Understanding Solder Balls
Before we dive into the steps to avoid solder balls, let’s first understand what they are and how they form.
What are Solder Balls?
Solder balls are small, spherical particles of solder that can form on the surface of a printed circuit board (PCB) or component during the SMT assembly process. They are typically less than 100 microns in diameter and can be difficult to detect with the naked eye.
How Do Solder Balls Form?
Solder balls can form due to several reasons, including:
- Excessive solder paste deposition
- Incorrect reflow profile
- Contamination of the PCB or components
- Improper handling or storage of materials
- Incompatible solder paste and flux chemistries
Step 1: Choose the Right Solder Paste
Selecting the appropriate solder paste is crucial in Avoiding solder balls. Look for a solder paste with the following characteristics:
- Compatible with your PCB surface finish and component metallization
- Appropriate particle size distribution for your stencil aperture dimensions
- Suitable viscosity and rheology for your printing process
- Low tendency to slump or cold flow
Step 2: Optimize Solder Paste Printing
Proper solder paste printing is essential for achieving consistent solder joints and minimizing solder balls. Follow these guidelines:
- Use a high-quality stencil with the correct aperture size and shape
- Ensure proper alignment between the stencil and PCB
- Maintain consistent print pressure and speed
- Keep the stencil clean and free of debris
- Regularly inspect and maintain your printer
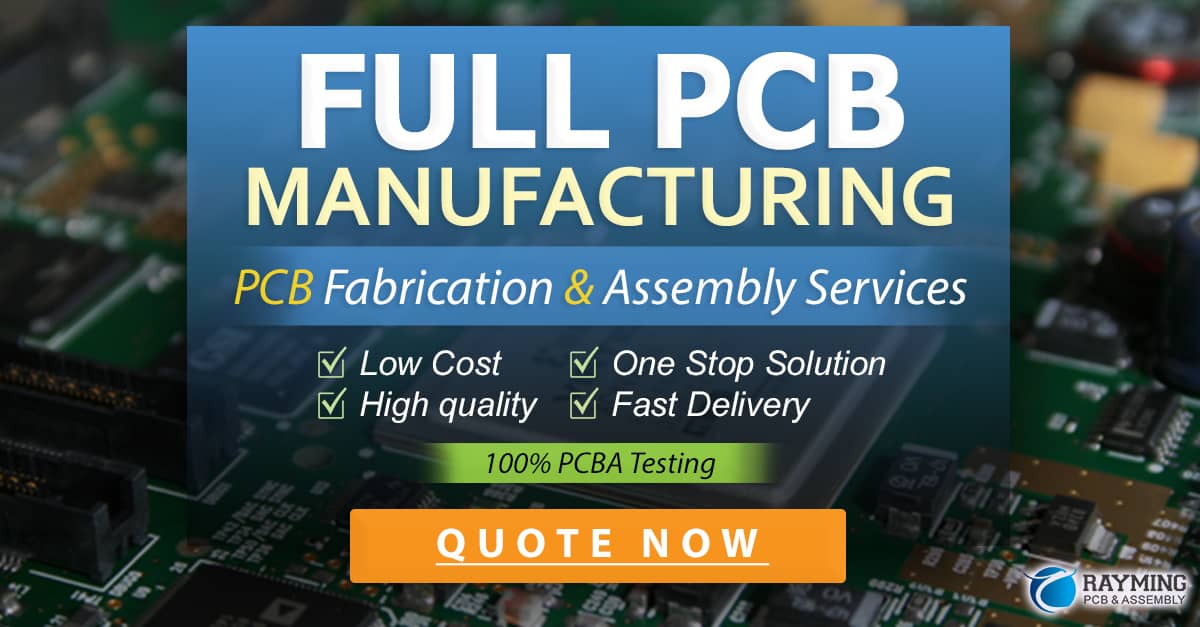
Step 3: Control Solder Paste Storage and Handling
Improper storage and handling of solder paste can lead to degradation and increased risk of solder balls. Adhere to these best practices:
- Store solder paste in a refrigerator at the manufacturer-recommended temperature
- Allow solder paste to reach room temperature before opening the container
- Gently mix the solder paste before use to ensure homogeneity
- Avoid exposing solder paste to excessive heat or humidity
- Use solder paste within its shelf life and discard expired material
Step 4: Maintain a Clean Manufacturing Environment
Contamination is a major contributor to solder ball formation. Implement these cleanliness measures:
- Regularly clean and maintain your manufacturing equipment
- Use clean, lint-free gloves when handling PCBs and components
- Store PCBs and components in a clean, dry environment
- Avoid exposing materials to dust, dirt, or other contaminants
- Use air filtration systems to control airborne particles
Step 5: Optimize Reflow Profile
An incorrect reflow profile can cause solder balling due to improper melting and solidification of the solder. Optimize your reflow profile by:
- Following the solder paste manufacturer’s recommended profile
- Ensuring adequate preheat time and temperature
- Achieving the correct peak temperature and time above liquidus
- Controlling the cooling rate to avoid thermal shock
- Regularly verifying and adjusting your reflow oven settings
Step 6: Minimize Component and PCB Warpage
Warpage of components or PCBs during reflow can lead to uneven solder paste melting and solder ball formation. Minimize warpage by:
- Selecting components with a coefficient of thermal expansion (CTE) that closely matches the PCB
- Using a PCB material with good thermal stability
- Designing a balanced copper distribution on the PCB
- Employing proper support and clamping during reflow
- Avoiding excessive component weight or size
Step 7: Use Nitrogen in Reflow
Nitrogen reflow can help reduce oxidation and improve solder joint quality, thus minimizing solder balls. Consider these factors when using nitrogen:
- Maintain a consistent nitrogen flow rate and purity
- Achieve an oxygen level below 100 ppm in the reflow oven
- Ensure proper ventilation and exhaust of the nitrogen
- Monitor and control the nitrogen consumption for cost-effectiveness
Step 8: Implement Solder Paste Inspection (SPI)
Solder paste inspection (SPI) systems can help detect and prevent solder paste printing issues that lead to solder balls. Implement SPI by:
- Selecting an SPI system with adequate resolution and speed
- Setting up appropriate inspection parameters and thresholds
- Regularly calibrating and maintaining the SPI system
- Analyzing SPI data to identify and correct printing issues
- Integrating SPI with your manufacturing line for real-time process control
Step 9: Perform Automated Optical Inspection (AOI)
Automated optical inspection (AOI) can help detect solder balls and other defects after reflow. Utilize AOI effectively by:
- Choosing an AOI system with sufficient resolution and lighting options
- Developing robust inspection programs for your specific PCBs and components
- Setting appropriate defect detection parameters and tolerances
- Regularly reviewing and optimizing AOI programs based on process changes
- Integrating AOI data with your quality management system for traceability
Step 10: Conduct Regular Process Audits
Regular process audits can help identify and correct issues that contribute to solder ball formation. Perform audits on:
- Solder paste printing parameters and stencil condition
- Reflow oven settings and temperature profiles
- Cleanliness and maintenance of manufacturing equipment
- Handling and storage of materials
- Employee training and adherence to standard operating procedures
Step 11: Continuously Monitor and Improve
Continuously monitoring and improving your SMT manufacturing process is key to minimizing solder balls and other defects. Implement these practices:
- Collect and analyze process data from SPI, AOI, and other inspection systems
- Use statistical process control (SPC) to identify trends and variations
- Conduct root cause analysis for recurring defects
- Implement corrective and preventive actions based on data analysis
- Encourage employee feedback and suggestions for process improvement
- Stay updated on industry best practices and emerging technologies
Frequently Asked Questions (FAQ)
1. What is the main cause of solder balls in SMT assembly?
The main causes of solder balls in SMT assembly include excessive solder paste deposition, incorrect reflow profile, contamination, improper handling or storage of materials, and incompatible solder paste and flux chemistries.
2. How can I detect solder balls on my PCBs?
Solder balls can be detected using automated optical inspection (AOI) systems, which use high-resolution cameras and advanced algorithms to identify defects on PCBs after reflow. Manual visual inspection under magnification can also be used for smaller batches or specific areas of concern.
3. Can solder balls cause short circuits on my PCBs?
Yes, solder balls can cause short circuits if they bridge adjacent pads or traces on the PCB. This can lead to electrical failures, reduced performance, and reliability issues in the final product.
4. How does nitrogen reflow help reduce solder balls?
Nitrogen reflow helps reduce oxidation during the soldering process, which can contribute to solder ball formation. By maintaining a low oxygen level in the reflow oven, nitrogen reflow promotes cleaner and more consistent solder joint formation, thus minimizing the risk of solder balls.
5. What is the role of employee training in preventing solder balls?
Employee training is crucial in preventing solder balls and other SMT defects. Properly trained employees are more likely to follow standard operating procedures, handle materials correctly, and identify potential issues before they lead to defects. Regular training also promotes a culture of quality and continuous improvement in the manufacturing process.
Cause of Solder Balls | Prevention Method |
---|---|
Excessive solder paste deposition | Optimize solder paste printing |
Incorrect reflow profile | Optimize reflow profile |
Contamination | Maintain a clean manufacturing environment |
Improper handling or storage of materials | Control solder paste storage and handling |
Incompatible solder paste and flux chemistries | Choose the right solder paste |
By implementing these 11 easy steps and continuously monitoring and improving your SMT manufacturing process, you can significantly reduce the occurrence of solder balls and improve the overall quality and reliability of your electronic assemblies.
0 Comments