Introduction to Peelable Solder Mask
Peelable solder mask, also known as temporary solder mask or removable solder mask, is a specialized coating applied to printed circuit boards (PCBs) to protect specific areas during the soldering process. Unlike permanent solder masks, which are designed to remain on the PCB throughout its lifetime, peelable solder masks are intended to be removed after soldering is complete. This unique property makes peelable solder masks a valuable tool in various PCB manufacturing and assembly processes.
Key Features of Peelable Solder Mask
- Temporary protection: Peelable solder masks provide temporary protection to selected areas of the PCB during soldering.
- Easy removal: After soldering, the peelable solder mask can be easily removed without damaging the PCB or its components.
- Selective application: Peelable solder masks can be applied to specific areas of the PCB, allowing for targeted protection.
Benefits of Using Peelable Solder Mask
1. Protecting Sensitive Components
One of the primary benefits of using peelable solder mask is its ability to protect sensitive components during the soldering process. Some electronic components, such as connectors, switches, and certain types of integrated circuits, can be damaged by the high temperatures and molten solder used in the soldering process. By applying a peelable solder mask to these components, manufacturers can ensure that they remain protected throughout the soldering process.
2. Facilitating Selective Soldering
Peelable solder masks also facilitate selective soldering, a process in which specific areas of the PCB are soldered while others are left unsoldered. This is particularly useful in situations where certain components need to be soldered separately or when different soldering techniques are required for different parts of the PCB. By applying a peelable solder mask to the areas that should not be soldered, manufacturers can ensure that the soldering process is limited to the desired areas.
3. Improving Solder Joint Quality
The use of peelable solder masks can also improve the quality of solder joints. By preventing solder from spreading to unintended areas, peelable solder masks help to ensure that solder joints are formed correctly and with the appropriate amount of solder. This can lead to stronger, more reliable solder connections and improved overall PCB performance.
4. Reducing Rework and Repair
Peelable solder masks can help to reduce the need for rework and repair in PCB manufacturing. By protecting sensitive components and facilitating selective soldering, peelable solder masks minimize the risk of damage and defects during the soldering process. This, in turn, reduces the need for costly and time-consuming rework and repair operations.
Types of Peelable Solder Mask
There are several types of peelable solder mask available, each with its own unique properties and applications. Some of the most common types include:
1. Latex-Based Peelable Solder Mask
Latex-based peelable solder masks are among the most widely used types. These masks are typically applied by dipping or spraying and cure at room temperature. Latex-based masks are known for their ease of application and removal, as well as their compatibility with a wide range of PCB materials and components.
2. Silicone-Based Peelable Solder Mask
Silicone-based peelable solder masks offer excellent high-temperature resistance and are well-suited for use in high-temperature soldering processes. These masks are typically applied by brushing or dispensing and cure at elevated temperatures. Silicone-based masks are known for their durability and resistance to harsh environmental conditions.
3. UV-Curable Peelable Solder Mask
UV-curable peelable solder masks are designed to cure quickly when exposed to ultraviolet (UV) light. These masks offer fast processing times and can be applied using various methods, including screen printing and spray coating. UV-curable masks are known for their precision and ability to produce high-resolution patterns.
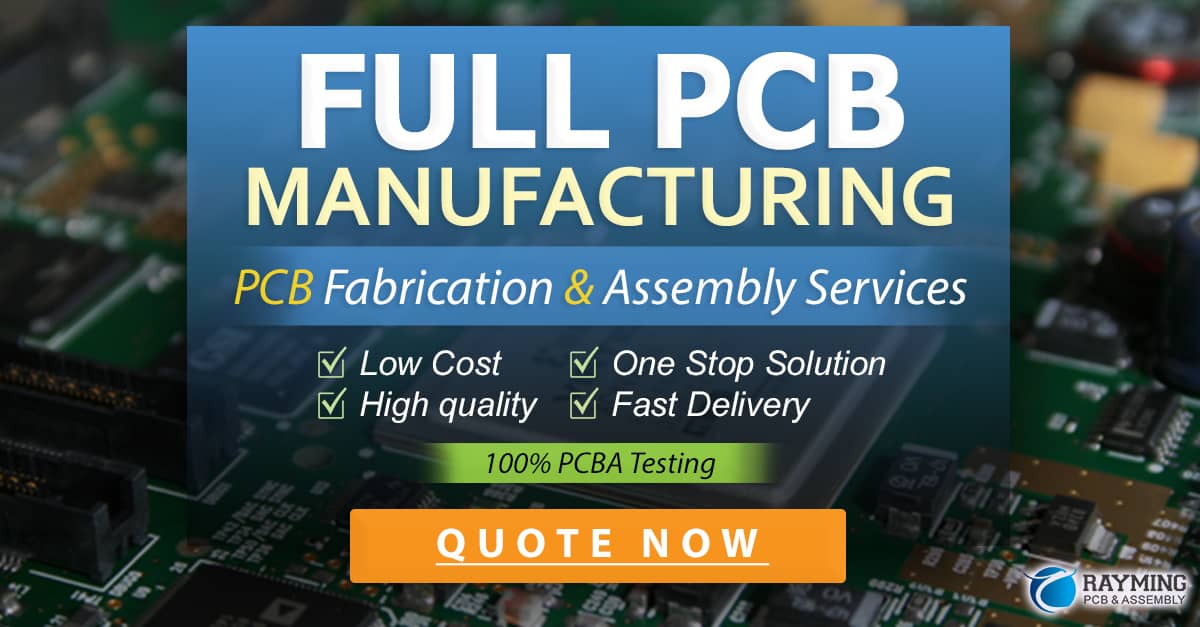
Applying Peelable Solder Mask
The process of applying peelable solder mask involves several steps, which may vary depending on the specific type of mask and the application method used. Generally, the process involves the following steps:
- Surface preparation: The PCB surface is cleaned and prepared to ensure proper adhesion of the peelable solder mask.
- Mask application: The peelable solder mask is applied to the desired areas of the PCB using a suitable application method, such as dipping, spraying, brushing, or screen printing.
- Curing: The applied mask is cured according to the manufacturer’s specifications. This may involve allowing the mask to cure at room temperature, exposing it to elevated temperatures, or subjecting it to UV light.
- Inspection: The cured mask is inspected to ensure proper coverage and adhesion.
Peelable Solder Mask Application Methods
Application Method | Description | Advantages | Disadvantages |
---|---|---|---|
Dipping | The PCB is dipped into a tank containing the peelable solder mask. | Fast and simple, suitable for large volumes. | Limited control over mask thickness and coverage. |
Spraying | The peelable solder mask is sprayed onto the PCB using a spray gun or automated spraying equipment. | Good control over mask thickness and coverage, suitable for complex geometries. | Requires specialized equipment and skilled operators. |
Brushing | The peelable solder mask is applied using a brush or other manual applicator. | Simple and low-cost, suitable for small-scale applications. | Time-consuming and labor-intensive, limited control over mask thickness and coverage. |
Screen Printing | The peelable solder mask is applied using a screen printing process, allowing for precise patterning. | High-resolution patterning, suitable for selective masking. | Requires specialized equipment and screens, limited to flat surfaces. |
Removing Peelable Solder Mask
After the soldering process is complete, the peelable solder mask must be removed from the PCB. The removal process typically involves the following steps:
- Peeling: The cured peelable solder mask is carefully peeled away from the PCB surface. This is usually done manually, using tweezers or other suitable tools.
- Cleaning: Any residual mask material is cleaned from the PCB surface using a suitable solvent or cleaning agent.
- Inspection: The PCB is inspected to ensure complete removal of the peelable solder mask and to check for any damage or defects.
It is important to follow the manufacturer’s guidelines for removing the peelable solder mask to avoid damaging the PCB or its components. Some masks may require the use of specific solvents or cleaning agents to ensure complete removal.
Choosing the Right Peelable Solder Mask
When selecting a peelable solder mask for a particular application, several factors should be considered:
- Compatibility: The peelable solder mask must be compatible with the PCB materials, components, and soldering processes used.
- Temperature resistance: The mask should be able to withstand the temperatures encountered during the soldering process without degrading or losing its protective properties.
- Ease of application and removal: The mask should be easy to apply and remove without damaging the PCB or its components.
- Thickness and coverage: The mask should provide the desired thickness and coverage to ensure adequate protection of the targeted areas.
- Curing requirements: The curing process for the mask should be compatible with the manufacturing workflow and equipment available.
- Cost: The cost of the peelable solder mask should be considered in relation to the overall manufacturing budget and the benefits it provides.
Frequently Asked Questions (FAQ)
1. Can peelable solder masks be reused?
No, peelable solder masks are designed for single use only. Once removed from the PCB, they should be discarded and replaced with a new mask for subsequent soldering operations.
2. How long does it take for a peelable solder mask to cure?
The curing time for a peelable solder mask depends on the specific type of mask and the curing method used. Some masks, such as latex-based masks, may cure at room temperature within a few hours, while others, such as silicone-based masks, may require elevated temperatures and longer curing times.
3. Can peelable solder masks be used on flexible PCBs?
Yes, peelable solder masks can be used on flexible PCBs, provided that the mask material is compatible with the flexible substrate and can withstand the flexing and bending encountered during the manufacturing process.
4. Are there any environmental concerns associated with using peelable solder masks?
Some peelable solder masks may contain solvents or other chemicals that can have environmental impacts if not handled and disposed of properly. It is important to follow the manufacturer’s guidelines and local regulations for the safe use and disposal of peelable solder masks.
5. Can peelable solder masks be used in conjunction with other types of solder masks?
Yes, peelable solder masks can be used in conjunction with other types of solder masks, such as permanent solder masks, in certain applications. For example, a permanent solder mask may be used to protect the majority of the PCB, while a peelable solder mask is used to selectively protect specific areas during the soldering process.
Conclusion
Peelable solder masks are a valuable tool in PCB manufacturing and assembly, offering temporary protection for sensitive components, facilitating selective soldering, improving solder joint quality, and reducing the need for rework and repair. By understanding the different types of peelable solder masks available, their application and removal processes, and the factors to consider when choosing a mask, manufacturers can effectively incorporate peelable solder masks into their PCB production workflows to enhance the quality and reliability of their products.
As PCB designs continue to become more complex and miniaturized, the use of peelable solder masks is likely to remain an important aspect of PCB manufacturing. By staying informed about the latest developments in peelable solder mask technology and best practices for their use, manufacturers can ensure that they are well-positioned to meet the evolving demands of the electronics industry.
0 Comments