What are PCB Drill Sizes?
PCB drill sizes refer to the diameter of the holes that are drilled into a printed circuit board. These holes are used to mount components, create vias for electrical connections between layers, and provide mechanical support for the board. The drill sizes are typically expressed in either inches or millimeters, with the most common sizes ranging from 0.3mm to 6.35mm (0.012″ to 0.25″).
Common PCB Drill Sizes
Drill Size (Inch) | Drill Size (mm) | Application |
---|---|---|
0.012″ | 0.3048 | Ultra-fine pitch components, high-density boards |
0.016″ | 0.4064 | Fine-pitch components, dense layouts |
0.020″ | 0.508 | Standard component leads, vias |
0.024″ | 0.6096 | Larger component leads, connectors |
0.028″ | 0.7112 | Power components, mounting holes |
0.032″ | 0.8128 | Mechanical support, grounding |
0.040″ | 1.016 | Larger connectors, mounting holes |
0.050″ | 1.27 | High-current connectors, heavy-duty components |
Factors Affecting PCB Drill Size Selection
Several factors influence the choice of PCB drill sizes, including:
- Component requirements
- Current carrying capacity
- Board thickness
- Manufacturing capabilities
- Cost considerations
Component Requirements
The component requirements are the primary factor in determining the appropriate PCB drill sizes. Different components have varying lead sizes and pitches, which dictate the hole sizes needed to accommodate them. For example, surface-mount devices (SMDs) typically require smaller drill sizes compared to through-hole components.
Current Carrying Capacity
The current carrying capacity of the holes is another crucial factor in selecting PCB drill sizes. Larger drill sizes allow for higher current carrying capacity, as they can accommodate thicker copper plating inside the holes. This is particularly important for power supply connections and high-current applications.
Board Thickness
The thickness of the PCB also influences the choice of drill sizes. Thicker boards require larger drill sizes to maintain the aspect ratio (hole depth to diameter ratio) within acceptable limits. This ensures the structural integrity of the board and prevents issues such as drill breakage or poor copper plating inside the holes.
Manufacturing Capabilities
The manufacturing capabilities of the PCB fabricator play a significant role in determining the available drill sizes. Some manufacturers may have limitations on the minimum and maximum drill sizes they can produce, as well as the tolerances they can achieve. It is essential to consult with the fabricator to ensure that the desired drill sizes are within their capabilities.
Cost Considerations
Cost is always a factor in PCB design and manufacturing. Smaller drill sizes and tighter tolerances generally increase the manufacturing cost, as they require more precise equipment and skilled operators. Designers must balance the need for smaller drill sizes with the cost implications to find an optimal solution.
PCB Drill Size Tolerances
PCB drill size tolerances are the acceptable variations in the diameter of the drilled holes. These tolerances are necessary to account for the inherent variability in the drilling process and ensure that the holes are within the specified limits.
The typical drill size tolerances are:
Drill Size Range (Inch) | Tolerance (Inch) |
---|---|
0.012″ – 0.020″ | ±0.002″ |
0.020″ – 0.060″ | ±0.003″ |
0.060″ – 0.100″ | ±0.004″ |
0.100″ – 0.250″ | ±0.005″ |
It is essential to consider these tolerances when designing the PCB and specifying the drill sizes. The tolerances should be accounted for in the design to ensure proper fit and functionality of the components.
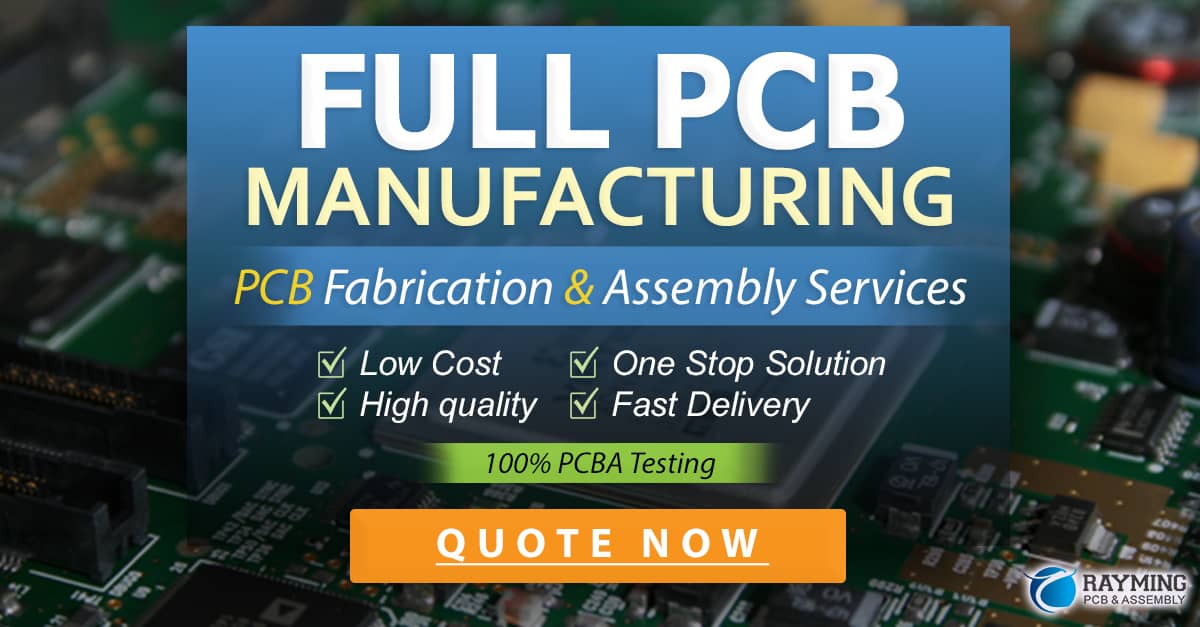
Aspect Ratio Considerations
The aspect ratio is the ratio of the hole depth to its diameter. It is an important consideration in PCB drill size selection, as it affects the manufacturability and reliability of the board.
A high aspect ratio (deep holes with small diameters) can lead to issues such as:
- Difficulty in drilling the holes accurately
- Poor copper plating uniformity inside the holes
- Increased risk of drill breakage
- Reduced mechanical strength of the board
To mitigate these issues, it is recommended to keep the aspect ratio within the following limits:
Board Thickness (Inch) | Maximum Aspect Ratio |
---|---|
0.062″ or less | 8:1 |
0.063″ – 0.093″ | 10:1 |
0.094″ – 0.124″ | 12:1 |
0.125″ or more | 14:1 |
By adhering to these aspect ratio guidelines, designers can ensure that the PCB can be manufactured reliably and with high quality.
Special Considerations for High-Density PCBs
High-density PCBs, such as those used in smartphones, wearables, and other compact electronic devices, present unique challenges in terms of drill sizes. These boards often require ultra-fine pitch components and high-density interconnects, which necessitate the use of smaller drill sizes.
Some key considerations for high-density PCBs include:
-
Use of microvias: Microvias are small, laser-drilled holes that provide interconnections between layers in high-density boards. They typically have diameters ranging from 0.05mm to 0.15mm and can be stacked to create complex routing patterns.
-
Reduced Annular Ring: The annular ring is the copper area surrounding the drilled hole. In high-density PCBs, the annular ring is often reduced to accommodate smaller drill sizes and tighter spacing between holes. This requires precise drilling and alignment to maintain the integrity of the connections.
-
Specialized manufacturing processes: High-density PCBs often require specialized manufacturing processes, such as laser drilling, plasma etching, and additive manufacturing techniques. These processes enable the creation of smaller features and tighter tolerances compared to traditional mechanical drilling.
-
Increased cost: The complexity and precision required for high-density PCBs often result in higher manufacturing costs compared to standard PCBs. Designers must carefully balance the need for miniaturization with the cost implications to ensure the viability of the final product.
Frequently Asked Questions (FAQ)
-
What is the most common PCB drill size?
The most common PCB drill size is 0.8mm (0.031″), which is suitable for a wide range of components and applications. -
Can I use different drill sizes on the same PCB?
Yes, it is common to use different drill sizes on the same PCB to accommodate various components and connectors. However, it is essential to minimize the number of different drill sizes to simplify the manufacturing process and reduce costs. -
How do I choose the appropriate drill size for my PCB?
To choose the appropriate drill size, consider factors such as component requirements, current carrying capacity, board thickness, manufacturing capabilities, and cost. Consult with your PCB fabricator to ensure that your chosen drill sizes are within their capabilities. -
What is the minimum drill size that can be achieved in PCB manufacturing?
The minimum drill size depends on the capabilities of the PCB fabricator. Some advanced manufacturers can produce drill sizes as small as 0.1mm (0.004″), but this requires specialized equipment and processes. The most common minimum drill size is around 0.3mm (0.012″). -
How do drill size tolerances affect the design of my PCB?
Drill size tolerances should be accounted for in the PCB design to ensure proper fit and functionality of the components. When designing the PCB, consider the worst-case scenario (i.e., the maximum hole size) to ensure that the components will fit even if the drilled holes are at the upper end of the tolerance range.
Conclusion
PCB drill sizes are a critical aspect of PCB design and manufacturing. Understanding the factors that influence drill size selection, such as component requirements, current carrying capacity, board thickness, manufacturing capabilities, and cost, is essential for creating reliable and high-quality PCBs.
By considering drill size tolerances, aspect ratios, and special requirements for high-density PCBs, designers can ensure that their boards are manufacturable and will perform as intended. Collaborating closely with PCB Fabricators and staying up-to-date with the latest manufacturing technologies and best practices can help optimize the design process and achieve the best possible results.
As PCB technology continues to evolve, with the increasing demand for miniaturization and high-performance devices, the importance of understanding and properly selecting PCB drill sizes will only grow. By mastering this crucial aspect of PCB design, engineers and manufacturers can create innovative, reliable, and cost-effective electronic products that meet the needs of today’s rapidly changing market.
0 Comments