What are Double Sided PCBs?
Double sided PCBs, also known as two-layer PCBs, have conductive copper layers on both sides of the insulating substrate material. The two copper layers are interconnected using plated through-holes (vias). Double sided PCBs offer several advantages over single sided PCBs:
- Higher component density
- More compact designs
- Improved electrical performance
- Better heat dissipation
- Reduced electromagnetic interference (EMI)
PCB Manufacturing Process
The manufacturing process for double sided PCBs typically involves the following steps:
-
PCB Design: The PCB layout is designed using specialized software, following the schematic diagram and component specifications.
-
Film Generation: The PCB design is used to generate photographic films or artwork for each layer of the PCB.
-
Copper Clad Laminate: The insulating substrate material, typically FR-4 glass epoxy, is laminated with copper foil on both sides.
-
Drilling: Holes are drilled through the PCB for mounting components and creating vias.
-
Plating: The drilled holes are plated with copper to create electrical connections between the layers.
-
Patterning: The copper layers are patterned using photolithography and etching processes to create the desired conductive traces and pads.
-
Solder Mask Application: A protective solder mask layer is applied to the PCB, leaving only the exposed pads for soldering.
-
Silkscreen: Text and symbols are printed on the PCB surface for component identification and assembly instructions.
-
Surface Finish: The exposed copper pads are coated with a surface finish, such as HASL, ENIG, or OSP, to prevent oxidation and enhance solderability.
-
Electrical Testing: The manufactured PCBs undergo electrical testing to ensure proper functionality and adherence to specifications.
Choosing a PCB Manufacturer
When selecting a PCB manufacturer, consider the following factors:
-
Manufacturing Capabilities: Ensure the manufacturer can handle your specific PCB requirements, such as layer count, material, thickness, and surface finish.
-
Quality Standards: Look for manufacturers with internationally recognized quality certifications, such as ISO 9001, IATF 16949, or IPC standards.
-
Lead Time: Consider the manufacturer’s lead time for prototyping and production to ensure timely delivery of your PCBs.
-
Cost: Compare pricing from multiple manufacturers, considering both unit cost and setup fees for your specific order quantity.
-
Customer Support: Evaluate the manufacturer’s responsiveness, technical support, and communication throughout the manufacturing process.
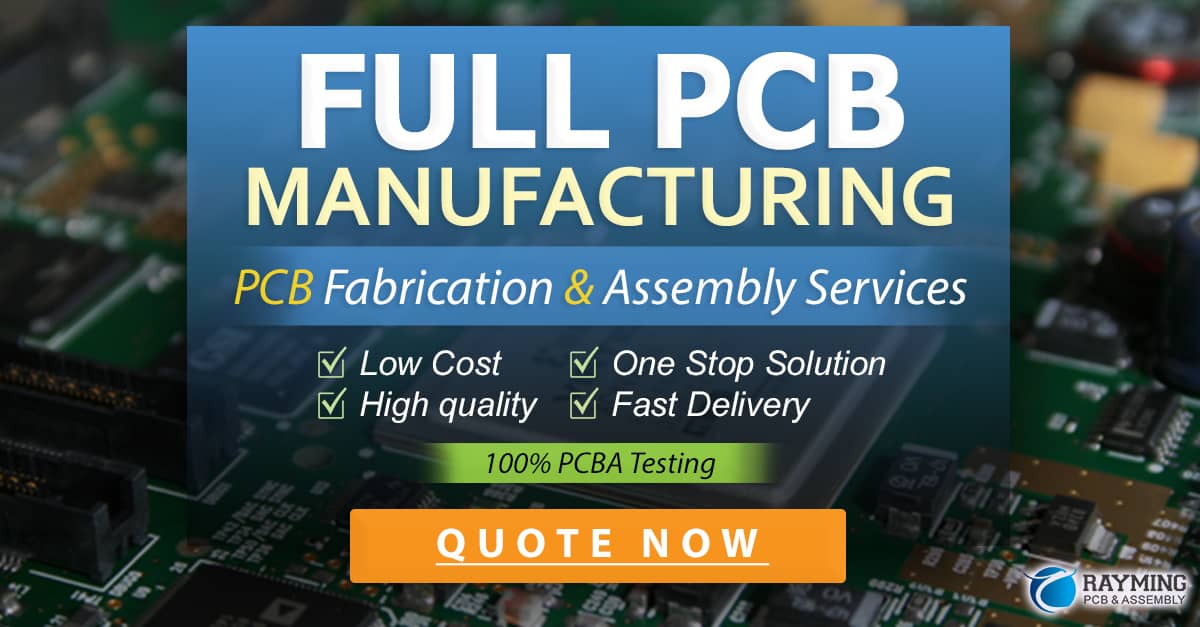
Top PCB Manufacturers
Here are some of the leading PCB manufacturers known for their high-quality double sided PCBs:
Manufacturer | Location | Specialties |
---|---|---|
Kinwong | China | High-volume production, automotive, consumer electronics |
TTM Technologies | USA | Aerospace, defense, automotive, medical |
Unimicron | Taiwan | HDI, flexible PCBs, IC substrates |
Zhen Ding Tech | Taiwan | Consumer electronics, automotive, server/networking |
Shennan Circuits | China | Communication, consumer electronics, industrial |
These manufacturers have established reputations for delivering high-quality PCBs and have a global presence, serving customers in various industries.
Design Considerations for Double Sided PCBs
When designing double sided PCBs, keep the following considerations in mind:
-
Component Placement: Optimize component placement to minimize the need for vias and reduce the overall PCB size.
-
Trace Width and Spacing: Determine appropriate trace widths and spacing based on the electrical requirements and PCB manufacturing capabilities.
-
Via Size and Placement: Select appropriate via sizes and strategically place them to ensure reliable interconnections between layers.
-
Impedance Control: Consider impedance control requirements for high-speed designs to maintain signal integrity.
-
Thermal Management: Incorporate thermal relief pads and copper pours to dissipate heat generated by components.
-
EMI Reduction: Employ techniques such as ground planes, shielding, and proper routing to minimize electromagnetic interference.
Assembly Considerations
Double sided PCBs require careful assembly to ensure proper component placement and soldering. Consider the following:
-
Component Orientation: Ensure components are oriented correctly on both sides of the PCB to avoid assembly errors.
-
Soldering Techniques: Use appropriate soldering techniques, such as reflow soldering or wave soldering, based on the component types and PCB design.
-
Inspection: Perform visual inspection and automated optical inspection (AOI) to detect any assembly defects or component misalignments.
-
Rework and Repair: Establish procedures for rework and repair of assembled PCBs to address any issues identified during inspection or testing.
Testing and Quality Control
Rigorous testing and quality control measures are essential to ensure the reliability and performance of double sided PCBs. Common testing methods include:
-
Flying Probe Testing: Automated flying probe testers check for open circuits, short circuits, and component values.
-
In-Circuit Testing (ICT): ICT fixtures verify the functionality of individual components and the overall PCB assembly.
-
Functional Testing: Custom functional test setups validate the PCB’s performance under real-world operating conditions.
-
Boundary Scan Testing: Boundary scan testing, using JTAG or other interfaces, checks for interconnect and component failures.
-
Environmental Testing: PCBs may undergo environmental tests, such as thermal cycling, vibration, or humidity exposure, to assess their durability.
Future Trends in PCB Manufacturing
The PCB manufacturing industry is constantly evolving to meet the demands of advancing electronics technology. Some notable trends include:
-
Miniaturization: The trend towards smaller, more compact electronic devices drives the need for higher-density PCBs with finer pitch components.
-
High-Speed Designs: As data rates continue to increase, PCB manufacturers are developing advanced materials and processes to support high-speed designs.
-
Flexible and Rigid-Flex PCBs: Flexible and rigid-flex PCBs are gaining popularity for applications that require flexibility, durability, and space savings.
-
Embedded Components: Embedding passive components within the PCB substrate is becoming more common to save space and improve performance.
-
Additive Manufacturing: 3D printing technologies are being explored for PCB fabrication, enabling rapid prototyping and customization.
FAQ
-
What is the typical lead time for double sided PCB manufacturing?
The lead time for double sided PCB manufacturing varies depending on the manufacturer and the specific requirements of the PCB. Prototype quantities may have lead times of a few days to a week, while production quantities can range from a few weeks to several months. -
How much does it cost to manufacture a double sided PCB?
The cost of manufacturing a double sided PCB depends on factors such as the PCB size, layer count, quantity, and surface finish. Small prototype quantities can cost a few hundred dollars, while large production runs can benefit from economies of scale. It’s best to request quotes from multiple manufacturers for your specific PCB design and quantity. -
What are the common PCB surface finishes?
Common PCB surface finishes include: - HASL (Hot Air Solder Leveling): A tin-lead alloy is applied to the exposed copper pads.
- ENIG (Electroless Nickel Immersion Gold): A layer of nickel is plated onto the copper, followed by a thin layer of gold.
- OSP (Organic Solderability Preservative): A protective organic coating is applied to the copper pads.
-
Immersion Silver: A thin layer of silver is chemically deposited onto the copper pads.
-
What is the minimum feature size for double sided PCBs?
The minimum feature size for double sided PCBs depends on the manufacturing capabilities of the PCB fabricator. Typical minimum feature sizes range from 3 to 6 mils (0.075 to 0.15 mm) for trace width and spacing. However, some advanced manufacturers can achieve finer feature sizes for high-density designs. -
Can double sided PCBs be manufactured with impedance control?
Yes, double sided PCBs can be manufactured with impedance control. Impedance control is essential for high-speed designs to maintain signal integrity. PCB manufacturers can adjust the trace width, spacing, and dielectric thickness to achieve the desired impedance values. However, impedance-controlled PCBs may have higher manufacturing costs and longer lead times.
Conclusion
Double sided PCBs are a fundamental component of modern electronics, offering enhanced functionality and packaging density compared to single sided PCBs. Choosing the right PCB manufacturer is crucial to ensure the quality, reliability, and cost-effectiveness of your PCBs. By understanding the manufacturing process, design considerations, assembly techniques, and testing methods, you can make informed decisions when selecting a PCB manufacturer and optimizing your PCB designs.
As technology advances, the PCB manufacturing industry continues to evolve, with trends towards miniaturization, high-speed designs, flexible and rigid-flex PCBs, embedded components, and additive manufacturing. Staying up-to-date with these trends and collaborating with experienced PCB manufacturers will help you leverage the latest technologies and techniques for your PCB projects.
By partnering with reputable PCB manufacturers and following best practices in PCB design and manufacturing, you can ensure the success of your electronic products and stay competitive in today’s rapidly evolving market.
0 Comments