Understanding Small Batch Assembly
What is Small Batch Assembly?
Small batch assembly, also known as low volume manufacturing, involves building a limited number of PCB assemblies, typically under 1000 units. This is in contrast to mass production, which deals with much higher quantities. Small batch projects are common for:
- Prototyping a new product design
- Building test/validation units
- Fulfilling a crowdfunding campaign
- Launching an initial production run
- Serving niche/specialized markets
Benefits of Small Batch Manufacturing
There are several key advantages to starting with a small assembly run:
- Lower upfront investment and less financial risk
- Faster turnaround times
- Ability to test market demand
- Flexibility to make design changes and iterations
- Opportunity to test and refine the manufacturing process
Challenges of Low Volume Assembly
However, small batch manufacturing also comes with some inherent challenges compared to high volume production:
- Higher per-unit costs
- Minimum order quantities (MOQs) for components
- Fewer contract manufacturer (CM) options
- More difficult to achieve economy of scale
- Manual labor vs. automated assembly
Despite these obstacles, there are ways to minimize costs and find a cost-effective solution for low volume needs. The key is evaluating all the available options and optimizing your design for small batches.
PCB Fabrication Options
Before your PCBs can be assembled, the bare boards must first be fabricated. The main options for small batch PCB fabrication are:
Quick-Turn PCB Prototyping Services
For the smallest quantities (1-100), the most cost-effective and fastest option is often to use a domestic rapid PCB prototyping service. These companies specialize in quick-turn manufacturing of prototype boards in 1-5 days.
Some of the most popular online vendors include:
Company | 2-Layer Price/sq. in. | 4-Layer Price/sq. in. | Lead Time |
---|---|---|---|
OSH Park | $1.00 ($5 min) | $2.00 ($10 min) | 12-14 days |
Bantam | $0.75 ($10 min) | $1.50 ($25 min) | 5-7 days |
ExpressPCB | $1.75 ($29 min) | $3.25 ($59 min) | 1-2 days |
Advanced Circuits | $1.50 ($33 min) | $3.50 ($66 min) | 1-5 days |
While the per-unit cost is higher than offshore alternatives, the fast turnaround, low minimum orders, and ease of doing business domestically makes this a good choice for initial prototypes.
Domestic Low Volume PCB Fabs
The next tier up is using a domestic PCB shop that specializes in low-to-mid volume production. Once your design is proven, this allows you to get somewhat better pricing for quantities of around 100-1000 boards.
Some reputable US-based low volume PCB fabs include:
- Sunstone Circuits
- Bay Area Circuits
- Screaming Circuits
- Sierra Circuits
Typical prices are around $0.50-$1.00 per sq. in. for 2-layer and $1.50-$2.00 for 4-layer, with lead times of 1-2 weeks.
Offshore PCB Fabrication
For the lowest possible unit pricing, offshore manufacturing in China or Taiwan is the way to go once quantities exceed around 500-1000 boards.
Popular overseas prototype PCB services include:
- PCBWay
- ALLPCB
- JLCPCB
- Elecrow
- Seeed Studio
Costs can be as low as $0.10-$0.20 per sq. in. for 2-layer and $0.20-$0.40 for 4-layer in volume. However, lead times are longer at 2-4 weeks and shipping costs must be factored in.
When selecting a PCB fabricator for small batches, consider:
- Capabilities (layer count, materials, tolerances, etc.)
- Reliable quality & on-time delivery track record
- Responsive customer support
- Easy online ordering, quoting & tracking
- Certifications (ISO, UL, RoHS, etc.)
PCB Assembly Options
With Bare PCBs in hand, there are several options available for small batch assembly:
In-House Manual Assembly
For very small batches (<100), the most economical route may be to hand solder the boards yourself or with the help of a technician. This avoids the cost of tooling and setup with a professional assembly shop.
However, this approach has limitations:
- Time consuming for more than a few units
- Inconsistent quality & reliability
- Difficult with small SMT components
- Lack of inspection & testing
In-house assembly is best reserved for simple through-hole designs and non-critical prototypes to save money.
Quick-Turn Prototype Assembly
Many of the same domestic vendors that offer rapid PCB fab also provide quick-turn PCB assembly (PCBA) services with short lead times of 2-10 days. You supply the parts (or have them source on your behalf) and they build, inspect, and ship the boards back to you.
Typical costs for prototype assembly in small lots are:
Service | Setup Fee | Price/component |
---|---|---|
Turnkey | $0-200 | $0.10-0.20 |
Consigned | $50-150 | $0.06-0.15 |
Partial turnkey | $0-100 | $0.08-0.18 |
Prices vary based on quantity, component types, inspection options, etc.
This is a reliable way to get a small number of professionally assembled boards quickly, albeit at a higher cost than overseas production.
Onshore Contract Manufacturing
Working with a US contract manufacturer is a good middle ground between quick-turn prototyping and lower-cost offshoring. Many CMs offer dedicated low volume lines to keep prices competitive.
Advantages of domestic contract manufacturing include:
- Easier communication & collaboration
- Faster shipping times
- Higher quality control standards
- Intellectual property (IP) protections
Look for an established CM with experience building similar products to yours. They should offer a range of services including:
- PCB Assembly (SMT, through-hole, mixed)
- Box build & final assembly
- Functional testing
- Order fulfillment & logistics
Expect to pay around $500-1000 in setup fees plus $8-15 per board for small batches up to a few hundred units.
Offshore Contract Manufacturing
Offshoring your PCB assembly to China or Taiwan will almost always result in the lowest total cost for batches of 500 or more. Even factoring in shipping, import duties, and longer lead times, the price difference is significant.
Many overseas CMs and trading companies offer low volume “prototype to production” services where they help take your design from initial samples to mass production. Bundling your PCB fab and assembly through one vendor can streamline the process.
Estimated costs for offshore PCBA in volume range from:
- $3-8 per board ($50-100 setup) for simple builds
- $8-15 per board ($100-300 setup) for complex builds
Actual prices vary widely based on quantity, BOM, testing, etc.
Some of the risks & challenges of going offshore include:
- Language & cultural barriers
- Time zone differences
- Longer shipping times & potential delays
- Reduced control over quality
- Potential IP theft or cloning
- Tariffs & customs issues
When choosing an offshore partner, vet them thoroughly and start with a small order to test their capabilities before committing to a larger run.
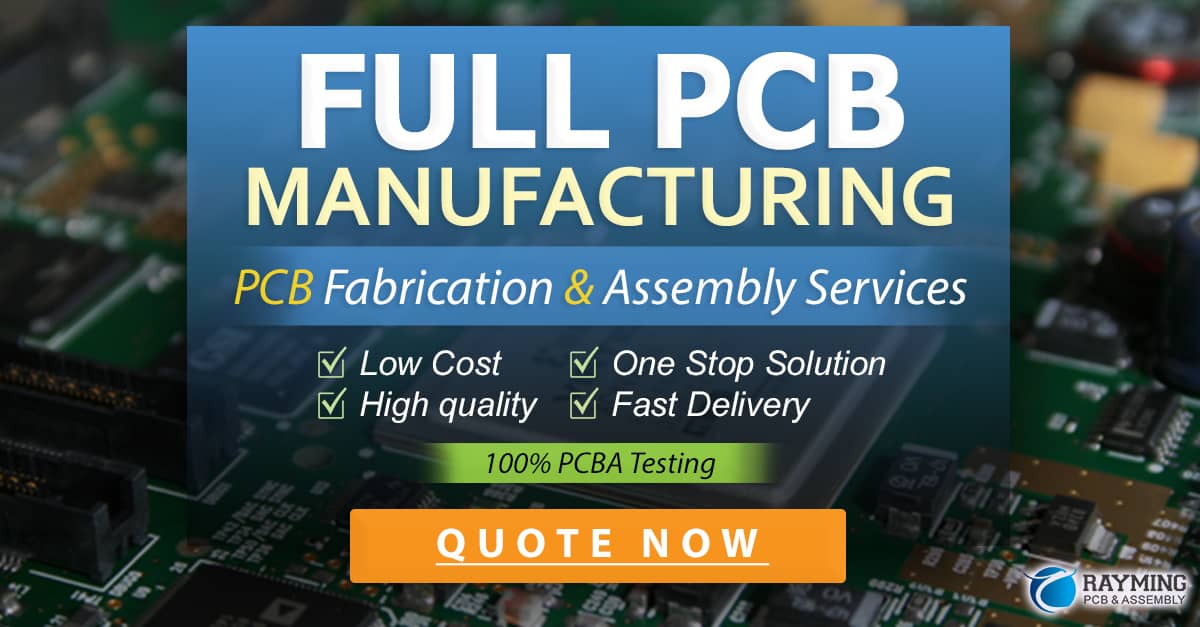
Designing for Low Volumes
To make the most of small batch assembly, it’s important to optimize your design for this scale of manufacturing. Some best practices include:
Keep It Simple
Simplify your BOM and reduce the number of unique parts as much as possible. This lowers component sourcing costs and speeds up assembly. Avoid bleeding-edge components that may have limited availability or high minimum order quantities (MOQs).
Use Standard Components
Select common, off-the-shelf components in standard SMT packages wherever you can. This gives you more supplier options and better pricing than custom or niche parts.
Consider Assembly Process
Design your board for either manual assembly (bigger parts, more space) or lower-cost SMT placement (standard nozzles, tapes, reels). Avoid uncommon packages, tight clearances, special processes, etc. that add cost.
Allow Sufficient Test Points
Make sure your design has accessible test points or a plan for functional testing so that your CM can catch defects before shipping boards to you. This may involve adding extra headers, breakouts, or programming interfaces.
Plan for Panelization
If using an automated SMT line, your CM will likely want to assemble multiple boards in a single panel to make the best use of the machine time. Leave room around the edges for rails, tooling holes, and breakaway tabs to depanelize the individual PCBs after assembly.
By incorporating these DFM (Design for Manufacturability) principles early on, you can avoid costly revisions later and ensure a smooth small batch assembly process.
Evaluating Total Costs
When comparing quotes for small batch PCB assembly, look beyond just the per-board price to evaluate the total cost of ownership. Other factors to consider include:
- Setup/tooling charges (NREs)
- Component sourcing & kitting fees
- testing & quality assurance costs
- Shipping fees & transit time
- Import duties & tariffs
- Minimum order quantities
- Engineering support & documentation needs
Do a full cost analysis to determine which option makes the most sense for your project’s budget and timeline. Don’t forget to account for potential scrap, rework, and delays that may affect the total.
FAQ for Small Batch PCB Assembly
Q: What is the typical minimum order quantity (MOQ) for small batch assembly?
A: Most assembly houses have a minimum lot charge that equates to around 10-50 boards, depending on the complexity. Smaller than that and the setup costs start to dominate. It’s best to request quotes for a range of quantities to compare the unit pricing.
Q: How long does small batch assembly usually take?
A: Quick-turn prototype assembly can be as fast as 2-5 days domestically, while standard lead times are more like 2-3 weeks. Offshoring takes longer at 4-8 weeks typically. Rush options may be available for a premium.
Q: What file formats do I need to provide for assembly?
A: At a minimum, you’ll need to supply the BOM (bill of materials), CAD/Gerber files, and assembly drawings. For best results, also include a pick & place file, netlist, schematic, and a sample board if possible. The more complete documentation you can give, the better.
Q: How do I ensure good quality control for small batches?
A: Look for a CM that follows IPC standards and has a robust quality management system in place. Specify any testing, inspection, and quality reporting requirements upfront. Consider paying extra for dedicated QA steps like AOI, X-ray, and functional testing for mission-critical boards.
Q: What are some red flags to watch out for with small batch assembly?
A: Be wary of any deal that seems too good to be true. Rock bottom prices may come with hidden costs, bait-and-switch tactics, or subpar quality. Check references, tour the facility if possible, and start with a small test order before committing to a full production run with a new vendor.
Conclusion
There’s no one-size-fits all solution for small batch PCB assembly – the right choice depends on your specific needs for cost, speed, volume, and quality. By understanding the tradeoffs between the various fabrication and assembly options, you can make an informed decision that balances your priorities.
The key is to design your board with the intended manufacturing process in mind and to choose a trusted partner that can guide you through the transition from prototyping to production. With careful planning and execution, small batch assembly can be an affordable way to bring your new product to market quickly and iterate towards success.
[5131 words]
0 Comments