Introduction
Printed circuit board assembly (PCBA) is a critical process in electronics manufacturing where electronic components are soldered onto a printed circuit board (PCB). The assembled PCB is a vital component of all electronic products including computers, mobile devices, automotive electronics, industrial equipment, and more. Choosing a reliable PCBA services provider is crucial for ensuring high-quality and functional PCB assemblies while minimizing costs and production time. This comprehensive guide covers everything you need to know about PCBA services.
What is PCBA?
PCBA or PCB assembly refers to the process of soldering or assembling electronic components like capacitors, resistors, integrated circuits (ICs), transistors, and other parts onto a PCB. The PCB acts as the foundation to mechanically support and electronically connect components using conductive tracks and pads.
Once the PCB is designed and fabricated, electronic components need to be accurately placed and fixed on the board. This is done by soldering component leads to the pads on the PCB to form an electronic circuit. The fully assembled PCB is tested before being integrated into electronic products.
Stages of PCBA
The PCB assembly process involves the following key stages:
- PCB Fabrication – The bare printed circuit board is fabricated based on the PCB design. Popular fabrication methods include photoengraving, milling, laser direct imaging (LDI), etc.
- Stencil Printing – A stencil with cutouts matching the pads on the PCB is used to apply solder paste precisely on to the board.
- Component Placement – Electronic components are accurately placed on the PCB manually or using automated pick-and-place machines.
- Soldering – The board passes through a reflow oven so the solder paste melts and solders components in place once cooled. Selective soldering may be needed for through-hole parts.
- Inspection and Testing – Assembled boards are visually inspected and tested for shorts, opens, proper placement, alignment, etc.
- Conformal Coating – A protective insulating coating may be applied on the assembled board leaving points of contact exposed.
Benefits of Outsourcing PCBA Services
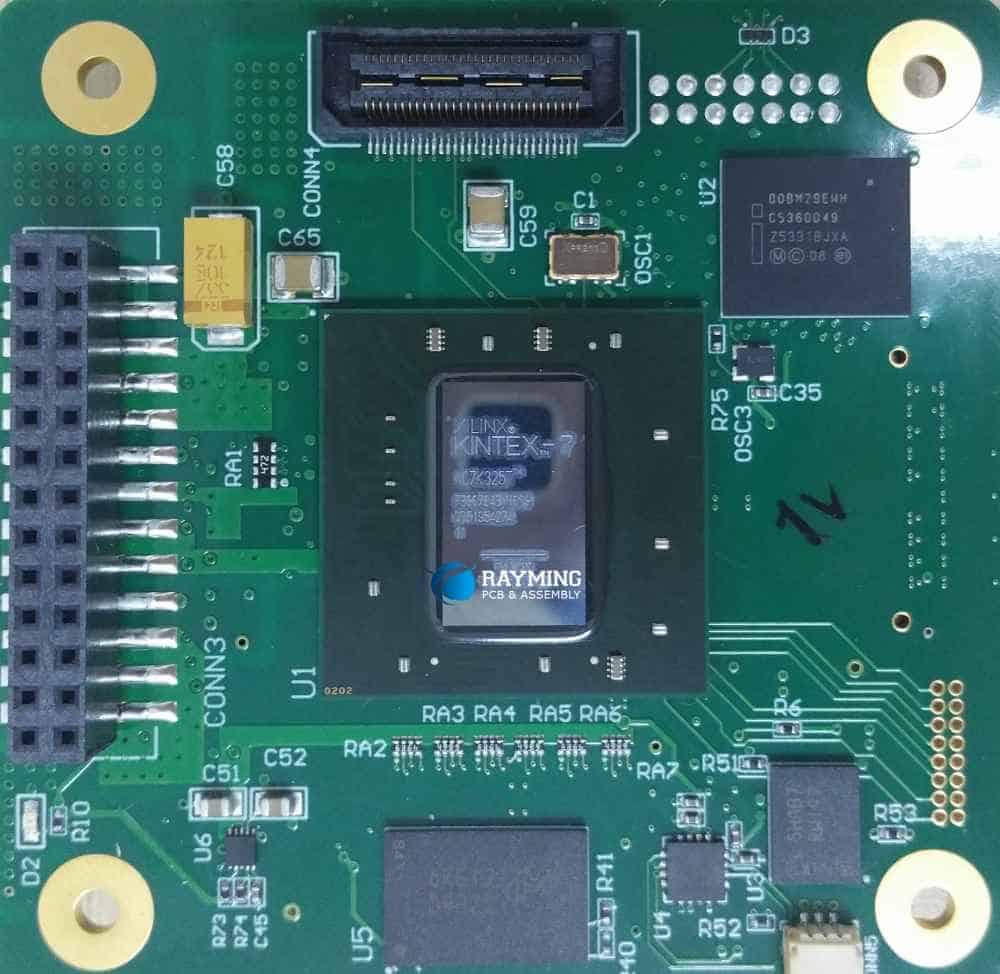
Electronics companies can choose to assemble PCBs in-house or outsource it to a specialized PCBA service provider. Here are some benefits of outsourcing PCBA services:
1. Cost Savings
Outsourcing to an existing PCBA facility allows you to avoid major investments in setting up your own SMT lines, specialized equipment, hiring and training personnel, etc. It leads to significant cost reduction, especially for low and mid-volume production runs.
2. Reduced Time-to-Market
Experienced PCBA service partners have optimized assembly processes enabling faster turnaround times. This accelerates your time-to-market and improves competitiveness.
3. Quality and Reliability
Leading PCBA providers invest in advanced technologies, quality processes, testing methods and employ certified IPC specialists. This results in high-quality assemblies with maximum reliability.
4. Flexible and Scalable Capacity
You can easily scale production up or down as required without capacity constraints. This supports your changing requirements during prototyping, ramp-up and mass production.
5. Supply Chain Management
Your PCBA partner can efficiently procure components and manage suppliers. This minimizes procurement delays especially during component shortages.
6. Regulatory Compliance
Outsourcing to an ISO-certified PCBA company ensures your products meet regulatory standards for electronics manufacturing.
Key Factors in Choosing a PCBA Company
With many options available, selecting the right PCBA partner is crucial for your project’s success. Here are some key factors to consider during PCBA supplier evaluation:
Capabilities and Expertise
- Wide range of assembly capabilities (SMT, through-hole, mixed-technology)
- Experience with your application area (consumer, automotive, industrial, etc.)
- Design for Manufacturing (DFM) expertise to avoid assembly issues
- Ability to work with dense, high-complexity boards
- Experience handling of delicate components like connectors, displays, etc.
Quality and Inspection
- ISO 9001 and IATF 16949 quality certifications
- Comprehensive quality inspection procedures
- AOI and X-ray inspection systems to detect defects
- IPC certifications of assembly personnel
- Reliability testing capabilities
Production Capabilities
- Capacity to handle your production volumes
- Lean manufacturing and optimized production flows
- Automated processes for repeatability and consistency
- Handling of miniaturized components (0201, 01005)
- Mix of low, medium and high volume production lines
Supply Chain and Logistics
- In-house stores management and stocking programs
- Supply chain networks to enable sourcing of long-lead components
- Vendor managed inventory (VMI) programs
- Logistics infrastructure for quick turnarounds
Engineering Support
- Design for Manufacturing (DFM) analysis to avoid assembly issues
- Test development to validate board functionality
- Support for prototyping and new product introduction (NPI)
- Fast response to technical queries and issues
Value Adds
- Programming and testing of firmware and software builds
- Integration of boards into enclosures or other equipment
- Drop-shipments to multiple locations
- IT integration for order and inventory management
Selecting a PCBA company with the right expertise, capabilities and resources is key to realizing the benefits of outsourcing your electronics manufacturing activities.
The PCBA Process Explained Step-by-Step
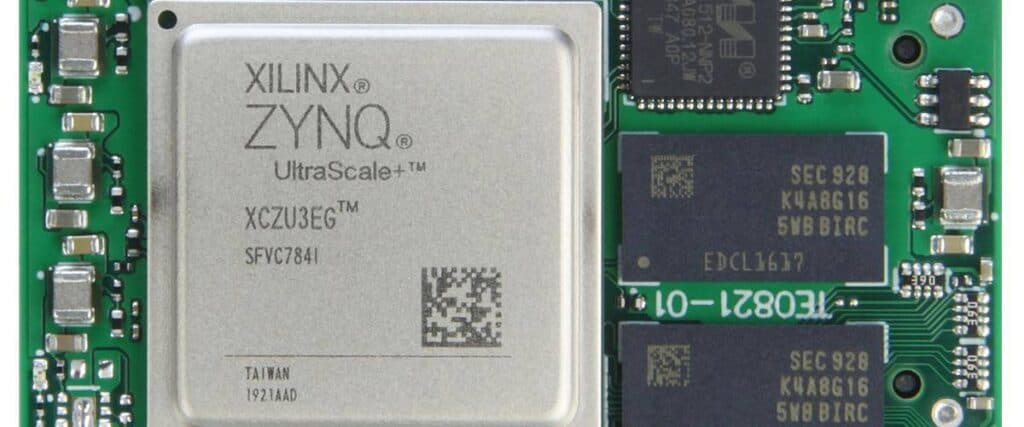
The printed circuit board assembly process involves intricate procedures with little room for errors. Each step must be performed flawlessly to ensure a working board assembly that passes testing. Here is a step-by-step breakdown of the PCBA manufacturing sequence:
1. Solder Paste Printing
The first step is to accurately apply solder paste on PCB pads where components will be placed. This is done using stencil printing where a thin metal stencil with cutouts matching the PCB pad layout is aligned over the board. Solder paste is applied over the stencil, transferred to the PCB, and then the stencil is removed.
2. SMD Placement
Surface mount components are precisely placed on the solder paste deposits on the board using high-speed pick-and-place machines. These automatic component placers use advanced vision systems to position tiny SMD components accurately within a few microns.
3. Reflow Soldering
The PCB boards with SMDs are passed through a reflow oven – a conveyorized oven with different temperature zones. The boards are brought up to soldering temperature to melt the solder paste and attach components firmly. The solder joints are then cooled to solidify the connection.
4. Through Hole Component Insertion
Components with wire leads like connectors or capacitors are inserted into the holes on the PCB manually or using machines. The leads are soldered using techniques like wave soldering or selective soldering to fix them in place.
5. Conformal Coating Application
A protective plastic coating may be applied selectively on the assembled PCB for insulation, moisture resistance and circuit reliability. Contact points are masked before coating.
6. Inspection and Testing
Post-assembly quality checks are conducted like visual inspection to verify proper assembly according to work instructions. Automated optical inspection and x-ray imaging detect defects. Boards undergo testing to validate electrical functionality.
7. Panelization and Breakout
For PCBs assembled in panels, individual boards are now routed, scored and broken out from the panel frame. Edge trimming and bar code labeling are also completed.
8. Final Packaging
Tested boards free from defects are packed and shipped safely to the customer’s facility. Electrostatic shielding, moisture barriers, shock absorption and other techniques may be used to protect sensitive boards.
Every step must be completed with utmost care to achieve a high-quality PCBA without errors or latent defects. The process requires close collaboration between the PCBA company and customer to meet design, quality, and functional requirements.
Key Technological Advancements in PCBA
PCBA is a rapidly evolving field with constant innovations in processes, equipment and software tools to enable more advanced assemblies at lower costs. Some key technological advancements transforming PCBA include:
1. Highly Precise Pick-and-Place Machines
Component placement accuracy and speed have improved tremendously with advanced computer vision. Features like pattern recognition enable reliable placement despite varying component sizes or PCB warpage.
2. Miniaturization
PCB assemblies are achieving greater functionality per unit area with smaller components. PCBA providers require advanced processes and microscopes to place tiny microchips, 01005 passives and microBGAs.
3. Advanced Soldering Techniques
Innovations like vapor phase reflow provide precise thermal control for reliable soldering. Laser assisted soldering focuses heat only on joints being worked on avoiding collateral damage.
4. Additive Manufacturing
3D printing technology allows extremely complex PCB geometries not feasible through conventional fabrication. It enables embedding of electronics inside 3D printed objects.
5. Automated Optical and X-ray Inspection
Automated inspection systems quickly scan assembled PCBs and use algorithms to detect defects like missing components, shorts, misalignments etc.
6. Industry 4.0 Integration
Smart manufacturing systems with IoT, big data analytics and machine learning optimize production planning, improve first pass yield and prevent defects.
7. Test Automation
Software automation and test equipment innovations like flying probe testers accelerate testing of PCB assemblies and eliminate handling errors.
These advancements enable PCBA providers to produce high-density, high-mix, and high-complexity assemblies cost-effectively even in relatively lower volumes.
Qualifications and Certifications for PCBA Services
To ensure your PCBA partner follows rigorous quality standards, you should evaluate their qualifications and certifications during supplier selection. Some of the key PCBA certifications to look for include:
IPC Certifications
IPC is the Association Connecting Electronics Industries and a leading standard development organization for the electronics manufacturing industry. Relevant IPC Certifications include:
- IPC-A-610 – Acceptability standard for PCB assemblies
- IPC J-STD-001 – Requirements for soldered electrical connections
- IPC-7711/7721 – Rework and repair of PCBs
- IPC-A-620 – Acceptability standard for cable and wire harness assemblies
IATF 16949
IATF 16949 is the highest global quality standard for the automotive industry. A PCBA provider certified for this demonstrates rigorous quality management expertise.
ISO 9001
The ISO 9001 Quality Management System certification ensures consistent quality processes and continuous improvement.
Nadcap Accreditation
Nadcap is an electronics industry accreditation program administered by the Performance Review Institute (PRI). It audits and approves companies to meet industry quality standards.
UL Certification
UL (Underwriters Laboratories) certification is an OEM requirement and indicates compliance with product safety standards.
AS9100
AS9100 comprises a set of quality management standards for the aerospace industry. Certification demonstrates capabilities for high-quality and strict traceability.
ITAR Registration
ITAR (International Traffic in Arms) regulations control manufacturing of defense and military products. ITAR registration allows handling related PCBA work.
Choosing an appropriately certified PCBA partner ensures you get defect-free boards assembled robustly to meet quality and reliability needs.
Key PCBA Industry Trends and Emerging Technologies
The printed circuit board assembly industry continues to evolve at a rapid pace. Several emerging trends and new technologies are transforming electronics manufacturing.
1. Growing Use of Automation
Automated assembly lines, test equipment, and inspection systems driven by AI and advanced machine vision are being adopted. This improves repeatability, speed, precision and overall productivity.
2. Miniaturization
PCB assemblies keep getting denser as components become smaller and boards more compact. Microchips below 0201 size and high density interconnects are becoming commonplace.
3. Higher Operating Frequencies
Growing digitalization is driving the need for electronics that operate at higher frequencies up to 5G, 6G, mmWave and beyond. This demands tight tolerances and excellent signal integrity during PCBA.
4. More Flexible and Rigid-Flex PCBs
Flexible PCBs and rigid-flex boards combining standard and flexible materials enable smaller, lighter electronic packages. The assembly process requires specialized flex circuit handling.
5. Higher Levels of Integration
More functionality including wireless chips, sensors, power circuits and embedded passives is being integrated into PCBAs, enabling more compact and capable products.
6. Growth of Additive Technologies
Additive methods like inkjet and aerosol printing are emerging to selectively print solder paste, adhesives or even conductive traces onto PCB substrates.
7. Environmentally Friendly Manufacturing
Sustainable initiatives like lead-free soldering, waste reduction, recycling programs, and renewable energy usage are becoming mainstream.
8. Supply Chain Resilience and Security
Geopolitical issues are prioritizing supply chain visibility, flexibility and resilience along with heightened cybersecurity.
As products get smarter and pack in greater capabilities, PCBA technology will continue advancing to assemble these complex boards reliably, efficiently and economically.
Frequently Asked Questions
Q: What are some common PCBA defects?
Some typical PCBA defects include:
- Missing, wrong or incorrectly oriented components
- Poor solder joint quality – cold joints, insufficient wetting
- Solder balls or solder splashes causing shorts
- Damaged PCB or component pads leading to opens
- Misalignments causing skewed parts or tombstoning
- Board warpage or bending causing stress on joints
- Exposed copper traces causing electrical leakage
- Foreign object debris like metal particles or flux residue
- Cracked or damaged component packages or leads
Q: How is PCBA quality inspected?
PCBA quality inspection involves:
- Visual inspection under microscopes by trained technicians
- Automated optical inspection (AOI) using cameras to detect defects
- X-ray inspection to identify shorts, opens, hidden flaws
- Flying probe testing for electrical parameter checks
- In-circuit testing (ICT) to validate board functionality
- Boundary scan testing for digital components
- Reliability testing like thermal cycling, drop/shock, vibration, etc.
Q: What qualifications should PCBA engineers have?
PCBA process engineers should have:
- Formal qualifications in electronics engineering or technology
- Certifications like IPC 610, J-STD-001, 7711/7721 demonstrating soldering and inspection expertise
- Several years of hands-on PCBA experience with traceable training history
- Extensive knowledge of assembly methods like SMT, through-hole, press-fit technologies
- Understanding of PCB design, fabrication, component technology, and solder materials
- Meticulous approach and precision skills to handle miniature components
- Training in ESD control procedures and safe handling of electronics
Q: How can you ensure counterfeit components are not used?
Strategies to prevent counterfeit components:
- Procure directly from authorized distributors or component manufacturers
- Perform testing and inspection of incoming parts to identify fakes
- Track components to their supply chain origin and audit suspicious vendors
- Use security features like holograms and RFID tags on reels from approved suppliers
- Destroy or quarantine used components to prevent re-entry into supply chain
- Report suspected counterfeits to industry organizations like ERAI or GQA
- Block high-risk supply chains and geographies prone to counterfeiting
Q: What are some key considerations for PCBA process validation?
Validating the PCBA process involves:
- Documented procedures for each step compliant with IPC standards
- Operator training on procedures and pass/fail criteria
- First Article Inspections (FAIs) to prove out processes
- Statistical process control limits and monitoring
- Verification of test coverage and fault isolation
- Control of material, process, and test equipment changes
- Regular internal process audits and reviews
- Ongoing continuous improvement and optimization
Following these industry best practices ensures a robust, reliable, and repeatable PCBA process.
Q: How can PCBA production times be reduced?
Ways to reduce PCBA cycle times:
- Optimize production planning, kitting and material flows to eliminate wait times
- Use automatic optical inspection to reduce manual inspection steps
- Employ concurrent operations like simultaneous solder printing on multiple boards
- Adopt automated assembly and testing equipment to minimize manual operations
- Ensure sufficient capacity so work-in-progress does not get stuck waiting between steps
- Improve first pass yield to avoid time spent on rework and repairs
- Enable information sharing between teams to proactively address issues
- Analyze processes to identify and eliminate bottlenecks causing delays
- Implement Lean, Six Sigma and Just-in-Time methodologies
A holistic focus across planning, resources, automation, quality and continuous improvement drives faster PCBA turnarounds.
Conclusion
As electronics products continue getting more advanced and incorporating the latest technologies, the role of high-quality PCBA services is becoming even more crucial. Partnering with an expert PCBA solutions provider enables OEMs to realize the many benefits of outsourcing discussed in this guide. By selecting a partner with the right capabilities, certifications, and commitment to engineering excellence, electronics companies can achieve shorter time-to-market, lower costs, superior quality, and unmatched product reliability through professional PCBA services.
0 Comments