Introduction to SEMI-FLEX PCBs
SEMI-Flex PCBs, also known as semi-flexible printed circuit boards, are a unique type of PCB that combines the best features of both rigid and Flexible PCBs. These boards are designed to provide a balance between the stability of rigid PCBs and the flexibility of flexible PCBs, making them ideal for a wide range of applications.
What are SEMI-FLEX PCBs?
SEMI-FLEX PCBs are a type of printed circuit board that consists of both rigid and flexible layers. The rigid layers provide structural support and stability, while the flexible layers allow for bending and folding of the board. This combination of rigid and flexible layers enables SEMI-FLEX PCBs to be used in applications where both stability and flexibility are required.
Advantages of SEMI-FLEX PCBs
SEMI-FLEX PCBs offer several advantages over traditional rigid and flexible PCBs, including:
-
Improved reliability: The combination of rigid and flexible layers in SEMI-FLEX PCBs provides improved reliability compared to fully flexible PCBs. The rigid layers help to prevent damage to the flexible layers during handling and use.
-
Increased design flexibility: SEMI-FLEX PCBs allow for greater design flexibility than rigid PCBs. The flexible layers can be folded and bent to fit into tight spaces or conform to unique shapes.
-
Reduced assembly time: SEMI-FLEX PCBs can be designed with fewer interconnects than rigid PCBs, which can reduce assembly time and cost.
-
Enhanced signal integrity: The combination of rigid and flexible layers in SEMI-FLEX PCBs can help to reduce signal loss and improve signal integrity compared to fully flexible PCBs.
SEMI-FLEX PCB Design Considerations
When designing SEMI-FLEX PCBs, there are several important considerations to keep in mind to ensure optimal performance and reliability.
Layer Stack-up
The layer stack-up of a SEMI-FLEX PCB is critical to its performance and reliability. A typical SEMI-FLEX PCB layer stack-up consists of:
- Rigid layers: These layers provide structural support and stability to the board.
- Flexible layers: These layers allow for bending and folding of the board.
- Adhesive layers: These layers bond the rigid and flexible layers together.
The number and thickness of each layer will depend on the specific application and design requirements.
Bend Radius
The bend radius is an important design consideration for SEMI-FLEX PCBs. The bend radius refers to the minimum radius that the flexible layers of the board can be bent without causing damage. The bend radius will depend on several factors, including:
- The thickness of the flexible layers
- The materials used in the flexible layers
- The number of copper traces in the flexible layers
It is important to carefully consider the bend radius when designing SEMI-FLEX PCBs to ensure that the board can withstand the required bending without damage.
Copper Thickness
The copper thickness of the traces in a SEMI-FLEX PCB is another important design consideration. Thicker copper traces can provide better electrical performance and improved reliability, but they can also make the board less flexible. Thinner copper traces, on the other hand, can improve flexibility but may reduce electrical performance and reliability.
It is important to carefully consider the copper thickness when designing SEMI-FLEX PCBs to ensure that the board meets the specific requirements of the application.
SEMI-Flex PCB Manufacturing Process
The manufacturing process for SEMI-FLEX PCBs is similar to that of traditional rigid PCBs, but with some important differences.
Material Selection
The first step in the SEMI-FLEX PCB manufacturing process is material selection. The materials used in SEMI-FLEX PCBs must be carefully chosen to ensure that the board meets the specific requirements of the application. Common materials used in SEMI-FLEX PCBs include:
- Polyimide: A flexible, heat-resistant material commonly used in the flexible layers of SEMI-FLEX PCBs.
- FR-4: A rigid, glass-reinforced epoxy laminate commonly used in the rigid layers of SEMI-FLEX PCBs.
- Adhesives: Special adhesives are used to bond the rigid and flexible layers together.
Lamination
After the materials have been selected, the next step in the SEMI-FLEX PCB manufacturing process is lamination. During lamination, the rigid and flexible layers are bonded together using heat and pressure. The adhesive layers are used to ensure a strong bond between the layers.
Drilling and Plating
After lamination, the next step is drilling and plating. Holes are drilled through the board to accommodate components and connectors. The holes are then plated with copper to provide electrical connectivity between the layers.
Etching and Solder Mask Application
After drilling and plating, the copper layers are etched to create the desired circuit pattern. A solder mask is then applied to protect the copper traces and prevent short circuits.
Finishing
The final step in the SEMI-FLEX PCB manufacturing process is finishing. During finishing, the board is cut to its final shape and size, and any required surface finishes are applied. Common surface finishes for SEMI-FLEX PCBs include:
- HASL (Hot Air Solder Leveling): A tin-lead finish that provides good solderability and reliability.
- ENIG (Electroless Nickel Immersion Gold): A gold finish that provides excellent solderability and durability.
- OSP (Organic Solderability Preservative): A organic finish that provides good solderability and is RoHS compliant.
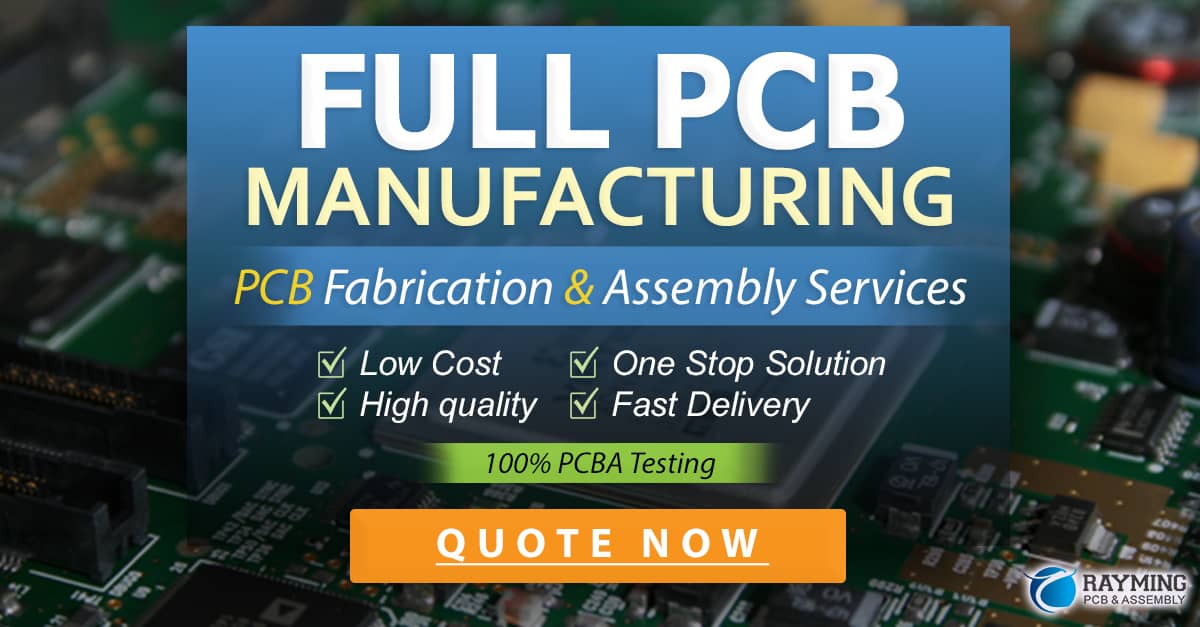
SEMI-FLEX PCB Assembly
After the SEMI-FLEX PCB has been manufactured, the next step is assembly. The assembly process for SEMI-FLEX PCBs is similar to that of traditional rigid PCBs, but with some important differences.
Component Placement
The first step in the SEMI-FLEX PCB assembly process is component placement. Components are placed on the board using automated pick-and-place machines or by hand. It is important to carefully consider the placement of components to ensure that they do not interfere with the bending of the flexible layers.
Soldering
After component placement, the next step is soldering. Soldering is typically performed using reflow or Wave Soldering processes. It is important to carefully control the soldering process to ensure that the components are properly attached to the board without damaging the flexible layers.
Testing and Inspection
After soldering, the assembled SEMI-FLEX PCB must be tested and inspected to ensure that it meets the required specifications. Common testing and inspection methods for SEMI-FLEX PCBs include:
- Visual inspection: A visual inspection is performed to check for defects such as missing components, solder bridges, or damaged traces.
- Electrical testing: Electrical testing is performed to ensure that the board is functioning properly and meets the required specifications.
- Functional testing: Functional testing is performed to ensure that the board performs as intended in its intended application.
Challenges in SEMI-FLEX PCB Assembly
While the assembly process for SEMI-FLEX PCBs is similar to that of traditional rigid PCBs, there are some unique challenges that must be considered.
- Bending: The flexible layers of SEMI-FLEX PCBs can be damaged during the assembly process if they are bent or flexed excessively. It is important to carefully control the bending of the board during assembly to avoid damage.
- Component placement: The placement of components on SEMI-FLEX PCBs must be carefully considered to ensure that they do not interfere with the bending of the flexible layers. Components should be placed in areas of the board that will not be subjected to excessive bending.
- Soldering: The soldering process for SEMI-FLEX PCBs must be carefully controlled to avoid damaging the flexible layers. It is important to use the appropriate soldering techniques and materials to ensure a strong and reliable solder joint.
Applications of SEMI-FLEX PCBs
SEMI-FLEX PCBs are used in a wide range of applications where both stability and flexibility are required. Some common applications of SEMI-FLEX PCBs include:
- Automotive electronics: SEMI-FLEX PCBs are commonly used in automotive electronics applications such as dashboard displays, infotainment systems, and sensors.
- Medical devices: SEMI-FLEX PCBs are used in medical devices such as wearable monitors, implantable devices, and diagnostic equipment.
- Aerospace and defense: SEMI-FLEX PCBs are used in aerospace and defense applications such as avionics, radar systems, and satellite communications.
- Consumer electronics: SEMI-FLEX PCBs are used in consumer electronics applications such as smartphones, tablets, and wearable devices.
- Industrial automation: SEMI-FLEX PCBs are used in industrial automation applications such as robotics, motion control, and machine vision.
Application | Advantages of SEMI-FLEX PCBs |
---|---|
Automotive electronics | Improved reliability, design flexibility |
Medical devices | Enhanced signal integrity, design flexibility |
Aerospace and defense | Improved reliability, reduced assembly time |
Consumer electronics | Design flexibility, reduced assembly time |
Industrial automation | Improved reliability, enhanced signal integrity |
Choosing a SEMI-FLEX PCB Manufacturer
When choosing a SEMI-FLEX PCB manufacturer, there are several important factors to consider to ensure that you receive high-quality boards that meet your specific requirements.
Experience and Expertise
One of the most important factors to consider when choosing a SEMI-FLEX PCB manufacturer is their experience and expertise. Look for a manufacturer that has a proven track record of producing high-quality SEMI-FLEX PCBs and has experience working with a wide range of materials and applications.
Quality Control
Another important factor to consider is the manufacturer’s quality control processes. Look for a manufacturer that has a robust quality control system in place to ensure that every board meets the required specifications. This may include automated inspection systems, statistical process control, and regular quality audits.
Certifications
It is also important to choose a manufacturer that has the necessary certifications to ensure that their processes and products meet industry standards. Look for certifications such as ISO 9001, UL, and IPC.
Customer Service and Support
Finally, consider the manufacturer’s customer service and support. Look for a manufacturer that is responsive to your needs and provides timely and accurate communication throughout the manufacturing process. Also consider the level of technical support that the manufacturer provides, such as design assistance and troubleshooting.
FAQs
- What is the difference between a SEMI-FLEX PCB and a rigid PCB?
-
A SEMI-FLEX PCB combines both rigid and flexible layers, allowing for greater design flexibility and improved reliability compared to a traditional rigid PCB.
-
What are the advantages of using a SEMI-FLEX PCB?
-
SEMI-FLEX PCBs offer several advantages, including improved reliability, increased design flexibility, reduced assembly time, and enhanced signal integrity.
-
What materials are commonly used in SEMI-FLEX PCBs?
-
Common materials used in SEMI-FLEX PCBs include polyimide for the flexible layers, FR-4 for the rigid layers, and special adhesives to bond the layers together.
-
What are some common applications for SEMI-FLEX PCBs?
-
SEMI-FLEX PCBs are commonly used in automotive electronics, medical devices, aerospace and defense, consumer electronics, and industrial automation applications.
-
What should I look for when choosing a SEMI-FLEX PCB manufacturer?
- When choosing a SEMI-FLEX PCB manufacturer, look for a company with experience and expertise in producing high-quality SEMI-FLEX PCBs, robust quality control processes, necessary certifications, and responsive customer service and support.
Conclusion
SEMI-FLEX PCBs offer a unique combination of stability and flexibility, making them ideal for a wide range of applications. When designing and manufacturing SEMI-FLEX PCBs, it is important to carefully consider factors such as layer stack-up, bend radius, and copper thickness to ensure optimal performance and reliability.
The manufacturing and assembly processes for SEMI-FLEX PCBs are similar to those of traditional rigid PCBs, but with some important differences that must be considered. Choosing the right materials, controlling the bending of the flexible layers, and using appropriate soldering techniques are all critical to ensuring a high-quality final product.
When choosing a SEMI-FLEX PCB manufacturer, it is important to look for a company with experience and expertise in producing high-quality boards, robust quality control processes, necessary certifications, and responsive customer service and support.
Overall, SEMI-FLEX PCBs offer a versatile and reliable solution for a wide range of applications, and with careful design and manufacturing considerations, can provide optimal performance and reliability in even the most demanding environments.
0 Comments