break-away force required for separation. A wider angle may result in a cleaner break, while a narrower angle may require more force.
- Consult with your PCB manufacturer to determine the optimal V-Score depth and angle for your specific application.
Material Considerations
- Choose a PCB material that is compatible with the selected V-Scoring method (mechanical or laser) to ensure optimal results.
- Consider the material’s properties, such as flexibility and brittleness, when designing V-Scores to avoid unintended breakage or damage.
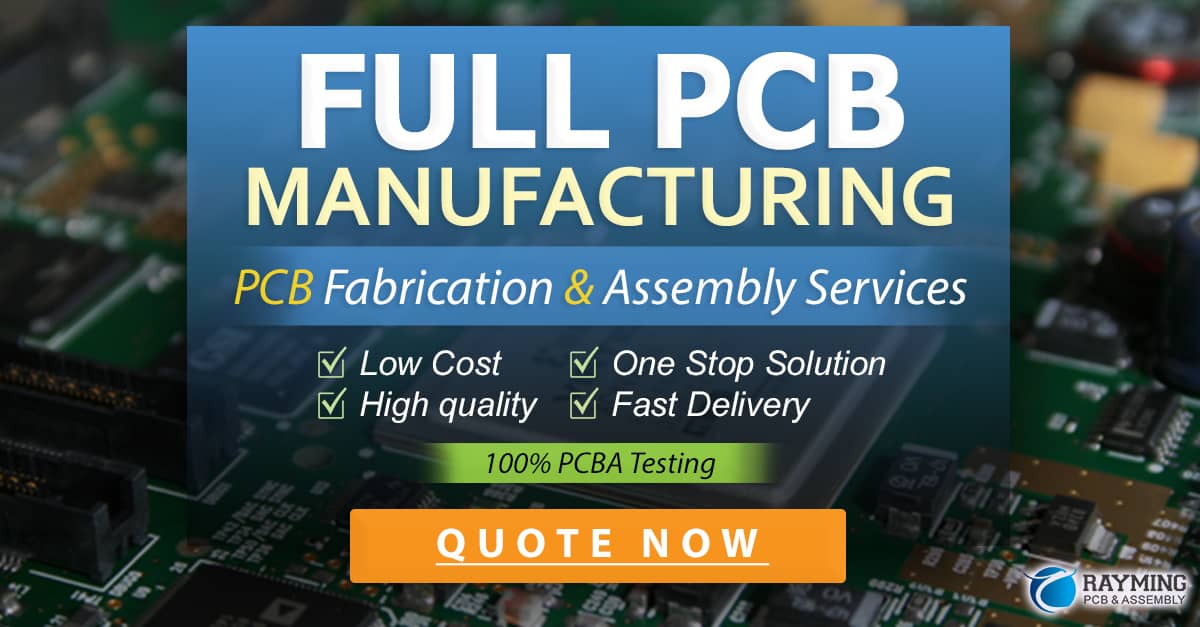
V-Scoring and PCB Assembly
Incorporating V-Scoring into your PCB assembly process can streamline production and improve efficiency. Here are some tips for integrating V-Scoring into your assembly workflow:
Panelization and V-Scoring
- Design your PCB panels with V-Scoring in mind, ensuring that the individual boards can be easily separated after assembly.
- Work with your PCB manufacturer to optimize the panel layout and V-Score placement for your specific assembly requirements.
Depaneling Techniques
- Manual depaneling: For low-volume production or prototyping, individual PCBs can be separated from the panel by hand, using the V-Scores as a guide.
- Automated depaneling: High-volume production can benefit from automated depaneling equipment, which uses the V-Scores to accurately separate the PCBs with minimal manual intervention.
Quality Control
- Inspect the V-Scores prior to assembly to ensure they meet the specified depth, angle, and placement requirements.
- After depaneling, visually inspect the separated PCBs for any signs of damage or stress along the break edges.
- Conduct functional testing on a sample of the separated PCBs to verify that the V-Scoring process has not compromised the circuit’s performance or reliability.
Frequently Asked Questions (FAQ)
-
Q: What is the difference between V-Scoring and routing in PCB fabrication?
A: V-Scoring creates a groove or notch on the surface of the PCB panel to facilitate controlled breaking, while routing involves cutting through the entire thickness of the panel to separate individual PCBs. -
Q: Can V-Scoring be used on multilayer PCBs?
A: Yes, V-Scoring can be used on multilayer PCBs, but the depth and angle of the V-Score must be carefully calculated to ensure proper separation without damaging the internal layers. -
Q: How does the choice of PCB material affect the V-Scoring process?
A: The PCB material’s properties, such as hardness, brittleness, and flexibility, can influence the optimal V-Score depth, angle, and break-away force. Some materials may be more challenging to process using certain V-Scoring methods. -
Q: Is it possible to combine V-Scoring with other depaneling techniques?
A: Yes, V-Scoring can be used in combination with other depaneling techniques, such as routing or perforating, to create more complex PCB panel designs and facilitate efficient separation of individual boards. -
Q: What are the cost implications of implementing V-Scoring in PCB production?
A: The cost impact of V-Scoring depends on factors such as the chosen V-Scoring method (mechanical or laser), the complexity of the PCB design, and the production volume. In general, V-Scoring can lead to cost savings by streamlining the assembly process and reducing material waste.
Conclusion
PCB V-Scoring is a valuable technique in PCB manufacturing that enables efficient and controlled separation of individual boards from a larger panel. By creating pre-determined breaking points, V-Scoring simplifies the assembly process, reduces the risk of damage, and improves overall production efficiency.
When designing for V-Scoring, it is essential to consider factors such as V-Score placement, depth, angle, and material compatibility. Collaborating closely with your PCB manufacturer can help ensure optimal results and seamless integration of V-Scoring into your assembly workflow.
By understanding the principles, techniques, and best practices associated with PCB V-Scoring, you can harness its benefits to enhance your PCB production process, improve product quality, and ultimately, drive business success in the competitive world of electronics manufacturing.
0 Comments