What is PCB Copper Weight?
PCB copper weight refers to the thickness of the copper layer on a printed circuit board (PCB). It is an essential factor to consider when designing and manufacturing PCBs, as it directly affects the board’s electrical and thermal properties, as well as its overall durability and reliability.
The copper weight is typically measured in ounces per square foot (oz/ft²) and ranges from 0.5 oz/ft² to 4 oz/ft². The most common copper weights used in PCB manufacturing are:
Copper Weight (oz/ft²) | Thickness (mils) | Thickness (µm) |
---|---|---|
0.5 | 0.7 | 17.5 |
1 | 1.4 | 35 |
2 | 2.8 | 70 |
3 | 4.2 | 105 |
4 | 5.6 | 140 |
It’s important to note that the copper weight is not the same as the copper thickness. The copper weight is a measure of the mass of copper per unit area, while the thickness is the actual physical thickness of the copper layer.
Factors to Consider When Choosing PCB Copper Weight
When selecting the appropriate copper weight for your PCB, there are several factors to consider:
Current Carrying Capacity
The copper weight directly affects the current carrying capacity of the PCB traces. Thicker copper layers can carry more current without overheating or experiencing voltage drops. The current carrying capacity can be calculated using the following formula:
I = (ΔT × A × k) / (ρ × L)
Where:
– I: Current (A)
– ΔT: Temperature rise above ambient (°C)
– A: Cross-sectional area of the trace (mils²)
– k: Thermal conductivity of copper (mW/°C·mil)
– ρ: Electrical resistivity of copper (Ω·mil)
– L: Length of the trace (mils)
Trace Width and Spacing
The copper weight also influences the minimum trace width and spacing that can be achieved on the PCB. Thinner copper layers allow for narrower traces and smaller spacing, which is essential for high-density designs. However, thinner traces are more susceptible to damage and may have lower current carrying capacity.
PCB Thickness and Rigidity
Thicker copper layers contribute to the overall thickness and rigidity of the PCB. This can be advantageous for applications that require a more robust and durable board. However, thicker boards may also be more difficult to manufacture and may increase the overall cost of the PCB.
Thermal Management
Copper is an excellent thermal conductor, and thicker copper layers can help dissipate heat more effectively from components on the PCB. This is particularly important for power-hungry devices or applications that generate significant amounts of heat.
Signal Integrity
The copper weight can impact signal integrity, especially at high frequencies. Thicker copper layers have lower resistance and inductance, which can help reduce signal loss and maintain signal integrity over longer distances.
How to Choose the Right PCB Copper Weight
Selecting the appropriate PCB copper weight depends on the specific requirements of your application. Here are some general guidelines to help you choose the right copper weight:
0.5 oz/ft² and 1 oz/ft²
These thin copper weights are suitable for low-power, high-density designs where space is limited, and the current carrying requirements are minimal. They are commonly used in consumer electronics, such as smartphones, tablets, and wearables.
2 oz/ft²
This is the most common copper weight used in PCB manufacturing. It offers a good balance between current carrying capacity, trace width and spacing, and overall board thickness. 2 oz/ft² is suitable for a wide range of applications, including industrial controls, automotive electronics, and medical devices.
3 oz/ft² and 4 oz/ft²
These heavy copper weights are used in high-power applications that require significant current carrying capacity and thermal management. They are commonly found in power electronics, aerospace and defense systems, and renewable energy applications.
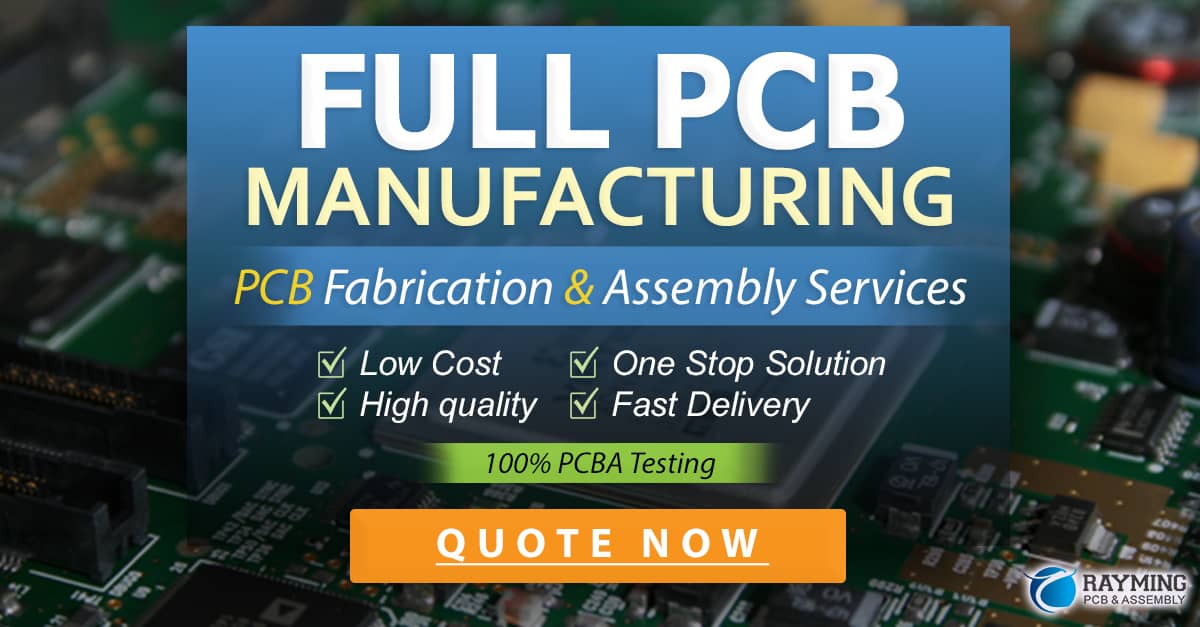
PCB Copper Weight and Manufacturing Considerations
The chosen PCB copper weight can impact the manufacturing process and the overall cost of the board. Here are some manufacturing considerations to keep in mind:
Etching Process
Thicker copper layers require longer etching times, which can increase the manufacturing lead time and cost. The etching process must also be carefully controlled to ensure consistent results and avoid over-etching or under-etching.
Plating Process
If the PCB requires additional copper plating, such as in the case of through-hole vias or surface finish, the base copper weight must be taken into account. Thicker base copper layers may require longer plating times or may impact the uniformity of the plating.
Lamination Process
The copper weight can affect the lamination process, particularly for multi-layer boards. Thicker copper layers may require higher lamination pressures and temperatures to ensure proper bonding between the layers.
Cost Implications
In general, thicker copper weights are more expensive than thinner ones due to the increased material cost and longer manufacturing times. However, the cost difference may be justified if the application requires the benefits provided by thicker copper, such as improved current carrying capacity or thermal management.
Tips for Applying the Right PCB Copper Weight
-
Understand your application’s requirements: Carefully consider the electrical, thermal, and mechanical requirements of your application before selecting the PCB copper weight.
-
Use current carrying capacity calculators: There are many online tools and calculators available to help determine the appropriate copper weight based on your current carrying requirements.
-
Consult with your PCB manufacturer: Discuss your copper weight requirements with your PCB manufacturer early in the design process. They can provide valuable insights and recommendations based on their experience and manufacturing capabilities.
-
Consider using varying copper weights: In some cases, it may be beneficial to use different copper weights on different layers of the PCB. For example, you could use a thicker copper weight on power layers and a thinner copper weight on signal layers to optimize performance and cost.
-
Don’t overspecify: While it may be tempting to use the thickest copper weight available, this can lead to unnecessary costs and manufacturing challenges. Choose the copper weight that meets your requirements without overspecifying.
Frequently Asked Questions (FAQ)
1. What is the most common PCB copper weight?
The most common PCB copper weight is 1 oz/ft², which offers a good balance between electrical performance, manufacturability, and cost for a wide range of applications.
2. Can I mix different copper weights on the same PCB?
Yes, it is possible to use different copper weights on different layers of the same PCB. This can be useful for optimizing the electrical and thermal performance of specific layers, such as using thicker copper for power layers and thinner copper for signal layers.
3. How does PCB copper weight affect the cost of the board?
In general, thicker copper weights are more expensive than thinner ones due to the increased material cost and longer manufacturing times. However, the cost difference may be justified if the application requires the benefits provided by thicker copper, such as improved current carrying capacity or thermal management.
4. What is the minimum trace width and spacing for different copper weights?
The minimum trace width and spacing depend on several factors, including the copper weight, PCB manufacturing capabilities, and the specific design rules for your application. As a general guideline, thinner copper weights allow for narrower traces and smaller spacing. However, it’s essential to consult with your PCB manufacturer to determine the specific design rules for your project.
5. How does PCB copper weight impact signal integrity?
The copper weight can impact signal integrity, especially at high frequencies. Thicker copper layers have lower resistance and inductance, which can help reduce signal loss and maintain signal integrity over longer distances. However, the impact of copper weight on signal integrity also depends on other factors, such as the dielectric material, trace geometry, and termination techniques used in the design.
Conclusion
PCB copper weight is a critical factor to consider when designing and manufacturing printed circuit boards. It directly affects the electrical, thermal, and mechanical properties of the board, as well as its overall cost and manufacturability. By understanding the factors that influence copper weight selection and following best practices for applying the right copper weight, you can ensure that your PCB meets the specific requirements of your application while balancing performance, reliability, and cost.
0 Comments