What is a PCB Solder Mask?
A PCB (Printed Circuit Board) solder mask is a thin layer of polymer that is applied to the copper traces of a PCB. The main purpose of the solder mask is to protect the copper traces from oxidation, prevent solder bridges from forming between closely spaced pads, and provide electrical insulation. The solder mask also serves as a barrier to prevent solder from adhering to areas of the PCB where it is not desired during the soldering process.
Types of Solder Masks
There are two main types of solder masks used in PCB manufacturing:
-
Liquid Photoimageable Solder Mask (LPSM): This type of solder mask is applied as a liquid and then exposed to UV light through a photographic film. The exposed areas of the solder mask harden, while the unexposed areas remain liquid and are washed away, leaving the desired solder mask pattern on the PCB.
-
Dry Film Solder Mask (DFSM): This type of solder mask is applied as a dry film and then exposed to UV light through a photographic film. The exposed areas of the solder mask crosslink and become insoluble, while the unexposed areas remain soluble and are washed away, leaving the desired solder mask pattern on the PCB.
Solder Mask Properties
A good solder mask should have the following properties:
- High electrical insulation resistance
- Good adhesion to the PCB surface
- Resistance to solvents and chemicals
- Resistance to high temperatures during soldering
- Smooth and even surface finish
- Good resolution and edge definition
PCB Solder Mask Colors
While the primary function of a solder mask is to protect the copper traces and provide insulation, the color of the solder mask can also serve important purposes in PCB design and manufacturing.
Common Solder Mask Colors
The most common solder mask colors used in PCB manufacturing are:
Color | Pantone Code | RGB Code | Hex Code |
---|---|---|---|
Green | 362 C | 0, 153, 0 | #009900 |
Red | 186 C | 255, 0, 0 | #FF0000 |
Blue | 293 C | 0, 71, 187 | #0047BB |
Black | Black C | 0, 0, 0 | #000000 |
White | White C | 255, 255, 255 | #FFFFFF |
Yellow | 116 C | 255, 211, 0 | #FFD300 |
Choosing a Solder Mask Color
The choice of solder mask color depends on several factors, including:
-
Aesthetic Considerations: The solder mask color can be chosen to match the color scheme of the final product or to provide a visually appealing contrast with the PCB substrate and components.
-
Functional Requirements: Certain solder mask colors may be chosen for their specific properties, such as high contrast for improved inspection or compatibility with optical sensors.
-
Industry Standards: Some industries have established standards for solder mask colors. For example, the automotive industry often uses green solder masks, while the aerospace industry may prefer blue solder masks.
-
Cost and Availability: Some solder mask colors may be more expensive or less readily available than others, which can influence the choice of color for a given PCB design.
Solder Mask Color and PCB Inspection
The choice of solder mask color can have a significant impact on the ease and accuracy of PCB inspection. High-contrast solder mask colors, such as white or yellow, can make it easier to visually inspect the PCB for defects such as solder bridges, open circuits, or misaligned components.
On the other hand, low-contrast solder mask colors, such as green or blue, can make visual inspection more challenging, especially for fine-pitch components or densely populated PCBs. In these cases, automated optical inspection (AOI) systems may be used to detect defects more reliably.
Solder Mask Color and Component Placement
The solder mask color can also affect the accuracy of component placement during PCB Assembly. Light-colored solder masks, such as white or yellow, can provide better contrast for machine vision systems used in automated component placement equipment. This can help to ensure that components are placed accurately and consistently, reducing the risk of assembly defects.
Solder Mask Color and Thermal Management
The choice of solder mask color can also have an impact on the thermal management of the PCB. Dark-colored solder masks, such as black or blue, can absorb more heat from the environment, which can help to dissipate heat from the PCB more effectively. This can be particularly important for high-power or high-density PCBs that generate significant amounts of heat.
On the other hand, light-colored solder masks, such as white or yellow, can reflect more heat from the environment, which can help to keep the PCB cooler in high-temperature environments.
Solder Mask Color and Electromagnetic Interference (EMI)
The solder mask color can also play a role in the electromagnetic compatibility (EMC) of the PCB. Some solder mask colors, such as black or blue, can provide better shielding against electromagnetic interference (EMI) than others. This can be particularly important for PCBs used in sensitive electronic equipment or in environments with high levels of EMI.
Solder Mask Color and PCB Substrate
The choice of solder mask color can also be influenced by the color and material of the PCB substrate. For example, a white solder mask may be preferred for a PCB with a black substrate to provide high contrast and improved visibility. Similarly, a green solder mask may be chosen for a PCB with a clear or translucent substrate to provide a visually appealing appearance.
Solder Mask Color Standards
While there are no universally accepted standards for solder mask colors, some industries and applications have established their own standards or guidelines.
IPC-A-600 Standard
The IPC-A-600 standard, published by the Association Connecting Electronics Industries (IPC), provides guidelines for the acceptability of printed circuit boards. While the standard does not specify particular solder mask colors, it does provide requirements for solder mask coverage, adhesion, and other properties.
Automotive Industry Standards
The automotive industry has established several standards related to PCB manufacturing, including solder mask requirements. For example, the USCAR-2 standard specifies the use of green solder masks for PCBs used in automotive applications.
Aerospace Industry Standards
The aerospace industry has also established standards for PCB manufacturing, including solder mask requirements. For example, the IPC-6012 standard, which is widely used in the aerospace industry, specifies the use of blue solder masks for certain types of PCBs.
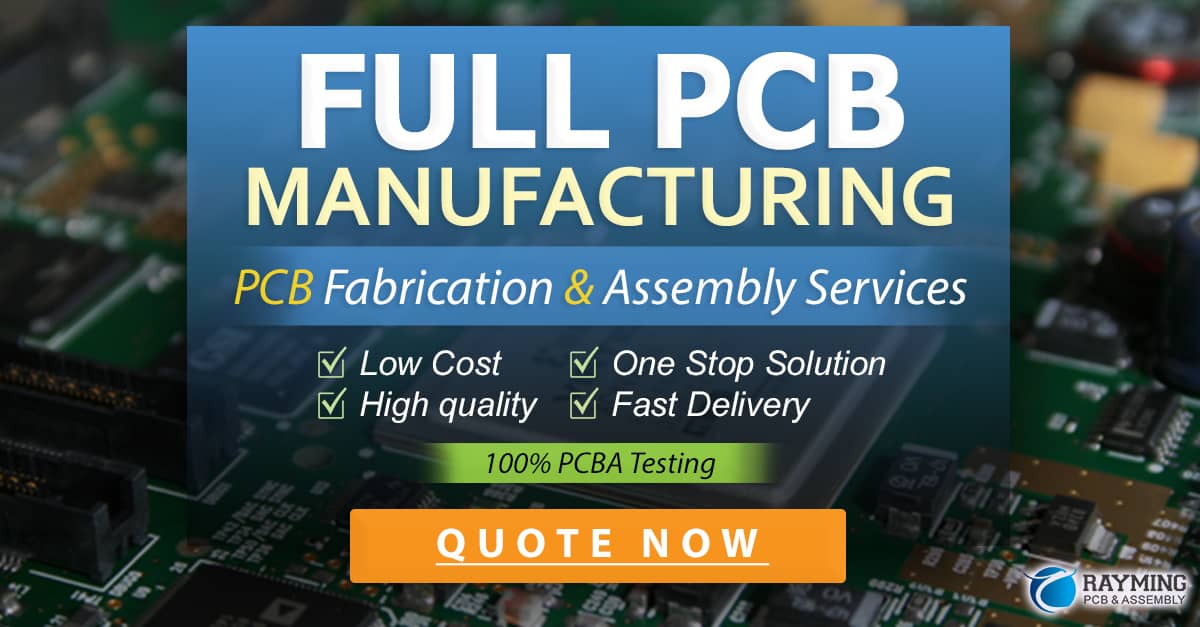
FAQ
-
What is the most common solder mask color?
The most common solder mask color is green, which is widely used in consumer electronics and general-purpose PCBs. -
Can solder mask color affect PCB performance?
While solder mask color does not directly affect PCB performance, it can have an impact on factors such as thermal management, EMI shielding, and inspection accuracy, which can indirectly affect PCB performance. -
Are there any disadvantages to using non-standard solder mask colors?
Non-standard solder mask colors may be more expensive or less readily available than standard colors, which can increase the cost and lead time of PCB manufacturing. Additionally, some automated inspection systems may not be calibrated for non-standard colors, which can affect inspection accuracy. -
Can solder mask color be changed after PCB assembly?
Once the solder mask has been applied and cured, it is not practical to change the color without removing the existing solder mask and reapplying a new layer. This process is time-consuming and can damage the PCB, so it is generally not recommended. -
Are there any environmental concerns with solder mask colors?
Some solder mask formulations may contain hazardous substances, such as lead or volatile organic compounds (VOCs), which can have environmental and health impacts. However, most modern solder masks are RoHS (Restriction of Hazardous Substances) compliant and do not contain these substances. It is important to choose a reputable PCB manufacturer that uses environmentally friendly solder mask formulations.
Conclusion
The choice of solder mask color is an important consideration in PCB design and manufacturing. While the primary function of the solder mask is to protect the copper traces and provide insulation, the color of the solder mask can also serve important purposes, such as improving inspection accuracy, enhancing thermal management, and providing EMI shielding.
When choosing a solder mask color, it is important to consider factors such as aesthetic requirements, functional requirements, industry standards, and cost and availability. By selecting the appropriate solder mask color for a given application, PCB designers and manufacturers can optimize the performance, reliability, and visual appeal of their products.
0 Comments