What is a PCB Substrate?
A PCB substrate is the insulating material that forms the base of a printed circuit board. It provides mechanical support and electrical insulation between the conductive copper layers. The substrate material plays a vital role in determining the PCB’s physical, thermal, and electrical properties.
Key Factors to Consider When Choosing a PCB Substrate
When selecting a PCB substrate material, several factors should be considered to ensure optimal performance and compatibility with your project requirements. These factors include:
-
Dielectric Constant (Dk): The dielectric constant measures the substrate’s ability to store electrical energy. A lower Dk value indicates better signal integrity and higher-frequency performance.
-
Dissipation Factor (Df): The dissipation factor quantifies the substrate’s energy loss due to heat generation. A lower Df value is desirable for high-frequency applications to minimize signal loss and maintain signal integrity.
-
Thermal Conductivity: Thermal conductivity determines the substrate’s ability to dissipate heat generated by components. Higher thermal conductivity helps prevent overheating and improves the PCB’s reliability.
-
Coefficient of Thermal Expansion (CTE): The CTE measures the substrate’s expansion and contraction rate with temperature changes. A close match between the substrate’s CTE and that of the components is essential to prevent mechanical stress and ensure reliability.
-
Mechanical Strength: The substrate should provide sufficient mechanical strength to withstand handling, assembly, and operational stresses.
-
Cost: The cost of the substrate material should be considered in relation to the project’s budget and the required performance characteristics.
Common Types of PCB Substrate Materials
1. FR-4 (Flame Retardant 4)
FR-4 is the most widely used PCB substrate material. It is a composite material made of woven fiberglass cloth impregnated with an epoxy resin. FR-4 offers a good balance of mechanical, electrical, and thermal properties at a reasonable cost.
Key characteristics of FR-4:
– Dielectric Constant (Dk): 4.2 – 4.5
– Dissipation Factor (Df): 0.02
– Thermal Conductivity: 0.3 W/mK
– Tg (Glass Transition Temperature): 130°C – 140°C
– Suitable for general-purpose applications and low-to-medium frequency designs
2. High Tg FR-4
High Tg FR-4 is an enhanced version of the standard FR-4 material. It offers improved thermal stability and higher glass transition temperature (Tg), making it suitable for applications that require better heat resistance and reliability.
Key characteristics of High Tg FR-4:
– Dielectric Constant (Dk): 4.2 – 4.5
– Dissipation Factor (Df): 0.02
– Thermal Conductivity: 0.3 W/mK
– Tg (Glass Transition Temperature): 170°C – 180°C
– Suitable for automotive, aerospace, and high-temperature applications
3. Rogers PCB Laminates
Rogers Corporation offers a range of high-performance PCB Laminates designed for demanding RF, microwave, and high-speed digital applications. These laminates provide excellent electrical properties, low loss, and controlled dielectric constant.
Some popular Rogers PCB laminates include:
a. RO4000 Series:
– Dielectric Constant (Dk): 3.3 – 3.7
– Dissipation Factor (Df): 0.0027 – 0.0037
– Thermal Conductivity: 0.6 – 0.7 W/mK
– Suitable for high-frequency, low-loss applications up to 30 GHz
b. RT/duroid 5870-5880:
– Dielectric Constant (Dk): 2.33 – 2.55
– Dissipation Factor (Df): 0.0005 – 0.0012
– Thermal Conductivity: 0.2 W/mK
– Suitable for microwave and millimeter-wave applications up to 100 GHz
c. RO3000 Series:
– Dielectric Constant (Dk): 3.0 – 3.5
– Dissipation Factor (Df): 0.0010 – 0.0030
– Thermal Conductivity: 0.5 W/mK
– Suitable for high-frequency, low-loss applications up to 40 GHz
4. Polyimide
Polyimide is a high-performance polymer material known for its excellent thermal stability, mechanical strength, and chemical resistance. It is commonly used in flexible and rigid-Flex PCBs.
Key characteristics of Polyimide:
– Dielectric Constant (Dk): 3.4 – 3.5
– Dissipation Factor (Df): 0.002 – 0.003
– Thermal Conductivity: 0.2 W/mK
– Tg (Glass Transition Temperature): 260°C – 350°C
– Suitable for high-temperature, aerospace, and military applications
5. PTFE (Polytetrafluoroethylene)
PTFE, also known as Teflon, is a fluoropolymer material with excellent electrical properties, low dielectric constant, and low dissipation factor. It is commonly used in high-frequency and microwave applications.
Key characteristics of PTFE:
– Dielectric Constant (Dk): 2.1
– Dissipation Factor (Df): 0.0002 – 0.0003
– Thermal Conductivity: 0.2 W/mK
– Suitable for high-frequency, low-loss applications up to 100 GHz
6. Ceramic Substrates
Ceramic substrates, such as alumina (Al2O3) and aluminum nitride (AlN), offer excellent thermal conductivity, high mechanical strength, and good electrical insulation. They are commonly used in high-power, high-frequency, and high-temperature applications.
Key characteristics of Ceramic Substrates:
a. Alumina (Al2O3):
– Dielectric Constant (Dk): 9.8 – 10.2
– Dissipation Factor (Df): 0.0001 – 0.0002
– Thermal Conductivity: 20 – 30 W/mK
– Suitable for high-power, high-frequency, and high-temperature applications
b. Aluminum Nitride (AlN):
– Dielectric Constant (Dk): 8.6
– Dissipation Factor (Df): 0.001 – 0.002
– Thermal Conductivity: 170 – 200 W/mK
– Suitable for high-power, high-frequency, and high-temperature applications requiring superior thermal management
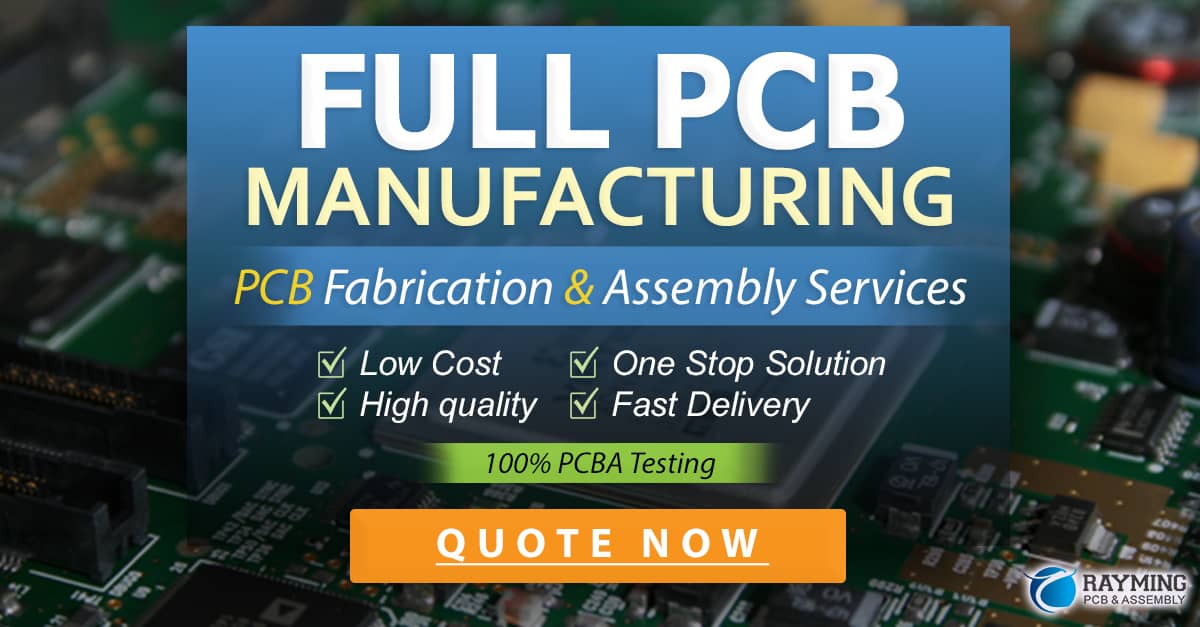
Comparison of PCB Substrate Materials
Material | Dielectric Constant (Dk) | Dissipation Factor (Df) | Thermal Conductivity (W/mK) | Typical Applications |
---|---|---|---|---|
FR-4 | 4.2 – 4.5 | 0.02 | 0.3 | General-purpose, low-to-medium frequency |
High Tg FR-4 | 4.2 – 4.5 | 0.02 | 0.3 | Automotive, aerospace, high-temperature |
RO4000 Series | 3.3 – 3.7 | 0.0027 – 0.0037 | 0.6 – 0.7 | High-frequency, low-loss up to 30 GHz |
RT/duroid 5870-5880 | 2.33 – 2.55 | 0.0005 – 0.0012 | 0.2 | Microwave and millimeter-wave up to 100 GHz |
RO3000 Series | 3.0 – 3.5 | 0.0010 – 0.0030 | 0.5 | High-frequency, low-loss up to 40 GHz |
Polyimide | 3.4 – 3.5 | 0.002 – 0.003 | 0.2 | High-temperature, aerospace, military |
PTFE | 2.1 | 0.0002 – 0.0003 | 0.2 | High-frequency, low-loss up to 100 GHz |
Alumina (Al2O3) | 9.8 – 10.2 | 0.0001 – 0.0002 | 20 – 30 | High-power, high-frequency, high-temperature |
Aluminum Nitride (AlN) | 8.6 | 0.001 – 0.002 | 170 – 200 | High-power, high-frequency, high-temperature, superior thermal management |
Frequently Asked Questions (FAQ)
-
Q: What is the most commonly used PCB substrate material?
A: FR-4 is the most widely used PCB substrate material due to its good balance of mechanical, electrical, and thermal properties at a reasonable cost. -
Q: Which PCB substrate materials are suitable for high-frequency applications?
A: For high-frequency applications, materials like Rogers PCB laminates (RO4000 Series, RT/duroid 5870-5880, RO3000 Series) and PTFE are commonly used due to their low dielectric constant, low dissipation factor, and excellent electrical properties. -
Q: What are the advantages of using ceramic substrates like alumina and aluminum nitride?
A: Ceramic substrates, such as alumina and aluminum nitride, offer excellent thermal conductivity, high mechanical strength, and good electrical insulation. They are suitable for high-power, high-frequency, and high-temperature applications. Aluminum nitride, in particular, provides superior thermal management capabilities. -
Q: Can polyimide be used for flexible PCBs?
A: Yes, polyimide is commonly used in flexible and rigid-flex PCBs due to its excellent thermal stability, mechanical strength, and chemical resistance. -
Q: What factors should I consider when choosing a PCB substrate material for my project?
A: When selecting a PCB substrate material, consider factors such as dielectric constant, dissipation factor, thermal conductivity, coefficient of thermal expansion, mechanical strength, and cost. Evaluate these factors in relation to your project’s specific requirements, including the operating frequency, temperature range, power handling, and budget constraints.
Conclusion
Choosing the right PCB substrate material is essential for the success of your project. By understanding the key characteristics and properties of different substrate materials, you can make an informed decision that meets your specific requirements. Whether you need a general-purpose material like FR-4, a high-performance laminate for RF and microwave applications, or a thermally conductive ceramic substrate for high-power designs, there is a suitable PCB substrate material available to fit your needs.
Consider factors such as dielectric constant, dissipation factor, thermal conductivity, and mechanical strength when selecting a substrate material. Additionally, keep in mind the operating frequency, temperature range, and power handling requirements of your application.
By carefully evaluating your project requirements and comparing the properties of various PCB substrate materials, you can ensure optimal performance, reliability, and cost-effectiveness for your PCB design. Remember to consult with PCB Manufacturers and material suppliers for more detailed information and guidance specific to your project.
0 Comments