Introduction to PCB Boards
A Printed Circuit Board (PCB) is a fundamental component in modern electronics. It is a flat board made of insulating materials, such as fiberglass or composite epoxy, with conductive pathways etched or printed onto its surface. These conductive pathways, also known as traces, connect various electronic components, such as resistors, capacitors, and integrated circuits, to form a complete electrical circuit.
PCBs have revolutionized the electronics industry by providing a reliable, compact, and cost-effective way to mass-produce electronic devices. They are used in a wide range of applications, from simple consumer electronics to complex aerospace and military systems.
History of PCB Boards
The concept of printed circuits dates back to the early 20th century, with the first patent for a printed wire filed by Albert Hanson in 1903. However, it wasn’t until the 1940s that PCBs began to gain widespread adoption in the electronics industry.
During World War II, the United States military heavily invested in the development of PCB technology to improve the reliability and efficiency of their electronic systems. After the war, PCBs quickly found their way into consumer electronics, such as radios and televisions.
In the 1960s, the introduction of through-hole technology further advanced PCB design and manufacturing. This allowed for the use of smaller components and higher component density on the boards.
The 1980s saw the advent of surface-mount technology (SMT), which revolutionized PCB manufacturing by allowing components to be mounted directly onto the surface of the board, rather than requiring holes to be drilled for each component lead.
Today, PCBs continue to evolve with advancements in materials, manufacturing processes, and design software, enabling the creation of increasingly complex and high-performance electronic devices.
Types of PCB Boards
There are several types of PCB boards, each with its own unique characteristics and applications. The most common types include:
Single-Layer PCBs
Single-layer PCBs, also known as single-sided PCBs, have conductive traces on only one side of the insulating substrate. These boards are the simplest and most cost-effective type of PCB, making them ideal for low-complexity circuits and prototypes.
Double-Layer PCBs
Double-layer PCBs, or double-sided PCBs, have conductive traces on both sides of the insulating substrate. The two layers are connected using through-holes, which are small holes drilled through the board and plated with conductive material. Double-layer PCBs offer higher component density and more complex routing compared to single-layer boards.
Multi-Layer PCBs
Multi-layer PCBs consist of three or more conductive layers separated by insulating layers. These boards offer the highest component density and most complex routing possibilities, making them suitable for advanced electronic systems, such as smartphones, computers, and aerospace applications.
PCB Type | Layers | Complexity | Cost | Applications |
---|---|---|---|---|
Single-Layer | 1 | Low | Low | Simple circuits, prototypes |
Double-Layer | 2 | Medium | Medium | More complex circuits, commercial products |
Multi-Layer | 3+ | High | High | Advanced electronic systems, high-density designs |
Rigid PCBs
Rigid PCBs are the most common type of PCB, characterized by their sturdy, inflexible substrate material. They are typically made of fiberglass-reinforced epoxy laminate, such as FR-4. Rigid PCBs offer excellent mechanical stability and are suitable for a wide range of applications.
Flexible PCBs
Flexible PCBs, or flex PCBs, are made of thin, flexible insulating materials, such as polyimide or polyester. They can bend and fold to fit into tight spaces or conform to non-planar surfaces, making them ideal for applications that require flexibility, such as wearable electronics, medical devices, and aerospace systems.
Rigid-Flex PCBs
Rigid-flex PCBs combine the benefits of both rigid and flexible PCBs by incorporating both types of substrates into a single board. This allows for the integration of rigid sections for component mounting and flexible sections for connecting various sub-assemblies or conforming to unique packaging requirements.
PCB Manufacturing Process
The PCB manufacturing process involves several key steps, each of which plays a crucial role in the creation of a high-quality, reliable circuit board.
PCB Design
The first step in the PCB manufacturing process is the design phase. This involves creating a schematic diagram of the electronic circuit and translating it into a physical layout using PCB design software, such as Altium Designer, Eagle, or KiCad.
During the design phase, engineers must consider factors such as component placement, trace routing, signal integrity, and manufacturing constraints. The design is then reviewed and optimized to ensure it meets all functional and performance requirements.
PCB Fabrication
Once the PCB design is finalized, the fabrication process begins. This typically involves the following steps:
-
Substrate Preparation: The insulating substrate material, such as FR-4, is cut to the desired size and thickness.
-
Copper Cladding: A thin layer of copper is laminated onto one or both sides of the substrate.
-
Drilling: Holes are drilled through the board to accommodate through-hole components and vias, which are used to connect different layers of the board.
-
Patterning: The desired circuit pattern is transferred onto the copper layer using a photolithographic process. This involves applying a light-sensitive resist to the copper, exposing it to UV light through a photomask, and then developing the resist to remove the unexposed areas.
-
Etching: The exposed copper is removed using a chemical etching process, leaving only the desired circuit pattern.
-
Plating: The holes and exposed copper traces are plated with a thin layer of copper, followed by a layer of tin-lead or other protective finish to prevent oxidation and improve solderability.
-
Solder Mask Application: A protective solder mask is applied to the board, covering the copper traces and leaving only the exposed pads and holes for component soldering.
-
Silkscreen Printing: A silkscreen layer is printed onto the board to add component labels, logos, and other identifying information.
PCB Assembly
After the PCB fabrication process is complete, the board moves on to the assembly phase. This involves the following steps:
-
Solder Paste Application: A precise amount of solder paste is applied to the component pads using a stencil or screen printing process.
-
Component Placement: Surface mount components are placed onto the solder paste using a pick-and-place machine, while through-hole components are inserted manually or with the aid of automated insertion equipment.
-
Reflow Soldering: The board is passed through a reflow oven, which heats the solder paste to its melting point, allowing it to form a strong electrical and mechanical bond between the components and the board.
-
Inspection and Testing: The assembled board is visually inspected and electrically tested to ensure proper functionality and quality.
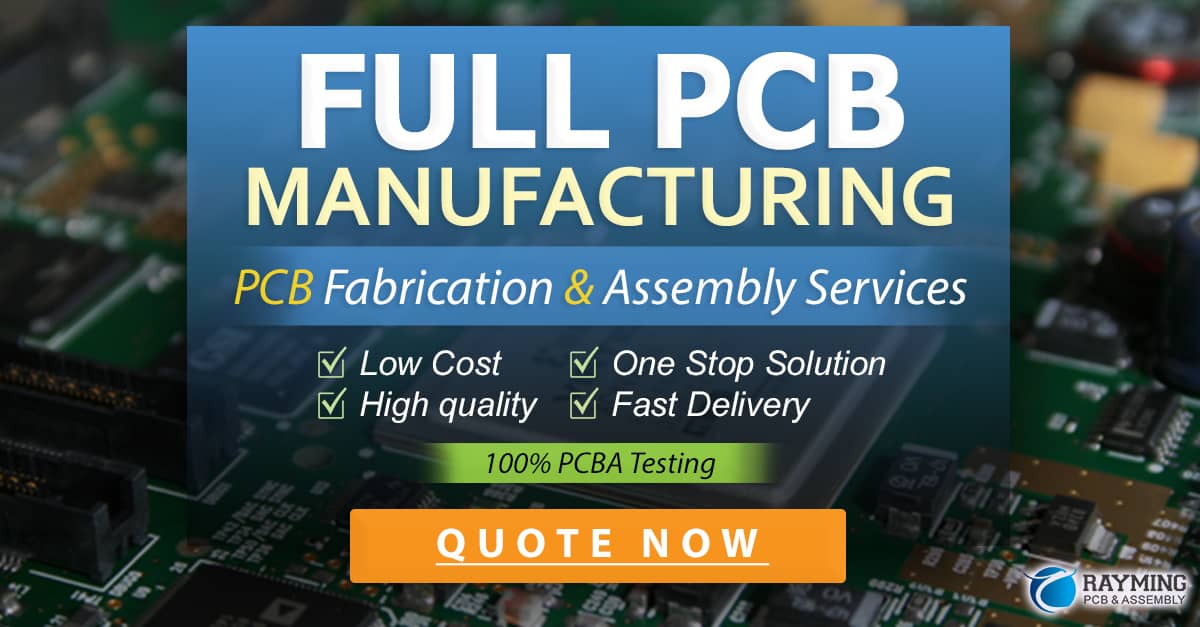
PCB Design Considerations
When designing a PCB, there are several key factors to consider to ensure optimal performance, reliability, and manufacturability.
Component Placement
Proper component placement is crucial for several reasons:
-
Signal Integrity: Components should be placed to minimize the length of critical signal paths and avoid unnecessary crossovers or vias, which can introduce noise and degrade signal quality.
-
Thermal Management: Heat-generating components, such as power regulators or processors, should be placed in a way that allows for adequate heat dissipation, either through the use of heatsinks or by providing sufficient spacing between components.
-
Mechanical Constraints: Component placement must take into account any mechanical constraints, such as the location of mounting holes, connectors, or enclosure features.
Trace Routing
Trace routing is the process of creating the conductive paths that connect components on the PCB. When routing traces, designers must consider:
-
Trace Width: The width of a trace determines its current-carrying capacity and resistance. Wider traces can handle higher currents and exhibit lower resistance, but they also take up more space on the board.
-
Trace Spacing: The spacing between traces affects the board’s signal integrity and electromagnetic compatibility (EMC). Traces that are too close together can lead to crosstalk and other unwanted interactions.
-
Vias: Vias are used to connect traces on different layers of the board. The size, number, and location of vias can impact signal integrity and manufacturing costs.
Grounding and Power Distribution
Proper grounding and power distribution are essential for ensuring the stability and performance of a PCB. Some key considerations include:
-
Ground Planes: The use of solid ground planes can help to reduce noise, improve signal integrity, and provide a low-impedance return path for currents.
-
Power Planes: Dedicated power planes can be used to distribute power evenly across the board, minimizing voltage drops and improving power supply stability.
-
Decoupling Capacitors: Decoupling capacitors should be placed close to power pins of integrated circuits to reduce noise and provide a stable power supply.
Signal Integrity
Signal integrity refers to the quality of the electrical signals transmitted through the PCB. To maintain good signal integrity, designers must consider factors such as:
-
Impedance Matching: Ensuring that the impedance of traces matches the impedance of the source and load components can help to minimize reflections and improve signal quality.
-
Crosstalk: Minimizing crosstalk between adjacent traces can be achieved through proper trace spacing, the use of ground planes, and other layout techniques.
-
Termination: Proper termination of high-speed signals can help to reduce reflections and improve signal quality.
Electromagnetic Compatibility (EMC)
EMC refers to the ability of a PCB to operate without causing or being affected by electromagnetic interference (EMI). To improve EMC, designers can:
-
Minimize Loop Areas: Reducing the area enclosed by current loops can help to minimize the board’s radiated emissions and susceptibility to external EMI.
-
Use Shielding: Enclosing sensitive components or sections of the board in a conductive shield can help to reduce EMI.
-
Filter Power Lines: Using filters on power lines can help to minimize conducted EMI and improve the board’s overall EMC performance.
PCB Testing and Inspection
After the PCB has been manufactured and assembled, it must undergo thorough testing and inspection to ensure proper functionality, reliability, and compliance with relevant standards.
Visual Inspection
Visual inspection is the first step in the testing process, involving a careful examination of the board for any obvious defects, such as:
-
Solder Bridges: Unintended connections between adjacent solder pads or traces.
-
Cold Solder Joints: Solder connections that appear dull, grainy, or incomplete.
-
Component Misalignment: Components that are not properly aligned with their pads or are rotated incorrectly.
Automated Optical Inspection (AOI)
AOI is a computer-based inspection method that uses cameras and image processing software to detect manufacturing defects, such as missing components, incorrect component placement, or solder bridging. AOI can quickly inspect a large number of boards and identify defects that may be difficult to detect through manual visual inspection.
X-Ray Inspection
X-ray inspection is used to examine solder joints and other internal structures that are not visible from the surface of the board. This technique is particularly useful for inspecting ball grid array (BGA) packages and other components with hidden connections.
In-Circuit Testing (ICT)
ICT is a method of testing individual components on the PCB by directly accessing their pins or pads using a bed-of-nails fixture. This allows for the verification of component values, polarities, and connectivity, as well as the detection of short circuits and open connections.
Functional Testing
Functional testing involves powering up the PCB and verifying that it performs its intended functions correctly. This may involve the use of automated test equipment (ATE) to apply test signals and measure responses or manual testing using oscilloscopes, logic analyzers, or other diagnostic tools.
Boundary Scan Testing
Boundary scan testing, also known as JTAG testing, is a method of testing the interconnections between integrated circuits on the PCB. This technique uses a special test access port (TAP) built into the ICs to control and observe the state of the pins, allowing for the detection of faults such as open or short circuits.
FAQ
What is the difference between a PCB and a printed wiring board (PWB)?
Technically, a PCB is a type of PWB that uses conductive traces to connect components, while a PWB can refer to any board with printed conductors, including those that use discrete wires. However, in practice, the terms PCB and PWB are often used interchangeably.
Can PCBs be recycled?
Yes, PCBs can be recycled to recover valuable materials, such as copper, gold, and silver. However, the recycling process is complex and requires specialized equipment to safely handle the hazardous substances present in some PCBs, such as lead and brominated flame retardants.
What is the difference between through-hole and surface-mount components?
Through-hole components have leads that are inserted into holes drilled in the PCB and soldered to pads on the opposite side. Surface-mount components are smaller and are soldered directly onto pads on the surface of the board. Surface-mount technology allows for higher component density and faster assembly compared to through-hole technology.
How do I choose the right PCB manufacturer?
When selecting a PCB manufacturer, consider factors such as their experience, capabilities, quality control processes, and customer support. Look for manufacturers that are certified to relevant quality standards, such as ISO 9001, and have experience working with the specific materials, technologies, and design requirements of your project. It’s also important to consider the manufacturer’s location, lead times, and pricing to ensure they align with your project goals and constraints.
What is the typical turnaround time for PCB manufacturing?
The turnaround time for PCB manufacturing can vary depending on factors such as the complexity of the design, the manufacturing processes required, and the manufacturer’s workload. Simple, single-layer PCBs can often be manufactured in as little as 24-48 hours, while more complex, multi-layer boards may take several weeks. When planning your project, be sure to communicate your timeline requirements with your chosen manufacturer and factor in additional time for shipping and any necessary revisions or updates.
Conclusion
PCBs are essential components in modern electronics, providing a reliable and efficient means of interconnecting electronic components. Understanding the types, manufacturing processes, design considerations, and testing methods associated with PCBs is crucial for anyone involved in the development or production of electronic devices.
By following best practices in PCB design, carefully selecting materials and components, and working with experienced manufacturing partners, designers and engineers can create high-quality, reliable PCBs that meet the demands of today’s increasingly complex electronic systems.
As PCB technology continues to evolve, staying up-to-date with the latest advancements and techniques will be essential for staying competitive in the fast-paced world of electronics design and manufacturing. With the knowledge and insights provided in this comprehensive guide, you’ll be well-equipped to navigate the exciting and challenging field of PCB design and manufacturing.
0 Comments