Introduction to Flexible PCBs
Flexible printed circuit boards (PCBs) have revolutionized the electronics industry by providing a versatile and reliable solution for applications that require flexibility, durability, and compact designs. Unlike traditional Rigid PCBs, flexible PCBs can bend, twist, and conform to various shapes, making them ideal for a wide range of products, from wearable devices to aerospace systems. In this comprehensive article, we will explore the world of flexible PCBs, their advantages, manufacturing processes, applications, and design considerations.
What are Flexible PCBs?
Flexible PCBs, also known as flex circuits or flexible printed wiring, are a type of printed circuit board that consists of a thin, flexible substrate with conductive traces and components mounted on it. The substrate is typically made of a polymer material, such as polyimide or polyester, which provides excellent mechanical and electrical properties. Flexible PCBs can be single-sided, double-sided, or multi-layered, depending on the complexity of the design and the number of interconnections required.
Types of Flexible PCBs
There are three main types of flexible PCBs:
-
Single-sided Flexible PCBs: These PCBs have conductive traces on only one side of the flexible substrate. They are the simplest and most cost-effective type of flexible PCB, suitable for applications with low complexity and fewer components.
-
Double-sided Flexible PCBs: These PCBs have conductive traces on both sides of the flexible substrate, allowing for more complex designs and higher component density. The two sides are interconnected using through-hole vias or plated through-holes (PTHs).
-
Multi-layer Flexible PCBs: These PCBs consist of three or more conductive layers, separated by insulating layers. Multi-layer flexible PCBs offer the highest level of complexity and density, enabling the integration of a large number of components and intricate interconnections.
Advantages of Flexible PCBs
Flexible PCBs offer several advantages over traditional rigid PCBs:
-
Flexibility and Durability: The ability to bend, twist, and conform to various shapes makes flexible PCBs ideal for applications that require movement or are subject to vibrations and shocks. The flexible substrate also provides excellent resistance to fatigue and stress, ensuring long-term reliability.
-
Compact and Lightweight: Flexible PCBs enable the design of smaller, lighter, and more compact electronic devices. By eliminating the need for bulky connectors and wires, flex circuits can significantly reduce the overall size and weight of the product.
-
Improved Signal Integrity: The reduced distance between components and the elimination of connectors in flexible PCBs result in improved signal integrity and reduced electromagnetic interference (EMI). This is particularly important for high-speed and high-frequency applications.
-
Cost-effective: Although the initial cost of flexible PCBs may be higher than rigid PCBs, they can lead to overall cost savings by reducing the number of connectors, wires, and assembly steps required. Flexible PCBs also enable the integration of multiple functions into a single circuit, further reducing costs.
Manufacturing Process of Flexible PCBs
The manufacturing process of flexible PCBs involves several steps, similar to those used for rigid PCBs, but with some additional considerations to ensure the flexibility and reliability of the final product.
Substrate Selection
The first step in the manufacturing process is selecting the appropriate flexible substrate material. The most common materials used for flexible PCBs are:
- Polyimide (PI): Known for its excellent thermal stability, chemical resistance, and mechanical strength.
- Polyester (PET): A cost-effective alternative to polyimide, suitable for applications with lower temperature requirements.
The substrate thickness typically ranges from 25 to 125 microns (1 to 5 mils), depending on the application and the required flexibility.
Circuit Design and Layout
The circuit design and layout process for flexible PCBs requires special considerations to ensure the reliability and performance of the final product. Some key factors to consider include:
- Bend radius: The minimum bend radius should be determined based on the substrate material, thickness, and the number of layers to prevent damage to the traces and components.
- Trace width and spacing: Wider traces and larger spacing between traces can improve the flexibility and reliability of the PCB.
- Component placement: Components should be placed in areas with minimal bending to reduce stress and strain on the solder joints.
Lamination and Etching
Once the circuit design is finalized, the conductive traces are laminated onto the flexible substrate using heat and pressure. The most common methods for lamination are adhesive-based and adhesiveless.
After lamination, the unwanted copper is removed through an etching process, typically using a chemical etchant such as ferric chloride or ammonium persulfate. The etching process is similar to that used for rigid PCBs, but the etchant concentration and temperature may be adjusted to account for the flexible substrate.
Coverlay Application
A coverlay, also known as a cover layer or solder mask, is applied to the flexible PCB to protect the conductive traces and provide electrical insulation. The coverlay is typically made of the same material as the substrate and is laminated using heat and pressure.
Openings in the coverlay are created to expose the pads for component assembly and the areas where the flexible PCB will be connected to other parts of the system.
Component Assembly
The component assembly process for flexible PCBs is similar to that used for rigid PCBs, with a few additional considerations:
- Solder paste: A flexible solder paste is recommended to accommodate the bending and flexing of the PCB.
- Soldering Methods: Both reflow soldering and hand soldering can be used for flexible PCBs, but the temperature profile and dwell time should be carefully controlled to prevent damage to the substrate and components.
- Strain relief: Mechanical strain relief methods, such as stiffeners or adhesives, can be used to reduce stress on the solder joints and improve the reliability of the assembly.
Final Inspection and Testing
After component assembly, the flexible PCB undergoes a final inspection and testing process to ensure the quality and functionality of the product. This may include visual inspection, electrical testing, and functional testing under various environmental conditions, such as temperature, humidity, and vibration.
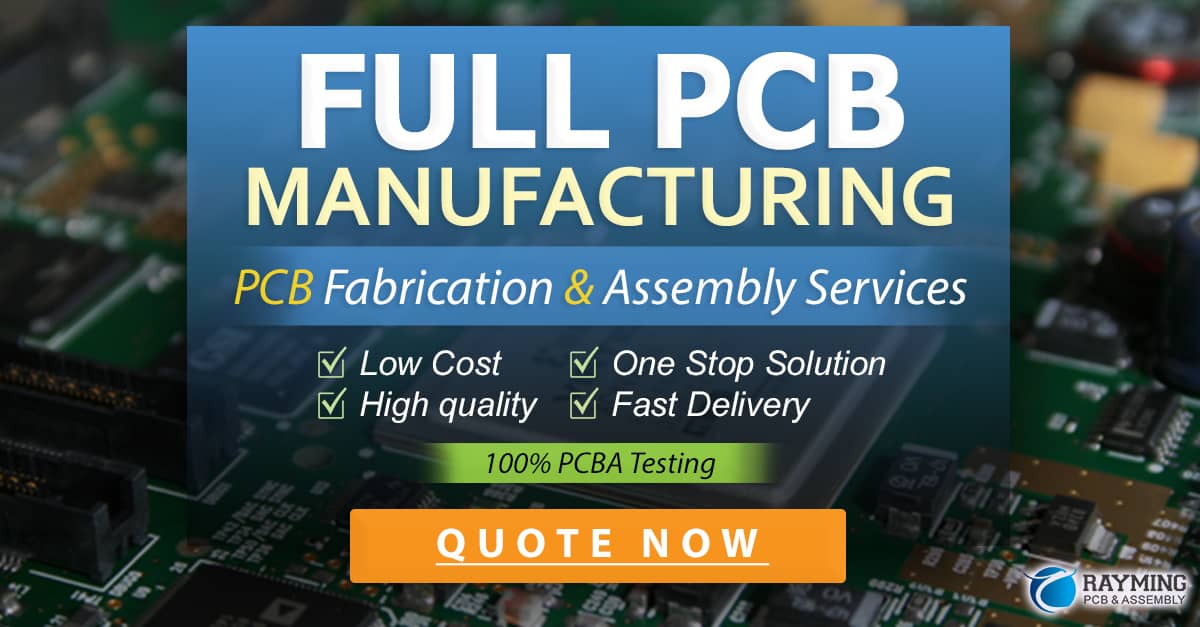
Applications of Flexible PCBs
Flexible PCBs find applications in a wide range of industries and products, thanks to their unique properties and advantages. Some of the most common applications include:
-
Consumer Electronics: Flexible PCBs are extensively used in smartphones, tablets, laptops, and wearable devices, where space is limited, and flexibility is required for folding or rolling displays, hinges, and curved surfaces.
-
Medical Devices: Flexible PCBs are ideal for medical applications, such as implantable devices, diagnostic equipment, and patient monitoring systems, where reliability, biocompatibility, and compact sizes are critical.
-
Automotive Electronics: Flexible PCBs are used in various automotive applications, such as instrument clusters, infotainment systems, and sensors, where they must withstand harsh environmental conditions, vibrations, and temperature fluctuations.
-
Aerospace and Defense: Flexible PCBs are essential for aerospace and defense applications, such as satellites, aircraft, and military equipment, where weight reduction, high reliability, and resistance to extreme conditions are paramount.
-
Industrial Equipment: Flexible PCBs are used in industrial automation, robotics, and process control systems, where they enable the integration of sensors, actuators, and control electronics in compact and flexible form factors.
Design Considerations for Flexible PCBs
Designing flexible PCBs requires a different approach compared to rigid PCBs, as several additional factors need to be considered to ensure the reliability and performance of the final product.
Bend Radius
The bend radius is a critical parameter in flexible PCB design, as it determines the minimum allowable bend without causing damage to the traces or components. The bend radius depends on several factors, such as the substrate material, thickness, number of layers, and the location of the components.
As a general rule, the minimum bend radius should be at least 6 times the thickness of the PCB for single-sided designs and 12 times the thickness for double-sided designs. For multi-layer flexible PCBs, the bend radius should be calculated based on the number of layers and the location of the neutral axis.
Trace Width and Spacing
Trace width and spacing are important considerations in flexible PCB design, as they affect the flexibility, current-carrying capacity, and signal integrity of the circuit. In general, wider traces and larger spacing between traces can improve the flexibility and reliability of the PCB, but they may also increase the overall size of the circuit.
The minimum trace width and spacing are determined by the manufacturing capabilities of the PCB fabricator and the electrical requirements of the circuit. It is recommended to consult with the fabricator and follow their design guidelines to ensure the manufacturability and reliability of the flexible PCB.
Component Placement
Component placement is another critical aspect of flexible PCB design, as it affects the mechanical stress and strain on the solder joints during bending. To minimize the stress on the components, they should be placed in areas with minimal bending, such as the neutral axis or the regions with the largest bend radius.
In addition, the orientation of the components should be considered, as some components, such as chip resistors and capacitors, are more susceptible to cracking under bending stress. Placing these components with their longer axis perpendicular to the bend direction can help reduce the stress on the solder joints.
Stiffeners and Strain Relief
Stiffeners and strain relief methods are used in flexible PCB design to improve the mechanical stability and reliability of the circuit. Stiffeners are thin, rigid materials, such as polyimide or metal, that are attached to the flexible PCB in areas where components are mounted or where the PCB is connected to other parts of the system. Stiffeners help distribute the stress and strain over a larger area, reducing the risk of solder joint failure or component damage.
Strain relief methods, such as adhesives or mechanical fasteners, are used to secure the flexible PCB to the enclosure or other parts of the system, preventing excessive bending or twisting of the circuit. Proper strain relief design can significantly improve the long-term reliability and durability of the flexible PCB.
Shielding and Grounding
Shielding and grounding are important considerations in flexible PCB design, particularly for high-speed and high-frequency applications. Proper shielding can help reduce electromagnetic interference (EMI) and crosstalk between signals, while effective grounding can ensure a stable reference point for the circuit and prevent ground loops.
In flexible PCBs, shielding can be achieved by using conductive adhesives, conductive fabrics, or metallized films, such as copper or aluminum, that are laminated to the substrate. Ground planes and traces should be strategically placed to provide a low-impedance return path for the signals and minimize the loop area.
Frequently Asked Questions (FAQ)
-
What is the difference between a flexible PCB and a rigid PCB?
A flexible PCB is made of a thin, flexible substrate material, such as polyimide or polyester, which allows it to bend, twist, and conform to various shapes. In contrast, a rigid PCB is made of a solid, non-flexible substrate material, such as FR-4, which provides a stable and rigid platform for the components and traces. -
Can flexible PCBs be used in high-temperature applications?
Yes, flexible PCBs can be used in high-temperature applications, provided that the appropriate substrate material and components are selected. Polyimide is the most common substrate material for high-temperature applications, as it can withstand temperatures up to 300°C. However, the maximum operating temperature of the flexible PCB will also depend on the temperature ratings of the components and the solder joints. -
How do I choose the right substrate material for my flexible PCB?
The choice of substrate material for a flexible PCB depends on several factors, such as the application requirements, environmental conditions, and cost constraints. Polyimide is the most common choice for high-performance applications, as it offers excellent thermal stability, chemical resistance, and mechanical strength. Polyester is a more cost-effective alternative for applications with lower temperature and performance requirements. -
Can flexible PCBs be repaired or reworked?
Repairing or reworking flexible PCBs can be challenging, as the thin and flexible substrate is more susceptible to damage during the repair process. However, with the right tools and techniques, such as precision soldering equipment and specialized repair materials, flexible PCBs can be successfully repaired or reworked. It is important to consult with experienced technicians and follow best practices to ensure the reliability and functionality of the repaired PCB. -
Are there any special considerations for storing and handling flexible PCBs?
Yes, flexible PCBs require special care during storage and handling to prevent damage and ensure their long-term reliability. Some key considerations include: -
Storing flexible PCBs in a cool, dry, and dust-free environment, away from direct sunlight and heat sources.
- Handling flexible PCBs with clean, lint-free gloves to avoid contamination and electrostatic discharge (ESD) damage.
- Avoiding excessive bending, twisting, or stretching of the flexible PCB, particularly in areas with components or solder joints.
- Using proper packaging materials, such as anti-static bags or containers, to protect the flexible PCBs during transportation and storage.
Conclusion
Flexible PCBs have revolutionized the electronics industry by enabling the design of compact, lightweight, and reliable electronic devices that can withstand the rigors of various applications. With their unique properties and advantages, flexible PCBs have found widespread use in consumer electronics, medical devices, automotive systems, aerospace, and industrial equipment.
However, designing and manufacturing flexible PCBs requires a different approach compared to rigid PCBs, as several additional factors, such as bend radius, trace width and spacing, component placement, and strain relief, need to be considered to ensure the reliability and performance of the final product.
As technology continues to advance and the demand for smaller, more flexible, and more reliable electronic devices grows, the importance of flexible PCBs will only continue to increase. By staying up-to-date with the latest developments in flexible PCB design, materials, and manufacturing processes, engineers and designers can create innovative and high-performance products that meet the evolving needs of the market.
0 Comments