What is a Backplane?
A backplane is a printed circuit board (PCB) that serves as the central connection point for other PCBs, modules, or components in an electronic system. It provides mechanical support and electrical interconnections, allowing communication and power distribution between the connected components.
Key Characteristics of a Backplane
- Provides a common interface for connecting multiple components
- Enables data transfer and power distribution
- Offers mechanical support for the connected components
- Allows for modular system design and easy maintenance
Types of Backplanes
There are several types of backplanes, each designed for specific applications and requirements.
Passive Backplanes
Passive backplanes are the simplest type, consisting of a PCB with connectors and no active components. They provide electrical interconnections and mechanical support but do not contain any circuitry for signal conditioning or processing.
Active Backplanes
Active backplanes incorporate additional circuitry, such as bus drivers, terminators, and logic devices, to enhance signal integrity and performance. They can also include features like clock distribution, power management, and monitoring capabilities.
Intelligent Backplanes
Intelligent backplanes take active backplanes a step further by integrating microprocessors, memory, and other intelligent devices. They can perform advanced functions, such as system management, data processing, and communication control.
Backplane Architectures
Backplanes can be designed using various architectures to suit different system requirements.
Bus-based Architectures
Bus-based architectures use a shared communication channel, called a bus, to connect multiple components. Examples include:
- VMEbus
- PCI bus
- CompactPCI
- ATCA (Advanced Telecommunications Computing Architecture)
Switched Fabric Architectures
Switched fabric architectures use a network of switches to provide dedicated communication paths between components. This allows for higher bandwidth, lower latency, and better scalability compared to bus-based architectures. Examples include:
- RapidIO
- Infiniband
- PCI Express
- Ethernet
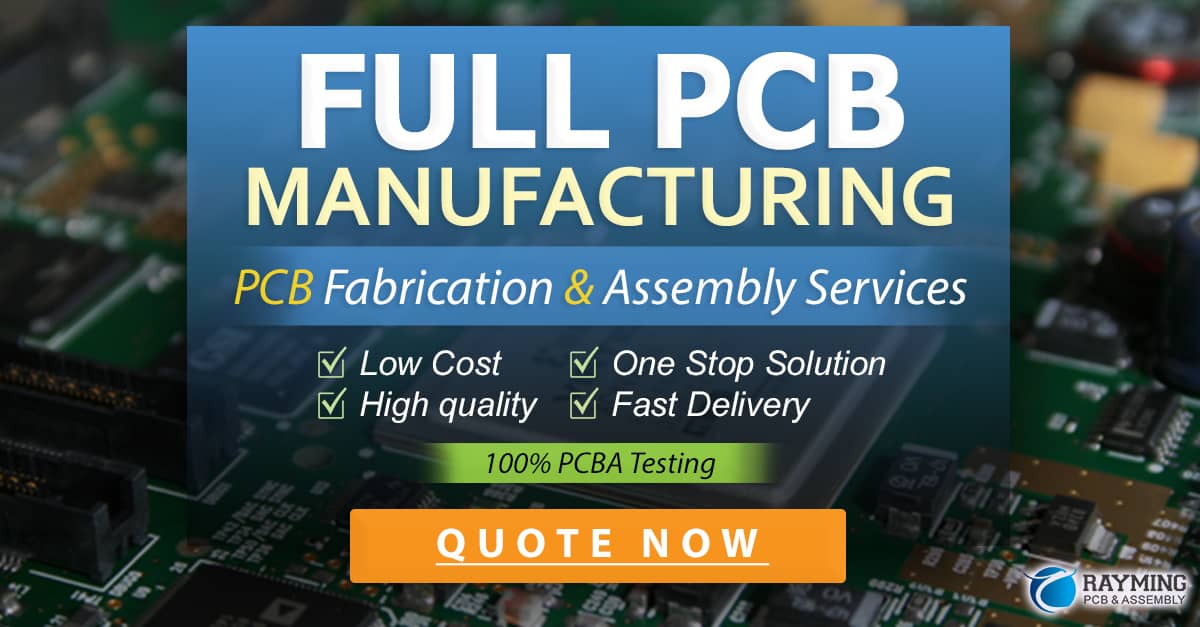
Backplane Connectors
Backplane connectors play a crucial role in establishing reliable connections between the backplane and the connected components.
Types of Backplane Connectors
- DIN 41612
- IEC 60603-2
- IEEE 1101.1
- HPM (High-Performance Modular)
- VITA (VMEbus International Trade Association)
Connector Type | Standards | Characteristics |
---|---|---|
DIN 41612 | DIN | Widely used in Europe, 2 or 3 rows, various sizes |
IEC 60603-2 | IEC | Similar to DIN 41612, improved performance |
IEEE 1101.1 | IEEE | Commonly used in VMEbus systems |
HPM | Proprietary | High-density, high-speed, used in ATCA systems |
VITA | VITA | Various standards for VMEbus and VPX systems |
Connector Selection Considerations
- Compatibility with the backplane and connected components
- Signal integrity and electrical performance
- Mechanical reliability and durability
- Cost and availability
Backplane Design Considerations
Designing a backplane requires careful consideration of various factors to ensure optimal performance and reliability.
Signal Integrity
- Impedance matching
- Crosstalk reduction
- Termination strategies
- Differential signaling
Power Distribution
- Voltage levels and current requirements
- Power plane design
- Decoupling and filtering
- Power sequencing
Mechanical Design
- Dimensions and form factors
- Mounting options
- Cooling and airflow
- Vibration and shock resistance
Manufacturing and Assembly
- PCB Fabrication process
- Soldering and assembly techniques
- Quality control and testing
- Compliance with industry standards
Applications of Backplanes
Backplanes are used in a wide range of applications across various industries.
Telecommunications
- Network switches and routers
- Base stations and wireless infrastructure
- Optical transport systems
Industrial Automation
- Process control systems
- Programmable logic controllers (PLCs)
- Distributed control systems (DCS)
Military and Aerospace
- Avionics systems
- Radar and sonar equipment
- Satellite communications
Data Centers and High-Performance Computing
- Servers and storage systems
- Supercomputers and clustered systems
- Network and security appliances
Frequently Asked Questions (FAQ)
1. What is the difference between a backplane and a motherboard?
A backplane is a PCB that provides interconnections and support for other PCBs or modules, while a motherboard is the main PCB in a computer that houses the CPU, memory, and other essential components. Backplanes are commonly used in modular systems, whereas motherboards are used in standalone devices like personal computers.
2. Can a backplane be upgraded or replaced?
Yes, backplanes can be upgraded or replaced, depending on the system design. Modular systems often allow for easy replacement of the backplane to accommodate new technologies or expand capabilities. However, it’s essential to ensure compatibility with the connected components and consider the impact on the overall system performance.
3. How do I choose the right backplane for my application?
Choosing the right backplane depends on several factors, including the system requirements, performance needs, scalability, and industry standards. Consider the following aspects:
– Bus or switched fabric architecture
– Bandwidth and data transfer rates
– Power distribution and management
– Mechanical form factor and compatibility
– Compliance with relevant industry standards
– Cost and availability
4. What are the advantages of using a backplane in an electronic system?
Using a backplane in an electronic system offers several advantages:
– Modularity and flexibility: Backplanes allow for easy addition, removal, or replacement of components, enabling modular system design and upgradability.
– Scalability: Backplanes can support multiple components and allow for system expansion as needed.
– Reliability: Backplanes provide a stable and reliable connection between components, ensuring proper communication and power distribution.
– Simplified maintenance: Modular design facilitated by backplanes makes system maintenance and troubleshooting easier, as individual components can be replaced without affecting the entire system.
5. What are the challenges in backplane design and how can they be addressed?
Backplane design presents several challenges, including:
– Signal integrity: Ensuring proper signal quality, minimizing crosstalk, and maintaining impedance matching require careful design and layout techniques, such as differential signaling, proper termination, and shielding.
– Power distribution: Providing stable and clean power to all connected components requires proper power plane design, decoupling, and filtering techniques.
– Mechanical constraints: Backplanes must fit within the specified form factor, provide adequate support and cooling, and withstand vibration and shock. Careful mechanical design and simulations can help address these challenges.
– Manufacturing and assembly: Ensuring reliable and consistent manufacturing requires adherence to industry standards, proper PCB fabrication processes, and strict quality control measures.
Conclusion
Backplanes are essential components in many electronic systems, providing the necessary interconnections, power distribution, and mechanical support for modular designs. Understanding the types of backplanes, architectures, and connectors is crucial for selecting the right backplane for a given application.
Careful consideration of signal integrity, power distribution, mechanical design, and manufacturing aspects is essential for developing a reliable and high-performance backplane. As technology advances and new applications emerge, backplane designs will continue to evolve to meet the ever-increasing demands for speed, reliability, and flexibility in electronic systems.
0 Comments