Introduction to Circuit Assembly
Circuit assembly is the process of connecting electronic components together to create a functional circuit board. It involves soldering components onto a printed circuit board (PCB) according to a specific design. The quality of the circuit assembly is crucial for the proper functioning and reliability of the electronic device.
In this comprehensive guide, we will cover the basics of quality circuit assembly, including the tools and techniques used, best practices, and common challenges faced during the assembly process.
Table of Contents
- Tools and Equipment for Circuit Assembly
- PCB design considerations
- Component Placement
- Soldering Techniques
- Inspection and Testing
- Common Assembly Challenges and Solutions
- Best Practices for Quality Circuit Assembly
- Frequently Asked Questions (FAQ)
Tools and Equipment for Circuit Assembly
To ensure quality circuit assembly, it is essential to have the right tools and equipment. Here are some of the essential tools required for circuit assembly:
Tool | Description |
---|---|
Soldering Iron | A tool used to melt solder and join electronic components to the PCB. |
Solder | A metal alloy used to create electrical connections between components and the PCB. |
Flux | A chemical used to improve the flow of solder and prevent oxidation. |
Tweezers | Used for handling small components and precise placement on the PCB. |
Wire Cutters | Used for cutting component leads and wires to the required length. |
Magnifying Glass | Helps in inspecting the quality of solder joints and identifying any defects. |
Multimeter | Used for testing the continuity and functionality of the assembled circuit. |
In addition to these tools, it is also important to have a clean and well-lit workspace, an ESD (Electrostatic Discharge) safe mat, and proper ventilation to minimize exposure to solder fumes.
PCB Design Considerations
Before starting the circuit assembly process, it is crucial to ensure that the PCB design is optimized for manufacturing. Here are some key considerations:
Component Placement
- Place components in a logical order, considering the flow of the circuit and minimizing the distance between connected components.
- Ensure adequate spacing between components to avoid short circuits and facilitate soldering.
- Consider the orientation of components for ease of assembly and to minimize the risk of incorrect placement.
Trace Width and Spacing
- Ensure that the trace width is appropriate for the current carrying capacity of the circuit.
- Maintain adequate spacing between traces to avoid signal interference and short circuits.
Solder Pad Design
- Design solder pads with sufficient size and shape to accommodate the component leads and allow for proper soldering.
- Consider the use of SMD (Surface Mount Device) pads for smaller components to save space on the PCB.
Silkscreen and Assembly Instructions
- Include clear and legible silkscreen markings on the PCB to indicate component placement, polarity, and any special instructions.
- Provide a detailed assembly drawing or instructions to guide the assembly process.
By considering these design aspects, you can ensure that the PCB is optimized for quality circuit assembly and minimize the risk of assembly errors.
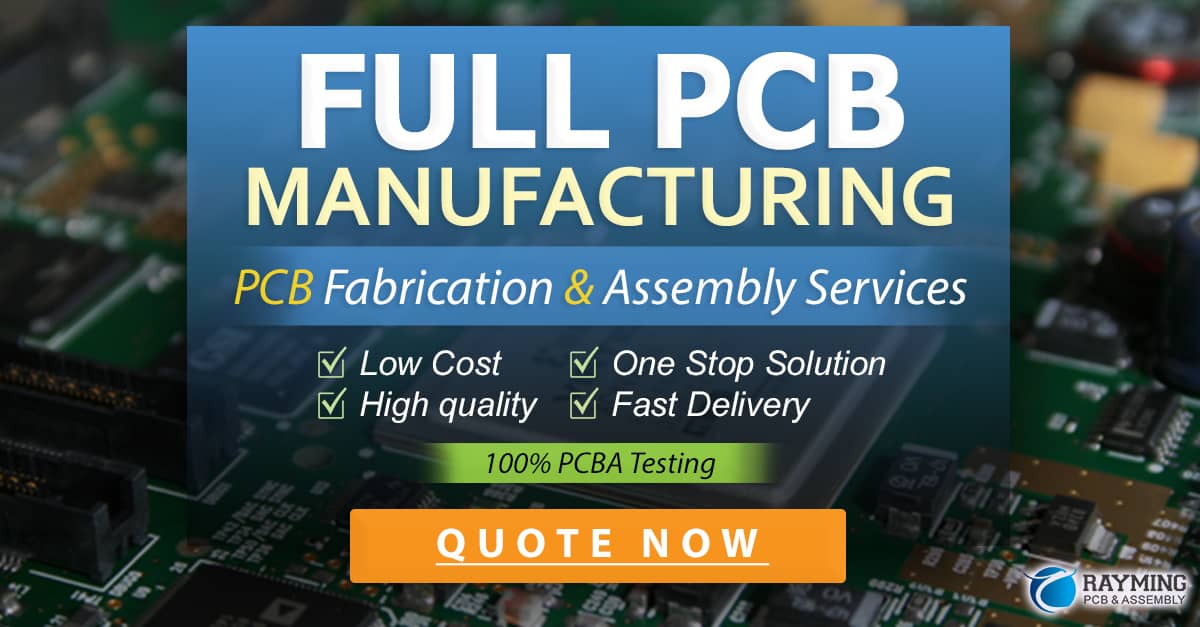
Component Placement
Accurate component placement is essential for quality circuit assembly. Here are some best practices to follow:
-
Use a pick and place machine: For high-volume production, using a pick and place machine can significantly improve the speed and accuracy of component placement. These machines use computer-controlled robotic arms to pick up components from reels or trays and place them precisely on the PCB.
-
Manual placement techniques: For low-volume or prototype assembly, manual placement techniques can be used. Use tweezers to handle components and refer to the assembly drawing or instructions for correct placement. Take care to orient components correctly, especially for polarized components like diodes and electrolytic capacitors.
-
Double-check component values: Before placing components, always double-check their values against the bill of materials (BOM) and the assembly drawing. This helps prevent incorrect component placement, which can lead to circuit malfunction or damage.
-
Inspect placement quality: After placing components, visually inspect the PCB to ensure that all components are placed correctly and securely. Check for any missing or misaligned components, and correct them before proceeding to soldering.
Soldering Techniques
Soldering is the process of joining electronic components to the PCB using a metal alloy called solder. Here are some common soldering techniques used in circuit assembly:
Through-Hole Soldering
- Used for components with wire leads that are inserted through holes in the PCB and soldered on the opposite side.
- Apply a small amount of solder to the iron tip and heat the component lead and the PCB pad simultaneously.
- Feed solder into the joint, allowing it to flow around the lead and fill the hole.
- Remove the iron and let the joint cool and solidify.
Surface Mount Soldering
- Used for SMD components that are placed directly on the surface of the PCB.
- Apply a small amount of solder paste to the PCB pads using a stencil or syringe.
- Place the SMD component on the solder paste using tweezers or a pick and place machine.
- Heat the component and the PCB pad using a hot air gun or a reflow oven, allowing the solder paste to melt and form a joint.
Wave Soldering
- Used for high-volume production of Through-hole PCBs.
- The PCB is passed over a molten solder wave, which selectively solders the component leads to the PCB pads.
- Requires careful control of the solder wave height, temperature, and conveyor speed to ensure quality joints.
Regardless of the soldering technique used, it is important to follow good soldering practices, such as using the correct temperature, applying the right amount of solder, and ensuring proper joint formation. Inspect the soldered joints visually and use a multimeter to test for continuity and short circuits.
Inspection and Testing
After the circuit assembly is complete, it is essential to perform thorough inspection and testing to ensure the quality and functionality of the assembLED PCB. Here are some key steps:
Visual Inspection
- Check for any visible defects, such as poor solder joints, bridging, or damaged components.
- Verify that all components are placed correctly and oriented according to the assembly drawing.
- Look for any missing or extra components, and correct them as needed.
Electrical Testing
- Use a multimeter to test for continuity between connected points and ensure there are no short circuits.
- Apply power to the PCB and measure the voltage levels at key points to verify proper operation.
- Test the functionality of the circuit by applying input signals and measuring the output response.
Functional Testing
- Perform a complete functional test of the assembled PCB in its intended operating environment.
- Verify that the circuit performs as expected and meets the specified requirements.
- Test the PCB under various conditions, such as different temperatures, humidity levels, and vibration, to ensure reliability.
Automated Optical Inspection (AOI)
- For high-volume production, AOI systems can be used to automatically inspect the assembled PCB for defects.
- AOI uses high-resolution cameras and image processing algorithms to detect solder joint defects, component placement errors, and other anomalies.
- AOI can quickly identify potential issues and provide feedback for process improvement.
By performing thorough inspection and testing, you can identify and correct any assembly defects early in the process, ensuring the quality and reliability of the final product.
Common Assembly Challenges and Solutions
Despite following best practices, circuit assembly can present various challenges. Here are some common issues and their solutions:
Challenge | Solution |
---|---|
Tombstoning of SMD components | Ensure equal heating of component leads, use a balanced pad design, and control solder volume. |
Solder bridges | Maintain proper solder volume, use a fine-tipped iron, and apply solder wick to remove excess. |
Cold Solder joints | Use the correct soldering temperature, apply sufficient heat, and ensure proper joint formation. |
Lifted or misaligned components | Use a pick and place machine for accurate placement, and ensure adequate adhesion of components. |
Electrostatic discharge (ESD) | Use an ESD-safe workspace, wear ESD-protective gear, and handle components with care. |
By being aware of these common challenges and implementing the appropriate solutions, you can minimize assembly defects and improve the overall quality of the circuit assembly process.
Best Practices for Quality Circuit Assembly
To ensure consistent quality in circuit assembly, follow these best practices:
-
Use high-quality components: Source components from reputable suppliers and ensure they meet the required specifications.
-
Follow the assembly drawing: Always refer to the assembly drawing or instructions for correct component placement and orientation.
-
Maintain a clean workspace: Keep the work area clean and organized to prevent contamination and reduce the risk of assembly errors.
-
Use the right tools: Invest in high-quality soldering tools and equipment, and ensure they are properly maintained.
-
Control the soldering process: Use the correct soldering temperature, apply the right amount of solder, and ensure proper joint formation.
-
Perform regular inspections: Conduct visual inspections and electrical tests at various stages of the assembly process to catch defects early.
-
Document the process: Maintain detailed records of the assembly process, including component lot numbers, process parameters, and test results.
-
Provide training: Ensure that assembly operators are properly trained in the required skills and techniques for quality circuit assembly.
-
Continuously improve: Monitor the assembly process, identify areas for improvement, and implement corrective actions to enhance quality and efficiency.
By adhering to these best practices, you can establish a robust quality management system for circuit assembly and consistently deliver high-quality products.
Frequently Asked Questions (FAQ)
- What is the difference between through-hole and surface mount soldering?
-
Through-hole soldering involves inserting component leads through holes in the PCB and soldering them on the opposite side. Surface mount soldering, on the other hand, involves placing components directly on the surface of the PCB and soldering them in place.
-
How can I prevent solder bridges during assembly?
-
To prevent solder bridges, maintain proper solder volume, use a fine-tipped soldering iron, and apply solder wick to remove any excess solder. Ensure adequate spacing between components and traces on the PCB design.
-
What is the purpose of flux in soldering?
-
Flux is a chemical used to improve the flow of solder and prevent oxidation during the soldering process. It helps remove contaminants from the surfaces being soldered and promotes the formation of a strong and reliable solder joint.
-
How can I test the functionality of an assembled PCB?
-
To test the functionality of an assembled PCB, apply power to the board and measure the voltage levels at key points using a multimeter. Apply input signals and measure the output response to verify proper operation. Perform a complete functional test in the intended operating environment.
-
What are some common causes of component damage during assembly?
- Common causes of component damage include excessive heat during soldering, electrostatic discharge (ESD), mechanical stress during handling, and incorrect component placement or orientation. To prevent damage, use the correct soldering temperature, handle components with care, and follow proper ESD precautions.
By understanding these common questions and their answers, you can troubleshoot assembly issues more effectively and ensure the quality and reliability of your circuit assembly process.
0 Comments