Introduction to Kapton PCB
Kapton PCB, also known as polyimide PCB, is a type of printed circuit board that utilizes Kapton as the base material. Kapton is a high-performance polymer developed by DuPont that possesses excellent thermal, mechanical, and electrical properties. These unique characteristics make Kapton PCBs ideal for applications that demand high reliability and durability in harsh environments.
In this comprehensive guide, we will explore the various aspects of Kapton PCBs, including their construction, properties, applications, manufacturing process, and design considerations. We will also address some frequently asked questions to help you better understand this remarkable technology.
What is Kapton?
Kapton is a polyimide film that was introduced by DuPont in the late 1960s. It is a synthetic polymer that is produced by polymerizing an aromatic dianhydride and an aromatic diamine. The resulting material is a transparent, amber-colored film that exhibits exceptional properties, such as:
- High thermal stability (up to 400°C)
- Excellent mechanical strength and flexibility
- Superior electrical insulation
- Resistance to chemicals and solvents
- Low dielectric constant and dissipation factor
- Dimensional stability over a wide temperature range
These properties make Kapton an ideal material for various applications, including aerospace, automotive, electronics, and medical industries.
Construction of Kapton PCBs
Kapton PCBs are constructed using Kapton film as the base material, which is laminated with copper foil on one or both sides. The copper foil is then etched to create the desired circuit pattern. The Kapton film acts as both the substrate and the dielectric layer, providing mechanical support and electrical insulation between the conductive layers.
The typical structure of a Kapton PCB consists of the following layers:
- Kapton film (substrate)
- Adhesive layer
- Copper foil (conductive layer)
- Solder mask (optional)
- Silkscreen (optional)
The thickness of the Kapton film can vary depending on the application requirements, ranging from 25 μm to 125 μm. The copper foil thickness is typically 18 μm or 35 μm, although other thicknesses are available for specific needs.
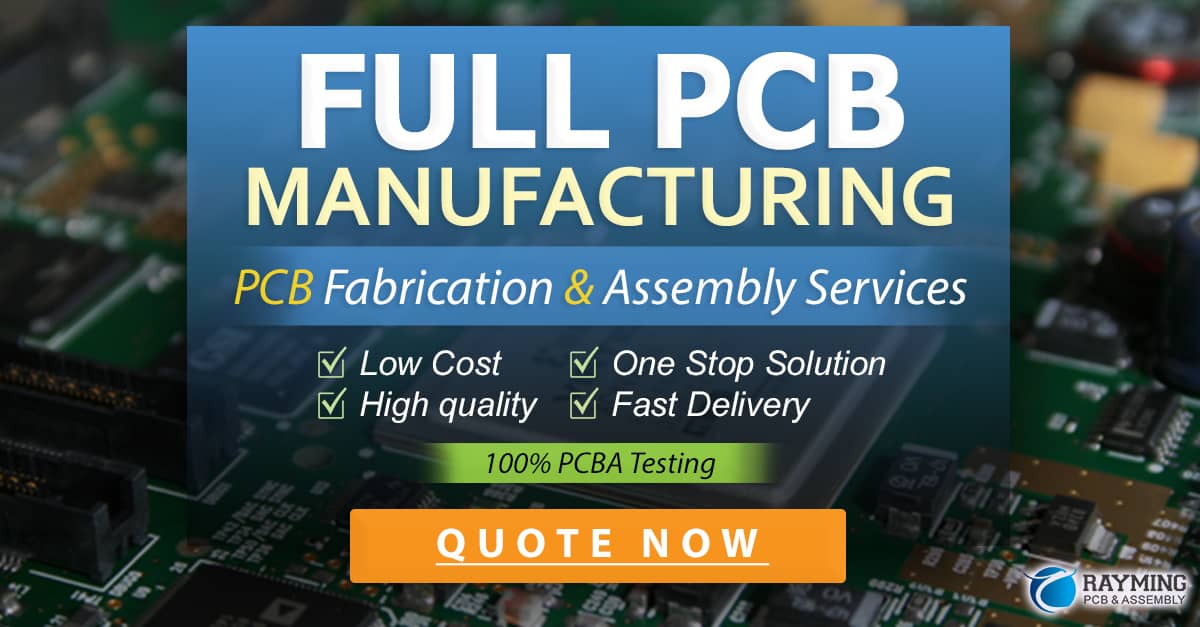
Properties of Kapton PCBs
Kapton PCBs inherit many of the desirable properties of Kapton film, making them suitable for demanding applications. Some of the key properties of Kapton PCBs include:
- High temperature resistance
-
Kapton PCBs can operate in temperatures ranging from -269°C to 400°C, making them suitable for extreme temperature environments.
-
Excellent dielectric properties
-
Kapton has a low dielectric constant (3.5 at 1 MHz) and a low dissipation factor (0.002 at 1 MHz), which minimizes signal loss and ensures high-quality signal transmission.
-
Mechanical strength and flexibility
-
Kapton PCBs exhibit high tensile strength (231 MPa) and elongation (72%), allowing them to withstand mechanical stress and vibrations. They can also be bent and flexed without damage.
-
Chemical resistance
-
Kapton PCBs are resistant to most chemicals, solvents, and oils, making them suitable for applications exposed to harsh chemical environments.
-
Dimensional stability
- Kapton PCBs maintain their dimensions over a wide temperature range, with a low coefficient of thermal expansion (20 ppm/°C), ensuring reliable performance in varying thermal conditions.
Applications of Kapton PCBs
Kapton PCBs find applications in various industries due to their unique properties. Some of the common applications include:
- Aerospace and defense
- Satellite and spacecraft electronics
- Avionics systems
- Missile guidance systems
-
Radar and communication equipment
-
Automotive
- Engine control units (ECUs)
- Sensors and actuators
- Electric and hybrid vehicle power electronics
-
Infotainment systems
-
Medical
- Implantable devices
- Surgical instruments
- Diagnostic equipment
-
Wearable health monitors
-
Industrial
- Oil and gas exploration equipment
- High-temperature sensors and probes
- Power electronics for renewable energy systems
-
Semiconductor manufacturing equipment
-
Consumer electronics
- Smartphones and tablets
- Wearable devices
- Flexible displays
- High-end audio equipment
Manufacturing Process of Kapton PCBs
The manufacturing process of Kapton PCBs is similar to that of traditional PCBs, with some modifications to accommodate the unique properties of Kapton film. The general steps involved in the manufacturing process are:
- Substrate preparation
- Kapton film is cleaned and treated to improve adhesion.
-
Copper foil is laminated onto the Kapton film using an adhesive layer.
-
Circuit pattern creation
- The desired circuit pattern is transferred onto the copper foil using photolithography or laser direct imaging (LDI).
-
The exposed copper is etched away, leaving the circuit pattern.
-
Drilling and plating
- Holes are drilled through the Kapton PCB for component mounting and interconnections.
-
The holes are plated with copper to establish electrical connections between layers.
-
Solder mask and silkscreen application
- A solder mask is applied to protect the copper traces and prevent solder bridging.
-
A silkscreen layer is added for component labeling and identification.
-
Surface finish
-
A surface finish, such as ENIG (Electroless Nickel Immersion Gold) or HASL (Hot Air Solder Leveling), is applied to the exposed copper to improve solderability and protect against oxidation.
-
Cutting and packaging
- The Kapton PCB panel is cut into individual boards using a router or laser.
- The finished boards are inspected, tested, and packaged for shipping.
Design Considerations for Kapton PCBs
When designing Kapton PCBs, several factors must be considered to ensure optimal performance and reliability. Some of the key design considerations include:
- Thermal management
- Ensure proper heat dissipation through appropriate component placement, copper pours, and thermal vias.
-
Consider the use of heat sinks or cooling solutions for high-power components.
-
Mechanical stress
- Design the PCB layout to minimize mechanical stress on components and solder joints, especially in flexing or vibrating environments.
-
Use strain relief features, such as bend reliefs or stiffeners, to protect the board from excessive bending.
-
Impedance control
- Carefully design the trace widths, spacing, and layer stackup to maintain proper impedance for high-speed signals.
-
Use simulation tools to analyze and optimize the signal integrity of the design.
-
Manufacturability
- Follow the design guidelines provided by the PCB manufacturer to ensure the design is compatible with their manufacturing process.
-
Consider the minimum feature sizes, such as trace width and spacing, hole size, and annular ring, to avoid manufacturing issues.
-
Assembly
- Select components that are compatible with the high-temperature requirements of the application.
- Use appropriate solder paste and reflow profiles for the chosen surface finish and components.
Frequently Asked Questions (FAQ)
-
Q: How does Kapton compare to other PCB materials, such as FR-4?
A: Kapton offers superior thermal stability, mechanical strength, and chemical resistance compared to FR-4. It can operate in a much wider temperature range (-269°C to 400°C) and withstand harsher environments. However, Kapton PCBs are more expensive than FR-4 PCBs and may require specialized manufacturing processes. -
Q: Can Kapton PCBs be used for multilayer designs?
A: Yes, Kapton PCBs can be fabricated with multiple layers, allowing for more complex circuit designs. The number of layers depends on the specific requirements of the application and the capabilities of the PCB manufacturer. -
Q: Are Kapton PCBs suitable for high-frequency applications?
A: Yes, Kapton PCBs are well-suited for high-frequency applications due to their low dielectric constant and dissipation factor. These properties minimize signal loss and ensure high-quality signal transmission, making Kapton PCBs a good choice for applications such as RF and microwave circuits. -
Q: How do I select the appropriate Kapton film thickness for my PCB?
A: The choice of Kapton film thickness depends on the specific requirements of your application, such as the required mechanical strength, flexibility, and electrical properties. Thinner films (25-50 μm) are more flexible and suitable for dynamic flex applications, while thicker films (75-125 μm) offer greater mechanical stability and are better suited for static flex or rigid-flex applications. Consult with your PCB manufacturer to determine the optimal film thickness for your design. -
Q: Can Kapton PCBs be recycled?
A: Recycling Kapton PCBs can be challenging due to the difficulty in separating the Kapton film from the copper and other materials. However, some specialized recycling facilities may be able to process Kapton PCBs, using techniques such as pyrolysis or chemical treatment to recover the valuable materials. It is essential to work with a reputable recycling company that has experience in handling Kapton PCBs to ensure proper disposal and minimize environmental impact.
Conclusion
Kapton PCBs offer a unique combination of thermal stability, mechanical strength, and electrical performance, making them an ideal choice for applications that demand high reliability in harsh environments. By understanding the properties, manufacturing process, and design considerations of Kapton PCBs, engineers can effectively leverage this technology to create innovative solutions in various industries, such as aerospace, automotive, medical, and industrial electronics.
As technology continues to advance, the demand for Kapton PCBs is expected to grow, driven by the increasing need for high-performance electronics in challenging operating conditions. By staying informed about the latest developments in Kapton PCB technology and working closely with experienced PCB manufacturers, designers can unlock the full potential of this remarkable material and push the boundaries of what is possible in electronic design.
0 Comments