What is PCB Edge Plating?
PCB edge plating refers to the process of applying a metallic coating, typically copper, to the edges of a printed circuit board (PCB). This technique is used to provide electrical continuity, improve mechanical strength, and protect the edges from environmental factors such as moisture and corrosion. Edge plating is particularly important for PCBs that require a reliable connection between layers or those that will be subjected to harsh operating conditions.
Why is PCB Edge Plating Necessary?
PCB edge plating serves several critical functions:
-
Electrical continuity: By metalizing the edges of a PCB, electrical continuity is established between the layers of the board. This is essential for multilayer PCBs, where signals need to travel from one layer to another.
-
Mechanical strength: Edge plating reinforces the edges of the PCB, making them more resistant to chipping, cracking, and other forms of mechanical damage. This is especially important for boards that will be subjected to physical stress or vibration.
-
Environmental protection: The metallic coating applied during edge plating helps to seal the edges of the PCB, preventing moisture and other contaminants from penetrating the board and causing corrosion or other forms of damage.
Electroless Copper Plating for PCB Edge Metalizing
Electroless copper plating is a chemical process that deposits a layer of copper onto the edges of a PCB without the use of an external electrical current. This method is widely used for PCB edge plating due to its simplicity, cost-effectiveness, and ability to produce a uniform coating.
How Does Electroless Copper Plating Work?
The electroless copper plating process involves several steps:
-
Cleaning: The PCB edges are thoroughly cleaned to remove any contaminants, such as dirt, grease, or oxidation, that could interfere with the plating process.
-
Activation: The edges are then treated with a catalyst, typically a palladium-based solution, which creates a surface that is receptive to the deposition of copper.
-
Plating: The activated PCB is immersed in an electroless copper plating solution, which contains a source of copper ions, a reducing agent, and various additives to control the plating rate and quality. The reducing agent chemically reduces the copper ions, causing them to deposit onto the catalyzed surface of the PCB edges.
-
Rinsing and drying: After plating, the PCB is rinsed to remove any excess plating solution and then dried.
Advantages of Electroless Copper Plating for PCB Edge Metalizing
Electroless copper plating offers several advantages over other edge metalizing techniques:
-
Uniformity: Electroless plating produces a uniform copper coating on the PCB edges, ensuring consistent electrical and mechanical properties.
-
Simplicity: The process does not require complex equipment or electrical connections, making it easier to implement and maintain.
-
Cost-effectiveness: Compared to other plating methods, electroless copper plating is relatively inexpensive, as it does not require expensive equipment or consumables.
-
Compatibility: Electroless copper plating is compatible with a wide range of PCB materials, including FR-4, polyimide, and high-frequency laminates.
Factors Affecting PCB Edge Plating Quality
Several factors can impact the quality and performance of PCB edge plating:
-
Edge preparation: Proper cleaning and activation of the PCB edges are critical for achieving a strong, uniform plating. Any contaminants or inconsistencies in the edge preparation can lead to poor adhesion or uneven plating.
-
Plating solution composition: The electroless copper plating solution must be carefully formulated and maintained to ensure consistent plating results. Factors such as the concentration of copper ions, the type and amount of reducing agent, and the presence of additives can all affect the plating rate, quality, and appearance.
-
Temperature: The temperature of the plating solution must be carefully controlled, as it can significantly impact the plating rate and quality. Higher temperatures generally result in faster plating rates but can also lead to increased solution instability and reduced plating quality.
-
Plating time: The duration of the plating process determines the thickness of the copper coating on the PCB edges. Longer plating times result in thicker coatings, which can provide better electrical and mechanical properties. However, excessive plating times can lead to uneven coating thickness or other quality issues.
-
Post-plating processing: After plating, the PCB edges may require additional processing, such as rinsing, drying, and inspection. Proper post-plating processing ensures that the plated edges meet the required specifications and are free from defects.
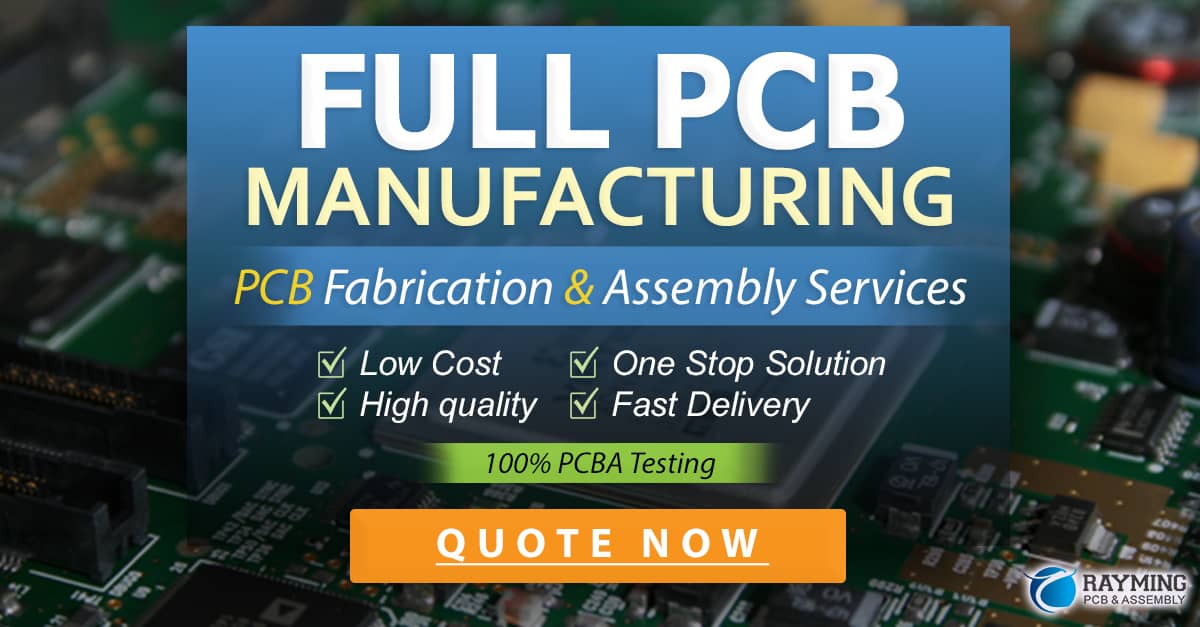
Troubleshooting Common PCB Edge Plating Issues
Despite the relative simplicity of the electroless copper plating process, several issues can arise that affect the quality and performance of the plated edges:
-
Uneven plating: Uneven plating can occur due to poor edge preparation, inconsistent plating solution composition, or improper temperature control. To address this issue, ensure that the edges are thoroughly cleaned and activated, the plating solution is properly formulated and maintained, and the temperature is carefully controlled.
-
Poor adhesion: Poor adhesion between the copper coating and the PCB edges can result from contaminants on the edge surface or inadequate activation. To improve adhesion, ensure that the edges are completely clean and properly activated before plating.
-
Blistering or peeling: Blistering or peeling of the copper coating can occur due to excessive plating times, high plating temperatures, or contamination of the plating solution. To prevent these issues, monitor the plating time and temperature closely and regularly test the plating solution for contaminants.
-
Insufficient plating thickness: Insufficient plating thickness can result from short plating times, low plating temperatures, or a depleted plating solution. To achieve the desired coating thickness, adjust the plating time and temperature as needed and regularly replenish the plating solution.
Best Practices for PCB Edge Plating
To ensure high-quality, reliable PCB edge plating, consider the following best practices:
-
Use a well-designed plating process: Develop a robust plating process that includes proper edge preparation, consistent plating solution composition, and careful control of plating parameters such as temperature and time.
-
Regularly maintain and monitor the plating solution: Regularly test the plating solution for contaminants and replenish it as needed to ensure consistent plating results.
-
Implement quality control measures: Establish quality control procedures to inspect the plated edges for uniformity, adhesion, and thickness. Use techniques such as cross-sectioning, peel testing, and thickness measurement to verify the quality of the plating.
-
Train personnel: Ensure that personnel involved in the edge plating process are properly trained in the process steps, quality control measures, and troubleshooting techniques.
-
Consider alternative plating methods: While electroless copper plating is a popular choice for PCB edge metalizing, other methods, such as immersion tin plating or direct metallization, may be more suitable for certain applications. Evaluate the specific requirements of your PCB and select the most appropriate plating method.
FAQ
-
What is the typical thickness of copper plating on PCB edges?
The typical thickness of copper plating on PCB edges ranges from 5 to 25 microns (0.2 to 1 mil). The specific thickness required depends on the application and the desired electrical and mechanical properties. -
Can electroless copper plating be used for both through-hole and SMT PCBs?
Yes, electroless copper plating can be used for both through-hole and surface-mount technology (SMT) PCBs. The process is versatile and can be adapted to various PCB designs and manufacturing techniques. -
How does electroless copper plating compare to other edge metalizing methods?
Electroless copper plating offers several advantages over other edge metalizing methods, such as simplicity, cost-effectiveness, and compatibility with a wide range of PCB materials. However, other methods, such as immersion tin plating or direct metallization, may be more suitable for certain applications, depending on the specific requirements of the PCB. -
What are the environmental considerations for electroless copper plating?
Electroless copper plating solutions contain chemicals that can be hazardous to the environment if not properly handled and disposed of. It is essential to follow appropriate safety and environmental guidelines when working with these solutions, including proper ventilation, personal protective equipment, and waste disposal practices. -
Can electroless copper plating be used for high-frequency PCBs?
Yes, electroless copper plating can be used for high-frequency PCBs, as it provides a uniform, conductive coating on the PCB edges. However, for high-frequency applications, it is essential to consider factors such as the plating thickness, surface roughness, and the specific dielectric materials used in the PCB to ensure optimal signal integrity and performance.
In conclusion, PCB edge plating using electroless copper plating is a reliable and cost-effective method for metalizing the edges of printed circuit boards. By providing electrical continuity, mechanical strength, and environmental protection, edge plating ensures the proper functioning and longevity of PCBs in various applications. By understanding the process, factors affecting plating quality, and best practices for implementation, manufacturers can produce high-quality, reliable PCBs with consistently plated edges.
0 Comments