What Causes PCB Measling?
Several factors can contribute to the development of PCB measling:
Moisture Absorption
One of the primary causes of PCB measling is moisture absorption. When the PCB is exposed to high humidity levels or comes into contact with moisture during the manufacturing process or in its operating environment, the laminate material can absorb the moisture. This absorption can cause the laminate to swell and create stress on the copper foil, leading to the formation of measles-like defects.
Thermal Stress
Thermal stress is another common cause of PCB measling. During the manufacturing process, PCBs are subjected to various heating and cooling cycles, such as soldering and reflow. If the PCB is not designed to withstand these temperature fluctuations or if the manufacturing process is not properly controlled, thermal stress can cause the laminate to expand and contract, resulting in measling.
Mechanical Stress
Mechanical stress, such as bending or twisting of the PCB, can also contribute to the formation of measles. This stress can occur during handling, assembly, or even during the PCB’s operation in its final application. Excessive mechanical stress can cause the copper foil to separate from the laminate, creating measles-like defects.
Laminate Quality
The quality of the laminate material used in the PCB can also play a role in the development of measling. Lower-quality laminates may be more susceptible to moisture absorption, thermal stress, and mechanical stress, increasing the likelihood of measling occurring.
Detecting PCB Measling
Detecting PCB measling is crucial for ensuring the quality and reliability of the final product. Several methods can be used to identify measling defects:
Visual Inspection
Visual inspection is the most basic method for detecting PCB measling. This process involves examining the surface of the PCB under proper lighting conditions, looking for the characteristic circular defects. However, visual inspection may not be sufficient for detecting smaller or less prominent measles.
Microscopic Examination
For more detailed analysis, microscopic examination can be employed. Using a microscope, engineers can closely inspect the surface of the PCB and identify measling defects that may not be visible to the naked eye. This method allows for a more accurate assessment of the extent and severity of the measling.
Automatic Optical Inspection (AOI)
Automatic Optical Inspection (AOI) systems can be used to detect PCB measling in a more efficient and consistent manner. These systems use high-resolution cameras and advanced image processing algorithms to scan the surface of the PCB and identify any measling defects. AOI systems can quickly inspect large numbers of PCBs and provide detailed reports on the location and severity of the measles.
X-Ray Inspection
In some cases, X-ray inspection may be used to detect measling defects that are not visible on the surface of the PCB. This method allows for the examination of the internal structure of the PCB, revealing any separation between the copper foil and the laminate caused by measling.
Preventing PCB Measling
Preventing PCB measling is essential for maintaining the quality and reliability of the final product. Several strategies can be employed to minimize the risk of measling:
Moisture Control
Proper moisture control during the manufacturing process and in the PCB’s operating environment is crucial for preventing measling. This can be achieved by:
- Storing PCBs and materials in a controlled environment with low humidity
- Using moisture-resistant packaging for PCBs during transportation and storage
- Employing baking processes to remove moisture from PCBs before assembly
Relative Humidity | Recommended Baking Time (hours) |
---|---|
< 30% | No baking required |
30% – 60% | 4 – 6 hours |
> 60% | 8 – 12 hours |
Thermal Management
Effective thermal management can help prevent PCB measling caused by thermal stress. This can be achieved through:
- Proper PCB design, considering the thermal expansion coefficients of the materials used
- Controlled heating and cooling rates during manufacturing processes
- Use of thermal relief patterns in the PCB layout to minimize stress concentration
Mechanical Stress Reduction
Reducing mechanical stress on the PCB can help prevent measling. This can be accomplished by:
- Careful handling and assembly of PCBs
- Use of support structures or stiffeners to minimize bending and twisting
- Proper design of the PCB and its enclosure to minimize mechanical stress during operation
Material Selection
Selecting high-quality laminate materials that are less susceptible to moisture absorption and thermal stress can help prevent PCB measling. When choosing laminate materials, consider:
- Glass transition temperature (Tg)
- Coefficient of thermal expansion (CTE)
- Moisture absorption rate
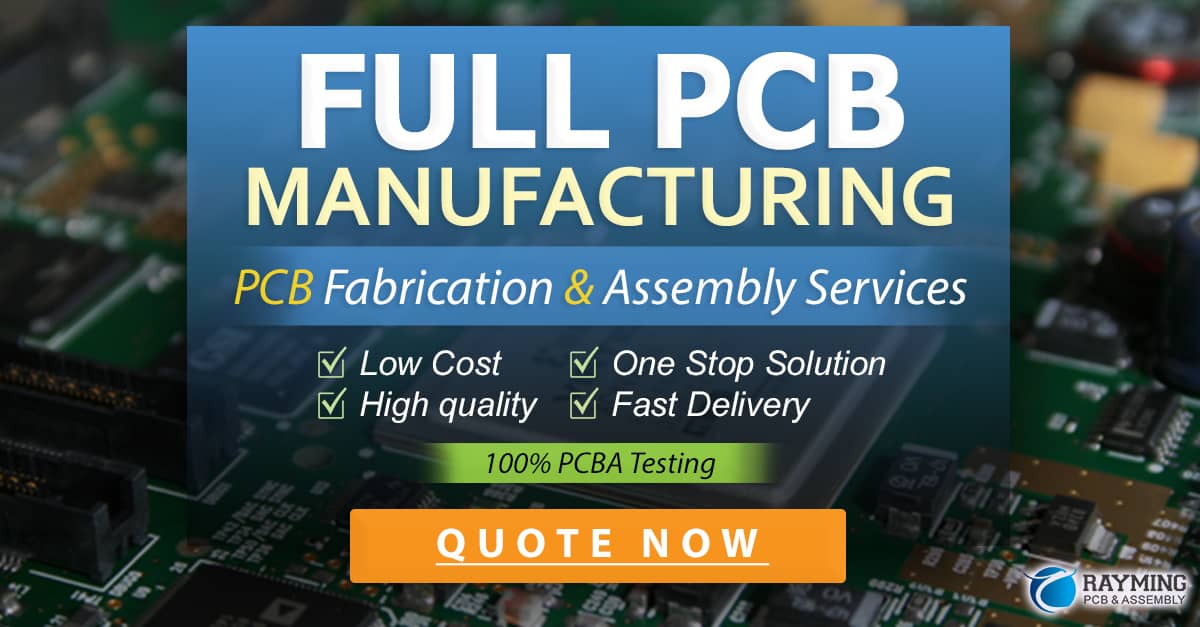
Solving PCB Measling Issues
If PCB measling is detected, several steps can be taken to address the issue:
Rework and Repair
In some cases, measling defects can be reworked or repaired. This may involve:
- Removing the affected area of the PCB and replacing it with new material
- Using conductive epoxy or other fillers to bridge the gaps caused by measling
- Applying conformal coatings to protect the repaired area from further damage
Design Modifications
If measling is found to be a recurring issue, it may be necessary to modify the PCB design to address the root causes. This can include:
- Changing the laminate material to one with better moisture resistance and thermal stability
- Modifying the PCB layout to reduce stress concentration and improve thermal management
- Adding support structures or stiffeners to minimize mechanical stress
Process Improvements
Improving the manufacturing process can also help solve PCB measling issues. This may involve:
- Optimizing the heating and cooling rates during soldering and reflow
- Implementing stricter moisture control measures
- Enhancing quality control procedures to detect and address measling issues early in the manufacturing process
Frequently Asked Questions (FAQ)
1. Can PCB measling be detected by automated inspection systems?
Yes, Automatic Optical Inspection (AOI) systems can be used to detect PCB measling efficiently and consistently. These systems use high-resolution cameras and advanced image processing algorithms to identify measling defects on the surface of the PCB.
2. How can moisture absorption be prevented during PCB storage and transportation?
Moisture absorption can be prevented by storing PCBs in a controlled environment with low humidity and using moisture-resistant packaging during transportation. Additionally, baking processes can be employed to remove moisture from PCBs before assembly.
3. What is the role of laminate material selection in preventing PCB measling?
Selecting high-quality laminate materials with better moisture resistance, thermal stability, and mechanical properties can help prevent PCB measling. When choosing laminate materials, factors such as glass transition temperature (Tg), coefficient of thermal expansion (CTE), and moisture absorption rate should be considered.
4. Can PCB measling be repaired, or is replacement necessary?
In some cases, PCB measling can be repaired through rework processes, such as removing the affected area and replacing it with new material or using conductive epoxy to bridge the gaps caused by measling. However, if the measling is extensive or if the PCB is critical to the application’s reliability, replacement may be necessary.
5. How can thermal stress be minimized during the PCB manufacturing process?
Thermal stress can be minimized by properly designing the PCB, considering the thermal expansion coefficients of the materials used, and controlling the heating and cooling rates during manufacturing processes. The use of thermal relief patterns in the PCB layout can also help minimize stress concentration.
Conclusion
PCB measling is a serious issue that can affect the reliability and performance of printed circuit boards. By understanding the causes, detection methods, prevention strategies, and solutions for PCB measling, engineers and manufacturers can take proactive steps to ensure the quality and longevity of their products. Implementing proper moisture control, thermal management, mechanical stress reduction, and material selection can help prevent measling from occurring. If measling is detected, rework, repair, design modifications, and process improvements can be employed to address the issue. By staying vigilant and proactively addressing PCB measling, manufacturers can deliver high-quality, reliable products to their customers.
0 Comments