Introduction to PCB Etching
Printed circuit board (PCB) etching is a critical process in the manufacturing of electronic devices. It involves removing unwanted copper from a PCB substrate to create conductive traces that electrically connect components. The two main methods for PCB etching are wet etching and dry etching. In this article, we will explore these two techniques, compare their advantages and disadvantages, and provide insights into selecting the appropriate etching solution for your PCB project.
What is Wet Etching?
Wet etching, also known as chemical etching, is a subtractive process that uses liquid etchants to remove unwanted copper from a PCB substrate. The process involves the following steps:
- Cleaning the PCB surface to remove contaminants
- Applying a photoresist layer to the copper surface
- Exposing the photoresist to UV light through a photomask
- Developing the photoresist to reveal the desired copper pattern
- Immersing the PCB in a chemical etchant solution
- Removing the remaining photoresist
Common Wet Etching Solutions
Several chemical etchants are used in wet etching, each with its own characteristics and applications. The most common wet etching solutions include:
Etchant | Composition | Etch Rate | Selectivity | Application |
---|---|---|---|---|
Ferric Chloride | FeCl3 | Moderate | Low | General-purpose, hobbyist use |
Cupric Chloride | CuCl2 | Fast | Moderate | High-volume production |
Ammonium Persulfate | (NH4)2S2O8 | Slow | High | Fine-pitch, high-resolution traces |
Sodium Persulfate | Na2S2O8 | Moderate | High | Fine-pitch, high-resolution traces |
Advantages of Wet Etching
- Low cost and simplicity
- Suitable for small-scale and hobbyist projects
- Can handle complex geometries and fine features
- Relatively fast etch rates
Disadvantages of Wet Etching
- Limited resolution and precision compared to dry etching
- Isotropic etching can lead to undercut and loss of fine features
- Requires proper handling and disposal of hazardous chemicals
- Susceptible to environmental factors (temperature, agitation, etc.)
What is Dry Etching?
Dry etching, also known as plasma etching, is a subtractive process that uses gaseous etchants to remove unwanted copper from a PCB substrate. The process involves the following steps:
- Cleaning the PCB surface to remove contaminants
- Applying a photoresist or hard mask layer to the copper surface
- Exposing the photoresist to UV light through a photomask (if using photoresist)
- Developing the photoresist to reveal the desired copper pattern (if using photoresist)
- Placing the PCB in a vacuum chamber
- Introducing reactive gases and creating a plasma
- Etching the exposed copper using the reactive plasma
- Removing the remaining photoresist or hard mask
Common Dry Etching Techniques
Several dry etching techniques are used in PCB manufacturing, each with its own characteristics and applications. The most common dry etching techniques include:
Technique | Etchant Gases | Etch Profile | Selectivity | Application |
---|---|---|---|---|
Reactive Ion Etching (RIE) | CF4, SF6, O2, Cl2 | Anisotropic | Moderate | High-resolution traces, fine-pitch |
Plasma Etching | CF4, SF6, O2 | Isotropic | Low | General-purpose, less critical features |
Ion Beam Etching (IBE) | Ar, Xe | Highly Anisotropic | High | Ultra-fine features, high aspect ratios |
Advantages of Dry Etching
- High resolution and precision
- Anisotropic etching for vertical sidewalls and minimal undercut
- Capable of etching ultra-fine features and high aspect ratios
- Highly controllable and repeatable process
- Reduced environmental impact compared to wet etching
Disadvantages of Dry Etching
- Higher cost and complexity compared to wet etching
- Requires specialized equipment and skilled operators
- Slower etch rates compared to wet etching
- Potential for plasma-induced damage to sensitive components
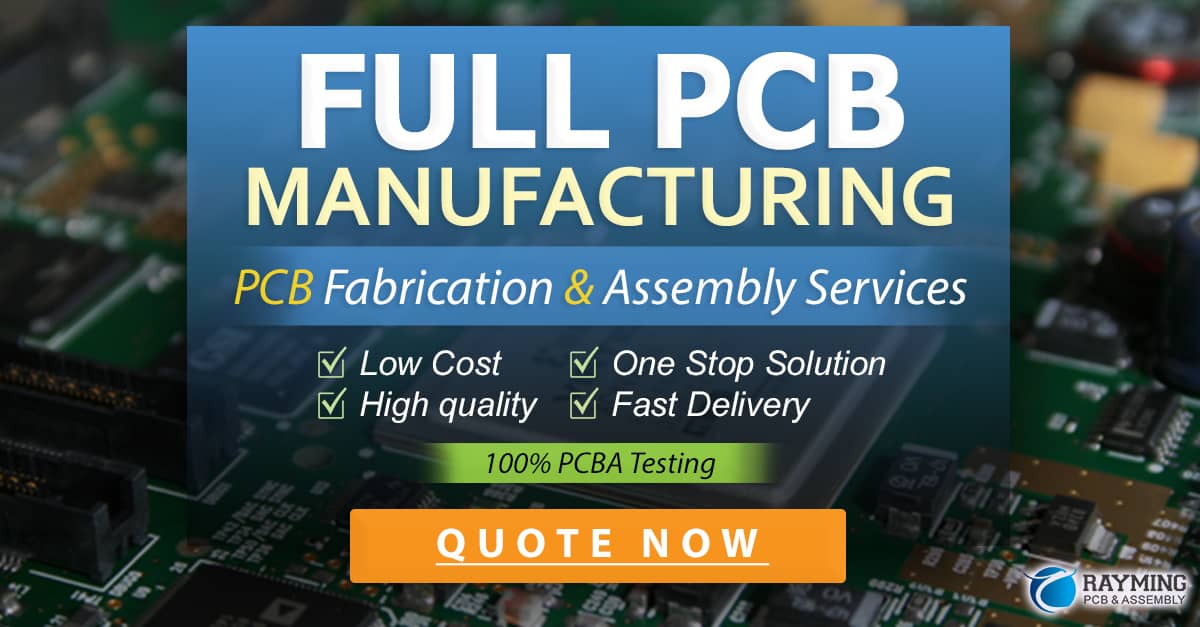
Selecting the Appropriate Etching Solution
When choosing between wet and dry etching for your PCB project, consider the following factors:
- Feature size and resolution requirements
- Production volume and throughput
- Cost and available resources
- Environmental and safety concerns
- Compatibility with substrate materials and components
In general, wet etching is suitable for small-scale projects, hobbyists, and less critical features, while dry etching is preferred for high-volume production, ultra-fine features, and high-precision applications.
FAQ
1. Can I use a combination of wet and dry etching in my PCB project?
Yes, it is possible to use both wet and dry etching in a single PCB project. This hybrid approach can be beneficial when different areas of the PCB require different levels of precision or when cost and time constraints are a factor. However, it is essential to ensure compatibility between the two processes and to properly plan the fabrication sequence.
2. How do I dispose of used wet etching solutions?
Proper disposal of used wet etching solutions is crucial to minimize environmental impact and ensure safety. Follow these steps:
- Neutralize the used etchant according to the manufacturer’s instructions.
- Filter out any solid particles and dispose of them as hazardous waste.
- Dilute the neutralized solution with water.
- Contact your local waste management authority for guidance on proper disposal methods.
Always consult the material safety data sheet (MSDS) and follow local regulations when handling and disposing of chemical etchants.
3. What is the typical resolution achievable with wet and dry etching?
The resolution of wet and dry etching depends on various factors, such as the etchant type, process parameters, and photoresist quality. In general:
- Wet etching: Typical resolution ranges from 50 to 100 μm, with a minimum feature size of around 25 μm.
- Dry etching: Typical resolution ranges from 1 to 10 μm, with a minimum feature size of less than 1 μm for advanced techniques like ion beam etching.
Keep in mind that these values are approximate and can vary based on specific process conditions and equipment capabilities.
4. Can I etch non-copper materials using wet or dry etching?
Yes, both wet and dry etching can be used to etch various materials beyond copper. Some examples include:
- Wet etching: Aluminum, silver, gold, and some dielectrics (e.g., silicon dioxide, silicon nitride)
- Dry etching: Silicon, polyimide, BCB, and various metals and dielectrics
The choice of etchant and process parameters will depend on the specific material and desired etch characteristics.
5. How can I improve the etch uniformity in my PCB project?
To improve etch uniformity, consider the following tips:
- Ensure proper cleaning and surface preparation before etching
- Maintain consistent temperature and agitation during wet etching
- Use high-quality photoresists and optimize exposure and development processes
- Monitor and control etchant concentration and pH levels
- Employ endpoint detection methods to prevent over-etching
- Use dummy fill patterns to promote even current density distribution in copper regions
By carefully controlling these factors and regularly monitoring the etching process, you can achieve better etch uniformity and overall PCB Quality.
Conclusion
PCB etching is a crucial step in the manufacturing of electronic devices, and selecting the appropriate etching solution is essential for achieving the desired circuit board traces. Wet etching and dry etching offer distinct advantages and disadvantages, catering to different project requirements and constraints. By understanding the principles, techniques, and considerations involved in each method, you can make an informed decision and optimize your PCB fabrication process. Whether you are a hobbyist or a professional, choosing the right etching solution will contribute to the success and reliability of your electronic projects.
0 Comments