What Are the Benefits of High Tg PCB?
There are several key benefits and advantages of using high TG PCBs:
1. Enhanced Thermal Stability
The primary benefit of high TG PCB is their enhanced thermal stability. With a glass transition temperature typically above 170°C, these PCBs are able to withstand higher operating temperatures without deformation or degradation of their properties. This makes them ideal for applications that generate significant heat or operate in high-temperature environments.
2. Improved Reliability
High TG PCBs offer improved reliability compared to standard PCBs. The higher glass transition temperature makes them less susceptible to thermal stress and cycling, which can lead to cracks, delamination, or other failures over time. This enhanced durability translates to longer product lifetimes and reduced failure rates.
3. Better Mechanical Strength
PCBs with a high Tg exhibit better mechanical strength and rigidity. They are less prone to warping, twisting, or bending under mechanical stress or at elevated temperatures. This dimensional stability is crucial for maintaining the integrity of the circuit and preventing issues like broken connections or short circuits.
4. Compatibility with Lead-Free Soldering
High TG PCBs are well-suited for lead-free soldering processes, which typically require higher soldering temperatures compared to traditional leaded soldering. The increased thermal stability of high TG PCBs allows them to withstand the higher soldering temperatures without damage, ensuring a reliable and robust solder joint.
5. Suitability for Harsh Environments
The enhanced thermal and mechanical properties of high TG PCBs make them suitable for harsh environments. They can operate reliably in conditions with high temperatures, thermal shock, vibration, or mechanical stress. This makes them ideal for applications in industries such as automotive, aerospace, military, and industrial electronics.
What Are the Applications of High TG PCB?
High TG PCBs find applications in various industries and sectors where thermal stability, reliability, and durability are critical. Some of the common applications include:
1. Automotive Electronics
In the automotive industry, high TG PCBs are used in various electronic systems and components that are exposed to high temperatures and harsh conditions. These include engine control units (ECUs), power management systems, lighting systems, and infotainment systems. The thermal stability of high TG PCBs ensures reliable operation even in the challenging environment under the hood.
2. Aerospace and Military
Aerospace and military applications demand electronics that can withstand extreme temperatures, vibration, and shock. High TG PCBs are used in avionics systems, radar equipment, communication devices, and other critical aerospace and military electronics. Their enhanced thermal and mechanical properties make them suitable for these demanding applications.
3. Industrial Electronics
Industrial electronics often operate in harsh environments with high temperatures, dust, and vibration. High TG PCBs are used in industrial control systems, power electronics, motor drives, and sensors. Their ability to maintain performance and reliability under challenging conditions makes them a preferred choice for industrial applications.
4. High-Power Applications
High TG PCBs are commonly used in high-power applications where significant heat generation occurs. These include power supplies, inverters, converters, and high-power amplifiers. The thermal stability of high TG PCBs allows them to dissipate heat effectively and maintain their electrical properties, ensuring reliable operation.
5. LED Lighting
LED lighting systems, especially high-power LED fixtures, generate considerable heat during operation. High TG PCBs are used as the substrate for LED mounting and interconnection. They provide the necessary thermal management and stability to ensure the long-term reliability and performance of LED lighting systems.
What Are the Material Options for High TG PCB?
Several materials are commonly used for the manufacture of high TG PCBs. The choice of material depends on the specific requirements of the application, such as the desired glass transition temperature, dielectric properties, and cost considerations. Here are some of the popular material options:
1. FR-4 High TG
FR-4 is the most widely used PCB material, and its high TG variant offers improved thermal stability compared to standard FR-4. FR-4 high TG has a glass transition temperature of around 170°C to 180°C. It is a cost-effective option for applications that require moderate thermal performance.
2. Polyimide (PI)
Polyimide is a high-performance polymer known for its excellent thermal stability and mechanical strength. PI-based PCBs have a glass transition temperature ranging from 250°C to 400°C, making them suitable for demanding high-temperature applications. However, PI is more expensive compared to FR-4 and other standard materials.
3. High Tg Epoxy
High Tg epoxy materials are specially formulated to provide enhanced thermal stability compared to standard epoxy resins. They typically have a glass transition temperature in the range of 180°C to 200°C. High Tg epoxy PCBs offer a balance between thermal performance and cost-effectiveness.
4. BT (Bismaleimide Triazine)
BT is a high-performance thermoset polymer with excellent thermal and mechanical properties. BT-based PCBs have a glass transition temperature around 210°C to 230°C. They offer superior thermal stability and are commonly used in high-reliability applications, such as aerospace and military electronics.
5. PTFE (Polytetrafluoroethylene)
PTFE, also known as Teflon, is a fluoropolymer with exceptional thermal stability and low dielectric loss. PTFE-based PCBs have a glass transition temperature above 300°C. They are used in high-frequency and microwave applications where low dielectric loss and high thermal stability are critical.
Here’s a table comparing the glass transition temperatures of different high TG PCB materials:
Material | Glass Transition Temperature (Tg) |
---|---|
FR-4 High TG | 170°C – 180°C |
Polyimide (PI) | 250°C – 400°C |
High Tg Epoxy | 180°C – 200°C |
BT | 210°C – 230°C |
PTFE | > 300°C |
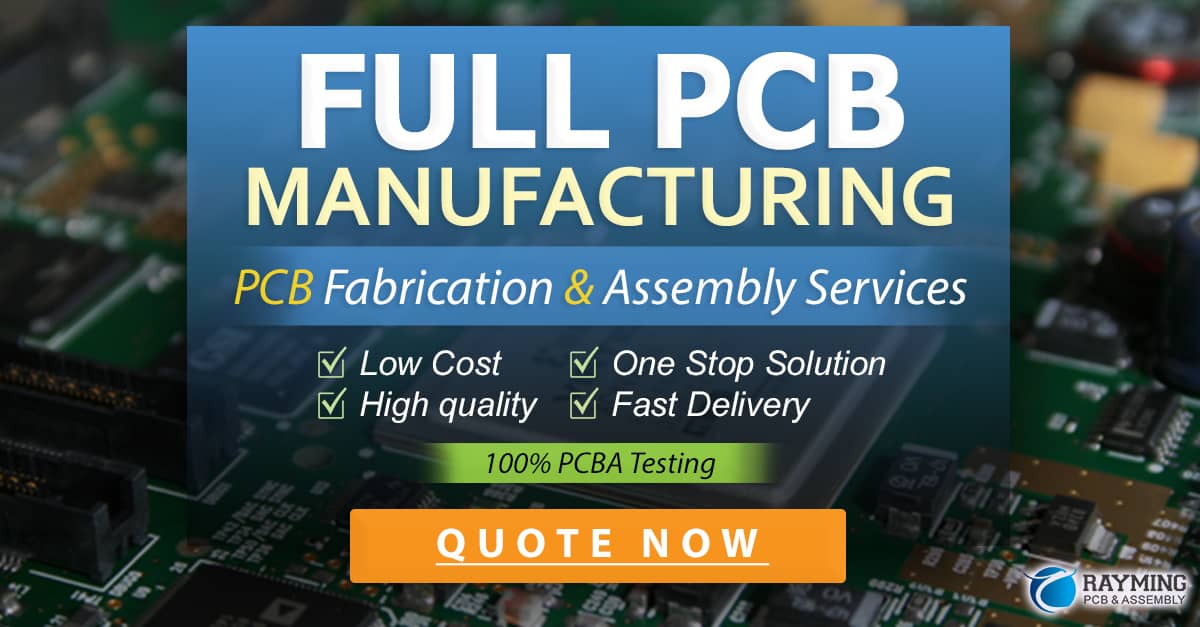
What Are the Manufacturing Considerations for High TG PCB?
Manufacturing high TG PCBs requires special considerations to ensure optimal performance and reliability. Here are some key aspects to consider:
1. Material Selection
Choosing the appropriate high TG material is crucial based on the specific application requirements. Factors such as the desired glass transition temperature, dielectric properties, thermal conductivity, and cost should be considered when selecting the material.
2. Controlled Impedance
High TG PCBs used in high-speed or high-frequency applications may require controlled impedance. Careful design and manufacturing processes are necessary to maintain the desired impedance values and minimize signal integrity issues. This involves precise control of trace widths, spacing, and dielectric thickness.
3. Thermal Management
Effective thermal management is essential for high TG PCBs to dissipate heat and prevent thermal-related failures. Proper design techniques, such as the use of thermal vias, heat spreaders, and appropriate copper thickness, can help improve thermal dissipation. Thermal simulations and analysis can aid in optimizing the thermal performance of the PCB.
4. Drilling and Plating
High TG materials may require special drilling and plating processes due to their enhanced thermal and mechanical properties. High-speed drilling, precise hole sizing, and proper plating techniques are necessary to ensure the integrity of the holes and maintain the desired electrical and thermal characteristics.
5. Soldering and Assembly
The assembly process for high TG PCBs requires careful control to prevent thermal damage during soldering. Lead-free soldering processes with higher temperatures are commonly used for high TG PCBs. Proper temperature profiles, soldering techniques, and handling procedures should be followed to ensure reliable solder joints and avoid thermal stress on the components.
6. Quality Control
Stringent quality control measures are essential throughout the manufacturing process of high TG PCBs. Visual inspection, automated optical inspection (AOI), and electrical testing should be performed to identify any defects or anomalies. Adherence to industry standards and customer specifications is crucial to ensure the desired performance and reliability of the PCBs.
Frequently Asked Questions (FAQ)
1. What is the difference between standard PCB and high TG PCB?
The main difference between standard PCB and high TG PCB lies in their glass transition temperature (Tg). Standard PCBs, such as those made with regular FR-4 material, have a Tg around 130°C to 140°C. In contrast, high TG PCBs have a Tg typically above 170°C, providing enhanced thermal stability and the ability to withstand higher operating temperatures.
2. How does the glass transition temperature affect PCB performance?
The glass transition temperature (Tg) is a critical parameter that determines the thermal stability and mechanical properties of a PCB. At temperatures above the Tg, the PCB material transitions from a rigid, glassy state to a softer, rubbery state. This transition can lead to deformation, warping, and degradation of the PCB’s electrical and mechanical properties. A higher Tg allows the PCB to maintain its properties at elevated temperatures, ensuring reliable performance in high-temperature environments.
3. Can high TG PCBs be used for all applications?
While high TG PCBs offer superior thermal stability and reliability, they may not be necessary or cost-effective for all applications. The choice of using a high TG PCB depends on the specific requirements of the application, such as the operating temperature range, thermal stress, mechanical demands, and reliability expectations. For applications that do not involve high temperatures or challenging environmental conditions, standard PCBs may suffice.
4. What are the cost implications of using high TG PCBs?
High TG PCBs generally come at a higher cost compared to standard PCBs due to the specialized materials and manufacturing processes involved. The cost premium can vary depending on the specific high TG material used, the complexity of the PCB design, and the manufacturing volume. However, the increased cost is often justified for applications that require enhanced thermal stability, reliability, and long-term performance, as it can lead to reduced failure rates and lower overall system costs in the long run.
5. Are there any challenges in designing with high TG PCBs?
Designing with high TG PCBs may present certain challenges compared to standard PCBs. The enhanced thermal and mechanical properties of high TG materials can impact the design considerations. For example, the different thermal expansion coefficients of high TG materials may require careful matching with other components to minimize thermal stress. High-speed or high-frequency designs may need precise control of impedance and signal integrity. Thermal management and heat dissipation also become critical considerations in high TG PCB designs. Designers should work closely with PCB manufacturers and follow established design guidelines to address these challenges effectively.
Conclusion
High TG PCBs, or PCB-TG, offer enhanced thermal stability, reliability, and mechanical strength compared to standard PCBs. With their ability to withstand higher operating temperatures and harsh environmental conditions, high TG PCBs find applications in various industries, including automotive, aerospace, military, industrial electronics, and high-power applications.
The choice of high TG material, such as FR-4 high TG, polyimide, high Tg epoxy, BT, or PTFE, depends on the specific requirements of the application. Careful consideration of manufacturing processes, thermal management, and design guidelines is necessary to ensure optimal performance and reliability of high TG PCBs.
As electronic systems continue to push the boundaries of performance and operate in increasingly challenging environments, the demand for high TG PCBs is expected to grow. By leveraging the benefits of high TG PCBs, designers and manufacturers can develop robust and reliable electronic products that can withstand the rigors of high-temperature and harsh operating conditions.
0 Comments