Understanding the Basics of PCBs
Printed Circuit Boards, commonly known as PCBs, are the backbone of modern electronics. These boards are used to mechanically support and electrically connect electronic components using conductive pathways, tracks, or signal traces etched from copper sheets laminated onto a non-conductive substrate. PCBs are used in nearly all electronic products, from simple devices like calculators and radios to complex systems like computers and spacecraft.
Types of PCBs
PCBs can be classified based on the number of layers they have:
Type | Layers | Description |
---|---|---|
Single-sided | 1 | Components are mounted on one side of the board |
Double-sided | 2 | Components are mounted on both sides of the board |
Multi-layered | 3+ | Multiple layers of conductive pathways separated by insulation |
The Significance of PCB Color
While the color of a PCB may seem like a purely aesthetic choice, it can actually serve important functions in the manufacturing and assembly process. Different colors can indicate different properties or purposes of the board.
Common PCB Colors and Their Meanings
Color | Meaning |
---|---|
Green | Standard PCB color, no special properties |
Red | High-frequency or high-speed applications |
Yellow | High-durability, often used in industrial settings |
Blue | Solder mask color, helps prevent Solder Bridges |
Black | High-end aesthetic, used in consumer electronics |
White | Reflective properties, used in LED lighting applications |
Why are Some Circuit Boards Blue?
The blue color commonly seen on PCBs is not the actual color of the board itself, but rather the color of the solder mask. Solder mask is a thin layer of polymer applied to the copper traces on a PCB to protect them from oxidation and prevent solder bridges from forming during the soldering process.
The Role of Solder Mask
Solder mask serves several important functions:
- Protection: It protects the copper traces from oxidation and mechanical damage.
- Insulation: It provides electrical insulation between the copper traces.
- Solder Control: It prevents solder from bridging between traces during the soldering process.
Advantages of Blue Solder Mask
While solder mask can come in a variety of colors, blue is a popular choice for several reasons:
- Visibility: The blue color provides good contrast against the copper traces, making it easier for technicians to inspect the board for defects.
- Durability: Blue solder mask is known for its durability and resistance to cracking or peeling over time.
- Aesthetics: The blue color gives the PCB a clean, professional look that is appealing to consumers.
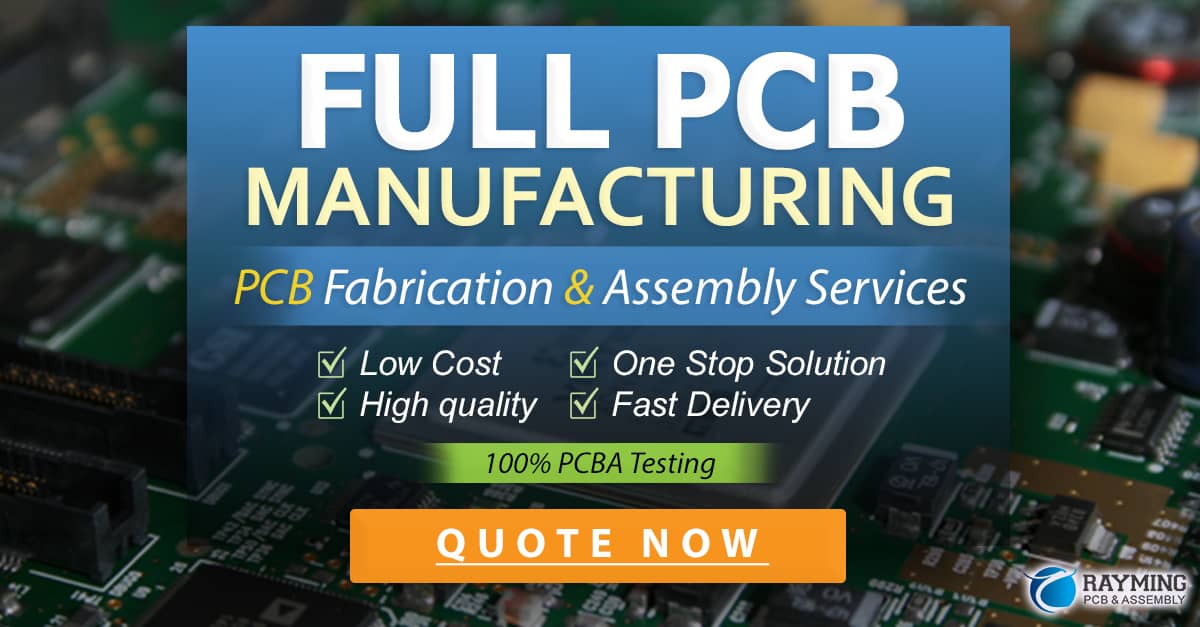
The Manufacturing Process of Blue PCBs
The process of manufacturing a blue PCB involves several steps:
- Design: The circuit is designed using specialized software, and the layout of the copper traces is determined.
- Printing: The design is printed onto the copper-clad board using a photoresist process.
- Etching: The unwanted copper is etched away, leaving only the desired traces.
- Solder Mask Application: The blue solder mask is applied to the board, covering the copper traces.
- Silkscreen Printing: Any text or symbols are printed onto the board using white silkscreen ink.
- Surface Finish: A surface finish, such as HASL or ENIG, is applied to the exposed copper to prevent oxidation and improve solderability.
Solder Mask Application Methods
There are two main methods for applying solder mask to a PCB:
-
Silk Screening: The solder mask is applied through a fine mesh screen, similar to how t-shirts are printed. This method is suitable for low-volume production.
-
Liquid Photo Imaging (LPI): The solder mask is applied as a liquid photopolymer and then exposed to UV light through a photographic film. This method offers higher precision and is suitable for high-volume production.
Advantages of Blue PCBs
Blue PCBs offer several advantages over other colors:
-
Improved Visibility: The blue color provides excellent contrast against the copper traces and any printed text or symbols, making it easier for technicians to inspect the board for defects.
-
Enhanced Durability: Blue solder mask is known for its durability and resistance to cracking or peeling over time, which helps maintain the integrity of the circuit.
-
Aesthetic Appeal: The clean, professional look of blue PCBs is appealing to consumers and can help enhance the perceived quality of the end product.
-
Better Solderability: The blue solder mask helps prevent solder bridges from forming during the soldering process, which can improve the reliability of the circuit.
-
Reduced Eye Strain: The blue color is easier on the eyes compared to other colors like green or red, which can help reduce eye strain for technicians who work with PCBs for extended periods.
Applications of Blue PCBs
Blue PCBs can be found in a wide variety of electronic products, including:
-
Consumer Electronics: Smartphones, laptops, televisions, and other consumer devices often use blue PCBs for their aesthetic appeal and durability.
-
Industrial Equipment: Blue PCBs are commonly used in industrial settings due to their high durability and resistance to harsh environments.
-
Medical Devices: The enhanced visibility and reliability of blue PCBs make them well-suited for use in medical devices, where accuracy and durability are critical.
-
Automotive Electronics: Blue PCBs can be found in various automotive electronic systems, such as infotainment systems and engine control modules.
-
Aerospace and Defense: The high reliability and durability of blue PCBs make them ideal for use in aerospace and defense applications, where failure is not an option.
Frequently Asked Questions (FAQ)
1. Are blue PCBs more expensive than other colors?
In general, the color of the solder mask does not significantly impact the cost of the PCB. However, some specialized colors or finishes may incur additional costs.
2. Can blue PCBs be used for high-frequency applications?
Yes, blue PCBs can be used for high-frequency applications. The color of the solder mask does not affect the electrical properties of the board.
3. Are blue PCBs more environmentally friendly than other colors?
The color of the solder mask does not have a direct impact on the environmental friendliness of the PCB. However, some manufacturers may use more eco-friendly materials or processes in the production of their PCBs, regardless of color.
4. Can blue PCBs be manufactured in small quantities?
Yes, blue PCBs can be manufactured in small quantities. Many PCB Fabrication houses offer low-volume production options, and the color of the solder mask does not affect the minimum order quantity.
5. Are there any disadvantages to using blue PCBs?
There are no significant disadvantages to using blue PCBs compared to other colors. The choice of solder mask color is largely a matter of personal preference and the specific requirements of the application.
Conclusion
Blue PCBs have become increasingly popular in recent years due to their enhanced visibility, durability, and aesthetic appeal. The blue color is not the actual color of the board itself, but rather the color of the solder mask, which serves to protect the copper traces and prevent solder bridges from forming during the soldering process.
While the color of the solder mask does not directly affect the electrical properties of the board, blue PCBs offer several advantages over other colors, including improved visibility, enhanced durability, and reduced eye strain for technicians.
Blue PCBs can be found in a wide variety of electronic products, from consumer electronics to industrial equipment and aerospace applications. As the demand for high-quality, reliable PCBs continues to grow, it is likely that blue PCBs will remain a popular choice among manufacturers and consumers alike.
0 Comments